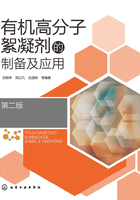
3.3 聚合型絮凝剂的制备
聚合型絮凝剂的制备方法归纳起来主要有水溶液聚合、乳液聚合(其中包括反相乳液聚合)、反相悬浮聚合3种,不过对于不同的聚合型絮凝剂,其制备方法的侧重点也有所不同[1-4]。
3.3.1 聚丙烯酸钠
聚丙烯酸钠是一种重要的精细化工产品,由于其结构为聚阴离子电解质,而且无毒,在食品、医药、纺织、化工、冶金、水处理等工业部门有广泛的用途。聚丙烯酸钠的用途与其分子量有很大关系,一般认为,分子量小于10000的产品主要用作颜料分散剂、水处理阻垢分散剂、化纤上浆剂、金属材料淬火剂、洗涤剂助剂、粒状农药载体等,分子量处于104~106之间的产品主要用作增稠剂、黏度稳定剂、保水剂等,分子量大于106的产品主要用作絮凝剂、增稠剂、吸水剂。
目前国内生产和使用的聚丙烯酸钠主要有40%胶体和95%干粉两种。40%胶体的分子量约2000万,溶解时间5~8h;95%干粉的分子量约1000万,溶解时间0.5~8h。此外,国外已有分子量大于等于3600万的胶体产品和分子量大于等于2000万的固体产品。聚丙烯酸钠的制备方法主要有水溶液聚合和反相乳液聚合两种。
3.3.1.1 水溶液聚合
聚丙烯酸钠可以用相应的单体直接在水介质中聚合而得。一般在聚合配方中包括水、丙烯酸系单体、引发剂和活性剂等。引发剂可用过硫酸铵、过硫酸钾、过氧化氢等,聚合温度可以在50~100℃的范围内选择。为了控制聚合物的链长,常使用一些链转移剂,常用的链转移剂为巯基琥珀酸、次磷酸钠和乙酸铜的混合组分。制备高分子量的聚合物,最简便的配方是10份单体、90份水和0.2份过硫酸铵。制备聚丙烯酸,则反应体系一直保持均相。
由于丙烯酸被碱中和生成盐时会产生大量热,容易引起单体在中和时的聚合,而且中和程度的不同会影响聚合度。因此,用单体的盐类来制备聚合物是会产生单体酸所没有的弊病的。但仍有一些工艺利用单体盐类的聚合方法制备聚合物,如把pH值提高到13时,可以成功地制得聚合物。用γ射线照射也可使丙烯酸盐聚合。如果把丙烯酸盐、水和引发剂组成的混合物喷射到热至150~580℃的空气中,可以使聚合和干燥一步完成。用紫外线照射丙烯酸的溶液也可以引起聚合,获得分子量很高的聚合物。
具体制备工艺为[5]:在配备有搅拌桨、温度控制器和冷凝器的1.5L的树脂反应器中加入906.79g去离子水、200g丙烯酸单体和220.34g 50%的氢氧化钠溶液,将上述混合溶液的pH值调至7.0,并加入0.20g EDTA,往上述反应体系通入氮气,氮气量为1000cm3/min,升温至45℃,加入5.00g 10% 2,2'-偶氮双(N,N-2-脒基丙烷)二氯化物溶液,聚合反应在5min内开始,反应20min后,体系溶液开始变黏稠,升温至80℃,并在78~82℃内持续反应16h,即得聚丙烯酸钠产品,所得产品在25℃下的Brookfield黏度为60000mPa·s。
水溶液聚合制备的聚丙烯酸钠溶液可以直接使用,也可以加以干燥,成为白色的、片状固体。经干燥的聚合物中,最好有5%的水分,这样在使用时就比较容易溶解。但水溶液法也存在许多不足,自由基聚合过程中反应释放的热量大,当水溶液黏度高时,热量更难均匀散去,经常出现局部过热、产物交联的现象,难以实现全自动化控制,且固含量较低,聚合物分子量分布较宽,当分子量较高时溶解性变差等[6]。
3.3.1.2 反相乳液聚合
反相乳液聚合[7,8](inverse emulsion polymerization),简单来说是指单体或单体溶液在乳化剂和搅拌作用下分散在连续相中而进行的聚合反应。工业上聚丙烯酸钠通常用溶液法制得,这种方法的不足在于聚合单体浓度低。水溶液法制备聚丙烯酸钠,要想得到固体产品,需要经过长时间干燥、粉碎等过程,工艺复杂。此外,也有人采用反相悬浮法制得聚丙烯酸钠,此法存在受搅拌速率影响大、易聚结、共沸时体系不稳定、易产生凝胶、出水时间长等问题。反相乳液聚合法制备聚丙烯酸钠是国外20世纪80年代开发出的技术。利用反相乳液法制备的聚丙烯酸钠高分子絮凝剂产品不仅克服了上述方法的缺点,从聚合到共沸出水过程体系稳定,且得到的聚丙烯酸钠具有更高的分子量和更好的溶解性。
反相乳液聚合的制备工艺为[9]:取定量丙烯酸在低温下用一定浓度的氢氧化钠溶液中和,然后加入定量的交联剂N,N-亚甲基双丙烯酰胺,搅拌溶解后得水相组分;称取定量油剂、乳化剂司盘80,搅拌溶解得油相组分;将水相与油相混合,用搅拌器在3000r/min速度下乳化,得到白色均匀乳液;向乳液中缓慢滴加引发剂(过硫酸铵与亚硫酸氢钠混合溶液),通氮排氧,升至设定的反应温度发生反应,反应结束后冷却,加入一定量的转相剂进行转相得到乳白色增稠剂乳液。
工艺的优选试验结果如下所述。
(1)反应温度
制备聚丙烯酸钠的聚合过程是一个放热反应过程,放出的大量热量会使体系温度上升,反应的稳定性会受到影响。若反应的温度过高,制备的产物分子量分布不均,且易出现爆聚现象;温度过低则使反应引发不彻底,影响单体参与反应。所以在制备增稠剂的聚合反应过程中一定要控制合适的反应温度,保证反应的稳定性。分别在10℃、20℃、30℃、40℃和50℃的温度下进行反相乳液聚合反应,随着聚合温度上升,聚丙烯酸钠(PANa)的分子量先升高,在40℃出现最大值,而后随着聚合温度的进一步升高,分子量下降。研究表明,聚合反应温度控制在40℃较为合适。
(2)引发剂
在制备聚丙烯酸钠的过程中,引发剂起引发聚合的作用,其用量的多少决定聚合的效率和产物的分子量。控制丙烯酸单体中和度为80%,引发剂比例过硫酸铵:亚硫酸氢钠=2:1(质量比)不变,其他条件按照基本工艺,通过改变引发剂的用量来合成聚丙烯酸钠。在聚合温度45℃,引发剂浓度为0.1%~0.3%范围内,当引发剂浓度为0.22%时,PANa的分子量最高;当引发剂浓度小于0.22%时,PANa的分子量随着氧化剂浓度的增大而增加;引发剂浓度大于0.22%时,PANa的分子量随着氧化剂浓度的增大而减小。所以,引发剂用量选取为占单体总质量的0.22%为宜。
(3)乳化剂
在反相乳液聚合的过程中,加入的乳化剂是不会参与反应的,但其对聚合反应的效率和聚合产物的性能具有较大的影响。根据文献,司盘80一般的使用量占单体总量的5%~10%,考察了PANa的分子量随乳化剂用量的变化。当乳化剂质量分数为8%时所得PANa分子量最高;当乳化剂质量分数小于8%时,随着乳化剂在油中含量的增加,所得PANa的分子量增加;但当乳化剂质量分数大于8%时,随着乳化剂在油中含量的增加,PANa的分子量下降。同时研究发现,乳化剂质量分数为10%时,聚合过程出现凝胶现象,这是由于乳化剂用量较多,形成的胶束数目增多,表面能过大,反应变得不稳定,出现凝胶现象。因此,乳化剂司盘80用量选取8%为宜。
(4)单体中和度
聚合过程中丙烯酸单体的中和度会影响其自身的反应性,且静电斥力的作用会影响单体的聚合和分配,因此丙烯酸的中和度会影响聚合产物的结构。单体丙烯酸在聚合前,加入氢氧化钠溶液中和,转变为丙烯酸钠之后聚合,形成PANa。当单体中和度为80%时,PANa的分子量最高;当单体中和度高于80%时;聚合物分子量较低且变化不大,单体之间的静电斥力影响聚合的发生和单体的分布,得到的聚合物的分子量较低,增稠性能降低。过高的中和度也会影响聚合物的交联程度,使呈现拉丝现象,因此单体中和度应选择80%左右。
3.3.2 聚-2-丙烯酰氨基-2-甲基丙磺酸
聚-2-丙烯酰氨基-2-甲基丙磺酸主要利用2-丙烯酰氨基-2-甲基丙磺酸单体通过自由基聚合制备而成,反应式为:

聚-2-丙烯酰氨基-2-甲基丙磺酸(AMPS)是一类能显著提高聚电解质主链离子强度的单体。其制备一般采用水溶液聚合法,具体工艺为[9]:在配备有搅拌桨、温度控制器和冷凝器的2.0L的树脂反应器中加入657.4g去离子水、344.8g 2-丙烯酰氨基-2-甲基丙磺酸单体和2.0g EDTA,加入2.0g EDTA后,升温至45℃,然后加入0.1g 2,2'-偶氮双(氨基丙烷)二氯化物,往上述反应体系通入氮气,通氮气量为1000cm3/min。15min后开始聚合反应,体系溶液开始变黏稠。反应14h后,混合物变成一种非常黏稠的透明溶液。随后将体系温度升至80℃,保温4h后加入666.6g去离子水,即可得到质量分数为12.0%的聚-2-丙烯酰氨基-2-甲基丙磺酸溶液。在1.0mol/L NaNO3溶液中测得聚-2-丙烯酰氨基-2-甲基丙磺酸溶液的特性黏数为3.73dL/g。
3.3.3 丙烯酸钠/2-丙烯酰氨基-2-甲基丙磺酸钠共聚物
丙烯酸钠/2-丙烯酰氨基-2-甲基丙磺酸钠共聚物主要是丙烯酸钠和2-丙烯酰氨基-2-甲基丙磺酸钠两种单体通过水溶液共聚而成的,具体反应式为:

制备方法[10]:向装有减压蒸馏装置的500mL三口烧瓶中加入一定量的丙烯酸和少量阻聚剂,控制水浴温度80℃,收集经减压蒸馏后的丙烯酸,密闭冷藏。在冷水浴中,用一定浓度的NaOH溶液缓慢中和丙烯酸溶液至pH=7,得丙烯酸钠(AANa)水溶液。向装有搅拌装置的三口烧瓶中加入甲苯、乳化剂司盘60、丙烯酸钠水溶液、2-丙烯酰氨基-2-甲基丙磺酸钠和乳化剂TX-10,将密闭三口烧瓶置于恒温水浴中,控制水浴温度60℃,高速乳化1h,然后加入交联剂MBA,同时向三口烧瓶中通入氮气,30min后加入引发剂BPO,并在60℃下聚合4.5h。将所得反相乳液经减压蒸馏装置脱水、离心分离,干燥后即得。
3.3.4 甲基丙烯酸钠/2-丙烯酰氨基-2-甲基丙磺酸钠共聚物
甲基丙烯酸钠/2-丙烯酰氨基-2-甲基丙磺酸钠共聚物的制备主要是利用甲基丙烯酸钠和2-丙烯酰氨基-2-甲基丙磺酸钠两种单体在水溶液介质中共聚而成,反应式为:

具体工艺为[6]:在配备有搅拌桨、温度控制器和冷凝器的1.5L的树脂反应器中加入945.59g去离子水、141.96g 58%2-丙烯酰氨基-2-甲基丙磺酸钠单体溶液、126.18g 99%甲基丙烯酸单体和114.9g 50%的氢氧化钠溶液,将上述混合溶液的pH值调至7.0后,加入0.20g EDTA,往上述反应体系通入氮气,通氮量为1000cm3/min,升温至45℃,加入0.5g 2,2'-偶氮双(N,N-2-脒基丙烷)二氯化物(V-50),聚合反应在5min内开始,反应60min后,体系溶液开始变黏稠,升温至50℃,并在48~52℃内持续反应72h,即得甲基丙烯酸钠/2-丙烯酰氨基-2-甲基丙磺酸钠共聚物,所得产品在25℃下的Brookfield黏度为61300mPa·s。在1.0mol/L NaNO3溶液中测得质量分数为15%的甲基丙烯酸钠/2-丙烯酰氨基-2-甲基丙磺酸钠共聚物溶液的特性黏数为4.26dL/g。(在聚合工艺中甲基丙烯酸钠和2-丙烯酰氨基-2-甲基丙磺酸钠的质量比为62.5:37.5。)
3.3.5 丙烯酰胺/丙烯酸(盐)共聚物
丙烯酰胺/丙烯酸(盐)共聚物的制备方法主要有水溶液聚合、反相乳液聚合和反相悬浮聚合三种。
3.3.5.1 水溶液聚合
姬彩云[11]以丙烯酰胺、丙烯酸为单体,过硫酸铵为引发剂,采用水溶液聚合法,制备了降滤失剂,得出了最佳实验条件,并考察了降滤失性能。具体工艺为:在300mL烧瓶中按照试验条件加入丙烯酸与丙烯酰胺,用氢氧化钠溶液调节pH值至7~8,以过硫酸铵为引发剂,在实验条件下进行反应,待反应完后即得丙烯酰胺/丙烯酸(盐)共聚物。他发现:用丙烯酰胺和丙烯酸合成的聚合物可以大大降低钻井液的滤失量。通过正交实验优化得到合成的最佳条件为:丙烯酰胺和丙烯酸的质量比为3:2,单体加量10%,引发剂加量0.2mL,反应温度为75℃,反应时间为3h。实验结果表明,聚合物型降滤失剂可通过吸附架桥作用有效降低钻井液滤失量。
3.3.5.2 反相乳液聚合
反相乳液法制备的丙烯酰胺/丙烯酸(钠)共聚物的产品有两种:胶乳和粉状。
制备粉状丙烯酰胺/丙烯酸钠共聚物产品的具体工艺为[12]:首先用NaOH溶液中和丙烯酸,再加入丙烯酰胺制得单体溶液;然后在250mL四口反应瓶上装上搅拌器、控温探头、温度计、导气管。向瓶中依次加入单体溶液、十二烷基磺酸钠,搅拌使其混合均匀,同时通氮驱氧20min,之后加入亚硫酸氢钠、司盘80、石油醚和过氧化物。将体系升温至反应温度,使单体聚合4h,再升温,共沸脱水,最后将固体物质过滤烘干,得到粉末状产物。通过优化工艺参数(如引发剂量、乳化剂量、抗交联剂量、单体摩尔比、油水体积比以及反应温度等),发现在最佳条件下,即乳化剂用量为0.80g、引发剂用量为2.50mL、抗交联剂用量为0.05g、单体丙烯酸与丙烯酰胺摩尔比为3.5:6.5、油水体积比为2.25:1以及反应温度为45℃时,所制备的丙烯酰胺/丙烯酸钠共聚物的特性黏数为12.07dL/g。
丙烯酰胺/丙烯酸共聚物胶乳产品的制备工艺为[13]:在0.5L四口瓶上装设搅拌器、回流冷凝器、温度计、导气管和取样器,并置于超级恒温水浴槽中,将配制好的复合乳化剂和200#溶剂油依次加入四口瓶中,用氮气置换30min,在水浴上加热,搅拌使之完全溶解。然后将已除氧的单体水溶液逐渐滴加到油相中,同时高速搅拌(400r/min)令其乳化形成乳状液。乳化操作结束后,降低搅拌速率(200r/min),加入偶氮二异丁腈(AIBN)的甲苯溶液,于45℃下保持4h,然后加入(NH4)2S2O8-Na2S2O5氧化还原引发剂,在相同的温度下继续反应2h。反应结束后降至室温并加入终止剂,停止搅拌,出料,即可得到均匀、稳定的W/O型丙烯酰胺/丙烯酸钠共聚物胶乳产品。为了优选丙烯酰胺/丙烯酸钠共聚物的制备工艺,王雨华等[13]综合研究了原料的纯度、乳化剂种类和用量、引发剂种类以及反应温度等因素对产品质量的影响。
(1)原料纯度的影响
原料的纯度,尤其是单体的质量,直接影响反相乳液聚合能否顺利进行以及产物分子量的大小。在本项研究中AM单体纯度对产品性能的影响比较明显,见表3-1。
表3-1 AM单体纯度对产品性能的影响[13]

注:AM 40%~60%,100mL;AA,8~10mL;溶剂油(200#),50~60mL;乳化剂(HLB值为8~9),3~4g;AIBN,0.05%~0.1%;(NH4)2S2O8,0.002%~0.008%;Na2S2O5,0.001%~0.004%。均为纯单体质量的百分数。
(2)乳化剂种类及用量的影响
乳化剂的种类决定乳液类型,使用亲油性乳化剂才能获得W/O型乳液。乳化剂用量在一定程度上影响胶乳粒子的大小和胶乳的稳定性以及产物分子量的大小。
三项研究是采用反相乳液聚合制备W/O型聚合物胶乳。因此,应选用亲油性的非离子型表面活性剂作为乳化剂。在这种乳液体系中,连续相为油相,分散相为水相,非离子型乳化剂一般只提供一合适的油水亲和力。分散的液滴不是靠它吸附乳化剂产生的离子电荷来稳定的,而是靠乳化剂存在所改变的内聚力作用及乳化剂分子的位障作用来达到分散稳定目的的。
过去曾有人提出W/O型乳液选用HLB值在4~6之间的乳化剂较为稳定。近年来又有人根据内聚能理论提出,选用乳化剂HLB值在7~10之间的胶乳更为稳定。本项研究的试验也证明,在较高的HLB值(8~9)下,按上述基本工艺配方和实验方法进行反相乳液聚合,可获得较好的结果。同时发现,采用复合型乳化剂比单一乳化剂效果好。本试验还研究了HLB值为8~9的复合乳化剂的加入量对乳液及产品性能的影响,见表3-2。
表3-2 乳化剂用量对乳液及产品性能的影响[13]

注:AM 40%~60%,100mL;AA(新蒸的),8~10mL;溶剂油(200#),50~60mL;AIBN,0.05%~0.1%;(NH4)2S2O8,0.002%~0.008%;Na2S2O5,0.001%~0.004%。均为纯单体质量的百分数。
从表3-2中可以看出,乳化剂用量小于2%时,乳液稳定性差,难以正常地进行反相乳液聚合;同时还可以看出,乳化剂用量超过8%时,虽然乳液的稳定性好,但产物分子量已下降到不属于高分子量范畴。因此,为了制备出高分子量的稳定的聚合物胶乳产品,在其他条件不变的情况下,乳化剂的加入量占单体加入量的4%~6%较为适宜。
(3)引发剂种类及添加工艺的影响
本项研究的突出特点就在于采用了油溶性和水溶性两种引发体系,进行分段引发制备出了高分子量、高含固量、高转化率、高稳定性的聚合物胶乳。即首先使用油溶性引发剂AIBN使80%以上的单体聚合,然后再使用水溶性引发剂(NH4)2S2O8-Na2S2O5(氧化-还原引发体系)使剩余的单体聚合,最终可制得单体残存量小于0.3%的聚合物胶乳。
若不添加水溶性引发剂,只用油溶性引发剂,要达到高转化率的目的,需要相当苛刻的条件,即需要高温或长时间熟化。此时,就会不可避免地造成聚合物降解或交联等副反应,严重影响产品性能。而若颠倒油溶性引发剂和水溶性引发剂的顺序,即改为先添加水溶性引发剂,后添加油溶性引发剂,则首先是水溶性引发剂造成乳液不稳定,其次是后加入的油溶性引发剂无法达到减少单体残存量的效果,所以也达不到预期的目的。
另外,若在聚合初期就紧接着加入水溶性引发剂,则乳液粒子就会迅速增大,在聚合体系中生成沉淀,形成块状物。即使不生成沉淀,数日后胶乳也会出现分层、水相部分固化等现象,使胶乳稳定性受到影响。而若同时加入油溶性引发剂和水溶性引发剂来引发反相乳液聚合,结果也会像上述在聚合初期加入水溶性引发剂一样,聚合体系出现沉淀、固化等现象。
(4)聚合温度的影响
聚合反应起始温度的拟定,首先要考虑到所选用油溶性引发剂适宜的分解温度。由于选用了AIBN引发剂,所以反应的起始温度一般不应低于40℃。其次应考虑到,虽然提高反应温度后能加快反应速率,缩短反应时间,或在相同反应时间内能适当提高转化率,但同时也会促使支化、交联现象发生,使得反应不易控制。试验证明,本工艺拟定反应温度为45℃是合理的,而且此温度对后期的水溶性引发剂也比较适宜。
(5)体系中氧的影响
氧对较低温度下的自由基聚合有明显的阻聚倾向,而且聚合温度越低,溶解氧含量越高,阻聚越强烈。这是因为在较低的温度下氧很容易与引发剂分解的自由基结合而导致阻聚。试验证明,体系中溶解氧含量大于10μg/g时,即会呈现阻聚(有明显的诱导期),因此反应前如不充分排氧,则会导致分子量下降,甚至造成不聚或低聚。氧对产物分子量的影响见表3-3。通N2时间一般大于25min,即可使体系中的氧含量小于10μg/g。
表3-3 氧对聚合物分子量的影响[13]

注:配方同表3-1下注。
王雨华等[13]还利用所研制的样品与国内外产品从溶解性、固含量及分子量等性能指标方面进行了对比。测定结果表明,所研制的样品性能指标优于国内对照样品,与国外对照样品相当,见表3-4。
表3-4 胶乳样品性能指标[13]

注:对照样品1为国内天津大学1991年研制的产品,对照样品2为欧IFCIDBONE产品。
3.3.5.3 反相悬浮聚合
采用水溶液聚合法、反相乳液聚合法和反相悬浮聚合法均可制备丙烯酰胺/丙烯酸钠共聚物,国内市场上的丙烯酰胺/丙烯酸钠共聚物主要是水溶液聚合产物,存在着溶解慢、溶解不完全等缺点。反相乳液聚合法有利于反应热的散发,可制备分子量高、溶解性好的产品,但工艺较复杂,生产成本较高,难制得稳定的乳液,而且乳状产品运输不方便[14]。反相悬浮聚合法是近二十多年来发展起来的方法[15,16],能克服上述两法的不足,且生产工艺简单、成本低,便于实现工业化,产品分子量可达千万以上,溶解性能比水溶液聚合产品好,可直接得到粉状或粒状产品,包装和运输方便。
张忠兴等[14]以丙烯酰胺和丙烯酸钠为单体,采用反相悬浮自由基共聚的方法进行了合成阴离子型聚丙烯酰胺的中试研究,并得到了分子量达1.45×107的超高分子量的丙烯酰胺/丙烯酸钠共聚物。具体工艺为:
①配料与投料。将130kg环己烷通过高位槽送至反应釜,加入1.7kg乳化剂失水山梨糖单硬脂酸酯(S-60)后搅拌,将釜温升至40℃,乳化剂溶解后将釜温降至30℃;称3.8kg NaOH置于化碱槽中,用6kg水溶解并冷至室温;称20kg丙烯酰胺、1.2kg醋酸钠置于配料槽中,加入10kg水搅拌使其溶解,再加入10kg丙烯酸和定量的脲、K2S2O8、甲基丙烯酸和N,N-二甲氨基乙酯(DM)等溶液搅拌均匀,送至高位槽。在搅拌情况下将配好的单体溶液加入反应釜中,搅拌10min使体系成为均匀稳定的悬浮液,然后依次滴入NaHSO3、NaOH溶液,滴碱时速度要缓慢并维持釜温不超30℃。
②聚合与脱水。氢氧化钠溶液滴完后,将釜温升至40℃并维持1h,再在1h内将釜温升至50℃,然后在2h内将釜温升至71℃使体系共沸脱水,当出水量达加入水量的75%时便可停止加热。
③出料。停止加热后继续搅拌,夹套通冷水,当釜温降至40℃后将丙烯酰胺/丙烯酸钠共聚物产品放到容器中,待聚合物颗粒完全沉降后,将上层溶剂转移到回收罐,产品风干。
此外,他们还比较了中试与实验室小试两种情况下聚合条件的不同,确定了原料丙烯酰胺中金属杂质铜和铁的含量,研究了原料丙烯酰胺在有机络合物乙二胺四乙酸二钠(EDTA)存在下与丙烯酸钠的共聚,并研究了中试条件下一些因素如引发剂浓度、脱水时间对产品分子量和溶解性能的影响。结果发现:在聚合反应体系中加入占丙烯酰胺单体质量0.025%的EDTA能显著提高聚丙烯酰胺的分子量;在反相悬浮法制备丙烯酰胺/丙烯酸钠共聚物的过程中,引发体系中K2S2O8-NaHSO3引发剂的最佳用量是K2S2O8、NaHSO3分别占单体质量的0.05%;而且,随着脱水时间的延长,聚丙烯酰胺的分子量和溶解性能均呈下降趋势。
刘莲英等[17]采用反相悬浮聚合、加碱水解、共沸脱水的方法合成了分子量达107数量级的粉状、速溶阴离子型聚丙烯酰胺,即丙烯酰胺/丙烯酸钠共聚物。具体工艺为:将环己烷、乳化剂加入装有回流冷凝管的三口反应瓶中搅拌,水浴控温加热待其完全溶解。称计量的丙烯酰胺,用去离子水配成质量分数为50%的水溶液,加入反应瓶中。待水相、油相分散均匀后滴入引发剂反应1.5~2h。反应结束后,加碱控温在一定时间内水解。适当增加一定量有机溶剂,共沸脱水得粉状产品。他们在工艺的优选试验中确定了最佳引发体系为K2S2O8-甲基丙烯酸二甲氨基乙酯-NaHSO3,适宜的反应温度为35℃;研究了水解度与水解时间、水解温度、水解剂加量之间的关系,确定最佳水解时间为40min,水解温度为50℃,碱与丙烯酰胺的摩尔比为0.2:1。
樊世科等[18]采用反向悬浮聚合法制备了丙烯酸(钠)与丙烯酰胺共聚物,通过分散剂的选择,确定了以羧甲基纤维素、司盘80、羊毛脂为分散剂的较稳定的聚合体系,其产物呈颗粒状;探讨了聚合反应条件的影响,并测试了共聚物的部分性能。具体工艺为:在装有搅拌器、回流冷凝器、氮气导入管的三口烧瓶中,加入环己烷、羧甲基纤维素(CMC)、司盘80、羊毛脂等,充分搅拌,通氮气。将一定量的丙烯酸(用活性炭处理已除去阻聚剂)进行中和后,加入三口瓶中,然后再加入丙烯酰胺(重结晶)及N,N'-亚甲基双丙烯酰胺。充分搅拌一定时间后,升温至60℃,加入引发剂,在60℃下恒温反应4h结束。待降至室温后过滤分离,用甲醇洗涤数次,干燥后得小颗粒状聚合物丙烯酸(钠)/丙烯酰胺共聚物。他们在工艺的优选试验中确定了最佳引发体系采用CMC、司盘80、羊毛脂为分散剂,且其质量比为2:1:1,制得颗粒状的丙烯酸(钠)/丙烯酰胺共聚物,并具有一定的吸水性;通过对各反应条件的讨论,其丙烯酸的中和度为75%,交联剂的用量为单体量的0.25%,且在反应约1h后加入交联剂,可制得性能良好的共聚物。
3.3.6 丙烯酰胺/甲基丙烯酸甲酯/丙烯酸三元共聚物
笔者和课题组成员以丙烯酰胺、甲基丙烯酸甲酯和丙烯酸为原料,采用反相乳液聚合法制备丙烯酰胺/甲基丙烯酸甲酯/丙烯酸共聚物乳液,所制备的产品的分子量达到8.3×106。反应式为:

制备工艺为:将配制好的复合乳化剂(HLB值为7.8)和环己烷依次加入1L的反应釜中,用氮气置换40min,升温至35℃,搅拌使之完全溶解。然后将已经除氧并含有乙二胺四乙酸二钠的单体水溶液逐渐滴加到环己烷中,同时快速搅拌(400~500r/min)令其乳化形成乳状液,乳化操作结束后,降低搅拌速率(150r/min),加入K2S2O8-脲氧化还原引发剂,于50℃下保持5h,然后再加入适量的K2S2O8-脲氧化还原引发剂,在相同的温度下继续反应3h。反应结束后降至室温并加入终止剂,停止搅拌,出料,即可得到均匀、稳定的W/O型丙烯酰胺/甲基丙烯酸甲酯/丙烯酸三元共聚物乳液。
影响丙烯酰胺/甲基丙烯酸甲酯/丙烯酸三元共聚物乳液性能的因素很多,主要有单体摩尔比、引发剂种类及用量、乳化剂种类及用量、反应时间、搅拌速率以及油水体积比等。本书主要讨论单体摩尔比、引发剂种类和用量以及复合乳化剂用量对产品质量的影响。
(1)单体摩尔比
丙烯酰胺(AM)、甲基丙烯酸甲酯(MMA)和丙烯酸(AA)单体摩尔比对三元共聚物的分子量影响很大,结果见表3-5。在三种单体中,甲基丙烯酸甲酯(MMA)的摩尔比越大,三元共聚物的分子量越小,因此三种单体的摩尔比宜控制在1:0.02:1左右。
表3-5 单体摩尔比对共聚物分子量的影响

(2)引发剂种类和用量
在反相乳液聚合反应中,引发剂的种类是影响共聚乳液分子量大小的关键因素之一。不同引发剂对共聚物产品分子量的影响见表3-6。从表中可以看出,过硫酸钾-脲引发体系的引发效果最好,所制备的丙烯酰胺/甲基丙烯酸甲酯/丙烯酸三元共聚物乳液性能稳定,分子量为9.0×106,而且单体转化率可达99.7%。
表3-6 引发剂种类的影响

增加引发剂的用量不仅可以提高单体的转化率,而且也使聚合反应以较快的速度进行。但这种用量的增加是有限度的。这是因为链自由基的生成及链增长反应是放热反应,引发剂的高用量必然导致反应体系高放热。如果体系蓄积的热量不能及时导出,体系的温度势必会进一步升高,聚合反应急剧进行而引起冲料和凝胶。当引发剂的用量大于0.6%时,所得的乳胶在两个月内会凝结成块,而且引发剂用量加大,引发剂自由基增多,不但未见成核粒子数增多以及乳胶粒子粒径减小,而且乳胶粒子粒径稍稍增大,体系的表观黏度降低。产生这一现象的原因是体系中的一部分引发剂实际起了电解质的作用,它使粒子易于凝聚,而使粒径增大。本实验中,氧化还原引发剂过硫酸钾-脲的最佳用量是过硫酸钾和脲分别为单体质量的0.08%和0.6%。
(3)乳化剂用量
复合乳化剂的HLB值控制在7.8左右,乳化剂用量对三元共聚物乳液性能的影响见表3-7。由表3-7可以看出,随着乳化剂用量的增加,乳液的黏度、固含量、转化率均有提高。当乳化剂的用量低于6%时,乳液的稀释稳定性变差。由此可以看出,乳化剂在乳液聚合的过程中具有非常重要的作用。乳化剂浓度增大时,聚合反应速率增大。这是由于乳化剂用量直接影响聚合过程及聚合度,随着乳化剂用量的增加,单体珠滴数目和引发点增多,而使每个珠滴中自由基终止机会减少。当乳化剂浓度低时,仅部分乳胶粒表面被乳化剂分子覆盖。在这样的条件下乳胶粒容易聚结,由小乳胶粒生成大乳胶粒,严重时发生凝聚,造成挂胶和抱轴,轻则降低收率,降低产品质量,重则发生生产事故。所以乳化剂用量以6%~9%为宜。
表3-7 乳化剂用量对乳液性能的影响
