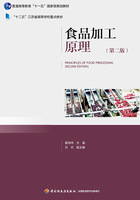
第三节 食品浓缩
浓缩是从溶液中除去部分溶剂(通常是水)的操作过程,也是溶质和溶剂均匀混合液的部分分离过程。按浓缩的原理,可分为平衡浓缩和非平衡浓缩两种方法。平衡浓缩是利用两相在分配上的某种差异而获得溶质浓缩液和溶剂的浓缩(分离)方法,如蒸发浓缩和冷冻浓缩。蒸发浓缩是利用溶液中的水受热汽化而达到浓缩(分离)的目的。冷冻浓缩是利用部分水分因放热而结冰,稀溶液与固态冰在凝固点以下的平衡关系,采用机械方法将浓缩液与冰晶分离的过程。非平衡浓缩是利用半透膜的选择透过性来达到分离溶质与溶剂(水)的过程。半透膜不仅可用于分离溶质和溶剂,也可用于分离各种不同分子大小的溶质,在膜分离技术领域中有广阔的应用。
一、浓缩的目的
浓缩在食品工业中的应用主要有以下目的。
除去食品中的大量水分,减少包装、贮藏和运输费用。浓缩的食品物料,有的直接是原液,如牛奶;有的是榨出汁或浸出液,如水果汁、蔬菜汁、甘蔗汁、咖啡浸提液、茶浸提液等。这些物料水分含量高,譬如100t固形物质量分数5%的番茄榨出汁浓缩至28%的番茄酱,质量将减至18t,不足原质量的1/5,体积缩小大致与此相同,这样就可大大降低包装、贮藏和运输费用。
提高制品浓度,增加制品的贮藏性。用浓缩方法提高制品的糖分或盐分可降低制品的水分活度,使制品达到微生物学上安全的程度,延长制品的有效贮藏期,如将含盐的肉类萃取液浓缩到不致产生细菌性的腐败。
浓缩经常用作干燥或更完全脱水的预处理过程。这种处理特别适用于原液含水量高的情况,用浓缩法排除这部分水分比用干燥法在能量上和时间上更节约,如制造奶粉时,牛奶先经预浓缩至固形物含量达45%~52%以后再进行干燥。蒸发浓缩用作某些结晶操作的预处理过程。
二、蒸发浓缩
蒸发是浓缩溶液的单元操作,是食品工业中应用最广泛的浓缩方法。食品工业浓缩的物料大多数为水溶液,在以后的讨论中,如不另加说明,蒸发就指水溶液的蒸发。蒸发浓缩就是将溶液加热至沸腾,使其中的一部分溶剂汽化并被排除,以提高溶液中溶质浓度的操作。由于固体溶质通常是不挥发的,所以蒸发也是不挥发性溶质和挥发性溶剂的分离过程。如图2-19所示为真空蒸发的基本流程。
(一)常压蒸发和真空蒸发
蒸发操作可以在常压、加压和减压条件下进行。常压蒸发是指冷凝器和蒸发器溶液侧的操作压力为大气压或稍高于大气压力,此时系统中的不凝性气体依靠本身的压力从冷凝器中排出。

图2-19 真空蒸发基本流程
1—加热室 2—分离室 3—混合冷凝器 4—分离器 5—缓冲罐 6—真空泵
减压下的蒸发常称为真空蒸发,食品工业广泛应用真空蒸发进行浓缩操作。因真空蒸发时冷凝器和蒸发器料液侧的操作压力低于大气压,必须依靠真空泵不断从系统中抽走不凝气来维持负压的工作环境。采用真空蒸发的基本目的是降低料液的沸点。与常压蒸发比较,它有以下优点:溶液沸点降低,可增大蒸发器的传热温差,所需的换热面积减小;溶液沸点低,可以应用温度较低的低压蒸汽和废热蒸汽作热源,有利于降低生产费用和投资;蒸发温度低,对浓缩热敏性食品物料有利;蒸发器操作温度低,系统的热损失小。当然,真空蒸发也有缺点:因蒸发温度低,料液黏度大,传热系数较小;因系统内负压,完成液排出需用泵,冷凝水也需用泵或高位产生压力排出,真空泵和输液泵都使能耗增加。
真空蒸发的操作压力取决于冷凝器中水的冷凝温度和真空泵的性能。冷凝器操作压力的极限是冷凝水的饱和蒸汽压,所以它取决于冷凝器的温度。真空泵的作用是抽走系统中的不凝性气体,真空泵的能力越大,就使得冷凝器内的操作压力越易维持于接近冷凝水的饱和蒸汽压。一般真空蒸发时,冷凝器的压力为10~20kPa。
(二)闪蒸
闪急蒸发(flash evaporation)简称闪蒸,是一种特殊的减压蒸发。将热溶液的压力降到低于溶液温度下的饱和压力,则部分水将在压力降低的瞬间沸腾汽化,就是闪蒸。水在闪蒸汽化时带走的热量,等于溶液从原压下温度降到降压后饱和温度所放出的显热。
在闪蒸过程中,溶液被浓缩。闪蒸的具体实施方法有两种:一种是直接把溶液分散喷入低压大空间,使闪蒸瞬间完成;另一种是从一个与降压压差相当的液柱底部引入较高压热溶液,使降压汽化在溶液上升中逐步实现。这种措施都为了减少闪蒸后汽流的雾沫夹带。
闪蒸的最大优点是避免在换热面上生成垢层。闪蒸前料液加热但并没浓缩,因而生垢问题不突出。而在闪蒸中不需加热,是溶液自身放出显热提供蒸发能量,因而不会产生壁面生垢问题。
(三)单效蒸发和多效蒸发
蒸发操作的效(effect)是指蒸汽被利用的次数。如果蒸发生成的二次蒸汽不再被用作加热介质,而是直接送到冷凝器中冷凝,称为单效蒸发。
如果第一个蒸发器产生的二次蒸汽引入第二个蒸发器作为加热蒸汽,两个蒸发器串联工作,第二个蒸发器产生的二次蒸汽送到冷凝器排出,则称为双效蒸发,双效蒸发是多效蒸发中最简单的一种。
多效蒸发是将多个蒸发器串联起来的系统,后效的操作压力和沸点均较前效低,仅在压力最高的首效使用新鲜蒸汽作加热蒸汽,产生的二次蒸汽作为后效的加热蒸汽,亦即后效的加热室成为前效二次蒸汽的冷凝器,只有末效二次蒸汽才用冷却介质冷凝。可见多效蒸发明显减少加热蒸汽耗量,也明显减少冷却水耗量。
(四)热泵蒸发
为提高热能利用率,除采用多效蒸发外,还可通过一种通称热泵的装置,提高二次蒸汽的压力和温度,重新用作蒸发的加热蒸汽,称为热泵蒸发,或称为蒸汽再压缩蒸发。
热泵是以消耗一部分高质能(机械能、电能)或高温位热能为代价,通过热力循环,将热由低温物体转移到高温物体的能量利用装置。常用的热泵有蒸汽喷射热泵和机械压缩式热泵。
蒸汽喷射热泵使用的蒸汽喷射器类似于蒸汽喷射真空泵,只是在喷嘴附近低压吸入的是蒸发产生的二次蒸汽,与高温高压的驱动蒸汽混合后,在扩压管处达到蒸发所需加热蒸汽的压力和温度用作蒸发的加热介质。机械压缩式热泵利用电动机或汽轮机等驱动往复式或离心式等压缩机,将二次蒸汽压缩,提高其压力和温度,以重新用作蒸发的加热蒸汽。
(五)间歇蒸发和连续蒸发
蒸发操作可分为间歇操作和连续操作两种。
间歇蒸发有两种操作方法:
1.一次进料,一次出料
在操作开始时,将料液加入蒸发器,当液面达到一定高度,停止加料,开始加热蒸发。随着溶液中的水分蒸发,溶液的浓度逐渐增大,相应地溶液的沸点不断升高。当溶液浓度达到规定的要求时,停止蒸发,将完成液放出,然后开始另一次操作。
2.连续进料,一次出料
当蒸发器液面加到一定高度时,开始加热蒸发,随着溶液中水分蒸发,不断加入料液,使蒸发器中液面保持不变,但溶液浓度随着溶液中水分的蒸发而不断增大。当溶液浓度达到规定值时,将完成液放出。
由上可知,间歇操作时,蒸发器内溶液浓度和沸点随时间而变,因此传热的温度差、传热系数也随时间而变,故间歇蒸发为非稳态操作。
连续蒸发时,料液连续加入蒸发器,完成液连续地从蒸发器放出,蒸发器内始终保持一定的液面和压强,器内各处的浓度与温度不随时间而变,所以连续蒸发为稳态操作。通常大规模生产中多采用连续操作。
三、蒸发设备
蒸发单元操作的主要设备是蒸发器,还需要冷凝器、真空泵、疏水器和捕沫器等辅助设备。蒸发器是浓缩设备的工作部件,主要是由加热室(器)和分离室(器)两部分组成。加热室的作用是利用水蒸气加热物料,使其中的水分汽化。
加热室的形式随着技术的发展而不断改进。最初采用的是夹层式和蛇(盘)管式,其后有各种管式、板式等换热器形式。为了强化传热,采用强制循环替代自然循环,也有采用带叶片的刮板薄膜蒸发器和离心薄膜蒸发器等。
蒸发器分离室的作用是将二次蒸汽中夹带的料液分离出来。为了使雾沫中的液体回落到料液中,分离室须具有足够大的直径和高度以降低蒸汽流速,并有充分的机会使其返回液体中。早期的分离室位于加热室之上,并与加热器合为一体。由于出现了外加热型加热室(加热器),分离室也能独立成为分离器。
(一)循环型蒸发器
循环型蒸发器的特点是溶液在蒸发器中循环流动,以提高传热效率。根据引起溶液循环运动的原因不同可分为自然循环和强制循环。自然循环是由于液体受热程度不同产生密度差引起的,强制循环是由外加机械力迫使液体沿一定方向流动。
1.中央循环管式蒸发器
该蒸发器主要由下部加热室和上部蒸发室两部分构成,如图2-20所示。食品料液经过加热管面进行加热,由于传热产生密度差,形成了对流循环,液面上的水蒸气向上部负压空间迅速蒸发,从而达到浓缩的目的。有时,也可以通过搅拌来促进流体流动。二次蒸汽夹带的部分料液在分离室分离,而剩余少量料液被蒸发室顶部捕集器截获。

图2-20 中央循环管式蒸发器
1—加热室 2—分离室(蒸发器)
中央循环管式蒸发器结构简单,操作方便,但清洗困难,料液在蒸发器中停留时间长,黏度高时循环效果差。这种蒸发器在食品工业中应用已不再普遍。但是,在制糖工业中还用到它,主要是用在从原料中结晶精制糖。
2.外循环管式蒸发器
外循环管式蒸发器的加热室在蒸发器的外面,因此便于检修和清洗,并可调节循环速度,改善分离器中的雾沫现象。循环管内的物料是不直接受热的,故可适用于果汁、牛奶等热敏性物料的浓缩。如图2-21、图2-22所示为自然循环与强制循环的外循环管式蒸发器的示意图。

图2-21 自然循环外加热式蒸发器
1—蒸气入口 2—料液入口 3—抽出口 4—二次蒸汽出口 5—冷凝水出口 6—不凝汽出口 7—浓缩液出口 8—分离器9—加热器 10—循环管

图2-22 强制循环外加热式蒸发器
1—加热器 2—循环管 3—二次蒸汽出口4—分离器 5—浓缩液出口 6—循环泵7—加料口
(二)膜式蒸发器
根据料液成膜作用力及加热特点,膜式蒸发器有:升(降)膜式蒸发器、刮板式和离心式薄膜蒸发器、板式薄膜蒸发器。
升(降)膜式蒸发器是典型的膜式蒸发器,是一种外加热式蒸发器。溶液通过加热室一次达到所需的浓度,且溶液沿加热管壁呈膜状流动进行传热和蒸发,故其传热效率高,蒸发速度快,溶液在蒸发器内停留时间短,特别适用于热敏性溶液的蒸发。
1.升膜式蒸发器
升膜式蒸发器如图2-23所示。加热室由列管式换热器构成,常用管长6~12m,管长径之比为100~150。料液的加热与蒸发分三部分。在底部,管内完全充满料液,由于液柱的静压作用,一般不发生沸腾,只起加热作用,随着温度升高,在中部开始沸腾产生蒸汽,使料液产生上升力。到了上部,蒸汽体积急剧增大,产生高速上升蒸汽使溶液在管壁上抹成一层薄膜,使传热效果大大改善。在管顶部呈喷雾状,快速进入分离室分离,浓缩液由分离室底部排出。

图2-23 升膜式蒸发器
升膜式蒸发器由于蒸发时间短(仅几秒到十余秒),具有良好的破乳作用,所以适用于蒸发量大、热敏性及易生成泡沫的溶液浓缩,一次通过浓缩比可达4倍,它已成功地应用于乳品和果汁工业中,但不适于高黏度、易结晶或结垢物料的浓缩。
2.降膜式蒸发器
降膜式蒸发器如图2-24所示。与升膜式蒸发器不同的是,料液由加热室的顶部进入,在重力作用下沿管壁内呈膜状下降,浓缩液从下部进入分离器。为了防止液膜分布不均匀,出现局部过热和焦壁现象,在加热列管的上部设置有各种不同结构的料液分配器装置,并保持一定的液柱高度。
降膜式蒸发器因不存在静液层效应,物料沸点均匀,传热系数高,停留时间短,但液膜的形成仅依靠重力及液体对管壁的亲润力,故蒸发量较小,一次蒸汽浓缩比一般小于7。
3.升—降膜蒸发器
升—降膜蒸发器是将加热器分成两程:一程做稀溶液的升膜蒸发;另一程为浓稠液的降膜蒸发,如图2-25所示。这种蒸发器集中了升、降膜蒸发器的优点。

图2-24 降膜式蒸发器

图2-25 升—降膜式蒸发器
4.刮板式薄膜蒸发器
如图2-26所示,刮板式薄膜蒸发器有立式和卧式两种。加热室壳体外部装有加热蒸汽夹套,内部装有可旋转的搅拌叶片,原料液受刮板离心力、重力以及叶片的刮带作用,以极薄液膜与加热表面接触,迅速完成蒸发。

图2-26 刮板式薄膜蒸发器
1—电动机 2—转轴 3—分离器 4—分配盘 5—刮板 6—夹套加热室
刮板式蒸发器有多种不同结构。按刮板的装置方式有固定式刮板和离心式刮板之分;按蒸发器的放置形式有立式、卧式和卧式倾斜放置之分;按刮板和传热面的形状有圆柱形和圆锥形两种。
刮板式薄膜蒸发器可用于易结晶、易结垢、高黏度或热敏性的料液浓缩。但该结构较复杂,动力消耗大,处理量较小,浓缩比一般小于3。
板式蒸发器是由板式换热器与分离器组合而成的一种蒸发器,见图2-27。通常由两个加热板和两个蒸发板构成一个浓缩单元,加热室与蒸发室交替排列。实际上料液在热交换器中的流动如升降膜形式,也是一种膜式蒸发器(传热面不是管壁而是平板)。数台板式热交换器也可串联使用,以节约能耗与水耗。通过改变加热系数,可任意调整蒸发量。由于板间液流速度高,传热快,停留时间短,也很适于果蔬汁物料的浓缩。板式蒸发器的另一显著特点是占地少,易于安装和清洗,也是一种新型蒸发器。其主要缺点是制造复杂,造价较高,周边密封橡胶圈易老化。
(三)多效蒸发
单效真空蒸发广泛应用于食品浓缩。单效真空蒸发的最大优点是容易操作控制,可依据物料黏性、热敏性,控制蒸发温度(通过控制加热蒸汽及真空度)及蒸发速率。但由于物料在单效蒸发器内停留时间长,会带来热敏性成分的破坏问题,且物料在不断浓缩过程中,其沸点温度随着浓度的提高而增大,黏度也随浓度及温度的变化而改变,因此浓缩过程要合理选择控制蒸发温度。由于液层静压效应引起的液面下局部沸腾温度高于液面上的沸腾温度,也是单效真空蒸发中容易出现的问题。料液黏度增大,物料在蒸发过程中湍动小,更易增大这种差异,甚至加热面附近料液温度接近加热面温度引起结垢、焦化,影响热的传递。

图2-27 板式蒸发器
单效蒸发存在热耗多、传热面积不大等缺点,限制其蒸发能力的提高。对于生产量大的现代食品工厂,单效蒸发已逐步被多效真空浓缩所代替。
1.多效真空蒸发浓缩的原理
从理论上,1kg水蒸气可蒸发1kg水,产生1kg二次蒸汽。若将二次蒸汽全部用作第二效的加热蒸汽,同样应该可蒸发产生1kg的蒸汽。但实际上,由于汽化潜热随温度降低而增大,且效间存在热量损失,蒸发1kg水所消耗的加热蒸汽量常高于理论上的消耗量。从总的蒸发效果看,由于汽化潜热随温度升高而减小,随着效数的增加,蒸发所需的蒸汽消耗量愈小,见表2-4。
表2-4 蒸发效数与蒸汽耗量的关系 单位:kg(汽)/kg(水)

多效真空蒸发器内的绝对压力依次下降,每一效蒸发器中的料液沸点都比上一效低,因此任何一效蒸发器中的加热室和蒸发室之间都有热传递所必须的温度差和压力差,这是多效蒸发的原理所在。
2.多效真空浓缩流程
由几个蒸发器相连接,以蒸汽加热的蒸发器为第一效,利用第一效产生的二次蒸汽加热的蒸发器为第二效,依此类推。按照多效蒸发加料方式与蒸汽流动方向,有顺流式、逆流式和平流式蒸发器。如图2-28所示为三效真空浓缩装置流程图。
(1)顺流加料法 如图2-28(1)所示,料液和蒸汽的流向相同,均由第一效顺序至末效,故也称并流加料法,这是工业上常用的一种多效流程。这种流程的优点:第一,由于后一效蒸发室的压力比前一效低,料液在效间的输送不用泵而可利用各效间的压力差;第二,后一效料液的沸点较前一效低,当料液进入下一效时发生闪蒸现象,产生较多的二次蒸汽;第三,浓缩液的温度依效序降低,对热敏性物料的浓缩有利。缺点是:料液浓度依效序增高,而加热蒸汽温度依效序降低,所以当溶液黏度升高较大时,传热系数下降,增加了末效蒸发的困难。
(2)逆流加料法 如图2-28(2)所示,原料液由末效进入,用泵依次输送至前一效,浓缩液由第一效下部排出。加热蒸汽的流向则由第一效顺序至末效。因蒸汽和料液的流动方向相反,故称逆流加料法。逆流加料法的优点是:随着料液向前一效流动,浓度愈来愈高,而蒸发温度也愈来愈高,故各效料液黏度变化较小,有利于改善循环条件,提高传热系数。缺点是:第一,高温加热面上的浓料液的局部过热易引起结垢和营养物质的破坏;第二,效间料液的输送需用泵,使能量消耗增大;第三,与顺流相比,水分蒸发量稍低,热量消耗稍大;第四,料液在高温操作的蒸发器内停留时间比顺流长,对热敏性食品不利。通常逆流法适于黏度随温度和浓度变化大的料液蒸发。
(3)平流加料法 如图2-28(3)所示,每效都平行送入原料液和排出浓缩液。加热蒸汽则由第一效依次至末效。平流法适用于在蒸发进行的同时有晶体析出的料液的浓缩,如食盐溶液的浓缩结晶。这种方法对结晶操作较易控制,并省掉了黏稠晶体悬浮液体的效间泵送。
(4)混流加料法 有些多效蒸发过程同时采用顺流和逆流加料法,即某些效用顺流,某些效用逆流,充分利用各流程的优点。这种称为混流加料法,尤其适用于料液黏度随浓度而显著增加的料液蒸发。
(5)额外蒸汽运用 根据生产情况,在多效蒸发流程中,有时将某一效的二次蒸汽引出一部分用于预热物料或用作其他加热目的,其余部分仍进入下一效作为加热蒸汽。被引出的二次蒸汽,称为额外蒸汽。从蒸发器中引出额外蒸汽作为它用,是一项提高热能经济利用的措施。一般情况下,额外蒸汽多自第1、2效引出。
(四)多效蒸发的效数
多效蒸发的最大优点是热能的充分利用。但实际应用中,多效蒸发的效数是受到限制的,原因如下所述。
1.实际耗气量大于理论值
由于汽化潜热随温度降低而增大,并且效间存在热损失,因此总热损随着效数增加而增加。

图2-28 三效真空浓缩装置流程图
2.设备费用增加
多效蒸发虽可节约蒸汽,但蒸发设备及其附属设备的费用却随着效数的增加而成倍的增加,当增加至不能弥补所节约的燃料费时,效数就到了极限。以牛奶浓缩为例,日处理鲜奶量10~20t,可选2~3效;日处理量为20~50t,选3~4效;日处理量为50~100t,选4~5效;日处理量为100~200t,选5~6效。
3.物料性质的限制
由于食品物料的性质,蒸发的最高温度和最终温度都有一定限制,使蒸发的总温差有限。据经验,当各效的传热有效温差小于5℃时,将大大降低传热效率,使传热面积增大。例如考虑牛奶蒸发过程的黏度变化,其最高浓缩温度为68℃,浓缩终温通常是42℃,则总传热温差是26℃,分配到各效,温差和效数就有限了。
四、冷冻浓缩
(一)冷冻浓缩的基本原理
1.冷冻浓缩的固液相平衡
冷冻浓缩是利用冰和水溶液之间的固相液相平衡原理进行浓缩的一种方法。冷冻浓缩将稀溶液中作为溶剂的水冻结并分离出冰晶,从而使溶液浓缩。冷冻浓缩涉及液固系统的相平衡,但它与常规的冷却结晶操作有所不同。
以盐水溶液为例,对于简单的二元系统(仅有一种溶剂和一种溶质),溶液在不同温度与浓度有对应的相平衡关系。若盐水浓度较低,随着溶液温度下降,盐水溶液浓度保持不变。当温度降到一个值时(即为冰点),溶液中如有种冰或晶核存在时,盐水中一部分水开始结冰析出,剩下的盐水浓度升高。当温度进一步下降,水就不断结冰析出,盐水浓度也越来越高。当温度降到一定值时,盐水在此温度下全部结冰,此时盐水浓度为低共熔浓度,对应的温度为低共熔温度。在此过程中盐水是不断浓缩的,此即是冷冻浓缩的原理所在。而若盐水的浓度高于低共熔浓度,溶液呈过饱和状态,此时降温的结果表现为溶质晶体析出,盐水浓度下降,这是冷却结晶的原理。
2.冷冻浓缩过程中的溶质夹带和溶质脱除
由于冷冻浓缩过程中的水分冻结和溶质浓缩是一个方向相反的传质过程,即水分从溶液主体迁移到冰晶表面析出,而溶质则从冰晶表面附近向溶液主体扩散。实际上,在冷冻浓缩过程中析出的冰结晶不可能达到纯水的状态,总是有或多或少的溶质混杂其中,这种现象称为溶质夹带。
溶质夹带有内部夹带和表面附着两种。内部夹带与冷冻浓缩过程中溶质在主体溶液中的迁移速率和迁移时间有关,在缓慢冻结时,冰晶周围增浓溶液中的溶质有足够的时间向主体溶液扩散,溶质夹带就少,速冻则相反。只有保持在极缓慢冻结的条件下,才有可能发生溶质脱除(水分冻结时,排斥溶质,保持冰晶纯净的现象)作用。搅拌可以加速溶质向主体溶液扩散,从而减少溶质夹带;另外溶液主体的传质阻力(如黏度)小时,溶质夹带也少。表面附着量与冰晶的比表面积成正比(即与冰晶体的体积成反比)。溶质夹带不可避免地会造成溶质的损失。
3.浓缩终点
理论上,冷冻浓缩过程可持续进行至低共熔点,但实际上,多数液体食品没有明显的低共熔点,而且在此点远未到达之前,浓缩液的黏度已经很高,其体积与冰晶相比甚小,此时就不可能很好地将冰晶与浓缩液分开。因此,冷冻浓缩的浓度在实践上是有限度的。
(二)冷冻浓缩的特点
由于冷冻浓缩过程不涉及加热,所以这种方法适用于热敏性食品物料的浓缩,可避免芳香物质因加热造成的挥发损失。冷冻浓缩制品的品质比蒸发浓缩和反渗透浓缩法高,目前主要用于原果汁、高档饮品、生物制品、药品、调味品等的浓缩。
冷冻浓缩的主要缺点是:浓缩过程中微生物和酶的活性得不到抑制,制品还需进行热处理或冷冻保藏;冷冻浓缩的溶质浓度有一定限制,且取决于冰晶与浓缩液的分离程度。一般来说,溶液黏度愈高,分离就会愈困难;有溶质损失;成本高。
(三)应用于食品工业的冷冻浓缩系统
对于不同的原料,冷冻浓缩系统及操作条件也不相同,一般可分为两类:一是单级冷冻浓缩;二是多级冷冻浓缩。后者在制品品质及回收率方面优于前者。
1.单级冷冻浓缩装置系统
图2-29为采用洗涤塔分离方式的单级冷冻浓缩装置系统示意图。它主要由刮板式结晶器、混合罐、洗涤塔、融冰装置、贮罐、泵等组成,用于果汁、咖啡等的浓缩。操作时,料液由泵7进入旋转刮板式结晶器,冷却至冰晶出现并达到要求后进入带搅拌器的混合罐2,在混合罐中,冰晶可继续成长,然后大部分浓缩液作为成品从成品罐6中排除,部分与来自贮罐5的料液混合后再进入结晶器1进行再循环,混合的目的是使进入结晶器的料液浓度均匀一致。从混合罐2中出来的冰晶(夹带部分浓缩液),经洗涤塔3洗涤,洗下来的一定浓度的洗液进入贮罐5,与原料混合后再进入结晶器,如此循环。洗涤塔的洗涤水是利用融冰装置(通常在洗涤塔顶部)将冰晶融化后再使用,多余的水排走。采用单级冷冻浓缩装置可以将浓度为8~14°Bx的原果汁浓缩成40~60°Bx的浓缩果汁,其产品质量非常高。

图2-29 单级冷冻浓缩装置系统示意图
1—旋转刮板式结晶器 2—混合罐 3—洗涤塔4—融冰装置 5—贮罐 6—成品罐 7—泵
2.多级冷冻浓缩装置
所谓多级冷冻浓缩是指将上一级浓缩得到的浓缩液作为下一级浓缩的原料液进行再次浓缩的一种冷冻浓缩装置。图2-30所示为咖啡二级冷冻浓缩装置流程。咖啡料液(浓度为260g/L)由管6进入贮料罐1,被泵送至一级结晶器8,然后冰晶和一次浓缩液的混合液进入一级分离机9离心分离,浓缩液(浓度<300g/L)由管进入贮罐7,再由泵12送入二级结晶器2,经二级结晶后的冰晶和浓缩液的混合液进入二级分离机3离心分离,浓缩液(浓度>370g/L)作为产品从管排出。为了减少冰晶夹带浓缩液的损失,离心分离机3、9内的冰晶需洗涤,若采用融冰水(沿管进入)洗涤,洗涤下来的稀咖啡液分别进入料槽1,所以贮料罐1中的料液浓度实际上低于最初进料浓度(<240g/L)。为了控制冰晶量,结晶器8中的进料浓度需维持一定值(高于来自管15的料液浓度),这可利用浓缩液的分支管16,用阀13控制流量进行调节,也可以通过管17和泵10来调节。但通过管17与管16的调节应该是平衡控制的,以使结晶器8中的冰晶含量质量分数在20%~30%。实践表明,当冰晶质量分数占26%~30%时,分离后的咖啡损失质量分数小于1%。

图2-30 二级冷冻浓缩装置流程示意图
1、7—贮料罐 2、8—结晶器 3、9—分离机4、10、11、12—泵 5、13—调节阀 6—进料管 14—融冰水进入管 15、17—管路16—浓缩液分支管
五、膜浓缩
膜浓缩是一种类似于过滤的浓缩方法,只不过“过滤介质”为天然或人工合成的高分子半透膜,如果“过滤”膜只允许溶剂通过,把溶质截留下来,使溶质在溶液中的相对浓度提高,就称为膜浓缩。如果在这种“过滤”过程中透过半透膜的不仅是溶剂,而且是有选择地透过某些溶质,使溶液中不同溶质达到分离,则称为膜分离。
(一)膜浓缩的种类及操作原理
在膜技术应用中常根据浓缩过程的推动力不同进行分类,膜浓缩的动力除压力差以外,还可以采用电位差、浓度差、温度差等。目前在工业上应用较成功的膜浓缩主要有以压力为推动力的反渗透(Reverse Osmosis,简称RO)和超滤(Ultra Filtration,简称UF),以及以电力为推动力的电渗析(ED)。由于膜浓缩不涉及加热,所以特别适合于热敏性食品的浓缩。与蒸发浓缩和冷冻浓缩相比,膜浓缩不存在相变,能耗少,操作比较经济,且易于连续进行。目前膜浓缩已成功地应用于牛乳、咖啡、果汁、明胶、乳清蛋白等的浓缩。
1.反渗透
溶液反渗透是利用反渗透膜选择性地只能透过溶剂(通常是水)的性质,对溶液施加压力以克服溶液的渗透压,使溶剂通过半透膜而使溶液得到浓缩。其原理如图2-31所示。

图2-31 渗透与反渗透原理图
当纯水与盐水用一张能透过水的半透膜隔开时,纯水将自发地向盐水侧流动,这种现象称为渗透。水分子的这种流动推动力,就是半透膜两侧水的化学势差。渗透要一直进行到盐水侧的静压力高到足以使水分子不再向盐水侧流动为止。平衡时的静压力即为盐水的渗透压。如果往盐水侧加压,使盐水侧与纯水侧的压差大于渗透压,则盐水中的水将通过半透膜流向纯水侧,此过程即反渗透。
反渗透的最大特点就是能截留绝大部分和溶剂分子大小同一数量级的溶质,从而获得相当纯净的溶剂(如纯水)。
2.超滤
应用孔径为1.0~20.0nm(或更大)的半透膜来过滤含有大分子或微细粒子的溶液,使大分子或微细粒子在溶液中得到浓缩的过程称之为超滤浓缩。与反渗透类似,超滤的推动力也是压力差,在溶液侧加压,使溶剂透过膜而使溶液得到浓缩。与反渗透不同的是,超滤膜对大分子的截留机理主要是筛分作用,即符合所谓的毛细孔流模型。决定截留效果的主要是膜的表面活性层上孔的大小和形状。除了筛分作用外,粒子在膜表面微孔内的吸附和在膜孔中的阻塞也使大分子被截留。由于理想的分离是筛分,因此要尽量避免吸附和阻塞的发生。在超滤过程中,小分子溶质将随同溶剂一起透过超滤膜,如图2-32所示。超滤所用的膜一般为非对称性膜,能够截留相对分子质量为500以上的大分子和胶体微粒,所用压差一般只有0.1~0.5MPa。
像反渗透一样,超滤也存在浓差极化问题,即在溶液透过膜时,在高压侧溶液与膜的界面上有溶质的积聚,使膜界面上溶质浓度高于主体溶液的浓度。图2-33是膜两侧浓度分布示意图。图中C1是浓溶液主体浓度,C2是由于浓差极化造成的比C1高的膜表面上的浓度,C3是透过液浓度。
超滤截留的溶质多数是高分子或胶体物质,浓差极化时这些物质会在膜表面上形成凝胶层,严重地阻碍流体的流动,使透水速率急剧下降。此时若增加操作压力,只能增加溶质在凝胶层上的积聚,使胶层厚度增加,导致分离效率下降。因此,增大膜界面附近的流速以减薄凝胶层厚度是十分重要的。

图2-32 超滤原理

图2-33 膜两侧的浓度分布图
3.电渗析
电渗析是在外电场的作用下,利用一种对离子具有不同的选择透过性的特殊膜(称为离子交换膜)而使溶液中阴、阳离子与其溶剂分离。由于溶液的导电是依靠离子迁移来实现的,其导电性取决于溶液中的离子浓度和离子的绝对速率。离子浓度愈高,离子绝对速率愈大,则溶液的导电性愈强,即溶液的电阻率愈小。纯水的主要特征,一是不导电,二是极性较大。当水中有电解质(如盐类离子)存在时,其电阻率就比纯水小,即导电性强。电渗析正是利用含离子溶液在通电时发生离子迁移这一特点。
图2-34所示为电渗析的原理图。当水用电渗析器进行脱盐时,将电渗析器接以电源,水溶液即导电,水中各种离子即在电场作用下发生迁移,阳离子向负极运动,阴离子向正极运动。由于电渗析器两极间交替排列多组的阳、阴离子交换膜,阳膜(C)只允许水中的阳离子透过而排斥阻挡阴离子,阴膜(A)只允许水中的阴离子透过而排斥阻挡阳离子。因而在外电场作用下,阳离子透过阳离子交换膜向负极方向运动,阴离子透过阴离子交换膜向正极方向运动。这样就形成了称为淡水(稀溶液)室的去除离子的区间和称为浓水(浓缩液)室的浓离子的区间,在靠近电极附近,则称为极水室。在电渗析器内,淡水室和浓水室多组交替排列,水流过淡水室,并从中引出,即得脱盐的水。

图2-34 电渗析的原理图
离子交换膜是一种由高分子材料制成的具有离子交换基团的薄膜。如图2-35所示,它之所以具有选择透水性,主要是由于膜的孔隙度和膜上离子基团的作用,膜上的孔隙可允许离子的进出和通过。这些孔隙,从膜正面看是直径为几十埃至几百埃的微孔;从膜侧面看,是一条条弯弯曲曲的通道。水中离子就是在这些通道中做电迁移运动,由膜的一侧进入另一侧。膜上的离子基团是在膜高分子链上连接着的一些可以发生解离作用的活性基团。凡是在高分子链上连接的是酸性活性基团(如—SO3H)的膜就称为阳膜,连接的是碱性活性基团(如—N(CH3)3OH)的膜就称为阴膜。例如一般水处理常用的磺酸型阳离子交换膜其结构为:R-SO3-H+,其中R为基膜,—SO3H为活性基团,—SO3—为固定基团,H+为解离离子;季胺型阴离子交换膜的结构为:R-N+(CH3)3-OH-,其中R为基膜,—N+(CH3)3OH为活性基团,—N+(CH3)3—为固定基团,—OH-为解离离子(又称反离子)。

图2-35 离子交换膜作用示意图
在水溶液中,膜上的活性基团会发生解离作用,解离产生的离子进入溶液,于是在膜上就留下了带一定电荷的固定基团。在阳膜上留下的是带负电荷的基团,构成了强烈的负电场,在外加直流电场的作用下,根据同性相斥、异性相吸的原理,溶液中阳离子被它吸引传递并通过微孔进入膜的另一侧,而溶液中的阴离子则受到排斥;相反,在阴膜上留下的是带正电荷的基团,构成了强烈的正电场。同理,溶液中阴离子可通过膜而阳离子则受到排斥。此即离子交换膜具有选择透过性的原因。可见,离子交换膜发生的作用并不是离子交换作用,而是离子选择透过作用,所以更精确地说,应称为离子选择性透过膜。
思考题
1.试述食品干燥的目的。
2.影响湿热传递的主要因素?
3.干燥方法的分类?
4.影响干燥速率的因素?
5.简述喷雾干燥的特点。
6.冷冻干燥的原理?
7.干燥对食品品质有哪些影响?
8.中间水平食品的加工原理?
9.简述中间水分食品的加工方法。
10.简述食品浓缩的目的。
11.简述真空蒸发的优点。
12.顺流加料法和逆流加料法的优缺点?
13.冷冻浓缩的原理?
14.冷冻浓缩的特点?
15.反渗透的原理及应用?
16.超滤的原理及应用?
17.电渗析的原理及应用?
18.名词解释:绝对湿度、相对湿度、湿基含水量、水分活度、干燥速率、中间水分食品、闪蒸。