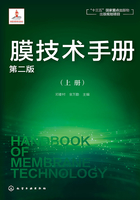
3.4 无机膜组件及成套化装置
3.4.1 概述
对于无机膜的实际工业应用而言,不仅要有良好的无机膜元件、膜组件,而且合适的操作工艺和清洗方法也是至关重要的。对一个膜过滤过程进行系统的实验研究,了解其分离机理,取得合适的操作参数,从而提出合理的工程设计,对于提高无机膜工程应用的技术经济指标是十分重要的。
3.4.2 膜元件
商品无机膜主要有三种形式:平板式、管式或管束式、多通道或蜂窝体。平板式主要用于实验室小规模分离和纯化,且多采用终端过滤的操作方式;而工业应用需要较大的膜过滤面积,于是管式或管束式,尤其是多通道或蜂窝体在工业过程中得以广泛的应用。多通道无机膜由于具有安装方便、易于维护,单位体积的膜过滤面积大,机械强度比管束式高等优点,适合于大规模的工业应用,已成为工业应用的主要品种。
管式及多通道式无机膜的操作方式基本为错流过滤形式。其中,多通道膜元件中流体流动方式见图3-39。液体(或气体)沿通道流动,在驱动力(通常为压力)作用下,渗透液依次通过膜层、过渡层和支撑层。同时,大量未渗透出的液体继续沿通道流动,并在膜表面产生冲刷作用,将过滤下来的物质带走,避免在膜表面形成滤饼。由于液体在通道中的流动方向和渗透液的流动方向垂直,因而将这种过滤方式称为错流过滤。以无机微滤膜元件为例,其支撑层的孔径一般为1~20μm,孔隙率为30%~65%,其作用是增加膜的机械强度,通常由Al2O3、ZrO2、C、SiC及金属等材料制成;过渡层的孔径比支撑层的孔径小,其作用是防止膜层制备过程中颗粒向多孔支撑层的渗透,厚度约20~60μm,孔隙率为30%~40%;膜层厚度大约为3~10μm,孔隙率为40%~55%。目前,孔径在0.05μm以上的陶瓷微滤膜仍然是应用最广泛的无机膜材料。近年来,小孔径的陶瓷超滤膜以及分离精度更高的陶瓷纳滤膜逐渐发展起来,在食品、化工及医药等领域得到越来越多的关注。表3-16为国内外无机膜厂家的主要产品。

图3-39 多通道膜元件中流体的流动示意图
1—通道;2—支撑层;3—过渡层;4—膜层
表3-16 国内外无机膜厂家的主要产品

3.4.3 膜组件
常见的无机膜组件是由单根、7根、19根、36根或更多单管或多通道的膜元件构成,如图3-40所示,组件中进出料流动示意图见图3-41。一台无机膜过滤设备通常包括很多膜组件,根据过程需要进行组合。图3-42是法国Novasep公司的一套ZrO2/TiO2复合陶瓷膜过滤装置,图3-43是我国自己开发的工业陶瓷膜过滤装置。

图3-40 膜组件照片

图3-41 组件的进出料示意图

图3-42 法国Novasep公司的工业陶瓷膜分离系统

图3-43 我国开发的工业陶瓷膜分离系统
膜组件的装填密度是指单位体积的壳体中装填的膜面积,一般无机膜组件的装填情况见表3-17。
表3-17 无机膜组件的装填密度

在陶瓷膜组件的设计和应用中必须解决膜的端封与膜组件的密封问题。管式或多通道膜的两端必须进行特殊处理,以达到对所有组分都不通过的要求,防止渗透液与截留液的返混及截留液通过分离层上的缺陷或膜两端支撑体上的大孔漏入渗透侧。目前主要采用两端涂上釉的方式进行陶瓷膜的端封。膜组件的密封是应用过程中的另一大问题,密封材料的选用与使用条件有密切的关系。在密封材料的选择中,需要注意以下因素:热稳定性,化学相容性,密封材料与膜材料之间热膨胀系数的匹配,避免在使用过程中挤碎。
对于液相过滤,硅橡胶、环氧树脂、聚酯等都已用于连接陶瓷膜与不锈钢或塑料(如:CPVC)制成的组件的壳体或封头。对于高温应用(尤其是气相过程),主要采用的密封材料有聚酰亚胺等,这些材料可以应用于230℃以下;石墨/碳纤维及弹性石墨填料在氧化条件下可用至300~400℃,在还原或惰性环境中可在1000℃以下使用。
3.4.4 过滤过程
3.4.4.1 错流过滤
20世纪60年代后期,错流过滤过程被用于反渗透和超滤过程中,以控制浓差极化。与终端过滤不同的是,错流过滤中存在着两股流出液体:一股是渗透液(或称滤液);另一股是用于提供膜表面冲刷作用的循环流体。错流过滤的另一特征是存在着两个方向的速度:垂直于膜表面的滤液速度(v1)和平行于膜表面的错流速度(v2)。其典型流动示意图见图3-44。后来由Alfa-Laval公司开发了一个新的微滤过程,又称Bactocatch过程;沿膜元件长度方向操作压差恒定,其流程图见图3-45。这一技术首先用于牛奶和乳制品的过滤。与传统的错流过滤相比,膜的过滤通量有明显的提高。

图3-44 错流过滤示意图

图3-45 恒压差微滤过程的流程图
1—进料液储槽;2—清洗液储槽;3—膜组件;4—换热器;5—进料泵;6—截留液循环泵; 7—渗透液循环泵;8—三通阀;9—截留液出口阀;10—调节阀;11—渗透液出口阀; 12—流量计;13—热电偶;14—压力表
传统错流微滤和Bactocatch过程的明显差别是:传统的错流微滤中,渗透侧压力保持恒定,而进料侧由于错流过滤造成了压力损失,所以沿组件长度方向操作压差不断变化;而Bactocatch过程中,渗透侧压力沿膜组件长度方向不断变化,以维持沿组件长度方向操作压差的恒定,这种操作方式可以通过在渗透侧加入泵进行循环得以实现。
在传统的错流过滤中,组件进口部分操作压力较高,膜的过滤通量也相应较高。但在高的膜面流速下操作,沿组件长度方向压力下降较快,所以通量也明显下降。这种通量的不均匀使得沿组件长度方向,膜的阻力分布不均(进口大、出口小),从而严重地影响了总的渗透通量;Bactocatch过程克服了传统错流微滤的缺点,且由于浓差极化减小,膜的清洗周期明显增长,总的渗透通量提高。
3.4.4.2 操作方式
用于液体过滤的陶瓷膜微滤、超滤和纳滤过程,成套装置的基本操作方式有三种:开放系统、封闭系统、半开半闭系统。
(1)开放系统
通常用于工艺的可行性实验,典型的操作流程见图3-46。系统的错流速率和操作压力由单个泵提供。其缺点是每次都需将截留液在泵进口处由大气压力升至操作压力,系统的能量损失较大。而且由于料液不断循环通过泵和各个阀门,对进料液的性质可能有影响。

图3-46 开放体系的流程图
D—流量计;P1,P2—压力表; Q1—渗透液;Q2—截留液
(2)封闭系统
典型流程见图3-47。系统的错流速度和操作压力由低流量、高扬程的进料泵和高流量、低扬程的循环泵共同维持,减少了开放系统能量损失大的缺点。然而,这种系统的负效应也是十分明显的:在循环回路中料液的浓度不断增加,加速了膜污染,降低了膜的过滤通量。

图3-47 封闭系统的流程图
D—流量计;P1,P2—压力表; Q1—渗透液;Q2—截留液
(3)半开半闭系统
工业应用中常用的一种系统,不仅克服了开放系统能耗高的缺点,也可以防止料液浓度的不断升高。一般可采用三种操作方式:间歇、连续和多级连续。
①间歇操作过程 只有部分截留液回到料液槽,减小了系统内浓度的快速增长,浓度增长的减小幅度取决于Q2/Q1。其典型流程图见图3-48。

图3-48 半开半闭系统间歇操作方式流程图
D—流量计;P1,P2—压力表;Q1—渗透液;Q2—进料液;Q3—截留液
②连续操作过程 见图3-49,一部分截留液不断排出过滤回路,体积浓缩倍数的调节可以通过调节操作条件和渗透通量获得。

图3-49 半开半闭系统连续操作方式流程图
D—流量计;P1,P2—压力表;Q1—渗透液;Q2,Q3—截留液
③多级连续的操作过程 这一方式可以达到较高的浓缩倍数,见图3-50。在给定的进料压力下,通过调节最后一级循环的截留侧压力就可以达到调节过滤压力差的目的。级数越多,过滤速率越接近间歇操作。这种操作方式下,单位膜面积可获较高的过滤通量。

图3-50 半开半闭系统多级连续操作方式的流程图
P1,P2—压力表
3.4.4.3 膜污染的控制及清洗方法
在无机膜的应用过程中,膜污染的控制和膜的清洗方法十分重要。膜污染控制的目的是延长清洗周期,减少膜的清洗次数,而只有开发出能够完全恢复膜的稳定过滤通量的清洗方法,膜的过滤过程才能够投入实际应用。膜污染的控制主要是通过合适的操作方式和工业参数来实现的,清洗的关键是清洗剂和清洗条件。
针对不同的分离体系,膜污染控制的方法主要有以下几种:
①原料液预处理;
②膜表面的改性;
③外加场对膜污染进行控制,包括电场、离心场和超声波场;
④高压反冲,主要分为气体和液体两种反冲介质;
⑤强化传质,主要有改变流道截面的形状,由圆形改为星形,组件内插入不同的金属型芯,在进料液中加入气泡的方法等。
膜清洗方法通常可分为物理方法和化学方法,物理方法是指采用压水射流冲洗、海绵球机械清洗等去除污染物的方法。化学方法是采用对膜材料本身没有破坏性、对污染物有溶解作用或置换作用的化学试剂对膜进行清洗。
无机膜具有优异的化学稳定性和高的机械强度,可采用比有机膜更广泛的清洗方法进行清洗。目前无机膜化学清洗的一般规律为:无机强酸使污染物中一部分不溶性物质变为可溶性物质;有机酸主要清除无机盐的沉积;螯合剂可与污染物中的无机离子络合生成溶解度大的物质,减少膜表面和孔内沉积的盐和吸附的无机污染物;表面活性剂主要清除有机污染物;强氧化剂和强碱是清除油脂和蛋白、藻类等生物物质污染的;而对于细胞碎片等污染体系,多采用酶清洗剂。对于污染非常严重的膜,通常采用强酸、强碱交替清洗,并加入次氯酸钠等氧化剂与表面活性剂。在这些清洗过程中,常采用高速低压的操作条件,有时配以反冲,以发挥物理方法的作用,最大程度恢复膜通量。