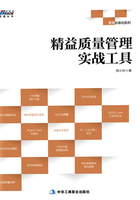
第五节 QCC案例分析
案例:改善课题——降低圆周爆接工序不良率
一、公司简介
公司名称:××××有限公司 成立时间:××××
投资金额:××万元 生产能力:××
雇员总人数:800人 主要产品:××
QCC小组名称:野狼组 组长:××
二、组立线工艺流程简介
组立线工艺流程简介如图2-14所示。

图2-14 组立线工艺流程简介
三、QCC小组简介
QCC小组简介如表2-11、表2-12所示。
表2-11 QCC小组简介1

表2-12 QCC小组简介2

四、改善活动计划
改善活动计划如表2-13所示。
表2-13 改善活动计划

五、选题理由
选题理由如图2-15所示。

图2-15 选题理由
表2-14 QCC小组简介1

六、组立线工艺流程
组立线工艺流程如图2-16所示。

图2-16 组立线工艺流程
七、目标设定(改善周期:6个月)
目标设定如图2-17所示。

图2-17 目标设定
(1)2010年7月曾达到3058PPM,已与3000PPM的目标接近。
(2)通过技术人员和焊接组长的指导,组员的技能逐步提高。
原因分析如表2-15、图2-18、图2-19所示。
表2-15 2010年4月—12月组立线圆周焊工序不良统计


图2-18 2010年4月—12月组立线圆周焊工序不良排列


图2-19 起弧不良、焊偏的原因分析(鱼骨图)
根据现场现物的原则对8个末端因素逐一进行验证。
(1)起弧不良的要因验证。
原因①:焊丝桶罩未固定,如图2-20所示。
现场检查了焊丝简罩稳定状况:生产2465PCS,落地1次,产生1台不良,不良率:406PPM。

图2-20 焊丝桶罩未固定
原因②:送丝管弯曲多,如图2-21所示。
现场进行对比实验:送丝管曲处多,送丝不畅,产生起弧不良。

图2-21 送丝管弯曲多
原因③:送丝管清扫次数少。
现场确认送丝管干净度及清扫记录,每月清扫2次,送丝管干净,现场确认非要因。
原因④:托盘清扫次数少。
现场检查托盘干净度及清扫记录,每班2次清扫,托盘干净。
(2)现场确认非要因。
原因①:同心度校正方法不当,如图2-22所示。
用目视与百分表校正同心度两种方法进行对比试验,目视校正误差较大,焊偏不良产生。

图2-22 同心度校正方法不当
原因②:吸入栓保护盖安装不良。
现场检查全部焊机吸入栓保护,盖安装情况及其影响,全部保护盖安装合格,无碰撞,定位良好。现场确认非要因。
原因③:定位块设计不完善,如图2-23所示。
现场确认使用中的30个托盘定位块的使用情况,10个托盘定位块有被焊渣卡死现象,压缩机易被夹偏。

图2-23 定位块设计不完善
原因④:焊接知识培训少。
抽查员工培训记录,现场考核作业者对不良的判断能力。半年内人均培训不到20小时,40%的作业者不良判定能力差,焊接技能不足。确认为要因。
(1)起弧不良的要因:
●焊丝桶罩未固定。
●送丝管弯曲多。
(2)焊偏的要因:
●同心度校正方法不当。
●定位块设计不完善。
●焊接知识培训少。
制定对策如表2-16所示。

实施一:焊丝桶罩改善——安装三个固定片。
改善前如图2-24所示。

图2-24 焊丝桶罩改善前
改善后如图2-24所示。

图2-25 焊丝桶罩改善后
实施二:送丝途径改善。
送丝途径改善前如图2-26所示。
送丝途径改善后如图2-27所示。

图2-26 送丝途径改善前

图2-27 送丝途径改善后
对策一、对策二实施效果如表2-17所示。
表2-17 对策一、对策二实施效果

实施三:旋转同心度保证——1次/月用百分表校正旋转同心度。
旋转同心度改善前如图2-28所示。

图2-28 旋转同心度改善前
旋转同心度改善后如图2-29所示。

图2-29 旋转同心度改善后
实施四:定位块改善。
定位块改善前如图2-30所示。

图2-30 定位块改善前
第一次改善:
增设防护板如图2-31所示。

图2-31 增设防护板
效果检讨:焊偏不良率对比如图2-32所示。
第二次改善:
定位块形状改善:下端磨成月牙形,如图2-33所示。
效果确认:焊偏不良对比如图2-34所示。

图2-32 焊偏不良率对比

图2-33 定位块形状改善

图2-34 焊偏不良对比
对策三、对策四实施效果如图2-35所示。

图2-35 对策三、对策四实施效果
实施五:焊接分科会及目标管理活动持续开展。
(1)以焊接分科会的形式进行焊接知识交流、学习(1次/月),如表2-18所示。
表2-18 焊接知识交流、学习

通过焊接知识的学习,作业者掌握了圆周焊的作业要领,提高了异常应对能力。
(2)作业日报填写及班别成绩公布,如图2-36所示。

图2-36 作业日报填写及班别成绩公布
(3)个人成绩每天公布:成绩优秀者奖励,促使未达标者向优秀者靠拢,如表2-37所示。

表2-37 个人成绩每天公布
2011年2月—6月圆周焊接工序不良率推移如图2-38所示。


图2-38 2011年2月—6月圆周焊接工序不良率推移
改善前后圆周焊接工序不良项目对比:改善后起弧不良、焊偏由原来的第1位、第2位降到第3位、第5位,如图2-39所示。

图2-39 改善前后圆周焊接工序不良项目对比
改善前后圆周气密泄漏不良对比:活动后泄漏不良率下降34%,如图2-40所示。

图2-40 改善前后圆周气密泄漏不良对比
巩固措施如表2-19所示。
表2-19巩固措施

不良率呈稳步下降趋势,如图2-41所示。

图2-41 效果维持
活动体会如表2-20所示。
表2-20 活动体会

为了对应2001年360万台生产,组立线今后的课题:
缩短焊接时间,降低工序不良。
项目报告完成:谢谢公司领导及QCC小组成员的支持与付出。