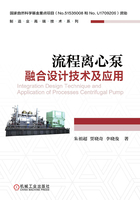
1.2 国内外研究现状
本书通过构建流程离心泵水力性能和转子动力特性的预测方法,建立运行状态监测与故障诊断技术,提出基于运行状态的监测预警及智能防控,开发具有远程监控、故障诊断的智能化大功率多级流程离心泵机组,并对产品进行应用示范和市场推广,为我国石化流程装备领域关键的核心设备实现国产化、替代进口提供一定的理论、技术和产品支撑。本书从离心泵水力性能预测、离心泵转子系统动力学特性预测、离心泵机组在线监测和故障诊断以及智能化流程离心泵机组产品开发和推广应用等方面来阐述国内外研究现状和发展趋势。
1.2.1 离心泵水力性能预测研究现状
1.离心泵内部流动计算的研究
在离心泵内部流动计算方面,大涡模拟(Large Eddy Simulation,LES)是目前最主要的数值计算方法。离心泵内部流动计算先后经历了无黏数值计算、准黏流数值计算和完全黏流数值计算三个阶段。随着旋转机械数值计算技术的发展,湍流模型的研究和应用也在不断深入。完全黏流湍流数值模拟方法可以分为直接数值模拟(Direct Numerical Simulation,DNS)、雷诺时均法(Reynolds Averaged Navier-Stokes,RANS)、大涡模拟方法和混合RANS/LES方法。在雷诺平均的框架下,常见的模型有k-ε模型[1]、k-ω模型[2]和雷诺应力模型(Reyn-olds Stress Model,RSM)[3]等。大涡模拟(LES)[4]方法与基于系综平均的RANS法相比,保留了可解尺度流场量尤其是压力的脉动特性,而且还可以捕捉湍流的大尺度结构以及模拟流动的非稳态效应,对资源需求(较DNS)也更合理。因此,LES具有模拟离心泵内复杂流动的极大潜力。但由于经典Smagorinsky模式基于小尺度脉动局部平衡假设,导致在剪切湍流中(尤其在近壁区)耗散过大;同时,由于该模型假设亚格子应力只正比于应变率张量,无法很好地适用于旋转流动[5],参考文献[6]提出了动态亚格子应力模式,但由于复杂湍流中无法实施时间或空间统计平均,参考文献[7]提出基于颗粒轨道的拉格朗日平均模式,仅比简单空间平均方法增加约10%的工作量,是一种有效用于复杂湍流的确定涡黏系数的动态方法。而参考文献[8]近年提出了一种雷诺应力约束的大涡模拟方法,改善了绕圆柱流动分离后的压力系数预估精度。在此基础上,参考文献[9]提出了一种包含三个应力张量项的联合约束亚格子应力模式,为螺旋湍流的大涡模拟提供了有利的工具。参考文献[10]利用动态亚格子模式的大涡模拟(LES)方法对25%设计流量工况离心叶轮的通道进行了数值模拟,捕捉到了“两通道”交替失速现象。参考文献[11]采用LES方法和滑移网格技术,对双吸离心泵不同工况下的内部三维非定常湍流流场进行了数值模拟,研究了叶轮区域流场特性及叶片表面的压力脉动。在具体流动计算中,考虑到次流场区域的离心泵内部全流场计算是最为合理也是最主要的计算途径。离心泵内部结构复杂,泵内除了主流道内部流动之外,还普遍存在间隙流、动静干涉等特殊流动现象,这些次流场流动的尺度相对主流动较小,但对离心泵的性能却有很大影响,在某些情况下甚至会引起离心泵运行故障。以上研究大多都是在设计工况下开展的,较少针对包括小流量及大流量工况的全流量工况进行研究。
随着叶轮流道的强旋转、大曲率、黏性及逆压梯度的作用,泵内不可避免地会出现各种流动分离、二次流、回流等不稳定流动结构。这些不稳定流动不仅表现出较为强烈的水动力学特性,同时在一定程度上改变了泵的能量转换特性,影响了泵的稳定运行。离心泵在外特性不稳定工况运行时,其内部流动存在的不同尺度轴向、径向和周向涡系等非稳态流动结构非常强烈,表现为明显的特性线驼峰和剧烈的出口压力波动等。带导叶液体火箭发动机(Liquid-propellant Rocket Engine,LRE)离心泵的扬程流量曲线曾在0.6倍设计流量和0.8倍设计流量附近出现两个典型的驼峰区域,导致所设计的离心泵不能使用。因此需要深入研究离心泵内部的不稳定流动,揭示泵内流动不稳定发生的机理及其对离心泵外特性不稳定影响的特性。
Pedersen N[12]结合数值研究了带有不同叶片数复合叶轮低比转速离心泵的内部流动结构,发现在小流量工况下存在强烈的流动不稳定现象。Atif A[13]利用PIV技术对混流泵在非设计工况下的流动结构进行了研究,表明性能曲线不稳定是由旋转失速造成的;压力脉动频谱有两个峰值,分别是动静干涉作用的频率及其谐振频率和旋转失速引起的叶片边界层分离产生的漩涡脱落频率。Feng[14]采用数值计算和PIV试验研究了离心泵内部导叶和叶轮动静干涉时叶轮内部的速度分布规律,研究发现导叶与叶轮之间的动静干涉作用造成泵内部流动的不稳定,并导致了泵内流体速度、压力等关键参数发生明显的波动。
为了捕捉离心泵内部的不稳定流动并进行特征提取,必须要定量研究叶轮流道内流体的运动细节,但运动部件的流场测量及其特征提取极为困难。离心泵叶轮出口的射流—尾迹结构是最常见的不稳定流动形式,叶轮出口的射流—尾迹作用易使出口处在周向上出现不均匀的压力分布,增强了叶轮与蜗壳之间的动静干涉作用效果。姚志峰等[15]通过试验研究叶轮形式对双吸离心压力脉动的影响,发现双吸离心泵普遍存在叶频、泵轴频和低于轴频的低频脉动成分,压力脉动沿圆周方向的不均匀性会产生其他谐波成分。Iino T和Kasai K[16]对离心泵内的压力脉动进行了试验测量,研究发现,流量和叶片与导叶之间的角度是引起脉动的主要原因。Furukawa A等[17]研究了离心泵导叶内的压力脉动特性,研究发现,离心泵叶轮与导叶间的相互干涉作用对离心泵内部流动的影响要明显强于叶轮的射流—尾迹作用对内部流动的影响,叶片的出口安放角对导叶内的压力脉动影响显著。
当离心泵在偏流量工况,尤其是小于设计工况区域运行时,内部流动更加复杂,流动分离、回流、二次流及旋转失速等现象尤为突出。Miyabe M[18]对离心叶轮的设计和非设计工况进行了试验研究,发现在设计工况相对速度场的射流—尾迹结构呈现出固定的非稳态特征;而在非设计工况下,旋转失速现象则表现出准周期性的不稳定特征。Abramian M[19]测量了三种工况下叶轮叶片出口边在中间高度上的二维瞬态速度场,并与激光多普勒测量结果进行了对比,发现在小流量工况下出现了大面积的旋转失速现象。Paone N[20]采用PIV和压力脉动试验研究了离心泵内旋转失速现象,研究发现,在旋转失速工况下,根据低通滤波压力不同,离心泵扩压器内的流动产生了外部射流和回流现象,并且两侧之间会交替变化;在设计工况附近,叶轮和导叶动静交界区域的高速泄漏流易造成导叶进口流道发生失速。Sinha M[21,22]利用PIV研究了离心泵内部旋转失速现象的演化规律,研究发现,离心泵导叶内失速团的泄漏和回流随着流量的减少而逐渐增强,失速团由一个流道扩散到两个流道。
离心泵结构复杂,泵内除了主流道内部流动之外,普遍存在间隙流等特殊流动现象,这些局部流动称为次流动,其尺度相对主流动较小,但对离心泵的性能有很大影响,在某些情况下甚至会引起离心泵的运行故障。国外学者对叶顶间隙的研究进行得较早,1965年Wood等[23]试验研究了叶顶间隙的影响,得到了叶顶间隙值与泵效率的关系。2006年,Engin等[24]研究了不同叶顶间隙下离心风机的性能,揭示了叶顶间隙值大小对半开式叶轮性能产生影响的主要因素。朱祖超针对半开式和全开式叶轮离心泵的试验表明,较大的间隙值可以有效地改善扬程—流量特性线的驼峰现象[25];而且对不同叶顶间隙下半开式叶轮离心泵进行了数值计算及外特性试验,分析了叶顶间隙流动对叶轮流道内流动的影响,并得到了该离心泵的最佳间隙值[26]。20世纪80年代,Dring等[27]提出了叶轮和导叶流体之间的相互作用由两部分组成,分别为势流的相互作用和尾迹的相互作用。随后,通过PIV[28]、热线仪[29]等设备,国内外学者对泵内的尾迹相互作用进行了一些试验研究[30]。在数值研究方面,Raul Barrio等[31]分析了叶轮与隔舌间隙率在8.8%~23.2%时对压力脉动和径向力特性的影响。徐朝晖[32]在动静叶栅间采用滑移网格技术建立了交互界面,同时,采用RNGk-ε湍流模型对高速泵全流场进行了非定常数值模拟。Yuan等[33]采用滑移网格技术,分析了动静干涉作用以及蜗壳流道和叶轮流道内压力脉动的变化规律。
综上可以看出,当离心泵在外特性不稳定的工况下运行时,各种内部不稳定流动结构的产生机理和对离心泵及其系统运行稳定的影响程度不同,具有各自独立的时频特性。但是,国内外对离心泵内部流动不稳定特性的研究还不够充分,还没有完全掌握各类不稳定流动的独立和联合作用机制。同时,需要进一步深入研究离心泵内不稳定流动引起的内部流动损失及其对离心泵振动等的影响。
2.离心泵水力性能预测的研究
在离心泵水力性能预测方面,由于离心泵流道形状和内部流动都非常复杂,尤其泵在非设计工况下的内部流动与设计工况相比变化较大,使得流动更为复杂,导致对其内部流动进行数值和试验研究比较困难,很难形成适合不同工况的性能预测模型。参考文献[34]编制程序预测了原、模型转换中粗糙度和雷诺数对离心泵效率变化的影响,研究发现叶轮、扩压器、蜗壳内部的损失比值随着比转速的增加而增加,粗糙度对扩压器、蜗壳的影响强于其对叶轮的影响。但随着比转速的增加,粗糙度对静止部件的影响,弱于其对转动部件的影响。参考文献[35]采用试验手段对输送表面活性添加剂的离心泵性能进行了分析,发现其效率比输送自来水高,而且随着活性剂浓度的增大而增加,同时流量的最大值也有所增加,在最佳温度情况下效率达到最大值。参考文献[36]选用标准k-ε和可伸缩壁面函数,在0°叶片安放角下,通过网格无关性分析,选择合适的网格数,分别在定常和非定常条件下对轴流泵进行了多工况点的数值模拟和外特性计算,发现非定常计算结果总体优于定常结果。参考文献[37]在分析基于水力光滑区Blasius摩擦系数的原、模型效率换算莫迪方法的基础上,采用适用于“过渡区”流动摩擦系数的Haaland和Swamee-Jain计算公式,参考莫迪拓展公式处理与雷诺数有关及无关的两种水力损失的方法,提出了考虑粗糙度影响的原、模型效率换算计算式,并进行了不同“过渡区”流动摩擦系数表达式、不同类型水力损失比例的计算研究。结果表明:在标准规定的原型粗糙度内,效率换算差值不大于0.0025。
参考文献[38]从介质能量的观点分析了不同工况下低比转数离心泵叶轮出口处的紊流流动结构,计算结果表明,在叶轮的出口附近靠近吸力面一侧存在一个低能区,而压力面一侧能量相对较高。当偏离设计工况时,该低能区的范围和强度略有增加,叶轮效率也相应降低。参考文献[39]通过泵的水力试验,对不同转速下大流量轴流泵的性能进行了对比分析。结果表明,在低转速下泵效率存在分层现象。分析发现效率分层的主要原因是低转速下试验所得的泵水力效率误差比较大,故需要对低转速下的试验效率值进行修正。为了使试验数据尽可能反映真实值,在试验设备能力允许的情况下,试验转速应不低于额定转速的80%。参考文献[40]采用一种研究泵汽蚀的CFD新方法对一台轴流水泵的性能进行了预测和验证。模拟采用多重参考系和瞬态方法,计算过程中流量从70%到120%发生变化,输出结果包括水泵扬程、水力效率和汽蚀特性,并与试验结果进行了对比,同时对泵内的汽蚀模式与试验中的动态影像也进行了对比。参考文献[41]发展了一种实用数值模型对离心泵性能曲线进行预测。该方法输入值包括离心泵几何参数和经验系数,输出结果为扬程、容积效率和功率。但该方法精度不够高,仅可作为工程中的简单速算。参考文献[42]从泵内瞬时转矩和能量的基本表达式出发,考虑叶轮和流体的加速以及瞬时流动结构演化的影响,并将蜗壳部分简化为额定等效长度的管路,得到了关于瞬时扬程的理论表达式,试验结果证实了该方法的有效性。参考文献[43]针对离心泵的汽蚀流动,提出了一种预测泵水力性能的计算模型,该空化模型基于黏性雷诺平均N-S求解器,采用该模型获得了非设计工况下流动的特征趋势,在两个不同流量系数情况下获取了低空化数时扬程系数的快速下降特征。
综上可知,尽管目前离心泵内部流动计算取得了一定进展,但经典Smagorinsky亚格子模式不能很好地预测旋转壁面附近流动的分离、回流以及多尺度漩涡等,LES方法在收敛精度、计算效率等方面还需进一步探索;在全面把握离心泵内部流动机理问题上还缺乏全流场全流量工况的系统性流动计算。在离心泵水力性能预测方面,虽然目前针对效率计算及性能预测进行的研究取得了一定的进展,但究其基本手段,一是基于某种湍流模型采用CFD的方法进行数值计算,二是采用试验方法进行统计分析,多数是针对某一具体对象进行研究,对非定常流动工况下离心泵效率计算和性能预测的误差分析研究得不够,适用于大功率多级流程离心泵性能预测的方法未能很好地总结出来,尤其是非定常流动工况下的离心泵。
1.2.2 离心泵转子系统动力学特性预测研究现状
1.离心泵流体激励力的研究
在离心泵流体激励力研究方面,流体激励对离心泵的振动具有显著的影响,而由于离心泵叶轮与蜗壳几何形状的复杂性与流动的工作介质,对其机理的研究相对于固体结构的振动而言更加困难。而叶轮内部流场流固耦合所造成的叶轮流体激励力主要是指在相对运动的叶轮与蜗壳间隙中,由于流体动量以及流体与叶片、蜗壳等的流固耦合作用而产生的流体力。要研究离心泵叶轮转子系统的振动特性,首先必须分析叶轮周围的非定常流场,并求出叶轮在流场中的受力情况,为离心泵的振动分析以及动力学特性预测做好理论基础。
目前,对于诱导离心泵流体激振的作用在叶轮上的流体激励力主要有三种不同的处理方法。第一种方法是将叶轮所受到的流体力简化为弹性支承,建立叶轮、蜗壳耦合作用下流体激励力引起叶轮涡动的二维数学模型,用数值分析叶轮流体力并采用试验方法进行验证[44]。但是,该方法并未考虑叶轮转子系统中的转轴,因此无法对转轴与叶轮间的相互作用力进行研究。同时,二维模型无法对叶轮涡动产生的陀螺力矩进行研究。因此,有不少学者通过数值方法,计算得到叶轮在两个垂直方向上受到的流体力,并在此基础上计算得到流体力支承的刚度、阻尼矩阵等[45],同时,通过试验测试方法进行验证[46]。第二种方法是将流体简化为转子的附加质量,忽略了叶轮所受的流体力,从而对转子系统的临界转速进行分析,其中,附加质量为叶轮中流体质量的20%~40%[47,48]。由于不需要计算真实的流体激励力,只需要从结构力学角度考虑系统的机械特性,因此这种方法在工程上得到了一定应用。但是,其具有明显的缺陷:由于叶轮增加了附加质量,转子系统的实际临界转速将发生变化,同样流量下随着叶轮转速的增加,叶轮实际所受的流体激励力也将以二次方增加,但是此简化模型并未考虑转速不同时附加质量的变化。同时,由于离心泵内流场呈现明显的不对称结构,在泵运行过程中,叶轮所受的流体激励力也是轴非对称的。因此,该模型需要进一步进行修正。第三种方法是直接将叶轮受到的两个方向的合力作用激励力加载到所建立的转子动力学模型上。参考文献[49]将叶轮径向力直接作为激励力,建立了离心泵转子刚性支承的Jeffcott转子系统,分析了转子系统的非线性特性以及转子的振动及轴心轨迹,研究结果表明,流体力与转子柔度的增加,叶轮间隙流动引起的振动对离心泵转子系统的不稳定性会产生非常重要的影响。
早在20世纪70年代初,就已经开展了对叶轮所受径向流体合力的研究[50]。主要集中于离心泵内压力脉动与压力脉动作用下蜗壳和叶轮结构自身的振动情况、叶轮—转子—支承系统流体激励力作用下的振动分析、汽蚀对离心泵振动的影响、流体激励作用下离心泵振动的稳定性分析、基于减小流体激励的离心泵结构设计、对离心泵流体激励的振动监测[51]、人体内离心血泵的减振研究[52-55]、不同工作介质对离心泵振动的影响[56]等。
随着试验手段的提高,研究人员对径向流体力进行了大量的试验研究[57-60]。Yoshida等人[61]通过改变叶片角度、叶片间距以及叶轮偏心对不平衡流体力进行了试验研究,研究结果表明,流体动力的幅值随着叶轮偏差程度的增加而变大,不平衡流体力与流体流量密切相关,而质量偏心所引起的不平衡力与流体流量无关。Black[62]对高速离心泵转子系统的横向振动和稳定性作了分析,首次发现离心泵在运行过程中会受到流体动力附加作用力的影响。Colding-Jorgensen[63]以一个简单二维叶轮为计算模型,并对流体作出无黏、不可压缩的假设,应用奇异势流理论计算出了刚度系数和阻尼系数,并建立了叶轮流固耦合力学模型。通过对转子稳定性的分析,得出结论:在一定运行条件下,叶轮所受到的流体附加作用力会使转子的稳定性下降。Tsujimoto等[64]以一个在蜗壳中涡动的二维离心式叶轮为研究对象,考虑蜗壳和脱流漩涡对叶轮周围流体的影响,得到了非定常流体的动力附加作用力。Adkins[65]以离心泵中的叶轮为研究对象对叶轮动力学特性进行分析,获得了刚度系数、阻尼系数、惯性系数,并提出了叶轮流固耦合作用力模型。Adkins和Brennen[66]开展了大量的理论和试验工作,对整个叶轮受到的流体附加作用力进行了分析,得出在总流体附加作用力中叶轮前侧盖板流固耦合力对叶轮的影响最大。Childs[67]提出了包含有叶轮涡动和倾摆的叶轮前侧盖板流固耦合作用力模型,采用Bulk-Flow理论推导了叶轮前侧盖板泄漏流的流体控制方程,通过摄动法对控制方程进行扰动分析,并应用分离变量法对一阶扰动方程进行求解,得出模型中的刚度系数、阻尼系数、惯性系数。Guinzburg等[68]分别对三种不同的泄漏流通道进行了研究,分析了不同泄漏流通道间隙、不同泄漏流量和不同叶轮偏心率对流体激励力的影响。随后Hsu Y[69]和Brennen C E[70]等人进一步研究了不同泄漏流通道、不同入口涡动率对叶轮前侧盖板流体附加作用力的影响。Childs[71]在整体流动模型理论的基础上,建立了叶轮转子系统中叶轮前侧盖板、叶轮后侧盖板、迷宫密封环的间隙流流体控制方程,得出了动态特性系数和流体附加作用力模型,并将理论分析与试验数据进行了对比。
20世纪末期,随着计算机技术的发展以及技术水平的进一步提高,研究人员通过数值计算与试验定量分析了叶轮蜗壳间隙变化所引起的叶轮径向流体力的变化[72]。Moore[73]将计算流体动力学的方法成功应用到了叶轮前侧盖板流固耦合作用力的求解中。Benra等[74]利用CFD软件和有限元软件,分别采用单向耦合和双向耦合计算方法,分析了单叶片无堵塞离心泵转子振动位移和所受的水力激励,对比了两种耦合方式下的计算结果,并使用非接触式电涡量传感器对转子系统的水力激振位移进行了测量。通过试验数据与数值计算结果的对比分析,发现数值计算所得的转子振动位移和流体激励力大于试验测得的值,且双向耦合的计算结果更接近试验值。Campbell等[75]建立了适用于泵叶片流体激振变形的流固耦合求解方法,并对一个典型涡轮叶片进行了定常流固耦合计算和水洞试验分析,两者结果吻合较好。Muench等[76]对一个由非定常湍流诱导振动的NACA翼型进行了流固耦合计算,结果与理论分析和试验值吻合较好,并提出了该流固耦合算法可以扩展到涡轮机械叶片的流固耦合分析方面。Jiang等[77]采用大涡模拟计算了泵的内部流场,利用有限元程序计算了泵部件的瞬态动力学特性,以叶轮内表面压力脉动作为边界条件,计算并分析了泵壳的流体诱导振动特性。
我国也有不少科研工作者对离心泵叶轮转子流固耦合问题的研究作出了贡献,但是相对于国外而言还处于起步阶段。裴吉[78]应用在单叶片离心泵上建立的流固耦合求解方法对1台蜗壳式离心泵转子—流动耦合系统进行了流固耦合振动求解。何希杰等[79]研究了离心泵水力设计对振动的影响。吴仁荣[80]以及黄国富等[81]对离心泵振动噪声的水力设计方法作了较全面、系统的分析,并提出了几种减小水激振动的水力设计原则。倪永燕[82]运用Fluent软件对离心泵进行了全流道非定常湍流模拟,研究了叶轮和蜗壳动静干涉对压力脉动和水力激振的影响。叶建平[83]分析了作用于蜗壳上的径向力变化规律,在仅受径向力的作用下,计算了离心泵的振动响应,并对其辐射声场进行了分析。Xu等[84]应用双向流固耦合方法对导叶式离心泵的外特性和内流场进行了分析,研究了流固耦合作用对外特性影响的机理。王洋等[85]采用单向流固耦合方法对离心泵冲压焊接叶轮的强度进行了分析,指出为了提高叶轮可靠性,应尽量避免其在小流量工况下运行。窦唯等[86,87]对高速泵三维流场进行了非定常计算,分析了高速泵内的压力分布情况,研究了高速泵叶轮上的稳态径向力和脉动径向力,分析了流体激励力对高速泵叶轮系统的振动及其轴心轨迹的影响。蒋爱华等[88-90]计算了离心泵叶轮转动过程中的瞬态内流场,同时,积分得出蜗壳内表面三个方向上的流体激励合力并进行频谱分析,最后运用九次多项式拟合、傅里叶级数与分段多项式拟合分别建立叶轮单周转动各向流体合力数学模型。结果表明:蜗壳所受出口方向、进口方向与垂直于进出口方向的流体激励力以叶片通过频率为基频波动,且波动幅值依次减小,波谷均出现于叶片通过蜗舌时;采用三段多项式拟合所建的数学模型与原始波形有最小的偏差,并且具有较低阶次。袁振伟等[91]在不考虑流体作用的转子动力学有限元模型的基础上,利用流固耦合分析导出的薄圆盘和圆柱体单独在流体中分别作平移和转角振动时受到的流体阻力公式,建立了组成转子的圆盘和轴段在流体中的单元运动方程,把作用在转子上的流体力整合到系统运动方程中,得到了考虑流体作用的转子动力学有限元模型。
胡朋志等[92]采用非定常不可压缩势流理论对叶轮所受的流体激励力进行了求解,以非线性油膜力为激励源对转子系统动力学特性和分岔特性进行分析,研究发现叶轮转子系统的稳定性会受到质量偏心和轴承间隙的影响。李同杰等[93]建立了故障叶轮转子系统非线性动力学模型,釆用处理非线性动力学问题的数值方法分析了横向流体激励力和转子故障这两个非线性因素对叶轮转子系统非线性动力学特性的影响。唐云冰等[94]分析了叶轮偏心引起的气流激励力对转子系统稳定性的影响,发展了系统失稳门槛值的计算方法,同时还讨论了叶轮偏心导致转子失稳的机理和特点。蒋庆磊等[95]将叶轮前侧盖板泄漏流通道简化成锥形结构,用CFX技术对内部流场进行分析,求出流体激励力,并把该流体作用力带入到离心泵转子系统方程,最后通过耦合法求出转子的不平衡响应。张妍[96]对叶轮前侧盖板流固耦合动力学特性进行了深入研究,分析了叶轮前侧盖板的轴向长度、叶轮前侧盖板的倾斜角度、转子偏心率、泄漏流通道平均间隙等相关参数对稳态压力分布和速度分布的影响,求出了叶轮前侧盖板的一系列刚度系数、阻尼系数和惯性系数。
对国内外相关研究情况进行对比分析可以看出:我国在离心泵流体激励力研究方面取得了长足的进展,并且研究成果也得到了广泛的应用。但是,相比于国外研究,我国在流体激振基础研究方面以及基础应用层面上还有较大的差距。大功率流程离心泵的振动问题十分复杂,相关研究涉及流体力学、传热学、结构力学、转子动力学、计算方法等学科交叉。
我国在大功率石化流程离心泵内部流体激振方面的理论基础储备和积累不够,可供借鉴的有效经验不多。对于大功率石化流程离心泵振动机理及影响因素的认识还停留在经验和试验上,缺乏专业的设计指导规范。在大多数研究中,基本上是利用商业软件进行数值分析研究,尽管研究问题的规模与复杂度日益增长,但是对于数值方法、计算模型的理解并不深入,尤其是对于大功率、高压、高转速离心泵目前仍停留在产品级的外特性试验,没有开展非定常内部流动的测试与分析工作,使得数值计算的模型和结果无从验证。由于缺乏相应的试验系统,只能基于最简单的公式得到了密封刚度参数,致使转子动力学计算结果误差较大和正确性判断较困难。而当振动问题出现后,国内目前主要依靠试车考核,从工艺方面考虑得较多,由于激振源、激励、路径和流固耦合的影响未知,只能被动采取抗振的措施。
2.转子系统动力学特性预测的研究
在转子系统动力学特性预测方面,随着流程离心泵向大型化、多级化方向发展,由于轴系转子设计不合理而引起的超标振动,以及由于转子系统动力学特性预测不准确而引起的轴系失稳现象,是影响流程离心泵机组运行稳定性及安全性的最主要因素。国内曾发生由于流程离心泵机组工作转速与临界转速相近引起的大轴弯曲事故,因此必须对多级流程离心泵开展转子动力特性分析,其关键是要提出准确的离心泵轴系建模及动力学特性求解方法,从而指导流程离心泵轴系转子设计。
目前,轴系转子动力学建模及分析应用最为广泛的是传递矩阵法与有限元法。早期,参考文献[97]和参考文献[98]拓展了Myklestad-Prohl传递矩阵法的使用范围,求解了考虑阻尼的复特征值和特征矢量。参考文献[99]应用传递矩阵法,建立了考虑机械密封影响的转子轴承模型,发现密封对于系统的临界转速有较大的影响。传递矩阵法的主要特点是不会因系统所划分单元数的增加而影响传递矩阵的阶次,且各阶频率计算方法相同,但当考虑支承等转子周围结构时建模比较困难[100]。参考文献[101]通过有限元法分别对转子、轴承、支承进行了建模研究,分析了不同刚度、阻尼的支承对于系统稳定性的影响,并提出了改进支承设计的方法。参考文献[102]对转子和支承进行了有限元建模,提出了一种减少轴承支承自由度的方法,并验证了其对系统稳定的影响。有限元法特别适应于转子和周围结构组成的复杂系统的建模和分析,能够较容易地通过编制程序来计算系统的特征值[103],而且有限元法适用于对精度要求很高的转子系统,建模准确性已得到了验证[104-106]。到目前为止,转子的有限元模型已经基本成熟,计算过程中考虑了转动惯量、轴向载荷、陀螺力矩、轴承刚度、剪切变形、内外阻尼等因素。
此外,大功率多级流程离心泵在设计及制造过程中,多应用环形密封以减小静止及转动部件间的流动损失,特别是在高压多级离心泵或高速离心泵中,由于密封及平衡压力的需要,存在多组如密封口环、级间密封及平衡鼓等液体环流密封。上述环形密封间隙内的流动一方面会造成泄漏,降低离心泵效率;另一方面,当水泵环形密封两端存在压差时,对泵轴系的动力学性能及动力学行为产生较大影响。以参考文献[107]和参考文献[108]为代表首次对环流密封动力特性进行了定量分析,并提出了阻塞流的假设。随后,Black和Jessen[109-112]基于滑动轴承动力学特性求解方法应用并发展了短轴承理论,给出了密封线性等效动力学特性系数的定义及求解方法,其计算结果在雷诺数小于2×104范围内已被试验证实。近年来,以Childs为代表的美国德州农工大学涡轮重点实验室针对不同长径比的光滑环流密封动力学特性求解,提出了完善的分析方法,并在轴系动力学特性计算、校核及布局优化设计中得到了一定的应用[113,114]。
离心泵转子动力学特性计算需要考虑叶轮口环和平衡鼓等间隙处的次流动与轴系结构的作用,次流动区域流场与轴系固体结构场的单向耦合计算是常用的动力学分析手段。参考文献[115]和参考文献[116]提出了代表性的耦合方法,分别利用有限差分或有限元法对流场及固体场划分网格,建立数学模型后计算得到转子位移响应及流场区域的压力分布,并利用交界网格法在两场之间传递数据,实现耦合计算。参考文献[117]对迷宫密封腔内可压缩气体间隙流场进行了CFD模拟,所得流体力与轴系结构进行单向耦合计算,并分析了预旋对轴系动力学特性及动力学行为的影响。参考文献[118]基于CFD方法求解得到了密封动力特性系数,建立了转子—轴承—密封系统有限元模型,对轴承和密封耦合作用下转子同步振动特性与转子不稳定振动特性进行了深入研究。以上分析中密封流场的CFD计算进出口边界条件均局限于经验公式及经验系数,没有从全流场计算角度准确判定次流动区域的边界条件,耦合求解所得轴系动力学特性及动力学行为有较大误差。
综上所述,国内外研究学者对轴系动力学特性求解模型与方法、轴系动力学行为定性与定量研究做了很多工作,但是与轴系固体场耦合计算中的间隙处次流场计算多基于经验公式及经验系数进行,流体激励力及轴系耦合模型还有待改进、完善。
1.2.3 离心泵机组在线监测和故障诊断研究现状
1.离心泵机组在线监测研究
离心泵机组在线监测研究方面,现代监测技术大致经历了以下两个阶段。第一个阶段是以动态测试技术和传感器技术为基础[119],信号处理技术是主要处理手段。得益于现代科技的快速发展,这两项技术已经在工程中得到广泛的应用。根据监测的参数不同,我们可以利用噪声、振动、温度、力、电、光、射线、磁等多种传感器,依赖各自的噪声、振动、热成像、光谱、铁谱、无损检测等监测分析技术进行分析。数值处理与信号分析理论的发展,给微计算机监测系统的应用提供了理论保障,对比分析、函数分析、状态空间分析、统计和模糊分析、逻辑分析方法等数据处理方法迅速被应用到工程中。
第二个阶段是以人工智能技术为基础[120],人工智能技术的应用是现代监测技术智能化发展的体现。这一阶段的研究内容与实现方法是以知识处理为核心,替代了以数据处理为核心的过程,开展了神经网络、专家系统和应用技术的研究和模糊分析等理论、方法。人类的知识,包括领域知识和求解问题的方法在这一阶段中起主导作用。同时通过将数据、知识处理与信号检测都整合在一套设备中,利用简单的操作来替代复杂的分析过程,使得这类设备的操作难度大大降低,甚至适用于一般操作人员。在泵运行状态的监测过程中,现代计算机信号分析测量技术,诸如红外测温、超声、声发射等已经代替了传统的眼看、耳听、手摸。
欧、美等发达国家对泵测试技术的研究起步较早,监测系统的产品已比较成熟,对于特殊泵的研制、泵的开发与创新特性测试等方面国外技术更加成熟。目前,国外的泵监测系统呈现出集成化高、体积小、可移动、多功能、易操作等特点[121]。1961年,英国国立工程实验室(NEL)就建立了自己的水力实验台,该实验台适用于水泵和模型水轮机(最大直径500mm)的性能试验,可以以开式和闭式两种循环方式进行效率和汽蚀试验,部分参数可自动控制,试验数据由计算机进行自动采集、处理,并自动绘制和打印试验结果。西德KSB公司和瑞士苏尔寿公司的水泵实验台均采用了计算机自动化监测系统。又例如英国Cussons Technology公司生产的P6250齿轮泵、轴流泵、离心泵和活塞泵测试平台等。但这类水泵测试装置仍存在如数据处理功能薄弱、缺少嵌入式数据处理分析系统、效率不高等缺陷。
在国内,泵监测技术的发展相对较慢,其发展历程可以简要划分为两个阶段:20世纪80年代以前和20世纪80年代至今[122-124]。20世纪80年代以前,我国的泵监测手段比较落后。泵性能参数测试设备仍主要以手动操作试验过程、手动测量试验数据、手工绘制曲线为主,存在测量手段落后、测试仪表众多、测试精度差、劳动强度高、测试效率低等缺点。20世纪80年代至今,随着计算机技术、通信技术和智能控制技术的高速发展,自动控制领域日新月异,智能仪表、先进的控制方法等层出不穷,这给泵的监测技术带来了契机。智能电磁流量计、超声波流量计、激光流量计、智能电容式压力变送器、转矩转速传感器、微机扭矩仪、单片机、PLC等先进的电子装置迅速地被应用于智能的泵监测系统中,极大地提高了泵监测系统的自动化程度、测试精度、响应速度和人工效率[125]。中国农业机械化科学研究院、山东省农业机械科学研究所、江苏大学等单位相继对水泵试验装置进行了研究与开发,建立了各具特色的试验装置,他们为水泵自动测试系统的不断完善发挥了先导作用。如山东省农业机械科学研究所给荏原博泵泵业有限公司研发的特大型水泵实验台,功能完备,但操作也相对复杂;另外,江苏大学TP自动化研究所开发的泵参数综合测试仪则结构紧凑,安装方便。
2.故障诊断的研究
故障诊断始于20世纪70年代英国和日本对锅炉、压力容器和铁路机车等领域的研究。国外普遍采用的故障诊断技术使得设备维修费用平均降低15%~20%。离心泵的故障诊断已从纯粹的以动态测试技术和传感器技术为特征逐步向以人工智能为特征进行转变。基于动态测试技术和传感器技术的离心泵在线监测技术的发展与应用已相对成熟,在在线监测的基础上实现基于人工智能的故障诊断是提高离心泵智能化水平的关键。采集数据的预处理、数据库建立和模型算法等相关方法相对成熟,关键是如何采用这些方法来构建适用于大功率多级流程离心泵的故障诊断模型。
在故障诊断模型研究方面,参考文献[126]运用离散事件系统规则研究了水泵和阀门系统的故障诊断问题,将系统状态划分为正常态和故障态两种情况,但没有提出故障诊断定性推理的具体策略。参考文献[127]运用模糊逻辑理论研究了中压输电线路间歇性接地故障的检测问题,这是一种典型的定性故障诊断方法。而基于定量分析的故障诊断方法则是通过对研究对象建立数学模型,得到表征故障对系统性能影响程度的残差信息,通过对残差进行分析以达到故障诊断的目的。常用的方法有Lyapunov理论、随机切换理论,以及统计模型、小波变换、经验模式分解、粗糙集和决策优化等。参考文献[128]提出了一种基于经验模式分解和多重支持向量机相结合的间歇故障诊断方法,研究表明此方法可以有效降低间歇故障对系统造成的虚警。参考文献[129]将信息嫡引入故障诊断中,提出了定量评价旋转机械振动状态的方法,并把它作为一种特征量来分析。讨论了功率谱嫡、小波空间特征嫡、奇异嫡和涡动状态特征嫡的定义及应用场合。参考文献[130]采用支持向量机(Support Vector Machine,SVM)的特征提取方法,基于振动信号概率密度服从正态分布假设的函数展开法,提出了在噪声环境中分离出有用信息的盲源分离法(Blind Source SeParation,BSS)。各种特征提取方法的综合利用也成为近年来故障诊断领域研究的热点,如隐马尔科夫模型(Hidden Markov Model,HMM)及其拓展方法引入到了离心泵振动信号的分析诊断中,把语音、图像等信号特征提取方法的研究推向了更深的层次。参考文献[131]和参考文献[132]把故障诊断技术应用于水电机组,采用模糊核聚类、多类支持向量机、模糊K近邻等方法利用振动数据判断水电机组的故障情况,其方法能分离有效特征,处理分布不均匀和线性不可分的复杂数据,具有较高精度。参考文献[133]和参考文献[134]建立了基于小波变换的振动特征提取方法,采用SVM方法应用故障诊断,具有比较高的准确度。
从上面的分析可以看出,尽管国内外已经针对旋转机械开展了基于振动的故障诊断技术研究,但针对多级流程离心泵也仅仅是针对振动的单一维度进行分析,定性结合定量故障诊断技术研究还不完善,特别是对基于流场和转子动力学的智能诊断方法还没有建立起来。
1.2.4 智能化流程离心泵机组产品开发研究现状
泵是流体输送的关键设备,是一种在国防和工农业生产领域广泛应用的动力机械,耗电量约占全国总发电量的20%,离心泵是最重要的一类泵产品,约占所有泵类产品的70%左右。而智能化大功率多级离心泵的应用前景十分广泛,主要潜在市场有中哈、中缅、中俄油气管道的原油输送项目;海上油气开采中的海洋平台与陆上终端建设项目;我国城市化进程中加大能源需求项目;节能减排与城市雾霾治理中的推进油品升级改造项目;推进我国能源战略储备与替代工程中的煤制油、煤制气、煤制烯烃、煤化工等项目;中东、俄罗斯等国家推进油气深加工建设项目;页岩气、原油产品开发项目。同时,在新能源领域智能化大功率多级离心泵的应用前景也十分可观,潜在市场主要有核电、新型核反应堆技术、核化工和核废处理等领域、光热发电中的一回路高压循环输送领域、海水淡化工程以及医药化工、精细化工等领域。同时,在国防与军工领域方面,伴随着复杂的国际环境,推进“一带一路”国家战略的利益保障,全面发展国防建设,为国家经济建设保驾护航的重要作用,中国海军走出第一岛链,迈向远洋是必然的趋势。安全可靠、长周期运行、低振动噪声以及高智能化战术装备是国防军工未来发展的重中之重。目前,现有常规舰船的换装升级,新建舰船系列装备对具有高可靠性、高效水力性能、低振动噪声的智能化离心泵机组产品的需求十分巨大。但是,我国离心泵产品在可靠性、效率、智能化等方面与国际先进水平还存在较大差距,涉及国防军工的特种离心泵产品仍受到西方的技术封锁。
目前国外的技术和产品的新进展要远远超过国内同行,近年来世界主要泵公司相继推出了各自具有不同特点的智能泵新技术和新产品。其中比较典型的包括:ITT公司推出的具有以14项专利技术为基础的Ps系列智能泵控制器(Pump Smart),集合了化工泵、化工工艺流程、变频器三方面的技术和专长,为优化流程系统的性能和提高泵运行的稳定性提供了一种世界领先的有效解决方案。其优点包括可实现泵送系统的智能控制,优化和保护整个泵送系统,稳定流程工艺,减少故障维修,延长泵送系统寿命,提高泵送效率,节能降耗。可以将能量消耗和维护成本降低30%~70%。这种智能泵控制器具有泵干运转保护、最小流量保护和汽蚀保护功能,并可以对流程系统内仪表的故障进行诊断和应急控制,可以在那些导致泵和机械密封损坏的异常工况下,对泵进行保护,并维护泵送流程。
这种智能泵控制器可以使泵以较低转速在最佳效率点附近运行,降低轴承和密封上的载荷,延长泵的使用寿命。而离心泵转速降低20%,则可以减少50%的电能消耗。第5代智能泵控制器产品也在近两年得以推出。新推出的智能泵控制器对泵的控制和保护功能更加强大,其中具有代表性的专利功能可以在无任何仪表检测设备的情况下实时计算泵送流量,并将误差控制在正负5%以内。
美国福斯集团研制开发出的IPS Tempo系列产品是一种智能泵优化控制和保护系统。这种新型智能泵能够调整泵的流量、压力、温度和液位的变化,监测流程的各种变量和泵功率,并提供状态监测和控制,其特点是改进泵的性能,降低泵的使用周期成本,降低能耗可达50%,同时可提高平均故障间隔时间。这种新型智能泵采用了变频驱动器技术、泵结构优化技术以及工业级电力驱动器,一个可提供极佳保护和可靠性的直观菜单驱动用户界面。这种新型智能泵适用于石油化工、水工业、采矿和一般工业等领域。而国内在智能泵研发方面,目前只有极少数的泵企业在进行一些初步的探索研发,属于刚刚起步阶段,相对于国外同行是非常落后的。为了改变我国的这一现状,与发达国家技术接轨,开发新型、高效、智能的大型流程离心泵系列产品是非常必要的,这对我国流程离心泵行业具有重大的战略意义。