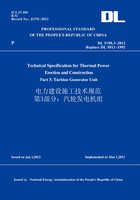
5.7 Water Inlet/Outlet Support and Cooler
5.7.1 The installation and locating of water inlet/outlet support for an internal water-cooled rotor shall be done after final locating of generator and excitation device rotors.
5.7.2 The inspection and installation of water inlet/outlet supports for an internal water-cooled rotor shall comply with the following provisions:
1 The water inlet support base plate shall be flat and free of burr,in close contact with soleplate and the connecting bolts shall be tightened homogeneously.
2 The exciter rotor shaft end flange water inlet stub shall be in secure and reliable fitting with connecting flange;the flange shall be flat and free of burr or radial groove,and it shall be tight and free of leakage after tightening the bolts on joint surfaces.
3 After the water inlet stub flange is tightened,the radial run out at the end of stub should be less than 0.05mm,and the surface of water inlet stub shall be smooth and free of damage.
4 The inside of water inlet sleeve,packing box inner surface,water seal ring inner and outer diameter surfaces,fixing flange and water inlet flange shall be flat,smooth and be cleaned.
5 The water inlet sleeve shall be kept concentric with water inlet stub when installed,the axial clearance shall be homogeneous,it shall be ensured that the water inlet flange end surface of water inlet sleeve will not contact with the water inlet stub end when the rotor has expanded in hot state,with a distance of preferably 35mm,as shown in Fig.5.7.2.

Fig.5.7.2 Schematic diagram of water inlet support
1-water inlet flange;2-Teflon ring;3-rotor;4-water inlet stub
6 The packing inside the water inlet sleeve packing box shall not contain metal wire and the sectional dimensions shall comply with manufacturer requirements;it shall be clean when packed,the overlapping technical and turns of packing front and back the water seal ring shall be correct,and after the packing is pressed tight,the water seal ring and water inlet hole shall be aligned,and be free of sundries.
7 The water seal ring and water inlet stub shall be concentric,the radial clearance shall comply with manufacturer requirements and they shall not rub each other during operation.
8 The flanges of cooling water pipe and water inlet sleeve must not be forcefully connected,to prevent deflection of water inlet sleeve center.
9 Rubber gasket shall be applied at water inlet sleeve water inlet flange,insulation sleeve and washer shall be provided for connecting bolts and nuts,and the packing box water inlet small tube shall be insulated.
10 Between the water inlet support and soleplate,adjusting shims and insulation shims shall be provided according to relevant provisions for bearing pedestals in this chapter,and after completion of installation,the insulation resistance value of water inlet pipe and soleplate shall comply with the provisions in 5.1.11.
5.7.3 The inspection and installation of water outlet supports for an internal water-cooled rotor shall comply with the following provisions:
1 Inside the rotor water outlet support shall be clean and free of casting sand or sundries,the inner and outer surfaces shall be free of porosity or crack;in the water filling test,no leakage shall occur at the pedestal body and spy hole.
2 The water outlet support and soleplate shall be in close contact,and adjusting shims shall be provided between pedestal and soleplate according to the relevant provisions in 5.2.2.
3 The horizontal joint surfaces of water outlet support shall be flat,and rubber gasket shall be provided when installed.
4 The rubber water stop ring shall be in close contact with shaft and with certain elasticity,and the hold down screw shall be locked;the radial clearance of water stop should be less than 0.5mm and be homogeneous on both left and right,and the gap at the top can be slightly larger than that at bottom.
5.7.4 When bellow couplings are provided between internal water-cooled generator rotor and exciter rotor,in addition to the inspection and measurement for semi-flexible couplings as specified in 4.6 hereof,the following provisions shall also be complied with:
1 The radial water throwing hole of the bellow cylinder shall be well through.
2 The connecting spool inside the bellow cylinder shall be smooth and clean on both internal and external sides,and the match with both ends shall comply with the requirements of manufacturer drawings.
3 The rubber sealing gasket shall be elastic,and be in close fit with the shaft hole and bottom of connecting spool.
5.7.5 Generator coolers shall be checked before installation and comply with the following provisions:
1 The inside the water chamber and shell iron plate shall be cleaned and coated with anti-corrosive material.
2 The inside of cooling tube shall be through,without residual welding slag or sundries on either side of wall,and the radiating fins shall be intact without damage.
3 During hydrostatic test,the cooler shall be placed vertically to allow vent of air.
4 For the water side,hydrostatic test shall be performed according to manufacturer requirements,the test pressure should be 1.25 times the design pressure when there is no definite requirement from the manufacturer,and there shall be no leakage when the pressure is maintained for 30min.
5 Additional expanding can be done for cooler tube expansion joints in case of any leakage,if additional expanding does not work or there is defect in tube,tube blocking is permissible,the number of tubes blocked must not exceed 3%of the total number of tubes of the cooler,and the blocked positions shall be recorded.
5.7.6 The gas cooler installed inside the generator casing shall have steel stamp mark and must not be mistaken.
5.7.7 Installation of air coolers shall comply with the following provisions:
1 Guide rails shall be horizontal and there shall be no jamming of rails with cooler rollers.
2 The longitudinal and transversal centerlines and elevation of cooler shall comply with design requirements,with permissible deviation as 10mm.
3 At the joint surfaces of cooler air chamber and air duct,packing with a thickness matching the actual condition shall be provided and it shall be tight without leakage.
4 The sloping of cooler water pipe shall facilitate drain of left water.
5.7.8 Installation of hydrogen coolers shall comply with the following provisions:
1 The cooler baffle and press plate locking bolts and press plate threads shall be cleaned,and the threaded part of bolts shall be coated with anaerobic adhesive before being tightened and locked.
2 Before removing the water inlet/outlet chamber cover,steel stamp marks shall be made with water chamber,the cooler bundle shall be thoroughly purged with compressed air,and the joint surfaces shall be cleaned.
3 The stator inner surface in contact with cooler shall be cleaned and repaired,and sundries inside be removed.
4 The tube plate of a vertical hydrogen cooler shall match with the frame in dimensions and must not be loose;the seal gasket along the baffle shall be flush over the whole length and have sufficient expanding force with the stator.
5 When a cooler is assembled on-site,press strips shall be fitted at position;seal glue shall be applied between seal frame,press strips and seal strips,and the joints of seal strips shall be bonded as specified.
6 When the cooler is inserted into the stator,the concaved side of the baffle seal bent by extrusion shall be put in the air flow direction,as shown in Fig.5.7.8.

Fig.5.7.8 Schematic diagram of air shield rubber 1-cooler frame;2-rubber pad
7 The cooler vent flange shall be connected with the vent pipe,and be routed to trench via a valve.
5.7.9 The expansion compensation seal at the end of hydrogen cooler shall meet the following provisions:
1 When rubber gasket is used as the expansion compensation seal at the end of hydrogen cooler,it should be in NBR of about 6mm in thickness;if it is stuck with rubber strip,the joint shall be oblique.
2 When aluminum gasket is used as the expansion compensation seal at the end of hydrogen cooler,the aluminum gasket shall be flat and has sufficient elasticity,at a thickness of 2mm.
5.7.10 The metal air duct of an air-cooled and dual internal water cooled generator shall meet the following provisions:
1 The metal air duct shall be flat,without apparent unevenness or twists,the duct surface shall be applied with anti-rust paint;the flange joint surfaces shall be tight without leakage.
2 The air duct shall have double wall with heat insulation material filled,to increase the efficiency of generator cooling system.
3 The air duct shall have thermal expansion compensation structure in vertical direction.
5.7.11 The ventilation system of an air-cooled and dual internal water cooled generator shall meet the following provisions:
1 The system shall be tight without leakage,tight isolation shall be provided between cold and hot air without short-circuiting.
2 When the air chamber is sealed,all parts of the chamber shall be clean and free of dust or sundries,and be coated with paint according to design requirements,and it can be sealed only after inspection and signature.
3 The air chamber door shall be locked.