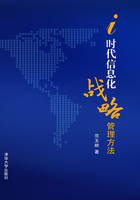
4.2 并行工程产生的背景和特点
4.2.1 并行工程产生的背景
随着市场竞争的加剧,竞争的焦点变为是否能以最短的时间开发出高质量、低成本的产品投放市场。而随着产品性能的提高和复杂性的增加,产品开发周期越来越长,采用传统的串行开发模式,会导致在设计早期阶段不能很好地考虑产品开发后期阶段的各种要求,不可避免地在后期造成较多的设计返工,导致产品开发时间和成本的增加。对产品开发成本-周期的统计分析表明,产品开发设计阶段决定了约70%的产品成本,而这一阶段本身所占的费用仅为产品总成本的5%左右,如图4-2所示。因此,在产品开发的早期阶段就考虑产品生命周期中的各种因素,在设计的早期阶段发现问题,尽可能减少后期错误修改的次数,对企业获得最佳效益至关重要。

图4-2 产品形成过程对产品成本的影响
产品开发过程是指从产品需求分析到产品最终定型的整个过程,包括产品的设计、制造、装配和测试等。传统采用的产品开发方式是一个串行流程,这是一种“抛过墙”式的开发方式,开发人员按要求完成各自任务后将结果抛向下游,出现问题后则返回上游。由于各部门间缺乏经常交流,且参与产品开发的人员往往对自己在整个过程中的角色缺乏清晰的认识,上、下游活动间可能存在不可调和的冲突,当最终出现产品的可制造性、可装配性或可维护性较差、不能很好地满足用户需求时,就需重新回到产品设计阶段,进行设计改进,使得产品开发过程变成了设计、加工、试验、修改设计的大循环,而且可能多次重复这一过程,从而导致设计改动量大、产品开发周期长和产品成本高的结果。
图4-3给出了产品形成过程中错误的发生和修改频度的分布情况,统计结果表明,在传统串行流程模式下,75%的错误是在产品形成过程引起的(早期形成),80%的修改工作是在产品制造或后续过程完成的(晚期发现和修改),而越晚改正错误花费的成本就越高、时间也越长。因此,采用传统的串行流程模式是导致产品开发成本高、开发周期长和产品质量低的主要原因。

图4-3 产品研制过程中错误发生和修改的频度分布及更改成本
除了上述问题外,传统的部门制及串行流程的产品开发模式还存在许多其他不足:
(1)设计时间在整个产品开发过程中所占比重相对较小,考虑的设计方案非常有限,最后只能选定一种特定方案执行。
(2)设计过程遵循部门制管理模式,不够灵活,部门之间的信息交流存在严重的障碍。
(3)生产规划、可制造性及可靠性等问题在开发过程中是分别考虑的,造成生产准备周期延长,更改反馈频繁。
(4)缺乏数字化产品定义,计算机辅助设计、制造、工艺、工程分析工具和面向制造的设计工具、面向装配的设计工具之间缺乏良好的信息集成。
(5)设计数据零散分布于开发过程,缺乏统一有效的管理,数据无法保持一致。缺乏跨平台的产品数据管理工具,大量工程图档、产品数据的管理与维护工作耗费了产品开发人员的大量精力,而且经常由于前后版本不一致而造成无法估量的损失。
并行工程(concurrent engineering, CE)正是在这一背景下被提出来的,它是对传统产品开发方式的一种根本性改进,是一种新的设计哲理。并行工程通过组织以产品为核心的跨部门的集成产品开发团队,改进产品开发流程,实现产品全生命周期的数字化定义和信息集成,采用新的质量哲理满足不断变化的用户需求,并采用新的计算机辅助工具,如DFA(面向装配的设计)、DFM(面向制造的设计)等,保证在产品开发过程的早期能做出正确决策,能够有效减少设计修改、缩短产品开发周期、降低产品的总成本。并行工程与传统串行产品设计方式的根本区别在于并行工程把产品开发的各个活动看成是一个整体、集成的过程,并从全局优化的角度出发,对集成过程进行管理与控制,使产品设计一次性成功。图4-4给出了串行产品开发过程与并行产品开发过程的对比情况,并行开发流程的重要特点是引入了信息预发布和反馈机制,从而使后期产品试制阶段的反馈数量大大减少。

图4-4 串行产品开发过程与并行产品开发过程的对比
并行工程具有传统设计模式所没有的优点,其技术研究和应用得到广泛重视。如美国的DICE计划投入巨资建立高校和研究机构联合的并行工程研究基地,日本的IMS计划、欧洲的ESPRIT Ⅱ&Ⅲ计划都进行了并行工程研究。国外一些著名企业通过实施并行工程取得了显著的效益,如波音公司在767开发过程中,采用数字化技术和并行工程方法,实现了五年内从设计到试飞的一次成功;洛克希德在1992年开始的新型号导弹开发中,采用并行工程的方法,将导弹开发周期从5年缩短到2年;法国的航空发动机公司SNECMA于1990年以来,把并行工程作为产品开发的基本方法,将航空发动机开发时间从原有的54个月,缩短到1992年的42个月和1998年的36个月,到2000年进一步缩短为24个月[42]。
4.2.2 并行工程的定义与特点
并行工程有代表性且被广泛采用的定义由美国国防分析研究所DARPA于1986年在R-338报告中给出:并行工程是对产品设计及其相关过程(包括制造过程和支持过程)进行并行、一体化设计的一种系统化工作模式。这种工作模式力图使开发者从一开始就考虑到产品全生命周期中的所有因素,包括质量、成本、进度和用户需求。
与传统设计模式相比,并行工程具有以下特点:
(1)并行性:在产品设计期间,尽可能并行地开展产品生命周期中的各种活动,应用团队合作、信任及信息共享机制消除由于串行过程而引起的部门分割、人员分散及信息交换障碍。
(2)质量管理:在设计初期就考虑到影响产品质量的各种因素,特别重视对用户需求的分析,销售商与用户直接参与产品设计的前期工作,可以在早期就确定部分与生产有关的设计要求。在产品开发过程的早期发现不同工程学科设计人员之间在产品功能、零部件可制造性、可装配性及可维修性等因素之间的冲突关系,最大程度地避免设计错误,减少设计的更改次数,提高质量,降低成本,使开发过程接近一次成功的目标。
(3)过程管理:良好的开发过程是提高产品设计质量的有效保证,在并行工程模式中,不仅仅重视产品本身,还更加重视产品的开发过程优化和开发过程管理。
(4)信息管理:采用高效的信息管理平台,实现在正确的时间、以正确的方式、把正确的信息传递给正确的人,从而帮助设计者做出正确的设计决策。
(5)协同性:建立多学科集成产品开发团队,在产品数据管理系统和协同产品开发支撑平台环境下,基于共同的设计目标实现协同产品开发。
(6)集成性:基于信息共享、工作流技术、计算机支持的群组工作环境技术,实现产品开发过程中的信息集成、过程集成和组织集成。