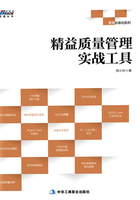
第三章 St EDEcube工位评价法
第一节 St EDEcube的定义和实施步骤
一、St EDEcube的定义
St E是standardexisting的缩写;D是Deployment的缩写,展开与执行;最后一个E, Enforcement中文翻译成强化。本工具的使用就是让生产企业员工能够正确使用标准作业,确保与标准要求一致,避免不按标准执行而导致问题发生。
我在很多中小企业做审核的时候,很喜欢问生产主管及质量主管一个问题:“你们的作业指导书/检验规范是给谁看的?”有的不回答,有的回答给审核员看的……其实,企业中很多作业员都没看作业指导书,他们可能在想这些文件都是来应付审核的,与自己没有关系。我曾经调查过一些生产组长及主管,他们的想法也一样,特别是一些搞技术的人,更加不愿意做作业指导书。为什么?
首先,作业指导书简单粗旷,给员工看基本上不能起到作业指导的作用,有的甚至是错误的。因为作业指导书的编写者都是根据自己的观点写的,很多内容都穿插了自己的主见,但作业员的水平层次不一样,有的人水平高一看就明白,有的人水平低,复杂一些就感到力不从心。
其次,很多中小企业老板自家公司的技术标准不愿意分享文件让别人学习,还有一些技术骨干不愿意把自己的技术分享给其他人。其实,在很多中小企业里,因为较多的技术被少数人掌握变成与老板谈判的筹码。有的因为被同行“挖墙角”导致公司技术流失而蒙受损失。如果把技术与经验形成文件,这样企业就不会因为人员的流失而导致技术不能得到传承的问题。有的老板会问:“如果我们把自己的核心技术做成通俗文件,也不会外传到竞争对手吗?”解决这个问题也很简单,现在已进入大数据时代,文件放在系统中设置阅读权限,根本无法复制拷贝。
二、St EDEcube实施步骤
整个评价过程分为四个部分,如表3-1所示。
表3-1 St EDEcube评价过程

(一)被评价工位现场巡视
首先,评价员需要对评价工位进行360度巡视,巡视要求如下:
(1)整体工位5S状况是否混乱,例如:工位材料是否有标识、所有材料是否按指定区域摆放好。
(2)对应作业指导书及样品是否展现出来?
(3)机台运作是否正常?
(4)作业员的操作是否流畅?
通过360度全面观察生产工位,找出一些较显著的差异并进行记录。这个方法早在20世纪30年代的丰田公司就得到运用,时任丰田公司车间主任的大野耐一先生,在每次招聘新的基层干部时会用这种方式检查应聘人员的能力与水平。应聘人员通常会被他邀请到一个车间通道的中间,然后他在过道的中间用粉笔画一个圈,应聘人员两脚站在圈中间,身体360度慢慢旋转,两眼仔细观察生产现场,两手如实记录现场问题点。大野先生当时的标准要求是:5分钟必须写出30个问题点,无论问题的大小都可以记录。如果超过时间未写完30个问题点或延期完成均视为面试不合格。
(二)standard生产工艺参数检查
第一步,检查工艺参数是否有标准。标准要求如下:
(1)适宜性:工艺参数标准是否适宜。例如:《标准工艺参数卡》中所标示的参数无法监视测量。评价判定结果分为OK和NOK,如果工艺卡中的参数无法进行监视与测量,说明生产工艺卡不适宜,直接判定为NOK。
(2)充分性:我们可以理解成标准的完整性。例如:现场评价发现较多的关键参数并未纳入《标准工艺参数卡》,如何检查工艺参数卡是否完整呢?我们可以让供应商提供此产品或类似产品的《特殊特性清单》,在此清单中可以找到产品实现的每个过程的关键特性。如果《标准工艺参数卡》不完整,评价员直接判定NOK。
(3)有效性:过程参数公差是否有效,例如:注塑过程中,《标准成型工艺卡》中要求前模模温80+/-10度,评价员要求将模温下调到下限70度时,此时产品发现黏模现象,我们称此为无效参数。因为参数并未得到验证,所以评价员可直接判定NOK。
第二步,Deproyed当第一步生产参数已被确认无异常后,评价员需进行下一步评价,即参数是否被适时监视与测量。很多企业现场都有标准要求,但是每次检查并未发现监视与测量记录。这样,所谓标准将变成一张白纸。所以,评价员在检查监视与测量记录的同时,需与机台实际显示相比对,看是否存在差异。其评价结果分为三种:
第1类:OK,评价员发现实际参数检查与标准相符合。
第2类:NOK,评价员发现实际机台参数与标准不相符。
第3类:Conditional OK,翻译成中文就是条件接受,例如:注塑成型实际模具温度测量,评价员现场发现模具温度测试值只有一个,经询问发现作业员只测量模仁的中间一个点,虽然测量值在标准要求范围内,但实际再测量模仁的四个角发现有一个角温度超出公差要求或者接近规格上下限。这种情况称之为条件OK,主要因为缺少执行标准而导致执行结果偏离规格要求。
第三步,Enforced标准参数的强化检查。中小企业总在抱怨标准无法“落地”,不能被作业员落实与执行。管理层都认为有了标准及培训,员工就会按标准执行。但实际情况与我们想象的完全不一样。事实证明,中小企业中较多的员工为了能争取多一点的休息时间,就会想出很多办法应对管理者的要求。例如:参数每隔两个小时需要进行监视与测量,有的作业员直接抄上一次的参数,并对其做轻微调整与修改。如模具温度两小时前测试记录为80度,他将修改成81度。所以,在执行的最后一步增加强化中,强化主要由作业员的直接上司来完成,通过作业员对实际参数点检并再次确认其参数点检的有效性。
(三)作业指导书
第一步,确认所评价的工位是否具有作业指导书。其评价方法同“standard生产工艺参数检查”一样,需对其作业指导书确认是否适宜、有效、充分,但对作业指导书内容基本要求如下:
(1)作业指导书是否包括到作业前准备要求。例如:穿洁净服、戴手套、指套等,作业环境如灯光要求等。
(2)标准作业内容应包括作业顺序、作业节拍及半成品的放置。生产过程中每一个动作前后都成相互关系。实际中也发现较多的作业指导书每一个动作都没有相关性,没有作业节拍,每一个操作动作必须有时间要求,然后我们要根据这些节拍来计数工位的标准工时。最后,要规定WIP半成品的摆放位置及数量。
(3)作业员质量控制。每个工位的WI应要求作业员在作业过程中或作业结束时,需对产品的质量进行自我检查与判定,我们通常称之为自检。所以,作业指导书中应包括作业员的自检内容。
(4)作业安全。现场作业很多任务位均有人机并行工作,有人机互操作的地方难免会产生一些安全隐患,那么纯手工作业有没有作业安全问题呢?如果你仔细观察现场,同样也存在安全问题。例如:很多手工作业会用到一些化学产品,有的会给作业员带来致命的安全事故。我们在一个生产现场审核过程中发现作业员不小心将502胶水挤进眼睛,按常人思维来看“这不可能”,但生产现场往往不可能的事就变成了可能。很多安全事故都是因为一些细节未做到位产生的,很多都是血淋淋的经验教训。其判定结论同上。
第二步,作业是否按作业指导书执行,评价员应先看作业指导书确认无误,再细观作业员作业是否与作业指导书相符。如果中间出现偏差,此时应要求班组长提供该员工的培训记录,如果该员工具有培训及考核记录,说明作业员未按作业指导书进行作业或培训无效果。如果作业不影响最终的结果,评价员应评价为conditional OK;如果结果会影响产品的特性,此时应判定NOK。
第三步,生产作业强化检查。评价员应检查生产工位的班组长有无对其进行强化检查,有没有确认作业员作业步骤是否与作业指导书一致。班组长每天可以抽查一个工位强化检查作业员的作业是否满足作业指导书的要求并形成记录。其评价要求与上面保持一致。
(四)质量控制
第一步,检查标准。
通过对标准作业的检查,评价员应对此工位的质量控制进行评价。同样,评价员先检查质量控制标准,例如:《产品检验规范》《控制计划》及工程样件等。检验标准应包括以下内容:
(1)检验前准备,例如:灯光强度要求、检查仪器的点检及检验规范的悬挂等。
(2)检验内容应包括所有产品特性,例如:产品功能尺寸检查、抽样比例及方法、用什么仪器去测量及样本量等。针对外观零件,外观检查应确认是否有对其进行分面检查,因为每个面的外观要求往往不同。我们通常将产品分为ABC面:A面为消费者的直观面,B面为消费者的侧视面,C面为消费者的直视的反面。我们对C面基本上可以忽略不计,但A、B面要求明显不同。之所以将产品分面来控制:一是避免一概而论;二是防止误判,将合格品判定为不合格品而产生不必要的成本损失;三是缺陷问题的界定,我们看到很多的不好的案例,如A面不能有3个黑点。这里隐含很多问题点:一是黑点的大小没有界定;二是黑点之间的距离。这样的检验规范是不能被发行的。如果企业碰到要求苛刻的客户,很快就会被客户投诉。
(3)检验的路径规划。我们正常检验作业都有一个习惯动作,但不能有一个面没有检查而流入到下一工序。所以,检验路径规划是必不可少的。按照常规,我们应把A面放在首位检查,因为A面为客户的直观面,如果放在最后检查很容易出现漏检现象。规划检验路径时,应把A面放在检验的首位,其次是B面,最后是C面。我们必须将每个面的检查内容以图文并茂的方式呈现出来,让检验员很快清楚此产品的检验要求。
(4)检验节拍时间。我们应将每个检验动作量化,以时间进行标示。一来体现检验员的检验效率;二来体现检验员的能力高低。
(5)客户投诉履历。我们往往忽略产品被投诉的履历,因为每次的投诉也反映了检验方式出现漏洞而导致不良外流至客户端。所以,有关此产品的内外部投诉均要以图文并茂的方式加入检验规范,不断更新检验规范。
如果上述内容有欠缺,评价员可直接判定为NOK。
第二步,检验标准的执行检查。
现场抽查QC首件及巡检记录,对比检验规范是否满足要求。评价员应随机抽取首件来实际核对,可以通知对应QC员现场实际测量某一个特性,对比一下测试记录是否有很大变异。我们经常发现员工因为编造一个数据或者因测量方法错误而导致数据偏差。其判定方法同上。
第三步,质量控制强化检验。
QC组长每个班次应随机抽取某一个机台或某位QC员的质量检验记录进行核查,核查方式是拿到QC员所保存的首件或巡检样品,对其进行测量并核对检验报告是否存在显著性差异。如果发现有明显差异,应及时通知责任QC要求重新测量;如果测量结果超出标准要求,应按《不合格品控制程序》执行。所有强化活动必须形成记录,评价员对其记录的有效性进行再次核对。如果发现偏差应记录不符合,详细内容写在Finding栏中。
(五)不符合项的书写要求
不符合项的书写要求符合要求,其表达方式:检查哪一份文件,结合文件要求检查现场发现了什么与标准不一致。注意不能缺少内容5W2H,即who、when、where、what、which、howandhowmany。例如:查组装作业员张某(工号210)在装配A零件时,用锤子将A零件敲入底座中,再次核对《装配作业指导书》编号××要求用手将A零件压入底座中。与标准不一致。
不符合项写完后应填写责任人及完成日期。最后,通知责任单位主管并签名确认,承诺改进完成时间及状态。