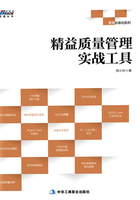
第四节 8D问题解决法
一、8D问题解决法定义
8D问题解决法(8DProblem Solving)是一种用以界定、矫正和消灭反复出现的质量问题的结构化管理方法,强调团队协同,其目的是产品和过程的改进。
8D因其包含8个解决问题的步骤而得名,其中的D,是英文“方法(Disciplines)”的首字母。8D适合以团队为单位来解决问题。8D指导思想认为,团队作为整体所拥有的智慧要远大于团队成员个体智慧的和。
8D问题解决法也被称作问题求解法或Global8D(G8D)、福特8D问题求解法(Ford8D)、团队导向的8D问题求解法(Team Oriented Problem Solving, TOPS8D)。8D问题解决法主要应用于团队作业对不合格的产品、过程问题、顾客投诉的问题进行解决的场合。
第二次世界大战期间,美国政府采用了一种类似8D的流程——“军事标准1520”,又称为“不合格品的修正行动及部署系统”。
1987年,福特汽车公司首次用书面语言的形式记载了8D法,在其一份课程手册中,这一方法被命名为“团队导向的问题解决法(Team Orien-ted Problem Solving)”。当时,福特的动力系统部门正被一些经年累月、反复出现的生产问题弄得焦头烂额,因此管理层提请福特集团提供指导课程,帮助其解决难题。
8D以系统、制式的方式解决问题,广泛应用于各种产业。因为8D法有着明显的步骤与逻辑,便于供应链中上下游间对质量问题进行沟通与整合,特别是第三方质量管理体系验证,诸如ISO9000、TS16949标准。在体系中纠正、预防措施的要求下,许多公司会要求上游供货商以8D法作为解决问题的制式方法,每当材料发生质量问题时,需交8D表以确认问题会被彻底解决。
8D虽然不是ISO/TS16949或QS9000的五个核心工具,但是被越来越多的企业用于问题解决过程,而且不仅仅限于汽车行业的供应商,例如:美国国家半导体公司(National Semiconductor)等都应用8D取得可喜效果。特别是企业的质量管理已经转向品质预防为重心的历史阶段,ISO/TS16949(QS9000)所要求的五个核心工具:PPAP、APQP、FMEA、SPC、MSA都是以预防为出发点,是十分重要且行之有效的管理工具。“智者千虑,必有一失”。事后出现/发现了问题怎么办?组织应有一套解决问题规定的过程以达到识别和消除根本原因。若有客户指定问题解决方式时,组织应使用指定的方式。8D方法便是解决这“一失”的有效过程方法,可谓“亡羊补牢,未为晚矣”。
二、8D实施步聚
8D步骤主要包括组成8D小组、描述问题、实施并验证临时性纠正措施、确认问题的根本原因、选择长期纠正措施、实施和确认长期措施、防止问题再发生、感谢团队贡献,如图1-29所示。公司可根据需要,在8D表的基础上增减、修正,但基本上涵盖问题叙述、短期对策、长期对策、防止问题再发生与文件更新等步骤。
在实施8D法之前,应做好实施8D的各项准备工作,并考虑是否一定需要应用8D(并非所有的问题都需要以团队的8D法来解决)。8D法是基于跨部门的过程管理文化,需要一定程度的持续改善的技能,在实施有效的8D法之前,组织有必要提供相应的培训。
(1)组织/建立问题解决小组。
(2)组员具备必要的知识、技能和授权。
(3)小组的目的是解决问题和执行纠正措施。

图1-29 8D步骤
(5)小组必须选出一位组长。
(1)使用可测量的术语来描述问题。
(2)使用明确的术语,明确具体地描述某个内部或外部顾客的问题。
(1)确定和执行一些暂时的(Intermediate)措施以保护顾客,直到正式的纠正措施被批准执行。
(2)用数据验证这些措施的效果。
(1)识别所有潜在的(可能的)“问题为什么会出现”的原因。
(2)对照问题描述及数据检查每一个潜在的(可能的)原因。
(3)为消除“根本原因”轮流识别纠正措施方案(两种或以上)。
(1)确认所选定的纠正措施能解决顾客问题且不会引起不希望发生的副作用。
(2)根据问题潜在的严重程度,如有必要,验证另外的措施。
(1)必须确定和执行正式的纠正措施。
(2)应持续不断地控制纠正措施的实施,以保证消除“根本原因”。
(3)当制造过程实施正式纠正措施后,监视并控制它的长期效果是必需的。
进行“修改技术规格”“提升培训”“评审作业流程”,“改善习惯做法和过程”的办法,预防该问题或所有相类似问题的再发生。
(1)认可团队完成的纠正措施。
(2)发布成果。
(3)分享和学习你们的知识。
8D分析报告如表1-15所示。
表1-15 8D分析报告

