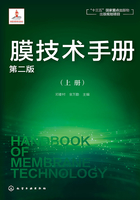
3.3 无机膜的制备
3.3.1 概述
无机膜的制备方法与材料的种类、膜的结构及孔径范围密切相关,并在借鉴陶瓷、金属材料制备技术的基础上发展并形成了多种制膜工艺,如悬浮粒子法、溶胶-凝胶(Sol-gel)法、阳极氧化法、CVD法、分相法和水热合成法等。
商品化的多孔陶瓷膜的外形主要有平板、单管和多通道3种,其结构通常是由支撑体、过渡层和顶层膜构成的多层非对称结构[29,30](见图3-10)。支撑体可提供足够的机械强度,典型的制备技术主要是挤压成型技术和流延成型技术,也可采用传统的注浆法制备。结构复杂的管式和多通道支撑体采用挤压成型技术或注浆法,而平板支撑体则使用流延成型技术。对于非对称膜的过渡层,孔径常介于微滤膜范围,常采用浸浆法成型,浸浆法有时也称其为悬浮粒子法。非对称膜的顶层如超滤和纳滤膜通常采用溶胶-凝胶技术制备。

图3-10 陶瓷膜外观形貌(a)及断面微观电镜照片(b)
近年来,随着无机膜技术的发展和材料科学及其制备技术的进展,无机膜的制备方法也不断拓宽,如:采用无电镀技术在多孔支撑体上制备金属及其合金膜,采用化学或物理气相沉积技术制膜或对膜进行修饰和表面改性;水热合成技术用于制备分子筛膜已经实现规模化生产;阳极氧化法制备氧化铝膜,分相法制备玻璃膜以及有机聚合物热分解法制备无机碳膜的研究也有较多报道;采用真空抽吸和外延生长等方法制备以石墨烯为代表的二维膜材料已经成为了研究热点。
3.3.2 多孔支撑体的制备
支撑体的作用主要为非对称膜,如微滤膜、超滤膜和纳滤膜提供足够的机械强度,其厚度一般在2mm左右。支撑体的制备主要采用挤出法、流延法、注浆法以及压制法成型,对于不同构型的膜采用不同的方法成型,表3-6列出支撑体成型方法和相应的构型。
表3-6 支撑体的成型方法与构型

(1)挤出成型法
在水或塑化剂中加入粉料和添加剂,经混合后,炼制成塑性泥料。利用各种成型机械进行挤出成型。制备过程如图3-11所示。

图3-11 挤出法制备支撑体的过程
①粉料粒子的选择 一般粒子粒径与膜孔径的比值为2.5左右,这一比值和孔隙率还受到粒子形貌的影响。另外,作为支撑体还要求其表面平整光滑、孔径分布窄,因此通常选择大小均匀、形状规整(如球形)的粒子。采用挤出法成型,可选粒子的大小在0.1~100μm。
②添加剂的选择 选择添加剂首先要求在烧结过程中能够分解烧尽,其主要作用在于改善泥料的可塑性和提高干燥过程中素坯的强度。因此添加剂多使用有机聚合物,表3-7列出了添加剂的种类和用途。另外根据泥料的要求还需加入消泡剂、致孔剂和防腐剂等。
表3-7 添加剂的种类和用途

多孔支撑体质量与添加剂的种类和加入量有着密切的关系,一般加入量占粉料的 15%~20%。
③混合 混合过程目的是获得分散均匀的物料。通常需要控制加料次序,首先混合粉料,然后加入有机添加剂。控制缓慢的加水速度,以防止粉料团聚,避免支撑体产生缺陷。
④练泥 练泥的目的在于使泥料中的水分和添加剂分布更加均匀并脱除泥料中的气泡,获得满足要求的塑性,通常采用真空练泥方式。
⑤陈化 经过练泥的泥料在一定温度和湿度的环境中放置一段时间,该过程水分和添加剂分布更加均匀。
⑥成型 采用挤出法成型时,泥料被挤出机的螺旋或活塞挤压向前、经过成型喷嘴出来达到要求的形状。制品的形状取决于喷嘴的内部形状,适于制备形状规则的管式和多通道支撑体,如图3-12所示,长度可根据要求进行切割,因此批量生产能力强。

图3-12 管式(a)和多通道(b)支撑体的挤出喷嘴[25]
挤出成型过程中通过调节挤出压力、速率和真空度等工艺参数,以获得无缺陷、表面光滑、形状规整的坯体。
⑦干燥与烧结 干燥过程是为了脱除坯体中的水分,提高坯体的强度,以便于搬运和烧成。在干燥过程中随着水分的减少,坯体将会出现收缩,如图3-13所示,因此必须制定严格的干燥程序,以避免干燥时产生缺陷。

图3-13 干燥过程坯体的收缩率变化
烧结的目的在于在高温下使粒子连接在一起,使坯体具有足够的机械强度,烧结过程中升温速率、烧结温度和保温时间以及冷却速率对制品的强度均有影响。对于多孔支撑体,烧结过程必须考虑到强度和孔隙率的矛盾。烧结温度越高、保温时间越长,强度就越高,但孔隙率却显著降低,孔隙率的降低将导致支撑体的渗透阻力增加。图3-14为两种烧结温度下α-Al2O3支撑体的表面形貌[31],与经1200℃烧结的支撑体相比,经1600℃烧结α-Al2O3支撑体的粒子边缘趋于圆滑,粒子之间发生显著连接,表面的粗糙度降低。烧结条件取决于粒子的大小、材料的种类以及添加剂的种类和数量。

图3-14 烧结温度对α-Al2O3支撑体结构的影响
(2)流延成型法
流延成型法已用来制备厚度在几毫米的平板多孔陶瓷支撑体或对称膜,其过程包括浆料制备、流延成型和干燥烧结三个步骤。粉料分散在液体中,加入分散剂、黏结剂和增塑剂,搅拌得到均匀的浆料,经过加料嘴不断地向转动的基带上流出,逐渐延展开来,干燥后得到一层薄膜。
①浆料制备 常用水或有机溶剂作为溶剂。水的干燥温度较高,时间长;为加速干燥,通常使用乙醇等有机物作为溶剂。蒸发速率低的溶剂用于制备厚膜,而蒸发快的用于制备薄膜。不饱和脂肪酸、磷酸酯用作分散剂。
搅拌和超声波处理的目的在于得到分散均匀的浆料。浆料的黏度和分散剂的质量影响分散效果。使用超声波可以避免引入杂质。丙烯酸树脂、聚苯乙烯和聚乙烯醇作为黏结剂使用,而聚乙二醇等用作增塑剂。
②流延成型 流延成型过程在专用的设备上完成,如图3-15所示。浆料由料槽底部流出,基带和刮刀相对运动,刮涂出一层平整而连续的薄膜。薄膜的厚度取决于刮刀与基带的间隙、基带的运动速度、浆料的浓度。

图3-15 流延成型设备示意图
1—基带;2—刮刀;3—浆料;4—加热元件
③干燥烧结 刮涂的薄膜经干燥和烧结后就得到多孔膜或支撑体。另外,注浆成型方法和压制成型方法(如等静压成型法)也已被用来制备管式和平板多孔陶瓷膜。
3.3.3 非对称微滤膜的制备
实用化的多孔陶瓷膜均采用多层的非对称结构,以降低渗透阻力,提高膜的渗透性。孔径介于0.2~10μm的单管和多通道非对称微滤膜主要采用浸浆方法成膜,即首先配制悬浮液,多孔支撑体与悬浮液接触浸浆时,在毛细管力和黏性力的作用下形成涂层,干燥烧结后得到多孔膜。非对称微滤膜的制备过程如图3-16所示。

图3-16 非对称微滤膜的制备过程
(1)悬浮液的制备
悬浮液主要由粉料、溶剂、分散剂、黏结剂和增塑剂组成。悬浮液的组成影响制膜的工艺和膜的性能,因此需要控制各成分的添加量。
①溶剂 选择溶剂需考虑以下影响因素:a.良好的溶解性能,能够溶解分散剂、黏结剂和增塑剂等添加剂;b.稳定的化学性能,不与粉料发生化学反应;c.可挥发和烧尽。常用的溶剂有水和有机溶剂两大类。水是最常用的溶剂,无毒安全且成本低,但对粉料的润湿性能较差,挥发慢,干燥时间长,而且悬浮液脱除气泡困难。乙醇、甲乙酮和甲苯等有机溶剂则具有表面张力小、润湿性能较佳、挥发速率高和干燥时间短的优点。
②分散剂 粉料在介质中的分散效果,取决于分散剂所提供的双电层斥力和聚合物的空间位阻作用。在水基悬浮液中,分散剂的两种作用可同时存在;而在非水基悬浮液中,以位阻作用为主。粉料分散效果影响膜的结构(如孔隙率)和烧结性能。由图3-17和图3-18可见,对水基氧化铝悬浮液,以HNO3为分散剂,体系的pH显著影响膜的孔隙率和孔径分布。该体系的等电点为pH接近8,pH大于8时,分散效果差,粒子容易团聚,悬浮液不稳定,粒子堆积形成的膜结构疏松,表现为孔径偏大,孔隙率升高;而低于等电点,粒子分散均匀,悬浮液稳定,膜结构紧凑,相应膜的孔径和孔隙率小,膜的强度也高。不仅如此,分散效果还会影响到膜的表面均匀性,在图3-19中,对于不稳定的悬浮液,粒子团聚现象十分明显,导致膜表面粗糙;而使用稳定的悬浮液,粒子分散均匀,所得到的膜表面均匀光滑。

图3-17 浆料pH值对α-Al2O3膜的孔隙率的影响

图3-18 浆料pH值对α-Al2O3膜孔径分布的影响

图3-19 浆料pH值对膜表面结构的影响[23]
常用的分散剂主要有非离子、阳离子、阴离子和两性离子型四种,分散剂的添加量取决于粉料的种类、粒径大小和分布以及浓度。
③黏结剂和增塑剂 黏结剂的作用在于提高悬浮液的流平性能,提高素坯膜的干燥强度和韧性。常用的黏结剂有聚乙烯醇、聚丙烯酸胺盐等水基黏结剂,以及聚丙烯酸甲酯和乙基纤维素等非水基黏结剂。
增塑剂可确保黏结剂在常温下具有较好的流动性而不出现凝结,还可对粉料粒子起到润滑和交联作用,有利于悬浮液的稳定。常用的增塑剂主要有聚乙二醇、乙二醇等。黏结剂和增塑剂的添加量依据粉料的性质、粒径分布和浓度,以及对悬浮液流变性能的要求而定。
(2)多孔支撑膜的涂膜过程
膜的浸涂过程是制膜过程的重要环节,关系到膜的厚度及其均匀性和膜的完整性。在多孔支撑体上浸涂膜通常利用两种机理:毛细过滤和薄膜形成机理[13,32]。
当干燥的支撑体与悬浮液接触时,在毛细管力的作用下产生过滤作用。支撑体的孔与粒子的大小相当时,粒子被截留在支撑体表面,而形成膜;若支撑体孔径过大,粒子与分散剂一起渗透进入支撑体,不仅难以形成连续的膜层,还将增加流体的渗透阻力。毛细过滤过程中膜的厚度与接触时间、悬浮液黏度和固含量、支撑体的孔径及分布有关。
当支撑体从悬浮液中提出时,在黏性力的作用下,将产生一黏滞层,干燥焙烧后也可得到膜。该过程膜的厚度与悬浮液的黏度和固含量、支撑体从悬浮液中提出的速率有关,而与接触时间无关。采用浸浆方法涂膜,可预处理支撑体,消除毛细管力,单独利用薄膜形成机理进行涂膜。也可同时利用两种机理涂膜,此时膜的厚度变化与浸浆接触时间的关系如图3-20所示。

图3-20 膜厚度与浸浆接触时间的关系
①毛细过滤机理 当干燥的多孔支撑体与悬浮液接触时,在毛细管力的作用下产生与支撑体表面垂直方向的吸浆作用,如图3-21所示,悬浮液中的粒子在支撑体表面堆积形成浓缩滤饼层,干燥烧结后得到多孔膜。毛细管吸力的大小(Δpc)与悬浮液的表面张力(γ)和支撑体的孔径(r)有关:
(3-23)

图3-21 毛细过滤涂膜过程示意图
Leenaars[13]等和Tiller等[32]根据过滤理论和毛细作用机理导出滤饼层厚度(LC)与浸浆时间(t)的平方根成正比:
(3-24)
式中,KC为吸浆速率常数,是支撑体的孔隙率、孔径及分布、悬浮液的表面张力、固含量和黏度的函数。
②薄膜形成机理 薄膜形成的涂膜机理如图3-22所示[33]。当浸入到悬浮液中的支撑体以一定速度提升脱离悬浮液时,在黏性力的作用下形成一黏滞层。

图3-22 薄膜形成的涂膜机理示意图
1—支撑体;2—悬浮液h0—支撑体顶端的黏滞厚度; h(x)—距支撑体顶端x处的黏滞层厚度
黏滞层的厚度(h)主要与悬浮液的黏度(μ)和提升速度(νw)有关,干燥后的膜厚度还与悬浮液固含量有关。同时黏滞层形成时还受到悬浮液表面张力(γ)和重力(ρg;ρ为悬浮液的密度)的影响。即:
(3-25)
对于稳定的提升过程,Scriven[34]假设悬浮液为牛顿(Newton)流体,由Navier-Stokes方程导出了如下的关系式:
(3-26)
Landau和Levich解式(3-26)得到:
(3-27)
即,黏滞层的厚度与提升速度(νw)的2/3次方成正比,与黏度(μ)的2/3次方成正比,仅与表面张力(γ)的1/6次方成反比。
由牛顿流体导出的式(3-27)并不适用于非牛顿流体,但导出非牛顿流体的表达式还十分困难。实际配制的悬浮液多为非牛顿流体,因此还必须借助实验手段,进一步考虑流变性质的影响。
涂膜过程中重要的是控制膜厚度的均匀性,这对商品膜的生产过程,显得尤为重要,上述成膜机理表明:对于干燥的多孔支撑体,采用浸浆法涂膜,膜的形成既有毛细过滤的贡献,也有薄膜形成的贡献。在毛细过滤过程中膜厚度受浸浆时间的影响,因此实际操作过程中必须准确控制浸浆接触时间,这对于长达1m的膜而言较为困难;而悬浮液的黏度、固含量和提升速度容易控制,因此利用薄膜形成机理在技术上有可能获得厚度均匀的膜。对多孔支撑体进行表面处理或预浸润,可以消除毛细吸力。实验对比了氧化铝悬浮液在多孔玻璃、多孔支撑体和表面经硅烷化处理后的支撑体上涂膜时,膜厚度与提升速度(同时包括浸浆接触时间)的关系,结果见图3-23[23]。

图3-23 膜厚度与提升速度的关系
值得注意的是薄膜形成机理虽然可以在涂膜时控制膜厚度的均匀性,但在干燥过程中膜厚度会在重力作用下发生变化。对此通常是利用非牛顿流体的性质,如低剪切速率下悬浮液具有高剪切压力的特点避免膜厚度的变化。另外对支撑体进行适当的处理,消除毛细管力可避免因粒子向支撑体中渗透所造成的渗透阻力增大问题。然而采用薄膜形成机理涂膜还应考虑到膜与支撑体的结合强度的问题。利用毛细过滤机理涂膜则对提高膜的结合强度是十分有效的,而且还可对浸涂的滤饼层或凝胶膜进行浓缩,提高其干燥时的强度。
3.3.4 湿化学法
近年来随着纳米技术的发展及粉体加工工艺的突破,有学者将粉体制备中湿化学法工艺与传统的粒子烧结法制备陶瓷膜工艺进行结合,形成了一种新型的制膜工艺,该工艺可以大幅缩短制膜流程和周期。美国Rice大学的研究人员[35,36]以纳米颗粒为原料,采用悬浮粒子烧结法制备陶瓷超滤膜,该工艺降低了成膜过程对支撑体的依赖度,只需浸涂一次即可形成完整的超滤膜。另一些研究者,将湿化学法制备纳米颗粒路线中干燥前的纳米晶粒悬浮液作为悬浮粒子烧结法制备陶瓷膜路线中的原料,再经过制膜液的配制、涂膜、干燥以及烧结过程制备出TiO2和ZrO2陶瓷超滤膜。其工艺流程如图3-24所示。

图3-24 湿化学法制备陶瓷膜流程图
汪信文等[37]采用湿化学法制备了ZrO2陶瓷超滤膜,结果表明应用这种方法制备的陶瓷膜完整无缺陷,孔径为16nm左右,对葡聚糖的截留分子量为42000Da。Ding等[38]以纳米颗粒悬浮液作为涂膜的制膜液,成功制备出了TiO2超滤膜,所制得的膜表面完整无缺陷,纯水通量达到860L/(m2·h·bar)(单管)、430L/(m2·h·bar)(19通道)。通过牛血清蛋白(Mw为67000)体系对其截留性能的考察,截留率达到90%以上。
水热法作为纳米粉体制备过程中一种比较常见的湿化学法,其突出的优势就是可以在保证粉体高纯度的同时能够保证粉体良好的分散性能。因此,有一些研究者将水热法与传统的制膜方法相结合,以一种耦合的湿化学法制备陶瓷膜。Suresh等[39]通过水热法在陶瓷支撑体上涂覆TiO2与γ-Al2O3粒子,制备出TiO2/γ-Al2O3复合膜,平均孔径为0.041μm,并且在水-油体系应用中表现出良好的分离性能。Basumatary[40]等通过水热方法在陶瓷载体上沉积沸石,形成的FAU沸石堆积膜孔径为0.153μm,对水溶液中Cr的脱除率可达82%。
这些研究成果都是通过湿化学法能够与传统的制膜方法相结合,形成一种新颖的制膜方式,显现出了突出的优势,并且这种方法相比于传统的制膜方法更适合规模化工业生产。
3.3.5 溶胶-凝胶法
严格意义上来说,有液相参加的并通过化学反应来制备材料的方法统称为湿化学法。溶胶-凝胶法也是湿化学方法中的一种,常用于小孔径膜材料的制备。与常规粒子烧结法相比,虽然粒子烧结法可通过调节粒子大小、烧结温度等参数制备不同孔径和孔隙率的多孔膜,具有结构可调等优点。但由于传统的方法如机械研磨法无法制备纳米级的超细粒子,因此该方法尚限于制备微滤孔径的膜,难以用来制备超滤范围的小孔径膜。因而,溶胶-凝胶技术作为一种可以制备出纳米级超细粒子的制膜技术逐步发展起来。目前,绝大多数商品化的γ-Al2O3、TiO2和ZrO2超滤及纳滤膜都是采用这一方法制备的。溶胶-凝胶法制膜过程中的关键在于控制膜的完整性,即避免针孔和裂纹等缺陷的产生。大量的研究结果表明不仅膜的完整性,而且膜的孔径都取决于溶胶、支撑体的性质以及凝胶膜的干燥和热处理条件。
3.3.5.1 溶胶的制备
Sol-gel法以醇盐如Al(OC3H7)3、Al(OC4H9)3、Ti(i-OC3H7)4、Zr(i-OC3H7)4、Si(OC2H5)4、Si(OCH3)4或金属无机盐如AlCl3为起始原料,通过水解,形成稳定的溶胶。然后在多孔支撑体上浸渍溶胶,在毛细吸力的作用下或者经干燥,溶胶层转变为凝胶膜,热处理后得到多孔无机膜,该过程存在溶胶到凝胶的转变,溶胶-凝胶制膜方法由此得名。
根据水解工艺,可形成两类不同性质的溶胶。一种是醇盐在水中快速完全水解形成水合氧化物沉淀,加入酸等电解质以得到稳定的胶粒溶胶;另一种是醇盐在大量有机溶剂中加入少量水,控制水解反应,形成聚合溶胶[41]。前者制备的溶胶也称物理溶胶,其制备过程称为DCS路线;而后者制备的溶胶称为化学溶胶,其制备过程称为PMU路线,两种路线制备膜的过程如图3-25所示。

图3-25 Sol-gel法制备多孔无机膜过程[42]
DCS法制备的溶胶,其初级粒子粒径在3~15nm,在陈化过程中初级粒子还会进一步团聚,所形成的次级粒子粒径可达1000nm。利用超声波或加入适当的电解质使粒子带电,可控制团聚度,从而控制胶粒的大小和分布。
采用适当的合成条件,PMU法可以得到粒径在3nm以下的粒子。反应过程水的加入方式是十分重要的,第一种是向醇盐溶液中缓慢地加入水或醇水混合物;第二种是通过有机酸与醇盐溶液反应生成水;第三种是在醇盐溶液中加入碱或水合盐而产生水。尽管PMU法得到的粒子较小,所得到的膜的孔径在2nm以下,但制备工艺要求较为苛刻。
3.3.5.2 涂膜
溶胶在多孔支撑体上的成膜过程,多采用浸渍涂膜技术。在毛细管力的作用下分散介质渗透到支撑体中,胶体粒子在支撑体表面堆积形成凝胶膜,涂膜的动态过程如前所述。溶胶性质、支撑体结构和表面性质以及溶胶添加剂均影响到膜的结构以及完整性。
(1)溶胶性质的影响
胶体性质决定了膜的结构。对于稳定的胶粒溶胶,有利于制备孔结构均匀的膜;而对于聚合溶胶,胶束的聚合度与结构也影响到膜的孔径[4,43,44],如图3-26所示[23]。胶粒溶胶的稳定性取决于胶粒表面电荷的强弱,只有当表面电荷强度足够高,远离等电位点时,才能获得稳定的溶胶,并防止胶粒的团聚,确保膜孔径的均匀性[45],由于制备溶胶过程中多采用无机酸作为解胶剂,过量游离酸将会破坏胶体的存在,因此必须控制适当的pH。

图3-26 溶胶稳定性对膜结构的影响
(2)支撑体结构的影响
研究结果表明:采用浸浆法涂膜,支撑体以下几个因素应予特别注意:
①孔径和孔径分布;
②表面粗糙度;
③润湿性能。
胶体粒子大小应当与支撑体孔径相匹配,否则胶粒直接进入支撑体孔内而得不到连续完整的膜。Leenaars等[13]实验研究了支撑体孔径对成膜特性的影响,结果见表3-8,发现只有当支撑体的孔径与粒子大小相当时才能得到连续的膜。当支撑体表面存在大孔或孔径分布较宽,难于形成连续的涂层,即产生针孔等缺陷,显然孔径分布窄的支撑体也有利于提高膜的完整性和均匀性。当支撑体的孔径一定时,也可通过增大溶胶浓度和在溶胶中添加PVA等聚合物提高溶胶的黏度,以提高成膜性能。尽管支撑体的表面粗糙度有不同的定义,但表面粗糙的支撑体,存在着裂纹或针孔缺陷,也将影响膜的完整性。在图3-27中,支撑体表面的缺陷“传递”到膜层,导致膜不完整。
表3-8 支撑体孔径对膜形成的影响(1.2mol/L Boehmite溶胶)


图3-27 支撑体表面缺陷影响膜的完整性
(a)支撑体表面存在裂纹;(b)支撑体表面存在针孔缺陷
溶胶体系的润湿性能对涂制厚度均匀的膜支撑体十分重要。图3-28表示三种润湿状态下膜与支撑体结合的状况,只有当支撑体表面具有很好的润湿性时,才能确保膜厚度均匀以及干燥过程的稳定性。否则溶胶在支撑体表面上难于铺展,或在凝胶膜的干燥过程中形成局部缺陷。在溶胶中加入适当的添加剂有助于改善支撑体表面的润湿性能,这反映在接触角的变化上,由表3-9可见在Boehmite溶胶中加入PVA可减小接触角,从而改善溶胶与支撑体的润湿性,提高膜的均匀性和完整性。

图3-28 支撑体的润湿性能
表3-9 PVA浓度对Boehmite溶胶接触角的影响

3.3.5.3 凝胶膜的干燥与热处理
干燥和烧结工艺条件直接影响膜的完整性和孔径分布。
(1)凝胶膜的干燥
由于凝胶在干燥过程中会发生弯曲、变形和开裂,从而导致膜缺陷的产生,因此必须严格控制干燥条件[46-49]。凝胶膜的干燥过程主要经历三个干燥阶段:恒速干燥阶段(CRP)、第一减速干燥阶段(FRP1)和第二减速干燥阶段(FRP2),如图3-29所示。

图3-29 氧化铝凝胶膜干燥失水速率[48]
在恒速干燥阶段,凝胶膜中分散剂的蒸发速率与常态时液体的蒸发速率相近。随着分散剂的蒸发,孔结构显露出来,并产生毛细管张力。由毛细管张力所引起的收缩应力会使凝胶膜的骨架收缩,收缩速率取决于分散剂的蒸发速率,一般凝胶膜的体积可收缩为原体积的十分之一[50]。恒速干燥过程,液面曲率逐渐增大,当曲率达到最大时,恒速干燥阶段结束,为该阶段的临界点,毛细管力也相应达到最大。收缩应力的存在使凝胶膜的结构塌陷,当凝胶膜的强度足够高时才能避免裂纹等缺陷的产生。对于胶粒溶胶,凝胶膜的强度主要取决于Van der Waals引力和双电层的排斥力;而对于聚合溶胶,强度主要由胶束的键力决定。另外溶胶中聚合物添加剂所形成的空间位阻作用也可提高凝胶膜的韧性,降低干燥应力。随着蒸发速率下降,进入FRP1阶段。此时骨架收缩停止,蒸发界面进入凝胶膜的主体,并在胶粒表面形成一层连续的液膜,致使凝胶膜呈乳白色。在FRP2阶段,以表面液膜的扩散蒸发干燥为主,凝胶膜逐步恢复干燥前的透明状态。在此阶段,干燥应力缓和,因各孔道间干燥速率的差异、产生应力的差异,使凝胶膜会有所扩张而发生弯曲变形[51]。
干燥过程中所产生的应力是导致膜出现缺陷的原因。为提高膜的完整性,减少凝胶膜的开裂,主要从增强骨架的强度和减小毛细管力两个方面入手。增强凝胶膜骨架强度可通过改变溶胶水解条件[52,53]、对溶胶进行适当的陈化和在溶胶中加入干燥控制剂等方法解决。在水解过程中加速缩聚反应,提高交联度和聚合度,从而提高凝胶膜的强度;利用溶胶的溶解和再沉淀的陈化过程,也可使胶粒之间的作用增强,提高凝胶膜的强度;甲酰胺、丙三醇等干燥控制剂能够抑制水解速率和提高缩聚反应速率,增强凝胶膜的强度,还能够提高胶粒大小的均匀性,从而使干燥时的应力分布均匀,并可缩短干燥时间。然而,为降低干燥控制剂的不利影响,必须选择合适的干燥控制剂种类和控制适当的加入量。
干燥过程中凝胶膜收缩开裂的主要原因在于所产生的毛细管力,因此减小毛细管应力是提高膜完整性的重要途径。依据Laplace方程,毛细管力与分散剂的表面张力成正比,而与孔径成反比。可见孔径越小,毛细作用力越大,防止收缩开裂也就越难,这正是溶胶-凝胶法在制备微孔膜中存在的主要困难。为减小或消除毛细作用力,通常采用低表面张力的分散介质或添加表面活性剂降低表面张力,如以醇作为分散介质[54]、采用超临界干燥或冷冻干燥技术[55]。
(2)凝胶膜的烧结
与粒子烧结法相同,烧结的目的在于获得一定的孔结构,使膜具有一定的机械强度和化学稳定性。一般,干凝胶的烧结包括两个阶段:在相对较低的温度范围内,如300~400℃内,无定形凝胶粒子发生晶型转变,并伴随脱水反应,生成无水粒子,有机添加剂也在该阶段被烧尽。这一阶段即通常所称的灼烧过程。灼烧得到的氧化物粒子相互以点接触方式进行堆积,升高温度,在接触点处粒子之间形成“颈”连接,这即所谓的烧结初期。随着温度的升高,“颈”变宽,相应膜的强度提高,如图3-30所示[23]。在凝胶膜的烧结过程中,随着温度的升高,膜的孔径增大,孔径分布变宽,见图3-31[13]、图3-32和表3-10。烧结时间也是影响膜孔结构的因素之一,由表3-11的结果可见随着烧结时间的延长,膜的孔径增大,比表面积下降。

图3-30 烧结过程示意图
R—粒子半径;x—颈宽;路径1—从粒子边界层向颈表面的质量传递;ρ—颈部的曲率

图3-31 烧结温度对γ-Al2O3膜孔径分布的影响
表3-10 干燥和烧结温度对SiO2膜孔径的影响


图3-32 烧结温度对γ-Al2O3膜孔径分布的影响
表3-11 烧结时间和温度对氧化铝膜孔结构的影响[44,56]

表3-12 烧结温度对TiO2和CeO2膜孔结构的影响[44,57]

①锐钛矿相;
②金红石相;
③圆柱孔模型;
④团聚溶胶粒子(10nm;超声波处理,激光散射法测定);
⑤检测不出;
⑥Si稳定的TiO2;
⑦初级粒子。
3.3.6 阳极氧化法
20世纪20年代为提高铝制品表面耐磨、耐腐蚀以及着色等性能,发展出阳极氧化的方法。该方法是对金属或合金的一种电化学氧化处理手段,将待处理的金属或合金置于相应的电解液中,由于外加电场的作用,在金属或合金(阳极)表面形成一层氧化膜。
1959年Hoar和Mott将该方法用于氧化铝膜的制备,并深入研究了铝的阳极氧化过程与膜结构的关系[58]。Smith[59]的进一步工作奠定了阳极氧化法在无机膜制备中的基础。阳极氧化法是将高纯度金属箔(如铝箔)置于酸性电解质溶液(如H2SO4、H3PO4)中进行电解阳极氧化。在氧化过程中,金属箔的一侧形成多孔的氧化层,另一侧金属被酸溶解,再经适当的热处理即可得到稳定的多孔结构氧化物膜。
阳极氧化法制出的膜具有近似直孔的结构,控制好电解氧化过程,可以得到孔径均一的对称和非对称两种结构的氧化铝膜。英国的Anotec Seperation公司采用阳极氧化法生产出两种结构氧化铝商品膜。一种为孔径200nm的对称膜,其孔隙率高达65%以上;另一种为非对称结构,分离层孔径为25nm,两种膜厚均在60μm左右。图3-33、图3-34分别为对称和非对称阳极氧化铝膜的断面结构照片。Mitrovic和Knezie采用阳极氧化法制备出了非对称超滤和反渗透氧化铝膜,膜主体孔径为200nm左右,而分离层只有1.5nm。Masuda等首次报道了采用两步法合成多孔阳极氧化铝膜,他们制备的氧化铝膜由高度有序的六角密排的孔道组成,随后的研究表明两步法工艺制备出的氧化铝膜有序度明显优于一步法。王宁等[60]采用两步阳极氧化法制备了双面氧化铝膜。在制备过程中,双面膜中间的铝基被氧化而溶解到溶液中,从而得到了大面积双面氧化铝膜。孙晓霞等[61]通过在草酸溶液中加入不同有机醇的方法来有效减少在氧化过程产生的大量热量,采用强烈氧化法快速制备了高度有序的氧化铝膜。

图3-33 对称阳极氧化铝膜

图3-34 非对称阳极氧化铝膜
非对称氧化铝膜在气体、液体分离[62],尤其是生化产品的精制等方面有着一定的应用潜力。但是阳极氧化法制备的氧化铝膜缺少支撑体,膜的强度较低,所以仅用来制备平板状实验室用膜和小面积的商品膜。
3.3.7 分相法
分相法首先由Corning公司开发,用于制备氧化硅多孔玻璃膜。分相法利用硼硅酸玻璃的分相原理(见图3-35),将位于Na2O-B2O3-SiO2三元不混溶区内的硼硅酸玻璃在1500℃以下熔融,然后在500~800℃进行热处理,使之分为不混溶的Na2O-B2O3相和SiO2相,再用5%左右的盐酸、硫酸或硝酸浸提,得到连续又互相连通的网络状SiO2多孔玻璃[63]。常见的Vycor玻璃膜就是利用这一方法制备的,其孔径分布见图3-36,平均孔径在4nm左右。

图3-35 Na2O-B2O3-SiO2体系相图

图3-36 Vycor玻璃膜的孔径分布(500℃热处理5h)
由于玻璃表面存在活泼的硅氧基团,使得膜孔表面在高温下不够稳定。采用化学改性的方法进行“钝化”处理,将硅氧基团中“≡Si—C≡”转化为“≡Si—O—C≡”,可提高膜的热稳定性。处理方法见图3-37。Maddison等[64]通过TiCl4浸渍多孔膜,热处理得到TiO2改性多孔玻璃膜。Eguchi等[65]用相似方法制备出ZrO2改性管状玻璃膜、膜孔径在20~2000nm之间。分相法可以通过控制配料组成,分相温度和酸抽提条件制备出孔径在20~2000nm的多孔玻璃膜。原料中Na2O/B2O3比例越大,分相温度越高,膜孔径越大;提高分相温度、延长分相时间,则膜的孔径分布变宽。

图3-37 玻璃膜的表面改性
分相法得到的膜孔径分布窄、比表面积可高达500m2/g,还可调节膜表面的Zeta电位以及与水的润湿性,可用于气体分离和膜反应过程。另外高温下的玻璃熔融体容易成型,可以制备出纤维或管状膜。但受制备技术的限制,膜的进一步薄化和复合十分困难。因此,对称结构的多孔玻璃膜因渗透阻力较大,实际应用受到了一定的限制。
3.3.8 有机聚合物热分解法
在适当条件下进行分解碳化,也可以将有机膜制成多孔无机膜。如用纤维素、酚醛树脂、聚丙烯腈(PAN)等有机膜可以制备碳分子筛膜,用硅橡胶可以得到硅基质多孔无机膜。
Koresh和Soffer[66,67]将PAN纤维膜在惰性气氛中分解,形成致密膜,然后控制氧化处理得到多孔膜。研究发现PAN在200~300℃低温的惰性气氛中热处理形成环状结构;而在600℃下分解碳化,得到的碳环为平面型致密结构。在真空条件下,热处理分解可制备超微孔隙纤维膜。碳膜可以用中温(400~500℃)氧化活化的方法增大膜孔。Lee和Khang[68]也研究了管状硅橡胶膜的热分解过程。在600~800℃,于N2或He惰性气氛中进行处理,再在500~900℃下进行氧化处理,最后形成完全交联的SiO2膜。BET测定膜的比表面积、孔隙率分别达到100m2/g量级和50%左右,孔径在5~10nm。Zheng和Yeap等[69]研究了用不同的烧结温度制备一系列不同结构的碳分子筛膜,并且得到了很好的应用。
由于有机膜在热分解过程中的收缩率很大,如硅橡胶膜分解时收缩率在10%以上。膜层和支撑体之间的结合力难以承受膜层收缩产生的应力,容易导致膜层出现缺陷。因此,采用有机聚合物热分解法制备非对称膜存在一定困难。
3.3.9 多孔膜的改性
采用浸渍或吸附的方法可将液相中改性组分沉积在膜的表面和膜孔内,也可用薄膜沉积技术[包括物理气相沉积(PVD)、化学气相沉积(CVD)和超临界流体沉积技术]对膜进行表面改性[45]。膜经改性后,一方面可进一步减小其孔径,见表3-13;还可以改变膜孔表面的化学性质,从而改善膜的分离性能。
表3-13 膜改性结果

①α-TiO2金红石型氧化钛。
表面接枝改性也是一种常见的膜材料表面性质调控手段,可以用来提高膜材料的渗透性能和抗污染性能。李雪等[70]通过两步表面接枝法成功制备了两性离子改性的陶瓷复合膜,提高了膜材料的亲水性,使得陶瓷膜的纯水通量提高了20%。同时,由于膜表面接枝的两性离子材料具有良好的抗蛋白吸附性能,使陶瓷膜的抗污染性能也得到了提升,过滤BSA溶液时的渗透通量提高了30%。表面接枝改性通常是单分子层接枝,其对孔径较大膜材料的孔结构影响不大。但当陶瓷膜的孔径只有几纳米时,表面接枝层厚度将对膜孔径产生较大影响。张婷等[71]通过在介孔陶瓷膜表面接枝亲水性的氨基硅烷对孔径进行调节。相比于未改性前,虽然陶瓷膜的孔径减小仅为约1nm,但截留分子量由2600Da显著减小到1000Da。
3.3.10 致密膜的制备
致密无机膜主要是金属膜和陶瓷膜。致密金属膜主要用于氢气的分离与纯化,其中最著名的是金属钯和钯合金膜,材质包括Pd-Ag、Pd-Cu、Pd-Au、Pd-Y、Pd-Ag-Au-Ni、Pd-Pt等,钯合金膜的工业化应用已有半个多世纪,至今仍被广泛用于超高纯氢的生产。此外,在核工业中钯合金膜还被用于氢同位素的分离与纯化。此外,金属钯和钯合金膜还可用作催化制氢反应器,形成反应与分离的耦合,不仅简化了设备与操作,还打破了反应平衡的限制,提高了反应产率。
除钯合金膜之外,其他金属膜(如Nb、Ta、Ni、Pt膜)和不含钯的合金膜也大量地、持续性地被报道,但是一直处于学术研究阶段,因为它们都或多或少地存在表面钝化、透氢率低、易中毒等致命问题,难以实现工业应用。除氢气分离外,将金属银膜用于氧气分离也有文献报道。致密金属膜都有良好的韧性,因此可以轧制成金属平板膜或拉制成金属膜管。需要强调的是,这里所说的“膜”是指具有选择性渗透作用的分离膜“membrane”,而非普通的金属薄膜或金属箔“film”,因此本节也不涉及普通金属薄膜的性能、用途和制备工艺。
传统自支撑(self-supporting)型金属膜面临成本高、膜强度差、氢气渗透率低等难题。氢气渗透率与金属膜厚度呈反比,降低膜厚不仅能够提高氢气渗透率而且还可以节约贵金属用量,但是这又受到制备难度、成本、操作便利性等因素的制约。因此,将金属膜沉积到高强度的基材并形成复合膜(composite membrane)或负载型膜(supported membrane),也就成为自然而然的选择。金属膜的基材一般是多孔陶瓷和多孔不锈钢材料。致密金属基材也有大量报道。例如,金属Ta的氢气渗透率远远高于金属Pd,将Ta片的两侧镀上金属Pd就可以形成Pd/Ta复合膜,还解决了Ta膜的表面钝化问题。但是,类似于Pd/Ta复合膜的此类材料都难以实现工业化应用,除制造难度大、成本高外,使用过程中还面临金属间的相互扩散问题,因为金属膜在氢气分离过程中的工作温度一般为300~400℃。
另一类致密无机膜则是具有选择透氧功能的金属氧化物膜,如氧化钇稳定的氧化锆(YSZ)固体电解质膜和混合导体的钙钛矿型致密膜。透氧膜在高温富氧燃烧、燃料电池、氧化反应以及膜传感器方面具有发展和应用潜力。但致密膜的主要不足在于膜的渗透通量较小,只有将其超薄化,制出支撑结构的膜才具有实用竞争力。
3.3.10.1 致密金属膜的制备
致密金属膜分为自支撑型和负载型。自支撑型致密金属膜(例如工业上广泛使用的钯合金膜)的制备方法主要是冷轧法,也可以通过其他方法制备平板膜,例如将金属薄膜沉积在表面光洁的镜面上然后进行剥离。负载型金属膜的制备方法更多,如电镀、化学镀、化学气相沉积、物理气相沉积等[72],但是化学镀法是目前报道最多、效果最好的方法。
(1)冷轧法
将炼制合金所需元素进行高温熔融、铸炼和均质化,获得制膜原材料,经过反复的冷轧和退火处理使金属膜达到预期厚度。制备过程中,随着膜厚的减小,需要小心杂质污染问题。碳、硫、硅、氯、氧等微量元素可导致其机械强度下降,因此也对原料纯度和制造过程中的外来污染提出了更高要求。冷轧时通常会导致晶格错位,导致膜材料硬度和脆性增加,因此在轧制到一定程度之后就必须进行退火。
(2)电镀法
电镀法原理是控制直流电压和温度,将金属或金属合金沉积在阴极的支撑体上形成薄膜[73]。金属钯比较容易在平板和管式支撑体上镀膜。Chen等[74]在多孔不锈钢表面通过电镀法制备了钯银合金膜,350℃以下氢气的渗透量达到28.5mL/(min·cm2)。Itoh等[75]采用脉冲电流的方法制备出钯合金膜,在多孔玻璃支撑体上制成的膜用于氢气混合物的分离。
钯膜的厚度主要通过电镀时间和电流强度加以控制,膜的厚度可控制在几微米到几毫米范围。然而对于合金膜,由于各种金属离子的沉积速率的差异,制备面积较大的膜会出现组分分布不均的问题。
(3)化学镀法
化学镀基本原理是利用控制自催化分解或降解亚稳态金属盐,在支撑体上形成薄膜。对于钯膜,使用的金属盐有Pd(NO3)4(NO2)2、Pd(NH3)4Cl2,常用的降解(催化)剂为肼或次磷酸钠。通常,支撑体还需预处理以带有钯核,从而降低液相中的自催化反应难度。该方法可在复杂表面形成厚度均匀、强度较高的膜,钯及其合金膜均可采用该方法制备。
(4)化学气相沉积(CVD)法
在化学气相沉积过程中,控制温度等条件,气态的金属化合物在支撑体表面发生化学反应,经成核、生长而形成薄膜[76,77]。Liguori等[78]采用CVD法分别在多孔不锈钢和多孔氧化铝载体上制备出平均厚度约为10μm和7μm的钯膜,H2/N2的分离因子分别为11700和6200,可以稳定运行600h以上。Feurer等[79]利用等离子体强化沉积过程,在200℃以下的温度制备出厚度只有10~300nm的钯膜。
(5)物理气相沉积(PVD)法
在PVD过程中,固体金属在高真空(1.3mPa)下蒸发,冷凝沉积在低温支撑体表面并形成薄膜。PVD法在制备金属及其合金膜中是一种非常实用的方法,物理气相沉积法可分为真空沉积、溅射沉积和粒子束沉积三种。
金属在坩埚中被加热至或高于其熔点,蒸气分压足以产生较高的沉积速率。钯在1550℃下很容易蒸发,并具有良好的沉积性能[73]。采用热蒸发法可以在多孔支撑体上制备出钯、银和铜膜。然而由于各组分的蒸气分压和蒸发速率差异,沉积金属合金尚有一定的困难。合金膜通常采用交替沉积或使用多个蒸发源的方法制备。溅射过程并不需要对金属进行加热,溅射靶上的金属原子被高速的氩等离子轰击出,并在支撑体上沉积。该方法的优势在于原子间的蒸发速率相近,适用于制备合金膜;蒸发速率较低,可制备超薄膜,另外低温也是其一个优点。使用物理气相沉积方法,膜层与支撑体的结合强度往往不高,因此必须对支撑体进行适当的预处理。采用上述方法也可在无机多孔膜上制备金属复合膜,这可大大提高金属膜的机械强度。
3.3.10.2 氧化物致密膜的制备
氧化物致密膜以对称结构为主,常采用挤出和等静压法成型。其制备过程包括粉料制备、成型和干燥、烧结三个基本步骤,如图3-38所示。下面以钙钛矿型混合导体膜为例介绍氧化物致密膜的制备方法和过程。

图3-38 氧化物致密膜的制备过程
(1)粉料制备
粉料制备是制备钙钛矿型透氧膜的关键步骤之一。对于粉料的要求包括平均粒度和分布以及晶型结构。目前文献中报道的方法主要为有机酸配位热分解法及高温固相反应法。
①有机酸配位热分解法[80] 又称“液体混合技术”。将所含阳离子的盐或氧化物溶于有机酸中配成一定浓度的溶液,经高温热分解、热处理,碾磨后得到一定粒度的粉料。该方法的优点在于粉料的化学均匀性好、粉料粒度细;但操作复杂、步骤多,一次粉料的制备量小。
②高温固相反应法[81] 是将含有所需元素的氧化物或硝酸盐、碳酸盐混合后,在高温下利用固相扩散-反应形成特定晶相结构的材料,再进一步研磨得到一定粒度粉料的一种粉体合成方法。为缩短反应时间,提高组分的分布均匀性,一般在高温反应前需进行适当的研磨,以减小粉料的粒度。高温固相反应法的优点是操作简单,不需要特别设备,合成粉料组分范围宽;但存在粉料粒度大及分布宽、比表面积小以及化学均匀性差的不足。
(2)成型
目前文献中报道的钙钛矿型氧化物膜主要有片状、单管和中空纤维型。其中片状膜主要采用干压成型或流延成型技术,单管膜主要采用注塑和挤出成型技术,而中空纤维主要采用纺丝成型技术。其中,由于中空纤维型钙钛矿膜具有装填密度高、渗透通量大等特点,近年来受到越来越多的关注[82-84]。
为提高透氧性能,获得有实用价值的透氧膜,减小膜的厚度,开发出对称或复合支撑膜一直是人们关心和研究的热点之一。制备支撑膜的问题在于膜材料与支撑体的化学相容性以及热膨胀性等因素。到目前为止各国研究者尝试过浸渍和喷涂等方法,但仍难得到致密或化学组成均匀的非对称膜。
(3)干燥、烧结
致密性是钙钛矿型致密膜制备过程的关键问题,影响致密化过程的因素主要包括:煅烧温度及保温时间,粉体粒径,添加剂和成型技术四个方面。一般钙钛矿型致密膜的热处理条件控制在1100~1300℃的煅烧温度,保温5~10h以及2℃/min的升温和降温速率。
在致密化过程中膜伴随着明显的收缩,控制不当会导致膜出现裂纹缺陷。Itoh等[85,86]用显微镜观察测定了烧结温度对膜尺寸收缩的影响,结果见表3-14,随着烧结温度的提高,膜的垂直和水平方向的收缩率均增加,表明膜趋于致密;但也不难发现垂直和水平方向的收缩率并不一致,这主要是由重力的影响所导致的。此外,烧结方法的确定还须考虑到材料的化学稳定性和结构稳定性。
表3-14 钙钛矿膜收缩率与烧结温度的关系

3.3.11 无机膜缺陷修复技术
膜材料在制备过程中,其膜表面不可避免地会存在一定数量和大小的缺陷。这些缺陷的存在对膜性能会产生严重影响,且膜孔径越小缺陷影响越大。因而,开发合适的无机膜材料缺陷修复技术至关重要。
制膜过程中产生缺陷的原因是十分复杂的,除了以上的影响因素外,还存在膜厚效应,即所涂膜的厚度也会影响其完整性。膜厚度越大,干燥过程中收缩应力分布越不均,也就越容易出现裂纹缺陷;相反厚度过小,支撑体的缺陷会传递到膜上,导致膜不连续。当支撑体一定时,存在一最大允许膜厚度(或临界厚度)。表3-15为在孔径0.2μm铝支撑体上氧化铝、氧化钛和氧化硅三种膜的最大允许厚度。
表3-15 氧化铝、氧化钛和氧化硅膜的最大允许厚度(孔径0.2μm,α-Al2O3支撑体)

制膜过程中出现裂纹、针孔缺陷往往是难以避免的,因此修复膜的缺陷显得十分必要。重复浸涂-干燥-烧结的制膜过程多次,可以逐步降低膜的缺陷,提高膜完整性。重复过程中,一方面可降低支撑体的表面粗糙度,以减少缺陷;另一方面利用缺陷吸浆速率大的特点,使缺陷得以“自我”修复(self-repairing)。
针对薄壁支撑体(如中空纤维),由于其毛细作用力弱,使用常规的浸浆方法涂膜,不能够得到一层完整无缺陷的膜层。Okubo[87]与Chu[88]都是采用终端过滤的方法,在多孔陶瓷中空纤维支撑体上制备了一层无缺陷的膜层。Zhu等[89]采用改进的浸浆法,结合毛细吸浆作用和表面剪切作用,在底膜上实现了一种动态的颗粒沉积,制备出表面均一且无针孔等缺陷的毛细管膜层,膜层的最大孔接近膜的平均孔径且孔径分布很窄。