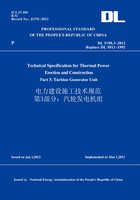
5.8 Cooling Water System
5.8.1 The installation of external cooling water piping for dual internal water cooled and water-hydrogen hydrogen-cooled generators shall comply with the following provisions:
1 All equipment,pipes,flanges and valves shall be in stainless steel.
2 Bends shall be hot-pressing or cold bending products,and threaded connecting parts should not be used in the piping system.
3 Installation of pipes and valves shall take into account convenience in operation,sampling,blowdown and flushing.
4 Before installation,pipes and fittings shall be cleaned inside,argon-arc welding shall be used for pipes,and the system shall be checked and purged after welding,to ensure no sundries will enter the generator.
5 Teflon gaskets shall be used for flanges in the system.
6 Stainless steel plate screen should be used as strainer at generator cooling water inlet,with flow area not less than 3 times the pipe flow area;the screens shall be tightly fitted inside the casing to avoid bypass of cooling water.
7 The cooling water pipe from water outlet support shall have certain sloping to ensure smooth water outflow.
8 The measuring instruments and protection devices in the piping system shall be qualified by calibration,and their locations shall facilitate inspection and maintenance.
5.8.2 The cooling water tank shall be made of stainless steel sheet or composite steel sheet,otherwise it shall be lined with rubber;the water tank shall not leak when filled with water and the inside shall be smooth without overlap;an inverted U shaped vent pipe shall be provided at the tank top.
5.8.3 On-site inspection and installation of compound corrugated umbrella plate coolers shall be performed in accordance with the following provisions:
1 The size,number of flow paths and passages and connection positions of the equipment shall be checked for conformity with design.
2 The combined compression of cooler shall comply with manufacturer requirements.
3 The flanging of all inlet and outlet stubs shall be flat and be free of warping or through groove.
4 Hydrostatic test shall be performed for the cooler as required by manufacturer,the test water shall be clean and free of sundries,and the inlet port shall be fitted with a strainer.
5 In the hydrostatic test,if serious leakage remains after tightening the bolts,it can be dismantled to check if the sealing gasket and cooling plate has damaged,the damaged cooling plate can be replaced with a new one or be removed.
6 Cooler assembling shall be done according to process diagram,and correct number of flows and channels shall be ensured,for disengaged or replaced seal gasket,binding compound required by manufacturer shall be used.
7 For the re-assembled cooler,the original dimensions shall be taken less the thickness of the removed plates and seal gaskets,the compression of seal gaskets shall be taken into account,and the compression value can be taken as 1mm.
8 For compression,the tightening bolts shall be tightened symmetrically and homogeneously,after completion of compression,the axial dimensions at the cooler corners or thickness of cooler shall be measured,and the permissible deviation is 1mm.
9 During installation,the cooling water and industrial water inlet and outlet port locations shall be verified according to manufacturer requirements.
5.8.4 Repair and installation of plate coolers shall be done with reference to the provisions in 5.8.3,and leakage test shall be performed according to manufacturer requirements.
5.8.5 After completion of installation,the cooling water system of a dual internal water cooled or waterhydrogen hydrogen-cooled generator can be put into operation only when the following has been done and it is qualified in inspection:
1 The generator cooling water system must be qualified after flushing.
2 Opening and welding work on piping system has been completed,and the packing in ion exchange filter shall be taken out.
3 Qualified condensate or demineralized water shall be used before flushing,and the water quality indicators are as shown in Table 5.8.5-1:
Table 5.8.5-1 Water quality indexes before flushing of generator cooling water system

4 In flushing,the generator external pipes shall be flushed first,and the whole system can be flushed after the water quality is qualified.
5 The maximum flow rate in the system shall be maintained during flushing.Any device in the system that may affect flow or be contaminated or damages shall be removed temporarily,and replaced with a spool for passage.The water shall first be discharged in open loop,then the flushing can be done alternatively with open loop and closed loop;when the conductivity is greater than 20μS/cm water shall be discharged for change;for a dual internal water cooled generator,if the turbo-generator unit is ready for turning,the rotor should be flushed while turning.
6 During flushing the strainer shall be cleaned periodically and must not be removed,branch instrument pipes shall be flushed with cooperation from instrument personnel,and after qualification,the relevant valves shall be closed.
7 Carbon steel pipe must not be used as a temporary pipe to be connected to the flushing circuit,clean rubber or plastic pipes with dissolvable not affecting conductivity can be used.
8 At the end of flushing,the water quality shall meet the specification in Table 5.8.5-2:
Table 5.8.5-2 Water quality indexes after flushing of generator cooling water system

Notes:1 in the insulation test,the conductivity shall be in accordance with the manufacturer requirements.
2 Dissolved oxygen is specified for a fully enclosed internal cooling water system.