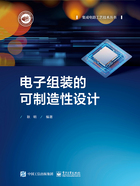
1.5 应用在电子组装的其他技术
随着新型元器件的出现,一些新技术、新工艺也随之产生,在电子组装的层级之间的交叉应用也越来越广泛。之前用于1级封装的技术也用到了2级和3级封装中,打破了传统的层级界限,从而极大地促进电子组装技术的改进、创新和发展。下面就简单介绍几种交叉技术的应用。
1.5.1 埋入技术
在多层板中预埋电阻R、电容C、电感L、滤波器组成复合元件或复合印制板,在制造多层板时,不仅可以把电阻、电容、电感、ESD元件等无源元件做在里面,需要时可以把它们放在靠近集成电路引脚的地方,甚至能够把一些有源器件做在PCB里面。这样不仅可以保证电路板的小、薄、轻,而且性能更好。埋入式元器件被制作为印制板中不可分割部分的分立或有源器件。传统电子组装和元器件埋入式组装方式如图1-39所示。

图1-39 传统电子组装和元器件埋入式组装方式
1.5.2 底部填充工艺
底部填充工艺(Underfill)一直用于元器件封装工艺中,就是对Flip-Chip芯片的底部进行填充;目前也同样用于电子组装中,对BGA/CSP封装的芯片,在经过再流焊之后将化学胶水(主要成分是环氧树脂)材料填充到器件与基板之间、芯片与基板之间的缝隙。Underfill是利用了毛细作用使得胶水迅速流过BGA底部的球间隙,然后用加热的固化形式,将BGA底部的空隙填满从而达到加固的目的,增强BGA封装芯片和PCBA之间的抗振动、抗跌落性能。当然这种胶水现在已经有可以返修的了,如乐泰3515、乐泰3568。近来为了改善CSP焊点的可靠性,底部填充工艺被越来越多地应用,如手机电路板上的CSP也采用底部填充来增加其连接强度。
BGA/CSP芯片的主成分硅(Si)的热膨胀系数(CTE)为2.8×10-6/℃,PCB材质环氧玻璃FR-4的CTE为15.8×10-6/℃,焊点的CTE为25×10-6/℃,填充环氧树脂就是为了降低硅芯片和有机基板之间的CTE不匹配问题,因为在功率循环与热循环工作中,CTE失配会导致焊点热应力,从而发生疲劳失效。为了增强BGA芯片的可靠性,防止在受热和应力的作用下拉伸焊点,填入底部填充胶水。底部填充工艺如图1-40所示。

图1-40 底部填充工艺
适合底部填充的PCB焊盘设计和良好的PCB设计可以减少或消除气孔、填充不完全的质量缺陷。以下是底部填充工艺对PCB焊盘设计的基本要求。
①PCB设计时尽可能避免把不需要底部填充的器件布局在距方形芯片边缘200μm以内。
②适当缩小焊盘面积,尽可能拉大焊盘间距以增大待填充的间隙。
③底部填充器件与周围元器件的最小间距应大于点胶针头的外径(0.7mm),如图1-41所示。

图1-41 底部填充器件与周围元器件的最小间距示意图
④所有的半通孔需要填平,并在其表面覆盖阻焊膜。开放的半通孔可能会产生空洞。
⑤阻焊膜需覆盖焊盘外所有的金属基底。
⑥减少弯曲,确保基板的平整度。
⑦尽可能消除沟渠状的阻焊膜开口以确保一致的流动性,确保阻焊膜一致、平整,没有细小间隙。
⑧减少BGA球周围暴露的材料,阻焊膜开口尺寸公差配合好,避免产生不一致的润湿效果。
1.5.3 点涂焊膏工艺
除了焊膏印刷工艺外还用到点涂焊膏,点涂焊膏有很大的灵活性,可三维点涂并且非常容易控制焊膏点的大小,自动更换机种,节省焊膏,不需要印刷钢网和其他治具,是一种非常清洁的工艺。由于点涂焊膏工艺有许多优点,因此正在被越来越多的生产厂商所采纳。
点涂焊膏的优点:
①点涂焊膏工艺不需要钢网。
②点涂焊膏工艺可作为一种非常有效的返修手段,用于中、大批量生产中,可以精确地将焊膏点涂到某一个元器件位置。对于又小又复杂的板,由于无法用手工组装和返修,这一点就显得非常重要。例如,BGA器件返修时,周围元器件密集没有足够的空间放置迷你钢网,为保证印刷质量,点涂焊膏就很方便,而且不需要对每个BGA器件制作钢网。
③与模板印刷相比,点涂的最大优点在于其灵活性。另外在一些不能印刷的场合也只能采用点涂,例如,在通孔内点涂焊膏(SPOTT)时,以及移动电话和汽车电子中采用的现代3D电路等。3D电路需要在不同高度平面点涂焊膏,这对于模板印刷而言是根本无法做到的。
实例:电路板利用特殊工艺粘在散热铜底板上,如图1-42(a)所示。在电路板上组装的大功率元器件需要很好的散热,功率元器件底部直接连接散热铜板,两个翼型引脚焊接在电路板上,如图1-42(b)所示。普通的钢网印刷是无法实现在元器件底部焊盘的焊膏涂布,可以采用放置预制焊片的方法,但常因预制焊片不平整而抬高元器件,导致元器件焊点开路或焊片振落而元器件底部少锡。像这样的组装工艺,在电路板的底部焊盘点涂焊膏,再进行再流焊很容易达到。

图1-42 点涂焊膏用于元器件组装
④可以对模板印刷起辅助作用,增加特殊焊点的焊膏量,防止再流焊缺陷发生。
1.5.4 堆叠装配技术
在1.3.2节中讲到堆叠封装(POP)是元器件的一种封装形式。在板级电路组装焊接中也出现了类似的堆叠装配技术。堆叠装配技术是PCB组装与半导体组装的最新结合交叉形式,是PCB电路高密度组装的最新成果。POP技术在PCBA的应用举例如图1-43所示。

图1-43 POP技术在PCBA的应用举例
1.POP的组装工艺
底部的封装元器件与组装板上的其他元器件一起印刷焊膏,上面堆叠的元器件采用浸蘸膏状助焊剂或焊膏的方法堆叠在底部元器件上。浸蘸膏状助焊剂的方法与晶圆级封装(WL-CSP)的贴装工艺基本相同。POP堆叠在PCB上的组装如图1-44所示。

图1-44 POP堆叠在PCB上的组装
2.POP装配的工艺关注点
①控制顶部封装元器件助焊剂和焊膏量。要求与倒装芯片浸蘸工艺相同,蘸取1/2焊球直径的高度。
②控制贴装过程中基准点的选择和压力。底部元器件以全域基准点来校正没有问题,顶层元器件应选择其底部元器件表面上的局部基准点。
③底部元器件焊膏印刷工艺的控制。底部元器件球间距为0.5mm或0.4mm的CSP,需要优化PCB焊盘的设计。
④再流焊工艺的控制。由于无铅焊接的温度较高,较薄的元器件和基板(小于0.3mm)在再流焊过程中很容易产生热变形,升温速度建议控制在1.5℃/s以内。同时监控顶部和底部元器件内部的温度,既要考虑元器件表面温度不要过高,又要保证元器件的球和焊膏熔化充分,形成好的焊点。
3.是否考虑底部填充
为了提高产品的可靠性,POP可以考虑进行底部填充工艺。对于两层堆叠,可以对上层元器件进行底部填充,也可以两层元器件都做填充。如果上、下层元器件外形尺寸相同,就没有空间单独对上层元器件进行底部填充。对上、下层元器件同时进行底部填充时,填料能否在两层元器件间完整流动需要关注。正确的点涂路径和精准的胶量,可以有效控制填料中的气泡,再流焊过程中过多的助焊剂残留会影响填料在元器件下的流动,导致气孔的产生。
1.5.5 无焊压接式连接技术
PCBA无焊压接式连接技术,又称压入式连接技术(Press Fit),是将弹性可变形插针或硬性插针嵌入印制板的金属化孔内形成的一种无焊连接,在插针与金属化孔之间形成紧密的接触点,靠机械连接实现电气连接。
随着电子产品的不断发展,产品的一致性和高密度化要求越来越高。对于细间距、多排插针的连接器,焊接技术无法完成。压接技术具有较高的可靠性、插接安全性以及易操作性,因此,压接技术至今仍然被广泛应用于通信、汽车、机车和军事行业。
1.压接与焊接工艺性能比较
压接技术与焊接技术相比,压接连接的特点和优势体现在:
①在电路板和连接器上无热应力。
②没有影响连接器可靠连接的焊接气体和焊剂残渣,环保。
③可靠性高,国际电工技术委员会规范认为此产品至少比焊接和刺破式连接器(IDC)可靠10倍。
④无焊接点短路、虚焊等缺陷。
⑤连接器压接后,一般无须再用螺钉与PCB固定。
⑥使用长插针连接器压接时,PCB背后伸出的针脚可作为背面插针,实现双面连接。
⑦快速和简单的装配工艺,压接效率高、成本低。
⑧非破坏性的快速检查。
⑨确定的接触阻抗(良好的高频特性)。
2.压接式连接器接端种类
压接式连接器的接端(压接的插针)分为刚性插针与柔性插针,如图1-45所示。在连接器压入过程中刚性插针不产生变形,PCB的孔会变形;在连接器压入过程中柔性插针会挤压而变形,PCB的孔不变形。

图1-45 刚性插针与柔性插针
3.压接区的结构
不同厂家生产的压接式连接器,其压接区的结构也不一样,常用的压接连接器和压接区的界面结构如图1-46所示。其中,鱼眼孔端子(Eye of Needle)是应用最为广泛的端子结构。

图1-46 常见压接连接器和压接区的界面结构
4.压接原理
连接器插针压接时,在插针的金属部分和其他金属之间产生类似于原子熔融的状态而使金属连成一体。通过金属相互之间压接,保持连接的电气和力学性能。
当插针受到压力时,插针和金属孔壁之间产生非常大的挤压力,使插针和金属孔壁同时受外力而发生塑性变形,保持紧密接触。当压力消失后,插针的弹性恢复原状,产生对金属孔壁的压力而形成电接触。压接原理示意图如图1-47所示。

图1-47 压接原理示意图
5.压接连接器的设备和工艺
压接连接器的设备和压接区对位如图1-48所示。压接时,将连接器放置到印制板对应的位置上,并确保压接上模、连接器、印制板和压接下模对齐,否则可能损坏印制板和连接器。
对压接的工艺要求如下:
①压接模具要与连接器相对应,不能混用。
②印制板的重复压接一般不超过三次。

图1-48 压接连接器的设备和压接区对位
③返工时退出来的连接器不能再使用。
④平压模和针压模不能混用。
1.5.6 三维模塑互连器件技术
三维模塑互连器件(Three Dimensional Molded Interconnect Devices,3D-MID)是指在注塑成型的塑料壳体的表面上,制作有电气功能的导线、图形,然后安装元器件,从而使普通的电路板具有的电气互连功能、支承元器件功能和塑料壳体的支撑、防护等功能,以及由机械实体与导电图形结合而产生的屏蔽、天线等功能集成于一体,形成所谓三维模塑互连器件,简称共形电路。3D-MID技术的应用如图1-49所示。

图1-49 3D-MID技术的应用
1.优势
(1)设计方面的优势
①三维电路载体,可供利用的空间增加;
②元器件更小、更轻;
③功能更多,设计自由度更大,有可能实现创新性功能。
(2)制造方面的优势
①采用塑料为材料,通过模具注塑成型形成基体,基础技术成熟可靠;
②减少了零部件数目,更为经济合理;
③导电图形加工步骤少,制造流程短;
④减少了组装层次,简化了安装,可靠性更高。
(3)生态经济方面的优势
①制造流程短,直接用壳体作为互连载体,投入制造的材料数量和种类都有所下降,环境友好性好;
②循环利用和处理容易;
③有害物质排放少。
2.材料的选择和设计
采用LDS技术制作3D-MID,市场上有不同品种、性能的热塑性塑料原料和供货渠道,可以根据3D-MID的应用需求进行选择。
PA6/6T(芳香化聚酰胺)是基于BASF的Ultramid尼龙,抗热形变好,适合再流焊(包括无铅再流焊);机械性能好。
聚酯类热塑性塑料PBT、PET及其共混聚合物是基于Bayer的Pocan,机械性能、电气性能好;PET的聚合物抗热形变性能好。
LCP(Liquid Crystal Polymer)液晶聚合物是基于Ticona GmbH的Vectra,流动性好;在热应力下,抗热变形性能好。
PC/ABS(聚碳酸酯/丙烯青丁二烯苯乙烯共聚物)表面性能好,机械性能好。
3.工艺流程
①注塑成型:以可激光化的改性塑料为原料,采用普通的注塑成型设备、模具和技术注塑出塑料本体。
②激光活化:用聚焦激光束投照塑料表面需要制作导电图形的部位,活化、粗糙图形部位表面。
③金属化:用化学方法在被激光活化的图形部位沉积上导电金属,从而实现在三维塑料件上制造导电图形,形成互连器件。
4.应用
3D-MID技术在美日欧等发达国家、地区已被较广泛应用,主要应用于通信、汽车电子、计算机、机电设备、医疗器械等行业领域,产品主要有连接器、电池、EM屏蔽壳、装配电子元器件、WLAN天线、LED、机械开关、电容开关、接触开关等。