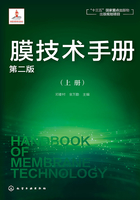
3.5 无机膜在分离和净化中的应用
无机膜的应用主要涉及液体分离与净化,应用范围包括食品工业、医药工业、生物工程、化学工业、石油化工等。在气体分离领域应用主要包括气体(空气)的净化和气体组分的分离,发展前景十分广阔。
3.5.1 在食品工业中的应用
膜过滤在食品工业中的应用非常广泛,无机膜在食品领域的规模应用始于1980年。得益于研究学者们的不断突破,膜技术在近20年得到了突飞猛进的发展。据中国膜工业协会相关数据显示,2013年食品饮料行业共安装无机陶瓷膜约0.65万平方米,2014年为0.75万平方米。预计2020年无机陶瓷膜在国内食品饮料领域应用的市场空间将超过3万平方米。微滤、超滤技术的应用愈来愈广,纳滤技术也逐步成熟并且呈现出了突出优势,促使无机膜分离技术逐步应用于无菌过滤、蛋白质浓缩、果汁浓缩、酒精的澄清以及饮用水的净化等诸多食品制造加工领域。
3.5.1.1 在奶业中的应用
陶瓷微滤膜和超滤膜技术被大量用于牛奶和乳清的生产过程,其主要优点是可耐较高的操作压力,膜不易压密,可以进行酸/碱清洗,并能承受高黏度流体的强剪切力。典型应用实例见表3-18。
表3-18 无机膜在奶业中应用实例

在奶业应用中,膜的污染主要来源于蛋白质在膜面的吸附,使用硝酸、磷酸和氢氧化钠、次氯酸钠、过乙酸等溶液对膜进行化学清洗可恢复膜的通量。
3.5.1.2 蛋白质的浓缩
蛋白质的浓缩和回收是无机膜在食品工业的另一主要应用领域。无机膜优异的化学稳定性和高机械强度,可以通过高压反冲以延缓蛋白质对膜的污染过程,同时采用酸/碱交替化学清洗使膜完全再生,这些特点使得无机膜在蛋白质加工过程具有明显的优点。但由于蛋白质加工一般需用超滤膜,无机膜的高成本、低装填面积限制了这一领域的大规模应用,目前主要工作大多处于实验研究之中,见表3-19。
表3-19 无机膜在蛋白质加工过程中的应用

3.5.1.3 果(蔬菜)汁澄清
传统的果汁澄清方法需要经过多步的过滤,并需要助滤剂等。膜技术的应用对于提高果汁含量、降低操作成本是十分有意义的,无机膜在果汁过滤中逐渐显示其优越性。表3-20是无机膜在果汁过滤中的应用实例,表3-21是无机膜过滤几种果汁的典型操作参数。就目前现状而言,果汁过滤是无机膜应用的重要领域之一,商品化的成套装置规模已达160m2以上。
表3-20 无机膜在果汁澄清过滤中的应用实例

表3-21 无机膜过滤几种果汁的典型操作参数

无机膜在果汁应用中对膜产生污染的物质主要为多糖。苹果汁澄清中膜的再生采用碱溶液冲洗、酸漂洗的方法,也可采用蒸汽灭菌的方法[114,115]。
3.5.1.4 饮用水的净化
无机膜可用于地下水和地表水的净化过程中,除去水中的颗粒、细菌及某些重金属污染物。欧洲尤其是法国自1984年以来,将无机膜与其他常规过滤方法相结合用于生产饮用水的装置已有多套,其产水量从7m3/h到120m3/h不等。0.2μm的陶瓷膜处理地表水前后的水质比较见表3-22,地表水经一级过滤即可达到饮用水要求。如果水中存在低分子有机物,则可以将陶瓷微滤膜与吸附过程相结合,生产出符合饮用水要求的净化水,图3-51是我国自主开发的吸附-陶瓷膜净化水集成装置。
表3-22 0.2μm陶瓷膜处理地表水前后的水质


图3-51 吸附-陶瓷膜净化水集成装置
3.5.1.5 酒的澄清过滤
采用无机膜错流微滤可以一步完成传统制酒业中的原酒的澄清、灭菌和稳定过程。其主要应用见表3-23,典型的陶瓷膜澄清红酒的操作参数见表3-24。无机膜具有良好的化学稳定性及耐热性,在啤酒澄清过滤中应用前景广阔。传统的啤酒澄清过程为:发酵液→离心分离→硅藻土过滤→平板过滤→终端过滤→灭菌过滤,而采用陶瓷膜则仅需两步过程即可完成:发酵液→离心过滤→陶瓷膜错流微滤。采用陶瓷膜澄清啤酒不仅可以减少操作过程,而且处理后的啤酒风味更佳,尤其可延长生啤酒的保质期。
表3-23 无机膜在酒的澄清过滤中的应用

表3-24 陶瓷膜澄清红酒的典型操作参数

注:膜孔径为0.2μm,Membralox的Al2O3陶瓷膜。
3.5.2 在生物化工与医药工业中的应用
无机膜在生物化工和医药工业中的应用主要用于分离和回收原生质,微生物和酶及生物发酵液的澄清、脱色活性炭的回收等,膜生物反应器则处于开发研究阶段。生物化工和医药工业是无机膜应用的重要领域,膜的污染控制和清洗方法的开发研究是进一步推广的技术基础。
3.5.2.1 发酵液的过滤
采用无机膜对发酵液进行错流过滤,可以将澄清与除菌过程一步完成,得到的澄清液清澈透明,有利于提高产品质量,简化后续提取过程。与传统的袋式过滤和离心过滤相比,无机膜过程可以实现连续密闭操作,具有明显的技术优势。发酵液过滤的污染主要来自生物在膜面的吸附和杂质对膜孔的堵塞,一般的再生方法是采用反冲技术延缓膜过滤通量的衰减,采用碱洗技术对膜进行再生。表3-25是有关发酵液过滤的若干研究报道。图3-52是南京工业大学膜科学技术研究所与江苏久吾高科技股份有限公司研制生产的用于生物发酵液过滤的成套装置。
表3-25 发酵液的过滤


图3-52 头孢霉素生产中的陶瓷膜装置
3.5.2.2 血液制品的分离与纯化
血浆的净化必须在低温下进行,以防止细菌的污染和蛋白质的变性,陶瓷微滤膜是合适的选择。影响陶瓷膜过滤的重要因素包括血浆的粒度以及血浆中细胞、蛋白质的浓度、种类、大小、形状等,过滤过程尚受到膜污染和凝胶层的限制。采用化学清洗方法可以使陶瓷膜得到完全再生。采用陶瓷膜对血浆净化在技术上是可行的,但其应用还必须得到卫生部门的认可,表3-26是部分研究工作。
表3-26 血液制品的分离和纯化

3.5.2.3 中药提取与纯化
中成药制备大多需经煎煮水提,水提液中含有悬浮及可溶性杂质,必须除杂处理后方可制成各种剂型成药。传统水提醇沉工艺存在一些不足之处:中药总固体及有效成分损失严重,乙醇用量大且回收率低,生产周期长等。用无机陶瓷膜对中药水提液进行澄清处理有显著优点:水提液无需冷却可直接过滤,减少生产环节,膜的再生方便;除菌彻底,膜本身可直接高温灭菌;无论中药水提液性质如何,对膜本身没有影响;对中药有效成分基本无截留等。
对水提液进行澄清处理,20世纪80年代初日本汉方制剂专利中采用的是微滤澄清再超滤除杂。随着中成药口服液的大量开发,中药水提液的澄清技术愈发重要,采用微滤膜进行中药水提液的澄清处理有广阔的应用前景[142-145]。邢卫红等[146]考察了皮康宁复方中药水溶液的微滤澄清的工艺参数,并获得了陶瓷膜在中成药生产中应用的成套装置设计数据和工艺操作参数。采用的陶瓷膜平均孔径为0.2μm,实验流程如图3-53所示。

图3-53 中药澄清实验装置流程图
1—储槽;2—离心泵;3—流量计;4—膜组件;5—液体缓冲罐;6—气体缓冲罐;7—氮气钢瓶
研究了操作压力对膜过滤通量的影响关系,在较低的压力范围内随着压力的增大膜通量随之增大;而在较高的压力下,随压力的增大膜通量的变化趋于平缓,适宜的操作压力为0.06~0.1MPa。膜面流速对过滤通量有一定影响,随着膜面流速的增大。料液的湍动程度及沿膜面的剪切力相应增加,膜面的凝胶阻力减小,膜通量随之增大,但流速过高,易产生大量泡沫,操作不稳定,通量有起伏,考虑到动力消耗,适宜的流速为2.5m/s左右。
温度升高有利于过滤通量的提高,在10~45℃温度范围内,基本呈线性关系,如图3-54所示,在表面流速为2.48m/s,操作温度为40℃时,过滤通量为80L/(m2·h·bar)。图3-55给出的是不同表面流速对通量衰减的影响,过滤通量基本上均是在10min之内下降,此后通量基本稳定,图3-56给出的是10℃下随表面流速改变而改变的通量,开始操作时表面流速为2.48m/s,过滤通量能维持在一个较高的水平,随后降低表面流速过滤通量也随之下降,当表面流速增大为2.98m/s时,过滤通量略有上升,当表面流速又恢复到2.48m/s时,过滤通量基本又恢复至45L/(m2·h·bar)左右,这说明较佳的表面流速为2.5m/s左右。实验研究表明浓缩比对过滤通量和澄清效果基本没有影响,结果见表3-27和表3-28。通过陶瓷膜的微滤过程,药液中的悬浮杂质已基本除去,达到了澄清目的,为后续工艺开发奠定了基础。

图3-54 操作温度对过滤通量的影响
(1bar=105Pa)

图3-55 不同表面流速对过滤通量的影响

图3-56 过滤通量随时间的衰减曲线
1—u=2.48m/s;2—u=1.96m/s;3—u=1.65m/s;4—u=2.98m/s;5—u=2.48m/s
表3-27 浓缩比对过滤通量的影响

表3-28 浓缩比对浊度、吸光度、黏度的影响

陶瓷膜具有优异的化学稳定性和良好的机械强度,在中成药制备过程中的突出优点在于其抗污染能力强,对料液的前处理要求不高,膜可以反复再生,操作过程稳定,产品质量能够得到充分保证,是值得大力发展的陶瓷膜应用领域,同时也是中成药制备技术的重要发展方向之一。
3.5.3 在环保工程中的应用
随着环境保护意识的提高和工业废水排放标准的严格化,膜分离作为一项新的高科技环保技术已越来越受到环境科学工作者的重视。无机膜在环境保护领域中主要用于废水和废气的处理。无机膜处理废水的对象是含有固体颗粒和大分子污染物的废水、含油废水、生物废水等,随着孔径处于纳米级的微孔膜的研究进展,无机膜对含低分子有机污染物、重金属离子、表面活性剂的废水处理也展现出良好的发展前景。无机膜处理废气主要涉及高温气体除尘和腐蚀性气体的净化。尽管无机膜在环境保护领域中应用技术上是完全可行的,但成本相对较高,在选择处理技术时,技术经济比较应予以特别关注。同时在开发此类技术时,必须对工艺操作条件进行细致研究,强化传质过程,降低操作成本,并在装置材料选择上尽可能采用廉价材料,减少投资。
3.5.3.1 在含油废水处理中的应用
工业生产中含油废水的来源极为广泛,如油田采出水、金属表面的清洗废水、石油化工生产中的含油废水、金属切削研磨所用的润滑剂废水、钢铁厂冷轧乳化液废水,等等。这些废水若直接排放,将污染环境。由于含油废水往往具有难降解、易乳化等特点,一般的方法处理难以得到理想的处理效果。无机膜处理含油废水具有操作稳定、出水水质好、占地面积小、扩建方便、正常工作时不消耗化学药剂,也不产生新的污泥以及回收油质量比较好等优点,在含油废水处理中已日益显示出极强的竞争力。
无机膜处理含油废水的机理主要是利用油的表面张力,使得大于膜孔径的油滴被膜孔截留,由于过滤过程中会形成凝胶层,实际过滤过程中往往能截留比膜孔径小的油滴。用于处理含油废水的无机膜主要有氧化锆膜、氧化铝膜,不锈钢和复合陶瓷膜也有过研究报道。早在20世纪70年代初期,由Union Carbide开发的ZrO2动态膜(UCARSEP),在废水处理中已得到应用,用孔径为0.02~0.1μm的UCARSEP超滤膜,透过液含极少量的油,可以直接排放或再利用,浓缩的油可以循环使用或作燃料。目前无机膜用于含油废水处理主要应用领域是油田采出水处理,金属清洗液、轧钢乳化液、冷轧乳化液的处理,以及石化、化工行业的含油废水处理。
(1)油田采出水处理
油田采出水是原油初加工过程的产物,我国每年大约有5亿吨的油田采出水需要处理,一般这些采出水经过处理后绝大部分用于回注油层,这样既解决了注水水源问题,又保护了环境。我国陆上油田已经探明储量的有一半以上为低渗透油田,低渗透油田对回注水有严格的要求,含油量要小于5mg/L,悬浮物小于1mg/L,目前工业上对低渗透油田的回注水处理还没有合适的方法[147]。解决低渗透油田采出水问题对保持我国石油的稳产、高产具有十分重要的意义。
无机膜由于其独特的材料性能,在处理油田采出水方面具有突出的优势,引起了国内外的广泛注意。Chen[148]、Humphrey[42]等采用Membralox陶瓷膜进行了陆上和海上采油平台的采出水处理研究,经过适当的预处理后取得了较好的结果。王怀林[149]等采用南京工业大学膜科学技术研究所研制的0.8μm氧化铝膜和0.2μm氧化锆膜对江苏石油勘探局真武油田真二站三相分离器出口水进行了处理,并将国产膜与Membralox(U.S.Filter)的0.2μm氧化铝膜进行了比较,认为两种国产膜的长期稳定运行通量较高。Simms[150]等采用了高分子膜和Membralox陶瓷膜对加拿大西部的重油采出水进行了处理,其通量相对较小。徐俊[151]等采用100nm孔径非对称结构的陶瓷超滤膜对大庆油田采出水进行了处理,出水达到了油田低渗透层的回注水质A1级要求。丁慧[152]等采用200nm孔径的陶瓷膜对胜利油田某污水处理站的油田采出水进行了操作参数的优化及污染机理的研究。表3-29是以上研究工作的主要结果,从中可以看出,采用陶瓷膜处理油田采出水基本是可行的,不同的采出水处理效果和通量不同,相对而言重油油田采出水较难处理。
表3-29 陶瓷膜处理油田采出水结果一览表

(2)金属清洗液、轧钢乳化液和冷轧乳化液废水处理
金属清洗液是机械加工行业的主要废水之一,这类废水往往成分比较复杂,主要为油脂、表面活性剂、悬浮杂质和水,一般废水量不大,但污染严重,且处理困难,与此类似的废水还有金属切削液、润滑液等。Superior Planting Inc.MN.为美国中西部最大的金属加工厂之一,推出了一种结构非常紧凑的陶瓷膜金属清洗液回收系统,其经济效益十分显著,1.6年即可收回装置投资。含油、脂和固体杂质的废水,通过陶瓷膜过滤,净化水回清洗槽循环使用,而浓缩的油脂浮在回收槽液面上而得以除去,一些悬浮固体,如Fe(OH)3等,定期从槽底移去。废水经陶瓷膜过滤,油含量从448mg/L降至19mg/L,去油率为96%。通过陶瓷膜处理,清洗液的更换周期从每周一次延长到6个月。
采用了孔径为0.05μm的氧化锆膜处理金属清洗液,通过过滤除去废水中的油和杂质,滤过水补充适当的表面活性剂即可重新使用,其结果见表3-30。冷轧乳化液是轧钢行业产生的一种废水,主要含有1%~3%的矿物油、乳化剂和水,与金属清洗液比较类似,常规的方法处理效果不好,且处理费用高,是困扰我国轧钢行业的一大技术难题。张国胜等[153]采用0.2μm的氧化锆膜处理冷轧乳化液废水,比较了孔径、膜材质等参数对过滤通量的影响,详细考察优化了操作过程,并采用添加湍流促进器来降低循环量,在保证过滤通量的前提下可以显著降低表面流速,其能耗仅为正常操作的20%。陈哲宇[154]采用陶瓷膜处理冷轧钢生产厂里的废乳化液,比较了废乳化液的预处理和未预处理时膜通量及设备运行周期的差异,发现有效预处理能够有效地延长设备运行周期,其结果见表3-30。
表3-30 陶瓷膜处理金属清洗液和冷轧乳化液结果一览表

(3)石化含油废水
Lahiere和Goodboy[158]采用孔径为0.2~0.8μm的氧化铝膜处理烷基苯厂废水中的芳烃和石蜡油,其含量为15~500mg/L,通过加入160mg/L盐酸和160mg/L氯化铁进行预处理可获得较大的通量,0.2μm膜通量较大,膜面流速为4.6m/s左右,稳定通量为1250~1540L/(m2·h)。对膜污染的控制采用自动反冲系统,用气顶水反冲,每3~5d对膜管进行一次清洗。先用5%热碱循环,用透过液漂洗,再用5%盐酸清洗,最后用透过液漂洗,时间为1h,试验结果表明陶瓷膜技术比传统的方法具有一定的优势。邢卫红等[159]采用孔径为0.2μm的陶瓷膜处理炼油厂含焦废水,过滤通量为300L/(m2·h),截留率95%以上,且可显著降低COD值。
3.5.3.2 在废油过滤中的应用
由于无机膜具有良好的耐热、耐化学溶剂和较好的机械强度,可以用于各种油品的过滤。无机膜用于废油的再生,已经建起了年处理5000t废机油的中试工厂。一般废油中含有水、泥浆、炭粒子、金属粒子等杂质,传统的废油再生方法是采用酸处理,并加黏土等对废油进行精制,这种方法将产生大量的酸性淤泥,为环保所不允许。采用孔径在20~40nm的无机超滤膜可以对废油进行处理,这一过程的操作温度一般在200~350℃,操作压差5bar,膜面流速3~5m/s,其渗透通量约为20~30L/(m2·h),反冲压力达30MPa。Kim等[160]采用陶瓷超滤和微滤膜过滤废润滑油,可使之转变为可用的燃料油,处理温度为150~200℃,过高的温度会引起油的碳化分解,通量主要取决于温度和膜与废油间的相互作用。
为了脱除重油中的沥青,一般加入溶剂使沥青沉降,Deschamps等[161]试验了采用孔径为2~15nm的氧化铝和氧化锆膜进行溶剂脱除,发现随孔径增大,分离效率从100%降低到30%。进一步还试验了用孔径为30~600nm的氧化锆和氧化铝膜回收转化油中的催化剂,在较高的膜面流速和温度下可获得稳定的通量,催化剂回收率大于98%。Guizard等[162,163]采用孔径为6.3nm的氧化锆膜从石油渣中直接脱沥青,处理温度为150℃,膜面流速为11.5m/s,通量为80L/(m2·h),沥青去除率大于75%。
钟道悦[164]用平均孔径为0.2μm的陶瓷膜,在过滤温度为75℃、真空度为0.095MPa条件下处理废润滑油,膜通量达到231.9L/(m2·h),再生油样的透光率为76.29%,40℃运动黏度为51.41mm2/s,黏度指数为156,酸值为2.03mg KOH/g。经过膜分离后,去除了部分胶质、沥青质和酸性物质等杂质,再生油质量得到了较大的改善。
3.5.3.3 在MBR中的应用
膜生物反应器(membrane bioreactor,MBR)是20世纪末发展起来的一项新型水处理技术,它将分离过程中的膜技术应用于活性污泥处理系统,使膜分离与生化处理相结合,以膜组件取代传统生化处理技术中的二次沉淀池和砂滤池,在生化反应器中既保持了高活性污泥浓度,又减少了污水处理设施的占地面积。
在1996年,陶瓷膜生物反应器在食品工业废水处理中就有应用[165],英国巴斯大学使用错流陶瓷膜耦合生物反应器处理乳制品加工废水,陶瓷膜提供的较高的曝气使BOD5与COD体积去除率明显提高(分别为117%和128%)。
(1)医药废水
西班牙某药厂[166]对生物碱类进行提取和纯化,生产过程中加入硅藻土过滤。经检测得到废液中含有大量50~100μm的微粒,并且溶剂的化学腐蚀性很强。用陶瓷膜生物反应器进行处理,反应器内微生物浓度高达35g/L,最大处理量350m3/d,平均处理量300m3/d,平均进水CODCr为15000mg/L,出水水质BOD5<25mg/L、SS<5mg/L、Ca2+<150mg/L、Fe2+<20mg/L、Si<5mg/L、硬度<500mg/L(以CaCO3计)。相比较之下,有机膜生物反应器短时间运行过后,通量变低且处理效果也变差。经分析,发现有机膜已经被料液腐蚀损坏,活性层已完全降解。
(2)印染废水
2009年中国地质大学用微滤陶瓷膜生物反应器处理印染废水,处理结果得到CODCr、TOC(总有机碳)和色度去除率分别达到85%、85%~90%和70%,出水的平均CODCr为70mg/L[167]。
(3)合成废水
2015年日本立命馆大学[168]用低成本的陶瓷过滤器制成膜生物反应器来处理合成废水,废水中主要含有洗发香波、洗洁精和衣物洗涤剂,采用重力出水,平均通量达到11.5LMH[1LMH=1L/(m2·h)],出水水质实现了表面活性剂基本完全降解(达到99%~100%)以及有机物去除率很高(达到97%~100%)。
陶瓷膜生物反应器对含有酚类等有毒有机化合物的处理也有相关应用。土耳其C.B. Ersu等[169]使用陶瓷膜管制成MBR对含有苯酚的废水进行处理,苯酚去除率大于88%。工业废水中的一些有机化合物的毒性会抑制微生物生长,导致微生物量下降进而影响出水水质,而膜生物反应器具有保留高浓度生物量的特点,使其在这些相关水处理中具有很好的优势。
(4)市政污水
对于市政生活污水的处理,国内也有一些相关研究报道。徐农等[170,171]采用多通道陶瓷膜管处理市政污水,并且使用湍流促进器增大膜通量、降低膜污染,通量可达70~175LMH,出水水质较好,CODCr去除率达到95%以上。
3.5.3.4 在其他废水处理中的应用
在化工及其他行业中往往产生一些具有强酸、强碱或强腐蚀性的废水,有机膜往往难于胜任,而无机膜由于其优异的化学稳定性,在处理这些废水时具有独到的优势。
(1)化工废水
在硫酸法生产钛白粉的过程中,产生大量的含酸废水,其中含有偏钛酸细微颗粒,传统的沉降方法不仅占地面积大,而且回收不完全,限制了废酸的回收,Bauer等[172]研究了采用碳纤维膜处理硫酸法生产氧化钛中产生的含氧化钛细颗粒废酸,其结果见表3-31。李红等[173]采用氧化铝陶瓷微滤膜处理类似的废酸,取得了较好的结果(见表3-31),并认为浓度对通量影响不大,可以用于钛白粉的浓缩回收,现已建成了多套工业性处理装置。NGK公司采用氧化锆陶瓷膜从盐酸溶液中回收ZrO2细微粒子,用去离子水进行洗涤,以除去产品中的酸液,经过处理,洗涤水的电导率从200mS/cm下降到0.5mS/cm。
表3-31 采用无机膜处理含钛白粉废酸结果

王树勖等[174]采用陶瓷膜过滤装置处理中国石油兰州石化公司化工污水处理厂的外排水(浊度153mg/L),在操作压力为0.12MPa、膜面流速为6.0m/s的最佳工艺条件下,可得到出水浊度<6.8mg/L的净化水。
(2)石化废水
在氯乙烯单体(VCM)生产过程中会产生一些含有重金属离子的废水,由于废水中同时含有0.3%的EDC(1,2-二氯乙烷)和其他有毒有害物质,沉降出的重金属离子废渣必须焚烧处理,Lahiere和Goodboy等[158]研究了采用0.8~1.4μm的氧化铝膜除去沉淀的重金属离子和浓缩污泥,重金属离子浓度从废水中的0.012%浓缩至17%~20%,废水过滤通量为630~920L/(m2·h),浓缩污泥通量为160~230L/(m2·h),温度为35~55℃。Lahiere和Goodboy等[158]还研究了采用0.2μm氧化铝膜除去VCM工厂废水中的EDC乳化液,中试获得的稳定通量为1290L/(m2·h),操作温度为30~45℃。
(3)胶乳废水
胶乳废水的浓缩早在20世纪70年代中期就有成功应用。采用动态氧化锆膜处理胶乳废水,可从0.5%浓缩到25%~65%以回收胶乳,其中最重要的参数是膜面流速、过滤压差和浓度。对4%的胶乳,压差为0.3MPa时,通量为150L/(m2·h),由于大于50℃时会发生胶乳团聚,因此适当的处理温度为20~35℃。美国Union Carbide公司研制的Ucarsep膜分离工艺,选用无机多孔膜处理含胶乳废水,可去除料液中80%~97%的水分,并获得总固含量为25%~50%的胶乳产品[175]。其过滤液实际上已基本不含悬浮物,因此可用作循环水来替代部分新鲜水。我国兰州化学工业公司利用HFM膜处理胶乳浓度为0.11%~0.57%的洗釜废水,在中试规模下取得了较好的效果,浓缩液胶乳浓度为28.0%~33.3%,排放水可达国家二级排放标准。在选定工艺条件下运行1100多小时,膜通量未出现明显衰减。
(4)造纸和纺织废水
无机膜由于其耐高温和酸碱,在造纸和纺织行业的废水处理上有一定的优势。然而由于存在处理成本过高、排放标准执行不严等问题,无机膜在许多场合尽管技术上是可行的,却难以得到应用。目前已经商业化应用的过程是从废水中回收合成高分子,如聚乙烯醇,另一个正在开发的领域是除去废水中的染料。
采用碳支撑氧化锆膜回收聚乙烯醇始于1973年,回收率大于95%,在强酸性条件下,使用寿命可达5年或更长,通量可达100~150L/(m2·h)。Soma等采用0.2μm氧化铝膜处理印染废水,取得了较好的效果,其中不溶性染料去除率大于98%,通过加入一些表面活性剂可使可溶性染料的去除率大于97%,工业性试验中染料的去除率为80%,COD去除率为40%,通量为26~28L/(m2·h·bar)。Nooijen和Muilwijk[176]则采用无机膜回收涂料生产废水中的涂料。
Neytzell-de-Wilde等采用氧化锆动态膜处理羊毛洗涤水,在4.7MPa的过滤压差下,通量为30~40L/(m2·h),处理温度为60~70℃,膜面流速为2m/s。Jönsson和Petersson等[177]采用0.2μm氧化锆膜处理造纸废水,随污水不同通量为150~1300L/(m2·h),COD去除率为25%~45%。Barnier等[178]采用截留分子量为70000~110000的金属氧化物膜处理造纸黑液,处理温度为85~115℃,磺化油可从(105~124)×10-6浓缩至(280~300)×10-6,通量为43~60L/(m2·h)。
处理印染废水等难降解有机物一种比较新的方法是采用光催化氧化降解,常用的催化剂为一些金属氧化物如氧化钛、氧化铁等,超细催化剂具有较高的效率,但其分离较为困难。Butters等[179]将无机膜与光催化氧化结合起来构成膜反应器,可以很好地解决这一问题,引起了国内外学者的广泛注意[180-183]。
黄江丽[184]采用0.8μm微滤(MF)与50nm超滤(UF)无机陶瓷膜组合工艺对造纸废水进行了处理,在温度为15℃、压力为0.1MPa的操作条件下,0.8μm膜对COD的去除率为30%~45%,50nm膜对COD的去除率为55%~70%。
韶晖等[185]采用无机陶瓷膜提纯凹凸棒石黏土(简称凹土),将提纯后的凹土用于染料废水处理。结果表明,当凹土投加量为3.0g、染料pH为10、振荡速率为150r/min、吸附时间为90min时,膜分离技术提纯后的凹土对印染废水COD值降低率约为85%,脱色率约为95%,优于抽滤方法提纯凹土。
(5)放射性废水
Cumming等[186]采用孔径为2nm的氧化锆膜和0.2μm的氧化铝膜处理低放射性废水,中试取得了较好的结果,并已建成工业设备。采用无机膜处理技术,放射性物质的去除率通常是絮凝方法的5倍,加入水化四氯化钛(0.01g/L的Ti)可以进一步调高去除率。氧化锆膜处理的膜面流速为4.5m/s,过滤压差为0.2~0.5MPa。采用氧化铝膜处理对137Cs的去除率较高,而60Co去除率较小。研究结果同时表明加入0.01g/L的铁离子,膜的通量可达210L/(m2·h)。白庆中等[187]以聚丙烯酸钠作为辅助药剂,采用截留分子量为1000Da的23通道陶瓷纳滤膜对含有Co2+、Sr2+、Cs2+的低浓度(5×10-6)放射性废水进行处理。结果表明,当废水pH为7~8、聚丙烯酸钠体积浓度不低于0.1%时,渗透通量为31~43L/(m2·h),对放射性元素的截留率达到95%。陈婷等[188,189]采用ZrO2-TiO2复合陶瓷纳滤膜处理模拟放射废水中的离子型核素,在不使用络合物添加剂的情况下,陶瓷纳滤膜对Co2+和Sr2+的截留率可以达到99.7%以上,同时渗透通量在180L/(m2·h)以上。
(6)生活污水及其他废水
Trouve和Manem等[190]报道了采用陶瓷膜生物反应器处理生活污水的半工业性中试结果。Visvanathan等[191]采用陶瓷膜处理地表废物渗出废水,首先用粉末活性炭处理,再以微滤膜过滤分离活性炭,废水净化效果较好。Boldnan和Florke[97]采用SiC陶瓷膜来处理烟道气净化水,渗透通量为114~170L/(m2·h)。Shen等[192]采用无机膜处理醋酸纤维素生产废水。Goemans等[193]研究了采用陶瓷膜错流过滤去除超临界水中的金属氧化物。徐农等[194]以管式陶瓷膜生物反应器处理生活污水,结果表明:COD的去除率高达99.5%,氨氮和悬浮性固体的去除率达到99.9%和100%。
3.5.4 在化工与石油化工中的应用
分离是化工与石油化工生产过程的核心之一。因分离效率不高而引起的资源、能源浪费与环境污染等问题日渐凸显,已成为关系到行业可持续发展的瓶颈问题[195]。此外,由于化工反应体系大多数都是在高温、高压、酸碱和有机溶剂的环境下进行,对分离材料提出了较高要求。近些年来,无机膜技术作为一种高效的分离技术,具有机械强度高、耐酸碱、耐高温、耐有机溶剂等特点,在化工与石油化工生产中得到越来越广泛的应用。
3.5.4.1 陶瓷膜在润滑油脱蜡过程中的应用
润滑油生产需要对含蜡原油进行脱蜡处理,传统的脱蜡方法工序冗长、设备复杂,无法保证溶剂的回用率,处理成本高。而陶瓷膜分离技术用于酮苯脱蜡溶剂的回收,不仅可以使溶剂脱蜡的生产能力提高,还可以使投资的成本大幅度降低。Biswajit等[196]采用19通道陶瓷膜对米糠油进行脱蜡处理,处理结果表明其渗透通量达到15L/(m2·h),油的损失仅为2.6%,这一过程表明陶瓷膜的处理是脱蜡过程中溶剂回收的可行性选择。Majid等[197]通过对SiO2不对称基体的表面进行改性处理,制备了一种具有功能化表面的超薄纳米复合膜,从而实现了润滑油脱蜡过程中溶剂的回收,渗透通量为13.85L/(m2·h)。
3.5.4.2 无机膜在化工产品脱色中的应用
化工产品的生产过程中,许多产品对色泽有着严格的要求,需要对产品进行脱色处理。Biswajit等[196]采用多通道陶瓷微滤膜对米糠油进行脱色处理,脱色率为50%以上,对丙酮不溶残渣去除率达到70%以上。由于色素分子通常较小,为了提高脱色率需要采用孔径更小的陶瓷超滤或纳滤膜。韦平和等[198]采用超滤-纳滤耦合工艺去除L-色氨酸中的色素,当pH调节至5.5~6.0、温度控制在20~25℃条件下,经陶瓷膜处理的料液透光率可达85%以上,是活性炭脱色处理后透光率的2.7倍。Chen等[199]采用陶瓷纳滤膜对脱氢醋酸钠生产过程中产生的色素进行脱除,脱色前后对比如图3-57所示。脱氢醋酸钠料液的脱色率达到89.5%,通量在30L/(m2·h)以上。脱氢醋酸钠产品的回收率在98%左右,比采用传统的活性炭脱色工艺提高了2~3个百分点。

图3-57 脱氢醋酸钠料液经陶瓷纳滤膜脱色前后对比
3.5.4.3 无机膜在催化剂回收中的应用
在石油化工催化剂的应用中存在着催化剂颗粒细小、回收困难,以及细小的催化剂颗粒容易混入到产品中去的问题。此外,由于化工反应体系大多数都是在高温、高压和有机溶剂的环境下进行,因而如何从化工物料中分离出这部分流失的细小催化剂颗粒,是化工生产中需要解决的难题。无机膜因其具有优良的物理化学性能,耐酸碱、耐高温、耐高压、耐有机溶剂,分离效率高等,可以实现纳米催化剂的高效分离。金珊等[200]采用平均孔径为0.2μm的陶瓷微滤膜回收对硝基苯酚催化加氢制备对氨基苯酚过程中的纳米镍催化剂。陶瓷膜的过滤通量可以稳定在1050L/(m2·h)以上,渗透液中镍含量小于3mg/L,截留率满足了化工产品质量要求。在此基础上,为进一步减少过滤过程中纳米催化剂的吸附,仲兆祥等[201]在纳米催化-膜分离耦合工艺中引入了微米与亚微米级氧化铝惰性颗粒。研究表明,氧化铝惰性颗粒的引入,可以将纳米镍催化剂的吸附量减少10%左右,但对催化剂反应活性及膜通量没有明显影响。
均相催化剂具有活性和选择性高、反应条件温和等特点。但由于其在反应体系中呈高度分散状态,且尺寸较小,分离难度较高,很大程度上限制了均相催化反应的应用。以过渡金属均相催化剂为例,其分子量通常小于2000,反应体系多为有机溶剂体系,难以采用常规的过滤手段将其从反应体系中分离出来。陶瓷纳滤膜具有耐高温、耐酸碱、耐有机溶剂等特点,能实现分子级别的过滤,在均相催化剂回收方面展现了良好的应用前景[202]。
3.5.5 无机膜用于气体净化
在空气净化方面,目前主要以纤维式的过滤器为主。这种净化器对粒径为0.1~0.5μm的固体颗粒的去除率不够理想,并且纤维存在脱落现象。无机膜可以很好地解决这些问题,一些陶瓷膜(如氧化铝膜)已经进入空气净化市场。陶瓷膜另一个重要应用是高温气体的净化。锅炉烟道气和发电厂透平供气的除尘、化工过程中催化剂的回收等都涉及高温气体的过滤。由于陶瓷膜可以在高温下使用,因此不再需要通常的在除尘前后的气体冷却和加热过程。该部分内容将在本书第13章中详细介绍。
3.5.6 无机膜用于气体分离
高温下氢气的回收、煤气化后为提高热值需要分离去除二氧化碳和水蒸气、烟道气中酸性气体(如二氧化硫、硫化氢、二氧化碳等)的去除、燃料气中硫化氢的去除等工业过程都需要高温气体分离。在高温下实现气体分离与常规的降温、分离、升温过程相比,既节省了热交换设备,又降低了能耗。例如,煤高压气化气在降低温度时出现煤焦油和其他有机物的冷凝,这又引起了废水处理的问题。由于无机膜的固有特性,无机膜在气体分离中有着独特的优势。
自从20世纪70年代末有机膜在氮气与氢气的分离中得到应用以来,许多学者对无机膜在气体分离中的应用进行了研究,表3-32列出了无机膜的可能应用领域。
表3-32 无机膜用于气体分离的可能应用领域

(1)高纯氢的制备
氢在金属中的扩散比氧或氮在金属中的扩散大15~20个数量级。致密的钯及其合金具有较高的氢的渗透性,透过钯-银合金膜的氢气纯度达到99.99995%。钯与钇、钯与铈的合金能提供更高的渗透性能。小型的氢气纯化装置已经商业化多年。高纯氢最主要的一个应用领域是电子工业。
(2)氧和氮的分离富集
空气分离是近年来有机膜快速发展的应用实例,也被认为是无机膜的重要应用之一。Rao等[203]用支撑碳膜分离空气,室温下分离系数达到24.2,远大于努森扩散理想分离系数(为0.94)。
固体电解质膜在高温下透氧也是无机膜应用研究的重要方面。氧化锆或钙钛矿型材料在高温下能够选择性透过氧,可以用于制备高纯度氧。Guo等[204]开发出双组成的钙钛矿膜用于纯氧分离,氧气渗透通量达到1.54mL/(min·cm2),该膜表现出良好的二氧化碳气氛耐受性。
(3)氢和烃的分离
在一些工业过程中,产生了必须从反应体系中排放的低碳烃,其中含有氢气。过去,这些氢气与低碳烃一起作为燃料。无机膜可以回收其中的氢气。一些研究结果列入表3-33。
表3-33 氢与烃的无机膜分离

(4)氢与一氧化碳的分离
由天然气、油或煤制备得到的合成气的主要成分是氢和一氧化碳,合成气生产氨、醇、乙醛、丙烯酸的不同物质的过程需要调节合成气中氢与一氧化碳的比例。一些研究结果如表3-34所示。
表3-34 氢和一氧化碳的无机膜分离

(5)氢和氮的分离
无机膜用于气体分离研究最多的是从合成氨弛放气中回收氢,氢从膜的低压侧分离出来,经过加压再回到反应体系中。主要研究结果如表3-35所示。
表3-35 氢和氮的无机膜分离

(6)其他体系的无机膜分离
除了以上介绍的分离体系,其他体系的无机膜分离过程也非常重要:氢与二氧化碳的分离[209],水与醇的分离[210,211],硫化氢的富集,空气中烃蒸气的回收[212],有机物组分的分离[211],氦与氧或氮的分离[207,212]等过程。