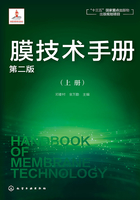
3.1 引言
3.1.1 概述
无机膜是固态膜的一种,它是由无机材料,如金属、金属氧化物、陶瓷、多孔玻璃、沸石、无机高分子材料等制成的半透膜。
建立于无机材料科学基础上的无机膜具有聚合物分离膜所无法比拟的一些优点:
①化学稳定性好,能耐酸、耐碱、耐有机溶剂;
②机械强度大,担载无机膜可承受几十个大气压的压力,并可反向冲洗;
③抗微生物能力强,不与微生物发生作用,可以在生物工程及医学科学领域中应用;
④耐高温,一般可以在400℃下操作,最高可在800℃以上操作;
⑤孔径分布窄,分离效率高。
无机膜的不足之处在于造价较高,陶瓷膜不耐强碱,并且无机材料脆性大、弹性小,给膜的成型加工及组件装备带来一定的困难。
无机膜的发展始于20世纪40年代,至今已经经历了三个阶段。第一阶段始于第二次世界大战时期的Manhattan原子弹计划,采用多孔陶瓷材料分离UF6同位素。70年代末,无机膜开始进入民用工业领域,开启了无机膜发展的第二个阶段。无机膜的工业应用首先是在法国的奶业、葡萄酒业获得成功,逐渐渗透到食品工业、环境工程、生物化工、高温气体除尘、电子行业气体净化等领域。这期间主要是发展工业用的无机微滤膜和无机超滤膜。90年代以来,无机膜的发展进入第三阶段,在无机超滤膜工业化的基础上,新型膜材料和新的制膜手段得到日益发展。无机膜市场进入了快速增长阶段,其销售额1986年为2000万美元,1991年达6600万美元,1999年达4亿美元,2014年,全球无机膜市场销售额超过10亿美元,占膜市场的14%以上。据研究咨询公司Marketsand Markets预测,2020年全球无机膜市场销售额将超过50亿美元。
我国无机膜的研究始于20世纪80年代末,通过国家自然科学基金以及各部委的支持,已经能在实验室规模制备出无机微滤膜和超滤膜以及高通量的金属钯膜,反应用膜以及微孔膜也在开发中。进入90年代,国家科技部对无机陶瓷膜的工业化技术组织了科技攻关,推进了陶瓷微滤膜的工业化进程。国家高技术研究发展计划(863计划)对无机分离催化膜的研究予以重点支持,促进了我国在这一领域的发展。进入21世纪,为支持膜材料的快速发展,科技部印发了《高性能膜材料科技发展“十二五”专项规划》,从基础研究、前沿技术、集成与应用示范等全方位布局,设立863重大专项,重点支持高性能膜材料。目前我国已实现了单管、多通道陶瓷微滤膜和超滤膜的工业化生产,并在相关的工业过程中获得成功的应用。膜反应器的基础性研究方面也具备了良好的基础,并在石油化工等领域实现了规模化应用,形成了一批无机膜生产企业,如江苏久吾高科技股份有限公司等。这些企业在无机膜材料制备技术方面逐渐积累经验,形成了自己的技术核心,总体上已处于国际先进水平,在部分领域达到了国际领先水平。但国内陶瓷膜的发展与国外先进国家相比差距依然存在,需要继续大力发展。
3.1.2 分类
无机分离膜可以分为致密膜和多孔膜两大类,致密膜主要有各类金属及其合金膜,如金属钯膜、金属银膜以及钯-镍、钯-金、钯-银合金膜,这类金属及合金膜主要是利用其对氢或氧的溶解机理而透氢或透氧,用于加氢或脱氢膜反应、超纯氢的制备以及氧化反应。另一类致密膜则是氧化物膜,主要是经三氧化二钇稳定的氧化锆(YSZ)膜、钙钛矿型氧化物膜等,这种膜是利用离子电子传导的原理而选择性透氧,其在氧化反应的膜反应器、燃料电池、传感器制造、富氧燃烧等领域具有良好的应用前景。由于致密膜的结构特性所决定,这类膜的选择性极高,但其渗透性较低,因而,提高致密无机膜材料的渗透通量是推进其工业应用的重要方向之一。
据IUPAC制定的标准,多孔无机膜按孔径范围可分为三大类:孔径大于50nm的称为大孔膜(macroporous membrane),孔径介于2~50nm的称为介孔膜(mesoporous membrane),孔径小于2nm的称为微孔膜(microporous membrane)。目前已经工业化的无机膜以大孔膜和介孔膜为主,其过滤精度处于微滤和超滤之内,而小孔径的介孔膜以及微孔膜的工业化应用报道还相对较少,这类无机膜可以实现分子级别分离,是当前研究和开发的热点。根据结构特点,无机膜又可分为非担载膜和担载膜,有工业应用价值的主要是担载膜,非担载膜主要是用于研究和实验室小规模应用。
此外,按照制膜材料,无机膜又可以分为金属膜、合金膜、陶瓷膜、碳膜、分子筛膜、玻璃膜等。
3.1.3 结构
工业用无机多孔分离膜主要由三层结构构成:多孔载体、过渡层和活性分离层。多孔载体的作用是保证膜的机械强度,对其要求是有较大的孔径和孔隙率,以增加渗透性,减少流体输送阻力。多孔载体的孔径一般在10~15μm左右,其形式有平板、管式以及多通道蜂窝状,且以后两者居多。多孔载体一般由氧化铝、氧化锆、碳、金属或碳化硅等材料制成。
所谓过渡层则是介于多孔载体和活性分离层中间的结构,有时也称为中间层。过渡层的作用是防止活性分离层制备过程中颗粒进入多孔载体孔道形成内渗,降低渗透通量。由于有过渡层的存在,多孔载体的孔径可以制备得较大,活性分离层的厚度可以制备得较薄,因而膜的总阻力较小,渗透通量较大。根据需要,过渡层可以是一层,也可以是多层,其孔径逐渐减小,以与活性分离层匹配。一般而言,过渡层的孔径在0.05~0.5μm之间,每层厚度不大于40μm。
活性分离层即是膜层,它是通过各种方法负载于多孔载体或过渡层上,分离过程主要在这层薄膜上发生。分离膜层的厚度一般为0.2~10μm,现在正在向超薄膜发展,已可以在实验室制备出几十纳米厚的超薄分离层。工业应用的分离膜孔径规格已经较为全面,从平均孔径为1nm左右的纳滤膜到平均孔径为几百纳米的微滤膜,再到平均孔径为几微米甚至几十微米的气固分离膜均已实现了商品化。此外,平均孔径小于1nm的微孔膜已有大量文献报道,相关产品市场也在快速发展。