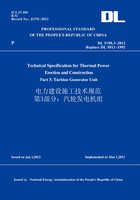
5.6 Shaft Sealing and Gas Cooling System of Hydrogen-cooled and Water-hydrogen-hydrogen-cooled Generator
5.6.1 Before installation of sealing pad base,the following shall be checked and comply with specification:
1 The horizontal joint surfaces of sealing pad base shall be in tight contact,with contact area over 75%and distributing evenly.
2 When the bolts of horizontal joint surfaces are tightened,the matching ring vertical surface of sealing pad and sealing pad base,and the matching vertical joint surface for sealing pad base and cover shall be flat without offset,there shall be no gap when checked with a 0.05mm feeler gauge at the external joint at horizontal joint surfaces;coloring check shall be made on both axial sides inside the sealing pad base and the contact surfaces shall be homogeneous and continuous.
3 The vertical joint surfaces shall be smooth,the oil chamber and hole shall be clean,through and free of sundries such as scrap iron or rust scale.
4 The sealing pad base shim shall be free of damage,the size and dimensions shall match those with sealing pad base and the materials shall comply with requirements on drawings of manufacturer.
5 The threaded connectors on the sealing pad base shall be trial fitted to confirm tight sealing.
5.6.2 Before installation of sealing pad,the following shall be checked and comply with specification:
1 The horizontal joint surfaces of sealing pad shall be in good contact,with contact area over 75%of the joint surfaces and distributing evenly.
2 The sealing ring thickness,hole diameter,ring groove width and the large shaft diameter corresponding to sealing ring and the matching gap of parts shall be measured with a micrometer,and they shall comply with requirements on manufacturer drawings.
3 When the bolts on horizontal joint surfaces are tightened,the vertical surfaces of the lower and upper halves of sealing pad shall be on the same plane without offset,and there shall be no gap when checked on a flat plate with a 0.03mm feeler gauge.
4 The vertical planes on both sides of sealing pad shall be smooth,and the non-parallelism between the two vertical planes shall be less than 0.03mm.
5 The Babbitt metal shall be free of porosity or slag inclusion,and free of dent or crack on surface,without disengagement in an oil permeation test.
6 The oil hole and ring oil chamber of sealing pad shall be smooth and free of sundries such as scrap iron or rust scale.
7 The radial clearances of sealing pad and journal shall comply with manufacturer requirements.
8 The sealing pad spring shall be checked and it shall be free of damage and its length complies with the requirements of manufacturer drawings.
9 After assembling of sealing pad and sealing pad base,a check shall be made to ensure that there is no offset between sealing pads,and the sealing pad can move freely in radial direction in the sealing pad base without jamming.
10 After assembling of sealing pad and sealing pad base,the axial clearance or play of sealing pad in the base shall be measured,and it shall comply with manufacturer requirements,as shown in Fig.5.6.2.

Fig.5.6.2 Schematic diagram of axial clearance of sealing pad in the base
5.6.3 The assembling of shaft seal device shall comply with the following provisions:
1 The stamp marks on the shaft seal device parts shall be checked,and they shall be in the right positions and comply with drawing.
2 The sealing pad base shall be concentric with journal,and the radial clearance difference shall be less than 0.15mm.
3 While the bolts on vertical joint surfaces between sealing pad base and end cover,the sealing pad shall be moved continually,to ensure that after the bolts are tightened,the sealing pads are flexible inside the base without jamming.
4 After completion of shaft seal device installation,the bolts on joint surfaces shall be locked.
5 The sealing pad locating pins shall be locked,the protruding part must not exceed the outer circular arc,the pin holes must not penetrate the pad wall,and pins must not block the pads when fitted.
6 The material of gasket between sealing pad base and cover shall comply with manufacturer requirements,it can be NBR rubber sheet when there is no specification,and the bolt hole on rubber sheet shall be larger than the hole diameter on cover.
7 The sealing oil inlet and outlet chamber on cover shall be thoroughly cleaned,and after it is qualified in inspection,the hand hole shall be blocked as required by manufacturer and be tight without leakage.
8 The oil and gas pressure sampling sockets shall be tightened without leakage.
9 When insulation to ground is specified for shaft seal device,its ground insulation resistance after installation shall comply with manufacturer requirements.
5.6.4 The oil baffle gap of shaft seal device shall comply with manufacturer requirements,and the provision in 4.5.11 can be implemented if there is no specific requirement from manufacturer.When insulation to ground is specified for oil baffle,its ground insulation resistance after installation shall comply with the provision in 5.1.11.
5.6.5 The cylinder rack and protection railing in the hydrogen control station of generator shall be securely and straightly mounted.
5.6.6 The installation of pipes of hydrogen and carbon dioxide system and of hydrogen supply system of the generator shall comply with the following provisions:
1 Stainless steel shall be used for pipes and fittings.
2 Inside the pipe shall be clean and free of sundries such as oily dirt or burr,and the connection shall be argon-arc welded.
3 The horizontal gas pipes in the plant shall have a sloping towards the drain side no less than 3/1000,and this sloping shall be no less than 2/1000 for gas supply pipes;a drain valve shall be provided at the lowest point of the pipe where water may deposit.
4 Diaphragm valves should be used in piping system,and seal tightness check shall be done for valves on pipes.
5 Vent pipes for gas containing hydrogen shall be separately connected to open space outside the building.
6 System layout shall facilitate gas substitution operation.
5.6.7 After completion of installation of generator and its gas systems,a whole set of leakage test must be done according to the provision in 5.6.9 and they must be qualified.
5.6.8 The following work shall be completed before the whole set of leakage test:
1 The generator equipment and the gas and seal oil systems shall be completely installed,the transition lead-outs for outgoing lines porcelain bushing shall be installed in place.
2 The seal oil system shall be qualified with oil circulation flushing,and be able to supply oil normally to sealing pads;the seal oil pressure shall be steadily kept above the test gas pressure inside the generator and the difference shall comply with the manufacturer requirements.
5.6.9 The test pressure and permissible gas leakage of the whole set of leakage test for the generator and gas systems must comply with manufacturer requirements,the test and calculation can be done with reference to Appendix G if there is no requirement from manufacturer,and the test work shall comply with the following provisions:
1 Before the whole set of leakage test,the hydrogen control panel,hydrogen and carbon dioxide pipes and other system equipment should be tested separately,to narrow the leakage detection range and ensure smooth carrying out of the whole set of leakage test.
2 The compressed air for test shall comply with the provision in 5.1.5,and its relative humidity shall be less than 50%.
3 A halogen leakage detector or soap solution can be used for leakage detection in leakage test.
4 In the whole set of leakage test,the water side of hydrogen cooler shall be fed with water,and the water pressure should be 0.10MPa-0.15MPa lower than the test gas pressure,to reduce the internal and external differential pressure at the cooling tube expansion joint.
5 The lower limit values should be used for leakage detection test pressure,and the pressure can be increased gradually for leakage point difficult to find,but the upper limit must not be exceeded.
6 Formal recording of gas leak rate shall be started when the gas pressure filled into the generator has reached the specified test value and stabilized for about 2h and the gas temperature inside the system has become homogeneous.
7 During gas leakage test,variation of ambient temperature of generator due to human factors shall be avoided as this will affect the accuracy of measuring result,and temperature measurement shall be done with thermometer of high precision.
8 In the gas leakage test,pressure measurement shall be done with a glass tube mercury pressure gauge or other high precision meters,in the measurement,the glass tube of a U-shaped mercury pressure gauge shall be set vertically and an inclined differential pressure gauge shall be set horizontally,and they shall not be exposed to sunlight or close to cold or heat source.
9 The gas leakage test shall continue for over 24h,and be recorded continually.The gas leak rate calculation of the generator and gas system shall be performed after completion of leak test.
10 During leak test and leak rate test of generator and gas systems,welding is strictly forbidden before the pressure in the system is released or when hydrogen is contained in the system.