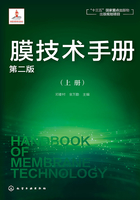
2.2 有机高分子分离膜的制备
膜分离技术的核心是分离膜。衡量一种分离膜有无实用价值,要看是否具备以下条件:
①高的截留率(或高分离系数)和高的通量(或高渗透性);
②优良的抗物理、化学和微生物侵蚀性能;
③柔韧性和足够的机械强度;
④使用寿命长,适用pH范围广;
⑤成本合理、制备方便,便于工业化生产。
每个膜过程,针对某个分离对象,一般都有更加具体、明确的指标要求。
许多有机高分子都可以做成薄膜,但若要成为一张高性能有实用价值的分离膜,除了选择合适的制膜材料外,同样重要的是必须找到一种使其具有合适结构的制造工艺技术。众所周知,Loeb和Sourirajan采用相转化工艺用醋酸纤维素(CA)制造出具有非对称结构的反渗透膜,在保持高脱盐率的同时,透水量提高近一个数量级。这就是膜分离问世以来,分离膜的制造工艺一直成为众所瞩目的研究和开发热点,持久而不衰的原因。如果把分离膜作为一种新材料,那么其内容应包括膜材料和制膜技术两部分,才是完整的、准确的。
如图2-3所示,有机高分子分离膜从形态结构上可以分为对称膜(或称均质膜)和非对称膜两大类。

图2-3 有机高分子膜的分类
2.2.1 均质膜的制备[97-101]
均质膜有致密均质膜、多孔均质膜和离子交换膜等类型。
2.2.1.1 致密均质膜
致密膜一般指结构紧密的膜,其孔径在1.5nm以下,膜中的高分子链以分子状态排列,有机高分子的致密均质膜在实验室研究工作中广泛用于研究膜材料本身的性质。致密均质膜由于太厚、通量太小,一般较少在实际工业生产上应用。其制法如下。
(1)流延法
将膜材料用适当的溶剂溶解,制成均匀的铸膜液,将铸膜液倾倒在铸膜板(一般为经过严格选择的平整玻璃板)上,用特制刮刀使之铺展成具有一定厚度的均匀薄层,然后移至特定环境中让溶剂完全挥发,最后形成均匀薄膜。铸膜液的浓度范围较宽,一般为15%~20%(质量分数),铸膜液要有一定的黏度,使其不至于在成膜过程中从铸膜板上流走。高沸点溶剂一般不适用于溶液浇铸,因其低挥发度需要太长的完全蒸发时间。
用于制备致密均质膜的溶剂性质、脱溶剂过程中铸膜液表面的空气相对湿度、流动状况等对膜的最终性质具有重大影响。致密均质膜可以经受某种改良其结构和特性的后加工处理,例如:无定形膜的热处理具有缩小平均链间间隔的作用,把聚碳酸酯膜暴露在丙酮蒸气中可提高其结晶度。
(2)熔融挤压
一些结晶性有机高分子找不到合适的溶剂制成铸膜液,则要采用熔融挤压法来成膜。将高分子放在两片加热的夹板之问,并施以高压(10~40MPa),保持0.5~5min。对高分子本体加热,最初使基团移动,最后较小的和大的链段也运动起来。控制熔融黏度(亦即控制由熔体制备的致密高分子膜结构)的因素是:
式中,η为熔融黏度;f为统计因子;J为链段跳跃频率;M为分子量;Vf为自由体积;T为温度。
统计因子与下述事实有关:由于链段由主价链连接,在一个剪切力的作用下,整个分子可以运动之前必然有单个链段运动的协调。自由体积Vf是测量值和高聚物分子实际占有的体积之差。温度T控制着对每个链段的有效能和熔体内孔洞的数目。
最佳的挤压温度是使高分子熔融,并能形成所需厚度薄膜的最低温度,提高温度会导致高分子的降解。为防止成膜后粘在压板上,一般将高分子放在两片涂有聚四氟乙烯涂层或两张可透水的玻璃纸之间,玻璃纸不会粘在压板上,熔融挤压下很容易从膜上脱落。如要制备超过100μm厚度的膜,可在压板之间放合适的金属垫片。
(3)聚合期间形成致密膜
无论什么时候,聚合作用都伴随有同时发生的交联和由此而来的高分子产物难以控制,它是由于各种链转移和偶联反应的交联作用所致。这类致密均质膜必须在聚合期间就形成。属于这一范畴的膜最重要种类是均质离子交换膜。这种高分子致密膜不同于从溶液或熔体制得的膜,前者可以展现出线型高分子所有三种限定的形态,而后者通常把生长于舒展高分子链的结晶参与排除在外(见图2-4)。

图2-4 线型聚合物的极限高分子构型
(a)无规线团;(b)折叠链;(c)舒展链;(d)以上三种混合物
2.2.1.2 多孔均质膜
多孔均质膜的制备方法很多。
(1)径迹蚀刻膜
1959年Silk和Bannas发现放射性衰变产生裂变碎片,在一定条件下可照射而穿过固体,对被照射和损伤的材料造成狭窄的径迹,可借助于适当试剂的腐蚀扩大这种径迹。后来Fleischer等利用这种现象发展成一种径迹蚀刻分离膜,又称为核孔膜、核径迹膜。这种膜的特点是孔呈圆柱状,孔径分布极窄(图2-5),而绝大多数其他种类高分子膜的孔都是弯弯曲曲的,且孔径分布宽。

图2-5 聚碳酸酯径迹蚀刻膜(1.0μm孔径)的扫描电子显微镜照片
(a)表面,5000×;(b)横截面,1000×
径迹蚀刻膜的制备主要有两个步骤:首先用荷电粒子照射高分子膜,使高分子化学键断裂,留下敏感径迹;然后将膜浸入适当的化学刻蚀试剂中,高分子的敏感径迹被溶解而形成垂直于膜表面的规整圆柱形孔。其工艺示意图见图2-6。

图2-6 制备径迹蚀刻膜的两步过程
1—荷电粒子;2—非导体;3—径迹;4—孔;5—蚀刻膜
一个核粒子引起的离子化损伤的密度,大致正比于粒子电荷的平方,而反比于其速度的平方,由于裂变碎片无规律扩散,必须使它们在一个聚合物薄膜中排列成直线以产生平行径迹。这可借助于从薄膜分离出铀辐射源一个平行粒子束,将中间抽成真空,然后将设备暴露于热中子里,间距越大和辐射源面积越小,就越能使所得的孔洞笔直。少数孔洞未能完全穿透膜,这是由于一部分裂变碎片能量在进入膜与辐射源之间的真空空间之前,已消耗于通过放射源的过程之中,这种情况可以设法减少,但不能完全消除。腐蚀剂的选择随高分子膜的化学性质、浓度、温度和被腐蚀表面的取向而异。在腐蚀之前进行部分退火和采用较弱的腐蚀剂,可得到较小的孔洞直径。高分子膜的腐蚀液见表2-13。
表2-13 各种高分子膜的腐蚀液[98]

不同高分子对环境条件的敏感程度不同。例如:若想得到均匀的通孔醋酸纤维素膜必须在腐蚀之前先退火;硝酸纤维素在室温下缓慢地腐蚀比在70℃下快速腐蚀得到更好的径迹。与此相反,聚碳酸酯薄膜对环境条件较不敏感。目前径迹蚀刻膜的材料主要是聚酯和聚碳酸酯。对聚碳酸酯薄膜,最高允许剂量约为每平方厘米有1011个裂变碎片,相当于总表面积的0.5%成为25×10-10m的孔洞。径迹蚀刻法制备的膜孔径范围为0.01~12μm,孔密度可达2×108个/cm2。
(2)拉伸法
拉伸法制膜一般要经过两步:首先将温度已达其熔点附近的高分子经过挤压,并在迅速冷却下制成高度取向的结晶膜;然后将该膜沿机械力方向再拉伸几倍,这一次拉伸破坏了它的结晶结构,并产生裂缝状的孔隙。这种方法一般称为Celgard法。
Celgard法选用商品聚丙烯为膜材料,在拉出速度远高于挤出速度的情况下,聚丙烯分子本身变成一种与机械力成一致方向的微纤维形式,它会在机械力垂直方向上形成的折叠链排薄片的微晶中起核心作用。然后,在低于高分子的熔融温度(Tm)而高于起始的退火温度下进行拉伸(50%~300%),使薄片之间的非晶区变形为微丝,结果形成了一种顺机械力方向的具有狭缝的多孔互联网络,孔的尺寸决定于拉伸后的微丝。
图2-7和图2-8显示拉伸的程度控制着孔径和孔径分布。当膜仅拉伸100%时,出现了内含许多孔大于0.15μm的双峰孔径分布。拉伸100%的膜比拉伸300%的膜的渗透性还大,这是因为后者所含主要孔径低于0.1μm。拉伸率超过300%时,将导致孔隙率的急速消失。

图2-7 拉伸率对微孔聚丙烯薄膜的表观密度的影响

图2-8 拉伸率100%和300%时微孔聚丙烯薄膜的孔径分布
商品牌号为Celgard2500的聚丙烯薄膜,孔长0.4μm、宽0.04μm,孔隙率是40%,孔密度为9×109孔/cm2。图2-9显示,被拉伸微丝平行于机械力方向和薄膜表面,构成了大量孔洞,可用作锂离子电池隔膜。

图2-9 Celgard2500聚丙烯微孔膜的表面扫描电镜图
表2-14和表2-15说明Celgard聚丙烯微孔膜具有优良的力学性质和化学药品相容性。Celgard商品膜有平板膜和中空纤维膜两种形式。Celgard2400和Celgard2500平板膜的有效孔径(孔宽度尺寸)多为0.02μm和0.04μm。Celgard X-10和Celgard X-20的有效孔径皆为0.03μm,孔隙率分别为20%和40%,内径100μm、200μm和240μm,壁厚25μm,可用于中空纤维血液氧合器。
表2-14 Celgard薄膜的典型物理性质[98]

注:1. MD=机械力方向;TD=横切于机械力方向。
2. 1kgf=9.80665N。
表2-15 Celgard薄膜与各种化合物的相容性[98]

注:相容性报告是在室温(25℃)下、暴露72h取得的。标号:A表示好(无效应);B表示稍溶胀;C表示材料溶胀。
Gore-Tex是另一种采用拉伸成孔的微孔分离膜。它用一种分子量为500000、具有微细(0.1μm)类纤维结构的、高度结晶(约98.5%)的分散聚合物Teflon6A,与15%~25%的润滑剂(如石脑油或煤油)混合,然后用柱塞压出,加热除掉润滑剂,在80℃下通过压延机的辊筒间隙使成薄膜,再经单轴或双轴拉伸以后,在327℃下烧结,在烧结过程中,无定形含量增高,起到了“镇定”的作用,且加固了拉伸膜中的孔洞。Gore-Tex膜也
具有隙缝般的孔洞,由于有时采用双轴拉伸,所以其隙缝不总是彼此平行的,见图2-10。

图2-10 Gore-Tex的表面扫描电子显微镜照片
Gore-Tex拉伸多孔膜的孔隙率高、孔径范围宽,具有极高的化学惰性,可以过滤有机溶剂与热的无机酸和碱,是一种重要的多孔分离膜。Gore-Tex膜的性质见表2-16。
表2-16 Gore-Tex膜的性质[98]

①空气流速:在21℃和1.2kPa的压力降下,每1min和每1cm2的膜面积透过去的空气体积(mL)。
②甲醇流速:在21℃和93kPa的压力降下,每1min和每1cm2的膜面积透过去的甲醇体积(mL)。
③在21℃下,膜经无水乙醇润湿。
④1lb/in2=6.895kPa。
(3)溶出法
溶出法是指在一些难溶的高分子膜材料中掺入某些可溶性的组分,制成均质膜后再用溶剂将可溶性组分浸提出来,形成微孔膜。这种方法并不常用,主要针对难溶的高分子。
也有将低分子表面活性剂以微胞的形式加到高分子溶液中,待其固化成薄膜后,先在一种流体中溶胀破坏微胞,使成为单独表面活性剂分子,然后再将表面活性剂浸出,形成微孔均质膜。这种方法已用于纤维素、聚丙烯酸、聚乙酸乙酯、聚乙烯等有机高分子膜材料。
表面活性剂的用量为10%~200%(以高分子膜材料质量计),膜的孔隙率与表面活性剂的浓度成正比(表2-17)。把200%十二烷基苯磺酸钠加到合适浓度的黏胶溶液中,得到的微孔膜具有约0.2μm的孔径。
表2-17 黏胶溶液中十二烷基硫酸钠的浓度对纤维素超凝胶膜的厚度及渗透率的影响[66]

①7%纤维素+5.8% NaOH。
②1in=25.4mm,1gH2O/(in2·20inHg)=0.023gH2O/(m2·Pa)。
(4)静电纺丝法
静电纺丝是一种特殊的纤维制造工艺,聚合物溶液或熔体在强电场中进行喷射纺丝。在电场作用下,针头处的液滴会由球形变为圆锥形(即泰勒锥),并从圆锥尖端延展得到纤维细丝,如图2-11所示。这种方式可以生产出纳米级直径的聚合物细丝。静电纺丝就是高分子流体静电雾化的特殊形式,此时雾化分裂出的物质不是微小液滴,而是聚合物微小射流,可以运行相当长的距离,最终固化成纤维。

图2-11 静电纺丝过程示意图
不同于传统相转化方法制备的膜材料,静电纺丝所制备的纳米纤维膜是由纳米尺寸的纤维材料重叠而成。因此,纳米纤维膜具有高比表面积、高孔隙率、高表面粗糙度、高定向性等特性。另外,相对其他制膜方法,静电纺丝的方法更易于将特定的功能性材料或官能团接枝在单根纳米纤维表面或者涂覆在纳米纤维膜基体的表面。图2-12是典型的静电纺丝法制备的纳米纤维膜扫描电镜图。

图2-12 静电纺丝纳米纤维扫描电镜图[102]
(a)聚乙烯基苯酚与无定形TiO2复合纳米纤维膜;(b)、(d)锐钛矿静电纺丝陶瓷纳米纤维;(c)、(e)金红石静电纺丝陶瓷纳米纤维
从20世纪90年代开始,静电纺丝技术的发展大致经历了四个阶段:第一阶段主要研究不同聚合物的可纺性和纺丝过程中工艺参数对纤维直径及性能的影响以及工艺参数的优化等;第二阶段主要研究静电纺丝纳米纤维成分的多样化及结构的精细调控;第三阶段主要研究电纺纤维在能源、环境、生物医学、光电等领域的应用;第四阶段主要研究电纺纤维的批量化制造问题。上述四个阶段相互交融,并没有明显的分界线。
静电纺丝作为一种简便有效的可生产纳米纤维的新型加工技术,纺丝过程受聚合物分子结构(支化度、分子量、分子量分布等)、溶液性质(浓度、黏度、导电性、表面张力、流量等)、电势大小、毛细管与收集屏的距离、环境条件(温度、湿度、空气流速等)、收集装置的移动、喷丝口大小与形状等的影响。所纺制的纳米纤维均匀重叠堆积成膜,孔隙率大、孔道贯通,可用作空气过滤膜、锂离子电池隔膜、反渗透/纳滤的底膜等。目前能够用来静电纺丝的聚合物种类很多,典型的聚合物及其溶剂与纺丝液浓度如表2-18所示。
表2-18 静电纺丝用聚合物及其溶剂与纺丝液浓度[103]

(5)模板法
模板法是近年来发展起来的一种新型多孔膜制备方法,所制备的多孔膜通常具有孔径分布窄(均孔)的优点,其种类包括水滴模板法、软刻法、光子晶体模板法、溶剂晶体模板法、乳液模板法、生物模板法等。这里着重介绍水滴模板法[104]。
水滴模板法,又称高湿度诱导相分离法或呼吸图法。呼吸图的称谓来源于我们日常生活中的常见现象——向寒冷的表面呼气,将在表面形成雾状图案。事实上,呼吸图的形成并不一定与呼吸有关,其必要条件为过饱和蒸气如水蒸气在冷的基质表面凝结。1994年,Widawski、Rawiso和Francois首先将呼吸图原理应用于制备具有蜂窝状图案的聚合物薄膜,他们将星形聚合物的二硫化碳(CS2)溶液在潮湿气流下涂覆在基底表面,得到了孔径均一的蜂窝状膜[105]。水滴模板法制备的典型蜂窝状均孔膜的表面扫描电镜图见图2-13。这种方法提供了一种简便、成本低廉、快速高效的制备有序多孔膜的技术,其膜孔孔径可在亚微米至十几微米间调节。

图2-13 水滴模板法制备的典型蜂窝状结构多孔膜
水滴模板法的操作非常简单,但背后的机理却极为复杂,确切的机理仍有争议。目前,这种非平衡方法被广泛接受的机理如图2-14所示。包括以下过程:将溶解在挥发性溶剂中的聚合物溶液涂覆于基底表面,在潮湿环境中,溶剂挥发使得周围温度降低,引起气氛中的水蒸气冷凝于聚合物溶液表面,形成液滴;溶液中的聚合物吸附或沉淀于水滴表面,包裹、稳定水滴,阻止水滴的聚并;液滴逐渐长大,并可能在马朗格尼对流和热毛细效应的作用下沉入溶液底部,自发排列成二维或三维水滴阵列;最后,溶剂与水滴完全挥发,得到蜂窝状有序多孔膜。

图2-14 水滴模板法制备蜂窝状结构均孔膜的形成机理[106]
根据上述机理,水滴模板法中膜孔的形成来源于成膜过程中水滴的自组装和模板作用,因此也可归属于自组装方法。水滴模板法制备的均孔膜还有一个特点,成膜过程中水滴与聚合物亲水基团或纳米粒子的相互作用能够诱导亲、疏水组分定向分布,亲水组分将集中分布在膜孔四周及内部,疏水组分在膜表面富集,该特点有助于蜂窝状结构多孔膜在微图案化、响应性涂层、传感器等领域的应用。
(6)烧结法
烧结指的是使一个微小颗粒或者一群均匀组成的微粒在高温条件下聚集,烧结不是一个简单的致密化作用。在高分子材料烧结过程中的物质传递包括:黏性或塑性流动、体积扩散、表面迁移和蠕变。对高分子物质发生烧结作用,微粒表面必须足够软化,以使大分子链段相互扩散而进入邻近的微粒中去。
制备高分子膜的烧结过程,主要限于具有柔性结构的高分子。一定材料的烧结温度主要取决于高分子的性质和分子量、结晶度,是否有增塑剂或其他添加剂以及烧结压力、周围气氛等。烧结温度随高分子的分子量与极性加大而增高,也随结晶的大小和结晶度增加而升高。往往加入一种非烧结性的添加剂(它在烧结以后可以从膜中被抽提出来)来提高膜的渗透性。例如淀粉粒子加入粉状聚乙烯中,最后用水把它沥洗出来。用烧结法制备的膜一般孔径分布均较宽,但是它们具有相当高的强度和抗压实性及化学惰性,使它们在某些特殊分离中具有重要应用。烧结法是制备PTFE微孔膜的一种重要方法。
其他的高分子微孔均质膜的制备方法还有光刻法、溶胀的致密薄膜法、聚合期间形成的多孔膜、羊皮纸和赛珞玢的溶胀等,不再一一详述。
2.2.1.3 离子交换膜
离子交换膜是用于电渗析、燃料电池、液流电池等膜过程的一种荷电有机高分子膜。根据膜中活性基团分布的均一程度,离子交换膜大体上可分为异相膜、均相膜和半均相膜三类。若根据在膜本体上的不同性能,离子交换膜可分为阳离子交换膜(简称阳膜)和阴离子交换膜(简称阴膜)两大类。阳膜的活性基团主要是磺酸、磷酸和羧酸基团,阴膜的活性基团则为伯胺、仲胺、叔胺等。近年来最常用的离子交换膜材料有:聚乙烯、聚丙烯、聚氯乙烯等的苯乙烯接枝高分子以及以聚偏氟乙烯、聚砜为骨架的磺酸型离子膜。
(1)异相离子交换膜
形成膜的整个材料呈现非均相的膜叫异相膜。例如离子交换树脂粉加上黏合剂和增塑剂后热压所成的膜即为异相膜。其结构见图2-15。

图2-15 异相膜结构示意图
1—黏合剂;2—离子交换树脂
热压成形法是制备异相离子交换膜最简单最常用的方法,典型的聚乙烯离子交换膜的制备工艺流程如下:
具体操作方法:先将黏合剂聚乙烯(高压、20%~25%)在辊压机中加热混炼,至完全塑化为止。随即加入合成橡胶5%,进行机械接枝,待混合均匀后,加入润滑剂(如硬脂酸钙),最后加入阳离子或阴离子交换树脂粉(250目过筛),反复混炼均匀,调节辊距为约0.4mm,再进行间断(或连续)拉片,拉出片后备用。另用尼龙网布覆盖在膜的两面,在油压机上加热(140℃左右)、加压(5~10MPa)0.5~1h,冷却出料即得离子交换膜。若为连续方式,可在拉片的同时覆盖网布。为了便于区别阴膜和阳膜,在制膜时可加点颜料,一般阴膜为淡蓝色,阳膜为米黄色。也可将离子交换材料加到一个已部分聚合的高分子中去,然后成膜并使其完全聚合。
(2)均相离子交换膜
均相离子交换膜的制备方法至少有5种。
①将能反应的混合物(即酚、苯磺酸、甲醛等)进行缩聚。混合物中至少有一种能在它的某一部分形成阴离子或阳离子。
②将能反应的混合物(即苯乙烯、乙烯基吡啶和二乙烯基苯)进行聚合。混合物中至少有一种含有阴离子或阳离子,或者有可以成为阴离子或阳离子的部位。
③将阴离子或阳离子基团引入高分子或高分子膜。例如将苯乙烯浸吸入聚乙烯薄膜内,使浸吸进去的单体聚合,然后将苯乙烯进行磺化。与此类似,也可通过接枝聚合将离子基团接到高分子薄膜的分子链上。
④将含有阴离子或阳离子的分子链段引到一个高分子上(例如聚砜),然后将此高分子溶解并浇铸成膜。
⑤通过把离子交换树脂高度分散于高分子中形成高分子合金或共聚体。
无论用以上哪一种方法制备的膜都必须用织物增强以改善其强度及形态稳定性。例如,用聚乙烯-苯乙烯浸吸接枝法制备均相离子交换膜,其工艺流程如下:
具体操作方法:取厚度为0.24mm的高压聚乙烯薄膜数张,浸于事先配制的单体中。阳膜所用单体比为苯乙烯∶二乙烯苯=100∶3(质量比),阴膜为100∶1。在单体中加入少量引发剂(二异丁腈)和透平油,逐步升温至60℃(约需1h),保温45min,然后挤出多余的单体,再用热水冲洗,在压机中进行固化,于65~70℃保温7h后即可逐张剥离,制得底膜。制备阳膜时,将底膜先在38~40℃下在二氯乙烷中溶胀2h(或在常温下过夜),抽除溶胀剂,再用硫酸(93%)在78~80℃下磺化8h,然后用稀硫酸逐步稀释、水洗、加入1mol/L NaOH溶液,水洗至中性,即得磺酸钠型阳膜。制备阴膜时,先将底膜浸入氯甲醚和无水氯化锌(质量比为100∶20)中,然后逐渐升温至50℃,并保温约9h,冷却后放出残液,再经多次水洗、风干,最后用三甲胺水溶液(30%)于室温下胺化,经水洗后浸入1moL/L HCl溶液中,洗至中性,得季铵型阴膜,如果对氯甲基化的膜用吡啶水溶液胺化,则得吡啶季铵型阴膜。
均相离子交换膜的性能远优于异相膜,所以目前使用的离子交换膜多为均相膜。均相膜与异相膜的比较见表2-19。
表2-19 均相膜与异相膜的性能比较

(3)半均相离子交换膜
从宏观上看是一种均匀一致的整体结构,成膜的高分子化合物与具有离子交换特性的高分子化合物十分紧密地结合为一体,但不是化学键结合;从微观看,应属于异相膜范畴,习惯上也可将此膜看作是均相离子交换膜。其制备方法类同异相和均相离子交换膜。
2.2.2 非对称膜的制备[97-99,107-112]
非对称膜一般比均质膜的通量高得多。目前在大多数液相分离工业应用中还是以有机高分子非对称膜为主。非对称膜由一层薄的多孔或致密皮层(起分离作用)和一层厚得多的多孔层(起支撑皮层作用)组成。有机高分子非对称分离膜主要包括相转化膜和复合膜。
2.2.2.1 相转化膜
将一个均相的高分子铸膜液通过各种途径使高分子从均相溶液中沉析出来,使之分为两相,一相为高分子富相,最后形成高分子膜;另一相为高分子贫相,最后成为膜孔。相转化法制备的高分子非对称膜具有以下两个特点:一是皮层与支撑层为同一种膜材料;二是皮层与支撑层是同时制备、形成的。
相转化法制备的高分子非对称膜的孔结构基本上可以归纳为以下四种类型。
①皮层是致密的,支撑层为海绵状小孔,醋酸纤维素反渗透膜属此类结构,见图2-16。

图2-16 非对称醋酸纤维素膜的断面电镜图
②皮层是致密的,支撑层为指状大孔,芳香聚酰胺反渗透膜属此类型,见图2-17。

图2-17 非对称芳香聚酰胺反渗透膜的断面电镜图
③皮层是多孔的,支撑层呈海绵状小孔,例如聚砜超滤膜,见图2-18。

图2-18 断面为海绵状孔结构的聚砜超滤膜电镜图
④皮层是多孔的,支撑层是指状大孔,很多超滤膜是这种结构。见图2-19。

图2-19 超滤膜断面的指状大孔结构电镜图
相转化非对称膜的结构与高分子铸膜液的组成及其发生相转化的条件密切相关。
(1)铸膜液
有机高分子分离膜中的大部分都是先将高分子膜材料配成高分子溶液,然后再经过不同工艺成膜。有机高分子是由许多很小的分子(单体)连接而成的大分子化合物,它的特点是分子量大、分子链的长度与直径之比非常大,因此有机高分子溶液的性质和行为与无机水溶液大相径庭。只有线型高分子才能溶解,达到一定交联度后线型高分子转变为体型高分子,体型高分子不能在溶剂中溶解。高分子溶液是线型高分子在含一种或多种成分的溶剂体系中均匀分散。形成高分子溶液的条件是高分子与溶剂的相互作用(P-S)大于聚合物分子间的相互作用(P-P),即只有P-S>P-P,才能达到P+S>P-S(溶液)。
大多数用以铸膜的高分子溶液是浓溶液。一般在室温下溶液中高分子的体积分数φ小于0.5;用于干纺致密中空纤维的溶液φ为0.3~0.4;用于湿法制备平板膜的溶液约为0.2;干法制备平板膜的溶液约为0.1。为了种种目的,铸膜液中除溶剂外常常还包含另外的组分,例如溶胀剂、非溶剂、保湿剂、致孔剂等。一个溶液体系的各种成分,可以用图2-20表示成为对高分子具有不同亲和力的物质的一个连续区域。

图2-20 聚合物-溶剂相互作用谱图
作用图的一端是能与高分子相互作用,从而影响溶液内高分子聚集程度和构象的溶剂,相反的另一端是为高分子或溶剂以或多或少的含量所能容忍的非溶剂。它有助于理解通过多组分高分子溶液的逐步脱溶剂制备分离膜。
高分子溶液的P-S相互作用强度有几种测量方法,其中有溶液黏度、溶液浊度、非溶剂(稀释剂)的允许含量、各种内聚参数以及高分子和溶剂的Lewis酸-Lewis碱特性等。但是如何正确、有效地用于铸膜液这样一个多组分的高分子浓溶液,至今仍是一个有待深入研究的问题。
一些代表性的高分子铸膜液见表2-20~表2-24。
表2-20 纤维素均聚物的铸膜液[98]

①ethyl cellulose perfluorobutyrate(乙基纤维素全氟丁酸酯)。
②sucrose acetate isobutyrate(蔗糖乙酸异丁酸酯)。
表2-21 聚酰胺及有关均聚物的铸膜液[98]

表2-22 其他均聚物的铸膜液[98]

①原文献未指出是何种凝胶。

表2-24 聚合物共混体系的铸膜液[98]

(2)制备方法
①溶剂蒸发法 这是相转化制膜工艺中最早的方法,1920~1930年就被Bechhold等使用。
最简单的情况是一种高分子溶于一双组分溶剂混合物,此混合物由易挥发的良溶剂(如氯仿)和相对不易挥发的非溶剂(如水或乙醇)组成。将此铸膜液在玻璃板上铺展成一薄层,随着易挥发的良溶剂不断蒸发逸出,非溶剂的比例愈来愈大,高分子就沉淀析出,形成薄膜,这一方法也称干法。
溶剂蒸发法铸膜液中的高分子状态在膜形成过程中经历图2-21所示的变化。刚配制的铸膜液如图2-21(a)所示,在胶体水平上是均匀的——溶胶1。随着溶剂的蒸发,高分子在剩下的溶剂混合物中时溶解性不断降低,直至留下的溶剂体系的溶解能力不足以维持图(a)状态,于是发生向另一状态[见图(b)]——溶胶2转化,这时大部分聚合物分子处于已经形成的微胞内,少部分聚合物分子(约0.5%)仍留下并分散在含微胞的液态母体之中。随着溶剂继续蒸发,微胞互相靠近[见图(c)],终使其在凝胶化的开始相中彼此接触[见图(d)],当凝胶网络收缩时,微胞变形成为多面体,聚合物分子间相互缠绕[见图(e)]。最后在形成有很大总表面积的无数微胞过程中,形成了凝胶网络化的裤管状骨架[见图(f)]。其相图如图2-22所示。

图2-21 溶剂蒸发成膜过程中高分子状态变化

图2-22 溶剂蒸发法制备多孔膜的铸膜液组成变化相图
1—原始铸膜液;2—两相区;3—单相区
大多数溶剂蒸发法铸膜液含有三个或更多个组分。
决定溶剂蒸发法膜的孔隙率和孔大小及其分布的主要因素有:
a.溶胶2中聚合物体积浓度,反比于凝胶孔隙率;
b.溶胶2中非溶剂与聚合物体积之比正比于凝胶孔隙率;
c.溶剂和非溶剂之间的沸点差正比于孔隙率和孔大小;
d.相对湿度正比于孔隙率和孔大小;
e.添加其他相容性不太好的聚合物可增大孔隙率;
f.高分子量聚合物会增大孔隙率。
由于非溶剂的存在,一方面溶剂体系承受高浓度高分子的能力大受限制,而另一方面铸膜液又必须有足够的黏性,这个矛盾可以通过以下方法来解决:制备特殊的高分子量聚合物、使用增黏剂(如加进第二种聚合物或高度分散的胶体二氧化硅)、在低温下铸膜等。
②湿气诱导相转化法 高分子铸膜液在平板上铺展成一薄层后,在溶剂蒸发的同时,吸入潮湿环境中的水蒸气使高分子从铸膜液中析出进行相分离,这一过程的相图见图2-23。这一过程有别于水滴模板制备蜂窝状均孔膜,铸膜液所采用的溶剂是与水完全互溶的非质子极性溶剂(如N,N-二甲基甲酰胺、N,N-二甲基乙酰胺、N-甲基吡咯烷酮等),能够诱导水蒸气的吸入。

图2-23 湿气诱导相转化法制备多孔膜的铸膜液组成变化相图
1—原始铸膜液;2—两相区;3—单相区
湿气诱导相转化法是商品相转化分离膜的一种常用的生产方法。图2-24是Hiley等用的设备工艺流程图。

图2-24 湿气诱导相转化法制备多孔膜工艺流程示意图
1—铸膜液;2—刮刀;3—环境腔;4—膜;5—卷膜辊筒;6—不锈钢带
典型的铸膜液组成中膜材料是醋酸纤维素或硝酸纤维素,溶剂为丙酮加水(或乙醇或乙二醇)。铸膜液铺展在一连续滚动的不锈钢薄板上,通过一连串具有特殊环境条件的空间,第一个空间充满热潮湿空气,铸膜液失去易挥发溶剂同时吸入水蒸气,整个高分子沉淀过程约需10min才能完成,这时膜的结构是对称的。然后膜进入第二空室,室中充满对流的干燥热空气,它使膜内残存的溶剂全部挥发掉而变成干膜。制膜时速度一般为0.3~0.6m/min。
③热致相分离法 英文缩写为TIPS法,是Castro发明的,它是利用一种潜在的溶剂(高温时能溶解成膜聚合物,低温时不能溶解)在高温时与成膜聚合物配成均相铸膜液,并热压或挤出成膜,然后冷却发生沉淀、分相,潜在的溶剂也可称为成膜聚合物的稀释剂。具体步骤如下。
a.在高温下将成膜聚合物与低分子稀释剂熔融混合成一均匀的溶液。
b.将溶液制成所需的形状(平板或中空)。
c.将溶液冷却使之发生相分离。
d.将稀释剂从膜中除去(一般用溶剂抽提)。
热致相分离法既适用于极性,又适用于非极性高分子,成膜聚合物包括聚乙烯、聚丙烯、聚偏氟乙烯、尼龙等,主要的稀释剂有二苯醚、二苯酮、石蜡、磷酸三乙酯等。成膜聚合物及其相对应的稀释剂如表2-25所示。其中TIPS法制备聚丙烯和聚偏氟乙烯中空纤维膜已经实现产业化和商业应用。
表2-25 TIPS法制备微孔膜的聚合物及其稀释剂

热致相分离法成膜过程的典型温度-组成相图如图2-25所示。图中,Tc为临界温度;为熔点。

图2-25 液液与液固相分离的温度-组成相图
1—双节线;2—旋节线
将一高分子与稀释剂的混合物(组成为φx)升温至X,在这温度混合物变为真正均相溶液。临界温度(Tc)必须小于稀释剂的沸点(一般为25~100℃)而大于高分子本身的熔点(Tm)。高分子在Tc必须是稳定的,稀释剂在Tc时应该挥发性较低。在缓慢冷却下溶液发生液-液相分离,分成两个液体,一为高分子富相(Rx),另一为高分子贫相(Lx),这时在高分子富相的流体中出现结晶及结晶生长。随着温度不断下降,两个液相的组成沿相图中实线不断变化,直至到水平的固-液线为止。这时高分子富相转变为固态,产生一种高分子结晶(聚合物体积分数为1)和一种稀释剂溶胀的无定形高分子(其组成为φm),同时高分子贫相被包裹在结晶内或被排挤在结晶之间,仍为液相。
若将一组成为φy的高分子与稀释剂混合物升温至Y,这时混合物呈真正均相溶液,然后缓慢冷却,溶液发生固-液相分离,形成一个组成由Ly代表的高分子贫相和纯聚合物相。当温度继续降低时,纯聚合物组成不变,但由于在其中结晶态增多,所以体积增加了,聚合物贫相(其中含有稀释剂和无定形聚合物)组成沿Ly线变化直至达低共熔点(偏晶点)。在低共熔点聚合物贫相进一步分离变成稀释剂-溶胀无定形聚合物和纯稀释剂两相。热致相分离法制备的非对称膜,膜的孔体积由铸膜液组成所决定,而孔分布、孔径则取决于冷却速度,冷却速度慢,形成大孔;冷却速度快,形成小孔。
热致相分离法可制平板膜和中空纤维膜,平板膜的流程示意图如2-26所示。

图2-26 热致相分离法制膜(平板膜)流程图
1—浇铸辊筒;2—抽提及后处理;3—卷膜辊筒
④非溶剂致相分离法 也称浸没沉淀相转化法,缩写为NIPS法,又称为L-S法,它是目前最重要、应用最广的非对称分离膜制备方法。20世纪60年代初Loeb和Sourirajan在研究醋酸纤维素反渗透膜时,发明了将高分子铸膜液浸入非溶剂中,通过相转化形成非对称膜的方法。与均质醋酸纤维素膜相比,这种非对称反渗透膜不但具有高脱盐率,而且其透水量比均质膜高几倍至一个数量级。电子显微镜观察发现,这种膜具有薄但非常致密的皮层以及海绵状疏松的多孔支撑层。非溶剂致相分离法是分离膜发展的里程碑,使聚合物分离膜有了工业化应用的价值,被广泛研究与应用,逐渐成为聚合物分离膜的主流制备方法。
在NIPS法制膜过程中,成膜体系至少包含3个组分,即聚合物、溶剂和非溶剂,其中溶剂和非溶剂必须完全互溶。NIPS法制备平板多孔膜的过程如图2-27所示,首先将聚合物溶解在溶剂中,配制成均一稳定的铸膜液,然后将铸膜液均匀刮涂在适当的支撑体上(玻璃板、无纺布、钢板等),然后连同支撑体浸入由非溶剂组成的凝固浴中,溶剂和非溶剂通过薄膜/凝胶浴界面相互扩散,当溶剂/非溶剂之间的交换达到一定程度,聚合物溶液变得热力学不稳定,从而发生分相。铸膜液体系分相后,随着溶剂/非溶剂的进一步交换,体系发生膜孔的凝聚、相间流动以及富聚合物相的固化等过程,最终形成具有不对称结构的固体聚合物多孔膜。

图2-27 非溶剂致相分离法制备平板多孔膜示意图
以非溶剂致相分离法制备醋酸纤维素反渗透膜的制备程序见图2-28。

图2-28 醋酸纤维素反渗透膜的制备程序
a.膜的形成机理
(a)铸膜液体系热力学。浸没沉淀相转化法工艺是通过铸膜液中溶剂与凝固浴中非溶剂相互交换而使初始热力学稳态的铸膜液产生非稳态而发生液-液相分离成膜的。因此,膜结构与铸膜液体系的相图密切相关。
图2-29是聚合物-溶剂-非溶剂三元体系液-液相分离示意图。当均匀聚合物溶液由于非溶剂浸入变成不稳定时,将导致液-液相分离,使混合Gibbs自由能最低。如果体系组成落在B、D之间,将分成组成为B'、D'的两相。

图2-29 聚合物-溶剂-非溶剂三元体系的自由能曲面和混溶区
Cr—临界点;X—聚合物贫相组成; Y—铸膜液组成;N—非溶剂;S—溶剂
三元体系完整的相图如图2-30所示细分为四个区域,图中Ⅰ是单相溶液区,由聚合物-溶剂轴和浊点线或称双节线构成;浊点线右边Ⅱ是液-液两相区。在两相区,旋节线又划分出亚稳区和非稳区,浊点线与旋节线之间是亚稳区,旋节线右边是非稳区;Ⅲ是固-液两相区;Ⅳ是单相玻璃态区。连接线表示聚合物富相与贫相对应的平衡浓度。玻璃化转变线以上区域是固态单相区,当铸膜液组分进入该区形成固态。

图2-30 三元体系典型相图
1—溶液单相区;2—双节线、浊点线;3—玻璃化转变线; 4—玻璃单相区;5—液-液两相区; 6—旋节线;7—连接线
当组成落在亚稳区或非稳区时,分相机制是不同的。亚稳区相分离是成核-成长机制,即当组分进入C时,在稀相产生核,其中超过临界尺寸的核将不断成长,直至核聚结而形成膜结构;非稳区相分离是增幅分解机制,即膜液中浓度波动在非稳区将持续增长,最后形成网络结构膜。
CP是临界点浓度,它决定液-液相分离时,是贫相成核还是富相成核。如果膜液在点CP下相分离,初生核在富相产生,连续相是稀相,最终形成的膜结构将是松散的,没有机械强度,不能使用。因此,有用的膜均要求在CP点以上发生相分离,使最终膜结构中富相是连续相,具备一定的力学性能。
制膜时,铸膜液浸入凝固浴的瞬间,溶剂迅速从膜液中扩散出,而凝胶剂则进入相当少,这时在膜液和凝固浴界面附近,聚合物浓度迅速增加,组成沿路径A-B变化直接达到玻璃化转变线,产生玻璃化转变固化,形成均质、致密玻璃态膜。玻璃化转变线越往上时,说明发生固化时要求聚合物浓度越高,这时形成皮层越致密。
一旦皮层形成,溶剂和沉淀剂的扩散受阻,相互交换的速率减小,皮层对溶剂扩散的阻碍大于对沉淀剂的内扩散。使皮层下聚合物浓度远低于皮层,膜液组成沿A-C线从Ⅰ区进入Ⅱ区而发生液-液分离C'与C″。随着溶剂与非溶剂的不断交换,富相组分浓度C将沿着浊点线上升,当穿过玻璃化转变线进入固相区D而被固化成膜,形成多孔结构,从而得到非对称膜结构。
与膜性能最为密切的是浊点线。浊点线愈靠右,意味着发生相分离所需沉淀剂量愈多,需要更长时间发生相分离,距离界面较远处膜液有充分时间进入Ⅳ区相转变,成膜时皮层愈厚。
浊点线可用滴定法测定,也可根据聚合物溶液理论计算。在铸膜液相图计算中,Flory-Huggins理论最为常用。对三元体系铸膜液,根据Flory-Huggins溶液理论,体系的Gibbs自由能ΔGm用下式表示:
式中,φi、ni分别是组分i的体积分数和物质的量;χij是组分间相互作用参数;R是气体常数;T是开尔文温度。
对上式求导,得到各组分的化学势方程,根据两相平衡时化学势相等,计算贫富两相组分浓度值,即得到浊点线和连接线。
χij表征铸膜液非理想性质,它是组成的函数。非溶剂-聚合物χij可用溶胀法测定,非溶剂-聚合物和溶剂-聚合物χij也可由溶解度参数进行估算。对小分子非溶剂-溶剂的χij可以通过活度系数计算,其活度系数值可从汽-液平衡数据求得,还可以通过其他途径如活度系数方程或功能团法得到。
理论上,对多元体系,上式应包含多元组分间相互作用参数,如对五元体系而言,包括二元组分、三元组分、四元组分、五元组分间相互作用参数。但由于三个以上分子同时碰撞在一起的概率远小于双分子碰撞的概率,再加上三元以上组分相互作用参数很难获得,因此,在具体处理时,通常都忽略三元以上相互作用参数。中国科学院大连化学物理研究所用二元相互作用参数计算了H2O/EtOH/THF/DMAC/PSF五元体系的浊点线,结果表明,理论值与实验基本吻合[119]。
(b)铸膜液固化过程。成膜过程经过液-液相分离和聚合物富相固化等步骤,富相可通过结晶、半结晶或玻璃化转变等固化。对于无定形聚合物(如聚砜)溶液不存在结晶、半结晶现象。
Li等根据Berghmans提出的聚合物溶液玻璃化转变解释了聚合物富相固化机理,Berghmans机理如图2-31所示[110]。图中浊点线与玻璃化转变温度线相交,交点B称Berghmans点。

图2-31 无定形聚合物凝胶Berghmans机理相图(二元体系)
Tg—玻璃化转变温度;Tgel—凝胶温度; B—Berghmans点,表示体系的双节点与玻璃化转变温度线交点
根据Berghmans机理,如果沿A虚线冷却均匀溶液至浊点线,溶液开始液-液相分离,形成聚合物贫相与富相,继续冷却,富相组成沿双节线变动最终到达B点,发生玻璃化转变而固化。
通常人们在室温制膜,固化也在室温(如25℃)进行,即Berghmans点温度是室温,而一般配制的铸膜液的玻璃化转变温度低于室温。当将铸膜液浸入沉淀浴后,膜液中溶剂与浴中的非溶剂相互交换,产生分相,随着交换继续进行,富相聚合物浓度增加,玻璃化转变温度不断提高,达到Berghmans温度时,富相发生玻璃化转变而被固化。
玻璃化转变时的聚合物浓度与铸膜液中组分有关。对H2O/NMP/PES体系,由于H2O的玻璃化转变温度与NMP相近,H2O/NMP/PES体系玻璃化转变时的聚合物浓度与NMP/PES体系相同。但对H2O/EtOH/THF/DMAC/PSF体系,中国科学院大连化学物理研究所利用聚合物自由体积进行理论分析表明:由于EtOH、THF玻璃化转变温度低于DMAC,当体系发生玻璃化转变时,聚合物浓度要高于H2O/DMAC/PSF体系。
(c)成膜过程传质动力学。在相转化成膜过程中,由于溶剂与非溶剂相互扩散,铸膜液内组分浓度是动态变化的,不同时刻铸膜液断面上浓度可处在相图不同区域内以不同的机理发生相转化,从而形成不同膜结构。
通常铸膜液初始膜厚很薄(约几百微米),而且相转化又是在很短时间内发生(<5s),很难用实验方法测定铸膜液内组分浓度分布随时间的变化。因此,通常采用适当的传质模型描述溶剂和非溶剂交换动力学,分析溶剂与非溶剂的传质现象。
根据建立传质模型所依据原理的不同,传质动力学方程可分为两大类:
一是依据Fick定律建立的,常见有William模型、Yil-maz模型、Tsay模型等;
二是依据不可逆热力学理论建立的,常见有Reuvers模型、Shijaie模型、曹义鸣等的五元模型等。
对简单二元组分扩散或虽多元但可忽略组分间耦合扩散,可用Fick定律建立传质模型。若要考虑有组分间相互作用以及多元组分间耦合扩散,通常用不可逆热力学理论来处理。
建立传质模型应考虑成膜过程中因铸膜液收缩而产生的两相界面移动、铸膜液组分之间相互作用以及溶剂与非溶剂耦合扩散效应以及凝固浴内传质等。
利用传质动力学模型计算得到的铸膜液内组分浓度轨迹线在相图上的位置,可以判断相分离类型,阐明膜非对称结构形成机理,通过计算机模拟计算,考察制膜工艺参数(如铸膜液组成、浓度,沉淀浴组成、挥发环境及时间等)对膜结构的影响。
根据铸膜液发生相分离的时间,相分离可分为瞬时相分离和延时相分离两种。所谓瞬时相分离是指铸膜液置于气相中或沉浸到沉淀浴中时相分离瞬时产生;而延时相分离则要经过一段时间后相分离才产生。两种不同相分离机制所得到的膜结构完全不同。瞬时相分离形成多孔皮层非对称膜结构,得到的膜用于微滤或超滤过程。而延时相分离则得到厚皮层膜结构,且随着延时时间延长,形成的膜更致密,得到的膜用于气体分离和渗透蒸发等。
Reuvers等用传质动力学方程计算得到的组分浓度轨迹线是否穿过三元相图中浊点线来判断铸膜液是发生瞬时相分离还是延时相分离,如图2-32所示。如果轨迹线没有穿过浊点线而位于外侧,那么液-液相分离将在玻璃板侧膜液浓度开始改变时发生,即延时相分离。如果在很短时间内,浓度轨迹线穿过浊点线,进入液-液两相区,立即发生相分离,为瞬时相分离。

图2-32 铸膜液凝胶过程浓度轨迹线
1,4—浓度轨迹线;2,5—浊点线;3,6—连接线;t—膜顶部(膜/浴界面);b—膜底部(膜/支撑体侧)
(d)支撑层中指状孔形成机理。在许多非对称膜的支撑层中存在着指状孔结构。关于指状孔形成机理已有不少文献报道,其中较引人注目的是Smolders等提出的成核-成长模型。Smolders等注意到:指状孔通常出现在膜皮层下;瞬时相分离往往产生指状孔,而延时相分离则是海绵状结构。因此提出,当铸膜液与沉淀浴接触发生瞬时分相时,在皮层下产生贫相细核,这初始核相当于新的沉淀浴,与其下面铸膜液接触。当核中溶剂浓度高时,将发生延时分相,没有新核产生。延时时间内,铸膜液本体中溶剂不断向核中扩散,核将持续成长,直至周围聚合物固化,最后形成指状孔结构(见图2-33);当核中非溶剂浓度高时,又发生瞬时相分离,这样初始细核的生长被抑制,通常形成海绵状结构。由此可见,抑制初始核产生或者抑制核生长,均可有效消除膜内指状孔产生。

图2-33 指状孔形成示意图
b.制膜工艺条件
(a)铸膜液中添加剂的作用。用于分离膜制备的高分子铸膜液,除高分子膜材枓和溶剂外,常常含有第三甚至第四组分。广义上铸膜液中除成膜聚合物和溶剂以外的任何组分都可称为添加剂,它们一般是对高分子不溶或有限溶解的有机物或无机物。添加剂的引入主要是为了改进分离膜的性能,其作用主要有以下几方面。
ⅰ.改变铸膜液中高分子的聚集状态。图2-34是膜材料(P)为醋酸纤维素(CA)、溶剂(S)为丙酮、添加剂(N)为Mg(ClO4)2和H2O(1∶8.5)三者变化与膜分离性能的关系。

图2-34 S/P、N/S和N/P对NaCl分离率的影响(操作压力0.7MPa,进料液200mg/L NaCl水溶液)
N/S和N/P增加或S/P减少都会使铸膜液中高分子的胶束聚集尺寸增大,从而导致形成较大的孔;由图2-34可知,在A方向上,S/P、N/S、N/P都是增加的,S/P的增加意味着铸膜液中高分子胶束聚集尺寸的减小,有利于形成较多数量的小孔,而N/S或N/P的增加有利于孔径的增大,这两个因素共同作用的结果是既增加了孔数又增大了孔径,因而在相同的脱盐率下,透水量增大。由此可见,要开发高通量膜,需寻求最佳的S/P和N/S值。图2-35显示,对于醋酸纤维素-丙酮-甲酰胺反渗透铸膜液体系,图中斜线部分是最佳的S/P和N/S范围。

图2-35 最佳的铸膜液组成范围
ⅱ.影响凝胶过程中溶剂与水的交换速度。图2-36是各种添加剂对凝胶化途径的影响。随着甲酰胺用量的增加,水向膜中的渗入速度和膜的多孔性都增大,结果膜的含水率增加。但是它与膜性能并不是呈简单的线性关系,如图2-37所示,甲酰胺在低浓度阶段,随着甲酰胺含量的增加,水和盐的透过速度都增大,其结果是脱盐率几乎不变,当甲酰胺含量超过30%时,盐的透过速度急速增加,脱盐率大幅下降。

图2-36 各种添加剂对凝胶化途径的影响
1—固相;2—无添加剂;3,5,7,9,10—10%、20%、30%、40%、50%的甲酰胺;4—1% ZnCl2;6—3% Mg(ClO4)2; 8—5.3% ZnCl2

图2-37 甲酰胺含量对膜性能的影响
醋酸纤维素,25%(质量分数);蒸发时间和温度, 1min,25℃;热处理时间和温度,2min,75℃;1gfd=0.978m3/(m2·d)
ⅲ.影响铸膜液表面的浓度。在铸膜液中加入低沸点有机添加剂会使铸膜液表面的高分子浓度在进入凝胶浴前显著变大,因而提高非对称膜的分离性能,使其截留能力增加,见表2-26。
表2-26 铸膜液中有机添加剂对所成膜性能的影响

①SPES-C为一种带酚酞侧链的磺化聚醚砜。
ⅳ.致孔作用。添加剂在凝胶过程中自铸膜液进入凝胶浴,这一过程造成膜中形成众多小孔。因此,一般情况下,铸膜液中加入添加剂后,分离膜的透水量都会得到不同程度的提高。
(b)溶剂蒸发速度的影响。在NIPS法制备醋酸纤维素反渗透膜时,当铸膜液铺展成一薄层后,未浸入水中凝胶化之前,有一个溶剂(丙酮)蒸发过程。由于溶剂的蒸发,铸膜液的组成发生变化,当溶剂蒸发到一定量后,铸膜液将发生相分离。图2-38中P、N、S分别表示醋酸纤维素、高氯酸镁水溶液和丙酮,相分离界线表示高分子溶液从单相向双相的转移,曲线靠近S的一侧为单相区。

图2-38 铸膜液组成、蒸发途径与相分离界线的三元相图
1—蒸发途径;2—0℃时的相分离界线
溶剂蒸发速度可以用一个特性参数——蒸发速率常数b来表征。将铸膜液流涎在一小块平板上,通过连续测定铸膜液重量随时间的变化,可得图2-39。

图2-39 膜的溶剂蒸发速度曲线
曲线的直线部分表示在该段时间内溶剂蒸发速度相同,由同一机理决定,这一阶段是溶剂初始蒸发,对膜表面孔结构的形成有重要影响。该直线段可用下式表示:
式中,Wt为时间t时膜和板的重量;W0为t为0时膜和板的重量;W∞为恒重时膜和板的重量;b为溶剂蒸发速率常数。
b可由直线斜率计算,直线的位置与斜率在给定的温度和铸膜液组成条件下,还取决于蒸发条件、膜的面积和膜的厚度。膜面积不同只改变直线位置、不改变斜率,膜厚度改变使直线的位置与斜率同时改变,因此测定b值时必须考虑和消除膜厚的影响。
b对NIPS法制备的醋酸纤维素反渗透膜具有十分重要的意义。从图2-40和表2-27可见,在相同的铸膜液组成时,只需要简单地改变铸膜液温度、环境的湿度和气氛,就能改变蒸发速率常数,从而提高透水速度;用曲线7的制膜条件,可以在相同脱盐率下获得最大透水速度,它对应的b,既非最高也不是最低,因此要获得最佳性能的膜应当有一个恰当的溶剂蒸发速度。

图2-40 制膜液温度和溶剂蒸发速度对膜性能的影响
操作压力1.7MPa,进料液3500mg/L NaCl水溶液,有效膜面积7.6cm21~7—膜编号,见表2-27
表2-27 制膜条件、蒸发速率常数对膜性能的影响

溶剂蒸发速率常数的另一重要意义是对不同的膜,只要铸膜液组成和溶剂蒸发速率常数相同,则膜的性能也相同(见表2-28和图2-41)。
表2-28 膜6和膜8的制膜条件


图2-41 膜6和膜8性能的比较
膜6;
膜8,在18℃中蒸发1min;
膜8,在18℃中蒸发2min,制膜液温度0℃
有不少反渗透、超滤等分离膜的铸膜液采用高沸点溶剂(DMAC、NMP等)或者制备过程没有溶剂蒸发这一步,上述的溶剂蒸发速率常数就不适用了。例如杜邦公司推出的B-9、B-10芳香聚酰胺型非对称反渗透膜,它是采用高沸点溶剂,铸膜液在进入水凝固浴前必须在 80~100℃下加热蒸发10~30min。这类膜的脱盐率与溶剂蒸发时间之间存在着一个突变点(图2-42),低于某一蒸发时间,膜脱盐率只有20%~40%,透水量非常大,膜的断面具有与上表皮层相连的指状大孔;若超过某一加热蒸发时间,则脱盐率迅速增至95%以上,水通量大幅度下降,膜断面具有与上表面不相连的针状大孔。以上现象与加热蒸发的环境条件无关。

图2-42 加热蒸发时间与脱盐率
(c)凝胶过程。凝胶过程是NIPS法制备分离膜的关键阶段,它使铸膜液相转化过程在一个对高分子膜材枓是非溶剂的槽中最终完成。一般的凝胶介质是水或水溶液。
凝胶过程中水和溶剂的交换速度决定分离膜的最终结构和性能,影响交换速度的因素主要有两个:一是凝胶介质,二是凝胶温度。
凝胶介质与溶剂的化学位差大、凝胶时溶剂与凝胶介质之间的交换速度快、铸膜液中高分子的沉淀速度也快,反之亦然。溶剂与凝胶介质(亦称沉淀剂)的化学位差一般不易测得,但可以用比较它们的混合热大小来类推。图2-43显示,混合热大的沉淀剂,凝胶时交换速度快,膜断面呈指状大孔结构;混合热小的沉淀剂,凝胶时交换速度慢,膜的断面为海绵状小孔。

图2-43 溶剂-沉淀剂混合时温度的增加对膜沉淀速度的影响
改变溶剂与沉淀剂化学位差的办法有三:一是换沉淀剂;二是在沉淀剂中加入第二或第三组分(例如在沉淀剂中加入溶剂);三是在铸膜液中加入第三或第四组分(即添加剂)。各种铸膜液都可通过上述方法,调节凝胶过程中溶剂与沉淀剂的交换速度,使所成膜达到最佳结构(图2-44)。

图2-44 不同的水渗入速度和溶剂扩散速度对凝胶化途径的影响
一般情况下凝胶时铸膜液和凝胶介质都为室温,如果升高或降低凝胶介质的温度,实际上就是改变高分子沉淀速度,会对膜的结构和性能发生重大影响。表2-29结果显示,凝胶介质温度升高,膜的透水量增加,脱盐率下降。
表2-29 凝胶槽温度的影响①

①制膜液组成:醋酸纤维素22.2g,丙酮66.7g,水10.0g,ZnCl2 5.0g(流延厚度0.25mm)。
(d)热处理。NIPS法制备的醋酸纤维素反渗透膜,在凝胶相转化后必须进行热处理,即将膜在80℃左右的热水中保持若干分钟,此时膜发生部分脱水收缩。热处理前,膜属于多孔超滤膜类型;热处理后,脱盐率增加、透水量下降,成为反渗透膜。
图2-45是三种醋酸纤维素膜的热处理温度与脱盐率变化的关系。由图可见,随着热处理温度上升,三种膜的脱盐率均上升。在相同的脱盐率下,较高的热处理温度反映了膜表面层有较大的初始平均孔径,热处理温度范围越窄,反映了膜表面层的孔径分布也越窄,因此可以定性看到,膜18的表面层具有较大的初始平均孔径和窄的孔径分布,而膜316表面层具有最小的初始平均孔径和宽的孔径分布,膜602处于中间。

图2-45 三种膜的收缩温度图
经过热处理的膜在使用中由于孔结构不够稳定,在压力下容易引起膜的压密,可以通过预压处理使孔结构稳定化,预压的压力通常比最高操作压力高15%~20%,预压时间为2~3h。芳香聚酰胺类非对称反渗透膜和用NIPS法制备的其他有机非对称分离膜,都不需经过热处理和预压处理。
(e)湿膜的保存与干化。NIPS法制备的分离膜最终是带水的湿膜,如何将它保存到使用时性能不发生变化,一般采用两种方法。
ⅰ.湿法保存:在使用前膜始终不离开水,为了防止膜在储存及运输过程中的水解、微生物分解及污染、冻结等,必须调节其pH并加入一些其他化学试剂,例如加入甲醛可以杀菌,加甘油可以防冻。不同的膜保存条件不一样,商品湿膜一般将其密封在塑料袋内,并注明有效期。
ⅱ.湿膜的脱水处理:湿膜若任其自然失水,结构发生不可逆变化,再润湿后其分离性能也得不到恢复。因此必须寻找一种使湿膜脱水变为干膜,其结构保持基本不变,当使用时复湿仍能维持原有分离性能的方法,这样有利于保存、运输和应用。湿膜脱水主要防止膜在干燥时的收缩变形,通常采用的湿膜脱水剂的主要成分是甘油等多元醇、表面活性剂、杀菌剂等。不同的分离膜脱水剂各不相同。
表2-30是用表面活性剂和增塑剂处理醋酸纤维素反渗透膜,然后在40~50℃、相对湿度(RH)为70% 条件下干燥、储存不同时间后再复湿后的性能比较。
表2-30 干态储存的性能

表2-31是醋酸纤维素超滤膜的不同脱水处理方法比较。
表2-31 膜脱水法对膜性能的影响

图2-46是三种表面活性剂在不同浓度和干燥温度时对聚砜酰胺超滤膜透水速度的影响。

图2-46 表面活性剂与膜性能的关系
1—Tween 20,室温风干;2—Tween 20,80℃干燥; 3—Triton 100,室温风干;4—Triton 100,80℃干燥; 5—十二烷基磺酸钠,室温风干; 6—十二烷基磺酸钠,80℃干燥
聚砜超滤膜用0.2%十二烷基磺酸钠(SDS)水溶液浸泡5~6d,在RH 88%下室温干燥,效果很好。
(f)具体操作注意事项。NIPS法制备非对称分离膜步骤较多,影响因素复杂,为了使膜的性能获得良好的重现性,具体操作时应重视以下几方面。由于极性成膜聚合物和极性溶剂的吸水性,要注意恒定它们的水分含量,必要时高分子材料与溶剂需进行纯化;高分子材料-溶剂-添加剂的完全溶解与熟化,表面均匀的铸膜液往往是分子分散的热力学不稳定体系,这种体系迟早会分相;铸膜液中的机械杂质可以在惰性气体中用压滤法除去,采用200~240目的滤网可以满足要求,残存在铸膜液中的气体用减压法去除。在含有丙酮等低沸点溶剂时,采用静置法去除;为了防止溶剂的挥发和某些组分(如甲酰胺)的自聚,铸膜液应在密封避光条件下保存,流延用的玻璃板以1∶1的无水酒精和乙醚溶液清洗,能有效地去除油脂;铸膜液流延时,要防止气体夹带;制膜和溶剂蒸发时要注意控制环境温度、湿度与气氛的恒定,避免周围气流的湍动,气流的湍动往往是造成膜缺陷——针孔或亮点的原因之一;膜在凝胶固化时,为了使溶剂和添加剂从膜中完全浸出,根据膜的不同形状,需要保持数小时至若干天;膜蒸发时接触空气的一侧是膜的致密皮层,该表面接触被分离的溶液;膜的热处理使膜孔径收缩,导致分离率上升而透量下降,因而要注意控制热处理的温度与时间。
⑤自组装-相转化复合法 2007年,德国的K.V.Peinemann和V.Abetz报道了一种新的相转化制膜方法——自组装非溶剂诱导相分离制膜法(SNIPS法)[120]。SNIPS法和普通NIPS法的最大不同之处在于SNIPS在成膜过程中利用嵌段聚合物的自组装能力并借助NIPS将预先形成的有序结构予以冻结,从而实现对膜孔结构的可控制备。
采用SNIPS法制备的聚合物膜的显著特征包括:膜孔在分离层上以正六边形或正四边形排列;表面孔结构呈现单分散性,且孔密度极高(>1014~1015个/m2);纯水通量比常规NIPS法制备的聚合物膜高10~100倍[121-123]。
SNIPS法制膜过程一般包括以下步骤:将嵌段共聚物溶解到合适的溶剂中形成铸膜液;将铸膜液刮涂到洁净的玻璃板或无纺布等支撑材料上;在空气中停留5~20s;浸入到非溶剂中(如去离子水)实现相转化。其过程如图2-47所示[124]。

图2-47 SNIPS法制膜的一般步骤(a)及所制备的聚合物膜的典型结构(b)
除了使用的成膜材料为嵌段共聚物以及让铸膜液在空气中作适当停留之外,SNIPS法的实现过程无限接近于传统的NIPS法。由于嵌段共聚物的自组装特性,决定了所形成的均孔膜在理论上必须具备相应的孔结构,并具备良好的可重复性。
对于SNIPS过程中均孔结构形成的机理,研究者们认为嵌段共聚物形成的聚集体在铸膜液体系中就已经存在。只不过在聚合物溶液刮涂成平板薄膜之后,随着溶剂的挥发,球形聚集体会进一步自发组装形成有序排列,以减少溶剂挥发造成聚集体彼此之间的拥挤,是能量降低而熵增大的过程。这一解释从动力学上解释了有序结构在成膜过程中快速形成的直接原因;能够解释嵌段共聚物只有在合适的聚合物浓度下才能够形成均孔膜,而且刚好在此浓度范围的铸膜液体系能够检测到聚集体存在的相关信号,高于或低于此浓度区间均不能形成有序结构;溶液中聚集体和最终形成均孔膜的有序结构相符,溶液中聚集体是何种排列,形成的均孔膜最终就是何种有序排列。
嵌段聚合物在铸膜液中形成胶束的观点也能得到小角光散射(SAXS)、低温冷冻透射电镜(cryo-TEM)、动态光散射(DLS)以及耗散粒子动力学模拟(DPD)等相关直接证明(图2-48)。

图2-48 SNIPS过程中在铸膜液中存在聚集体的相关证据[124,125]
(a)铸膜液的SAXS检测结果;(b)从17%浓度(质量分数)的铸膜液制备的聚合物均孔膜;(c)对(b)中电镜图片的分析拟合得到的FFT数据;(d)耗散粒子动力学模拟得到嵌段共聚物在溶液中的状态;(e)铸膜液低温透射电镜观察到的聚集态结构;(f)在较高浓度下制备的聚合物膜的典型结构
用于SNIPS法成膜的聚合物主要为聚苯乙烯的嵌段共聚物,包括聚苯乙烯-嵌段-聚(4-乙烯基吡啶)(PS-b-P4VP)、聚苯乙烯-嵌段-聚(2-乙烯基吡啶)(PS-b-P2VP),聚(4-三甲基硅烷苯乙烯)-嵌段-聚(4-乙烯基吡啶)(PTMSS-b-P4VP)、聚氧乙烯-嵌段-聚苯乙烯-聚(2-乙烯基吡啶)(PEO-b-PS-b-P2VP),以及聚(异戊二烯)-嵌段-聚苯乙烯-嵌段-聚(4-乙烯基吡啶)(PI-b-PS-b-P4VP)等。
2.2.2.2 复合膜
对于非对称分离膜而言,膜的渗透性与皮层的厚度大致成反比,所以降低分离层厚度是提高膜渗透性的有效途径。Anderson等根据高分子溶液的松弛理论,计算出CA/丙酮体系非对称反渗透膜的皮层厚度约为0.1μm,再变薄就困难了。另外,在压力下由于高分子膜被压密,使膜的透水量下降。相转化法制备的非对称反渗透膜的压密主要发生在介于表面致密层和下部多孔支撑层之间的过渡层。
假如采用其他制膜工艺,分别制备致密皮层和多孔支撑层,这样既可减小致密皮层的厚度,又可消除容易引起压密的过渡层,从而提高膜的渗透性和抗压密性,这是当年设计复合膜工艺的基本思路。1963年Riley首先采用分别制备超薄脱盐层和多孔支撑层,然后再将二者进行复合的制膜工艺,制出反渗透复合膜,这种复合膜又称为薄层复合膜(TFC膜)。致密皮层厚度一般可达50nm左右,最薄的为30nm。
与通过相转化法制备的非对称膜不同的是,复合膜的分离层和支撑层是分开制备的。复合膜的支撑层常常选用聚砜、聚丙烯腈、聚丙烯、聚偏氟乙烯等膜材料。多孔支撑膜的孔结构、孔隙率、孔径及其分布将直接影响分离层的形成和结构,从而影响整个复合膜的传质特性。通常,支撑膜的孔径大、孔隙率高有利于提高膜通量;小孔径支撑层具有较好的耐压性;海绵状孔的力学性能优于指状大孔,耐压性更好;支撑膜指状孔方向越与分离层垂直,越有利于提高复合膜的耐压性能;支撑层中应尽量避免大孔,以保证分离层的结构完整性。
与均质膜相比,复合膜具有以下特点:
①可以分别优选不同的膜材料制备致密皮层(也称超薄脱盐层)和多孔支撑层,使它们的功能分别达到最佳化。
②可以用不同方法制备高交联度和带离子性基团的致密皮层,从而使膜对无机物和有机小分子具有良好的分辨率,以及良好的物理化学稳定性和耐压密性。
在支撑膜上形成复合分离层的主要方法包括界面聚合、原位沉积、层层自组装、浸涂等方法。
(1)界面聚合
1972年,Cadotte等首次采用界面聚合法制备了不对称结构的聚酰胺复合膜,这一突破是膜技术发展史上的重要突破[126]。界面聚合是利用两种反应活性很高的单体(或预聚物)在两个不互溶的溶剂界面处发生聚合反应,从而在多孔支撑膜上形成薄的分离层。以由哌嗪(PIP)和均苯三甲酰氯(TMC)为功能单体制备的聚酰胺纳滤膜NS-300为例,其制备方法是:将聚砜多孔膜浸入到PIP的水相溶液中,浸渍一定时间后,去除膜表面多余的水溶液;再将其浸入到TMC的正己烷溶液中,反应一定时间后,用试剂清洗膜的表面,去除未反应的物质;最后经热固化处理得到聚酰胺复合纳滤膜NS-300(图2-49)。这种聚酰胺复合膜与此前的NIPS相转化法制备不对称纳滤膜相比,操作压力大幅度降低,水通量和盐截留率都有较大程度的提高。这一制膜技术现已成为纳滤膜/反渗透膜生产的主要方法。

图2-49 界面聚合法制备NS-300聚酰胺复合纳滤膜反应式和过程示意图
界面聚合制备的聚酰胺复合膜性能主要取决于聚酰胺活性层的交联致密度、皮层厚度、粗糙度、亲水性以及化学官能团活性等,其中所用界面聚合单体的种类和性质对上述综合性能起到了决定性作用。表2-32列出了常见与最新研究报道的用于聚酰胺反渗透膜/纳滤膜制备的多元胺单体和多元酰氯单体,此外,界面聚合法制备复合膜的性质受到很多因素的影响,如支撑膜性质(如亲水性、膜的孔径和孔隙率等)的影响,界面聚合条件的影响(单体浓度及其配比、溶剂类型、反应温度及时间等)和后处理工艺(膜的清洗和热固化条件)等都会影响最终膜的性能。
表2-32 用于制备聚酰胺反渗透膜/纳滤膜的单体[127]


(2)原位沉积
原位沉积制备复合膜可以采用动态的过滤沉积实现,也可以通过浸涂方法实现。以加压闭合循环流动的方式,使胶体粒子、微粒、聚合物等附着沉积在多孔支撑体表面以形成薄层底膜,然后再用高分子聚电解质稀溶液同样以加压闭合循环流动的方式,将它附着沉积在底膜上,可制备具有溶质分离性能、有双层结构的反渗透复合膜。
几乎所有的无机与有机聚电解质都可以作为沉积膜材料。在无机电解质中有Al3+、Fe3+、Si4+、Th4+、V4+、U4+等的水合氧化物或氢氧化物,其中Zr4+的性能最好;在有机聚电解质中有聚丙烯酸(PAA)、聚乙烯磺酸、聚马来酸、聚乙烯胺、聚苯乙烯磺酸、聚乙烯基吡啶、聚谷氨酸等;某些中性的非聚电解质如甲基纤维素、聚氧化乙烯、聚丙烯酰胺,以及某些天然物如黏土、腐殖酸、乳清、纸浆废液等也能作为动态膜材科。
原位沉积膜的多孔支撑体可用陶瓷、烧结金属、烧结玻璃、炭等无机材料以及醋酸纤维素、聚氯乙烯、聚酰胺、四氟乙烯树脂等有机烧结材料,也可以采用拉伸法或相转化法制备的聚合物多孔膜。多孔支撑体孔径范围通常要求在0.01~1μm,与材质有关,最适宜范围为0.025~0.5μm。厚度没有特别限制,根据使用要求,只需保证足够的机械强度。
最早研究较多的是Zr4+-PAA双层结构的沉积膜,它是在金属氧化物形成的动态膜表面,在酸性条件下再附着一层聚丙烯酸,构成双层膜。这种膜透水量比一般反渗透膜高得多,其脱盐率与原料液的pH有很大关系(图2-50),另一特点是使用周期一般只有几周,最长使用寿命记录为55d,但可以用化学药品清洗,再将PAA用循环加压流动法涂上,膜的性能几乎得到恢复。双层结构膜的性能受Zr4+水合氧化物的浓度、PAA的分子量、形成膜时的pH与压力等因素的影响,适宜的PAA分子量为50000~100000。

图2-50 在Zr4+原位沉积膜上用50mg/L PAA形成薄层时pH的影响
0.05mol/L NaCl 水溶液,0.945MPa,10.7m/s, 25℃,1gfd=0.978m3/(m2·d) 0.27μm Selas微孔滤膜;
0.22μm Millipore微孔滤膜;
0.45μm Acropore 微孔滤膜
原位沉积膜也可制成单层结构的超滤膜,前述的Zr4+水合氧化物所制成的单层沉积膜就可认为是超滤膜,采用0.59μm平均孔径的微孔陶瓷管为多孔支撑体,以氢氧化铁为膜材料制成的单层结构复合膜,可用于废水处理。
(3)层层自组装
分子自组装的原理是利用分子与分子,或分子中的某一片段与另一片段之间的分子识别,通过非共价相互作用形成具有特定排列顺序的分子聚合体,分子间无数的非共价相互作用是发生自组装的关键。
层层组装技术最早报道于1966年,Iler等[128]首次利用静电相互作用,通过交替吸附的方法将正负胶体粒子沉积在带电基材表面,从而形成多层膜,但限于当时的科技水平,这一技术并未引起足够重视。直至1991年,Decher等运用阴、阳离子聚电解质静电层层自组装(ELbL)技术,成功制备了多层的超薄膜以来,层层自组装方法被越来越多地用于分离膜的制备[129,130],如气体分离膜、渗透汽化膜、反渗透膜和纳滤膜等。
基本制备过程如图2-51所示,首先将带正电荷的基片浸入与其带相反电荷的聚阴离子溶液中,静置一定时间后取出,用去离子水冲洗,去掉物理吸附的聚阴离子,并用氮气吹扫使其干燥;然后,将上述基片转移到聚阳离子溶液中,经水洗、干燥后,循环以上操作即可得到多层静电自组装膜。ELbL方法适合制备荷电反渗透膜和纳滤膜[131,132],首先,其复合物膜表面荷电性可通过最外层聚电解质的化学结构进行控制,根据Donnan静电排斥理论,可获得最佳的分离效果;其次,ELbL复合膜的厚度可通过组装层数进行调控,获得几十纳米到亚微米范围的超薄分离层,有利于提高膜的水渗透通量;再次,ELbL复合膜内部为离子交联结构,既保持了膜的亲水性,又可抑制其过度溶胀,保证良好的分离稳定性。层层组装膜的成膜驱动力不仅仅局限于静电力,其他分子间的作用力,如氢键、配位键、电荷转移、范德华力、π-π*相互作用、分子识别、共价键或几种驱动力的协同作用都可以作为组装膜成膜的驱动力。尽管上述的驱动力有弱有强,但正是由于组装体的驱动力具有多样性和协同性的特点,才为研究者们提供了在时间和空间上对组装膜进行精细调控的可能。

图2-51 静电层层自组装膜的制备过程示意图
为了提高静态层层自组装膜的制备效率,相继发展了压力驱动自组装成膜方法[133]。其基本过程是:将一定浓度的阴、阳离子聚电解质溶液在一定的压力下,交替在基膜表面动态过滤。被基膜截留的聚电解质和聚电解质复合物(聚阳离子和聚阴离子反应的产物)形成了具有一定分离作用的聚电解质自组装复合膜。进而,基于聚电解质分子链在电场下可以进行有序化,又提出了电场强化自组装法[134]。其具体过程如图2-52所示:用石墨作为阴、阳电极,平行放入料液池中,连接直流电源以调节电压。在两料液池内分别加入一定浓度的阴、阳离子聚电解质溶液。随组装过程中膜表面的电荷反转,依次将其放入与其表面所带电荷相反的聚电解质溶液中,聚电解质分子链在外加电场强化的作用下,快速吸附到膜表面上,并进行有序化重组,有效提高了组装速度。

图2-52 电场强化自组装制膜过程示意图