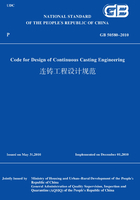
3 General Principle for Design of Continuous Casting Engineering
3.0.1 New iron and steel enterprises and general steelmaking plant shall adopt sequence casting process;except that mold casting is required for a very few special product,the continuous casting is also the prevailing process in special steelmaking plant.
3.0.2 New continuous casting engineering shall adopt hot delivery of casting strand,and the possibility of direct rolling shall be reserved for future according to the conditions.
3.0.3 The revamped continuous casting machine in the existing plant shall continuously optimize the production process conditions.
3.0.4 The relevant unit shall continuously promote the development and application of near-net shape continuous casting technology such as thin slab continuous casting.
3.0.5 According to the different raw material conditions and the product requirement,new steelmaking plant shall equip with necessary ladle refining facilities.The liquid steel shall be subject to ladle refining prior to casting.
3.0.6 The liquid steel supplied to continuous casting shall be tapped in hot ladle,and the thermal insulation measure of liquid steel shall be intensified.
3.0.7 The design shall create the conditions for sequence casting,and the following requirement shall be met:
1 The new or revamped caster shall adopt the ladle turret,and the interference during liquid steel transportation shall be reduced.
2 Two tundish cars with fast replacement shall be adopted.
3.0.8 The design of tundish shall be in accordance with following requirement:
1 The large volume tundish with flow control shall be adopted;
2 The shape of tundish shall be selected according to the type of machine;
3 The square bloom caster,round bloom caster and slab caster with large section shall adopt stopper rod or sliding gate to control the liquid steel flow.The square billet caster and round billet caster with small section shall adopt stopper rod or sizing nozzle;
4 According to the continuous casting process requirement,the tundish for slab as well as square bloom and round bloom with large section shall adopt the built-in or outboard submerged nozzle.The outboard submerged nozzle shall be equipped with quick-changing unit,and the built-in submersed nozzle shall be equipped with emergency gate.
3.0.9 The different type of protective casting design shall meet the following requirement:
1 When casting the deep-draw steel,silicon steel,stainless steel,alloy steel and other high quality steel grade,the protection device for liquid steel flow shall be adopted between the ladle and tundish.
2 When casting the slab or high quality square bloom with edge length bigger than or equal to 130mm or the round bloom with diameter bigger than or equal to 140mm,the casting with submerged nozzle and protective powder shall be adopted between the tundish and mould.When the high quality square billet with edge less than 130mm and round billet with diameter less than 140mm requires the protective casting,casting with either inert gas protection or submerged nozzle and protective powder can be used.
3 When casting the beam blank,the casting with semi-submerged nozzle and protective powder shall be adopted between tundish and mould.
4 The surface of liquid steel in ladle and tundish shall be covered by thermal insulation powder,and the cover shall be placed on the ladle and tundish.
3.0.10 New square bloom caster,round bloom caster and slab caster preferably adopts the hydraulic oscillation unit.
3.0.11 Continuous caster shall adopt the automatic control of mould level.
3.0.12 Superheat degree of liquid steel shall be selected according to the quality requirement of steel grade.The low temperature casting is preferably used for the steel grade with strict quality requirement.The reheating facilities for liquid steel in tundish can be adopted in case of necessary.
3.0.13 Selection and control of secondary cooling mode shall meet the following requirement:
1 The secondary cooling for square bloom and round bloom with edge or diameter less than 200mm can either adopt the water spray cooling or air-water mist cooling based on the steel grade requirement.The secondary cooling for slab,bloom and round bloom with edge or diameter bigger than 200mm can adopt the air-water mist cooling.
2 The secondary cooling of continuous casting product shall adopt L1 automatic control or dynamic control by L2 model.
3.0.14 Slab caster shall preferably adopt the remote and automatic roll gap adjustment technology of segment,and the automatic inspection unit of roll gap shall be equipped accordingly.
3.0.15 Slab caster(including thin slab caster)and the square bloom caster for production of alloy steel and high carbon steel shall adopt the dynamic solidification model and soft reduction technology.
3.0.16 For the slab caster,square billet caster and round billet caster for production of high quality steel grade such as silicon steel,stainless steel,alloy steel,and high carbon steel,the corresponding electromagnetic stirrer shall be provided in the proper position of caster according to the requirement.
3.0.17 Thin slab caster and conventional slab caster with high casting speed shall adopt the electromagnetic flow control technology for mould.
3.0.18 Fume and dust collection and dedusting unit shall be provided for torch cutting,scarfing or hot grinding of stainless steel and high chrome alloy casting products and in the tundish tilting area.
3.0.19 Utility facilities of continuous caster such as water and gas shall meet the following requirement:
1 The continuous caster shall be equipped with dedicated cooling water circulating system,and the quality and parameters of cooling water shall meet the requirement of production process.The attention shall be paid for antifreezing of piping in north area in winter.
2 The cooling water system of continuous caster shall be equipped with safety water supply facilities.
3 Various gas media and fuel materials used by continuous caster shall meet the requirement of pressure,flow and quality at TOP of production consumers.The compressed air for secondary air mist cooling of continuous caster shall be supplied in dedicated line.
3.0.20 Various energy media supply systems of continuous caster shall be equipped with metering and detection instrument.The measured data shall be input into the data collection system of computer.
3.0.21 Continuous caster must have two power supply lines.
3.0.22 Key equipment shall be equipped with power facilities for emergency drive
3.0.23 Equipment maintenance facilities shall be designed in the continuous casting,engineering,which shall meet the following requirement:
1 The continuous caster shall be designed with integral replacement as per component and assembled parts and fast lifting by crane and shall adopt the offline maintenance.
2 When additional continuous caster is provided in steelmaking plant(workshop),the corresponding maintenance facilities shall be provided at same time.
3 New continuous caster shall be equipped with production satisfied operational exchange part.
3.0.24 Ladle turret in casting floor and tundish area shall be provided with liquid steel emergency treatment system which shall include the facilities such as emergency tank,overflow tank,emergency chute and emergency ladle.
3.0.25 Design of energy conservation and environment protection,industrial hygiene,safety and firefighting,etc for continuous casting engineering shall meet the regulations of application national standard.
3.0.26 Design of continuous casting engineering shall preferably adopt the domestic equipment and technology.The supporting technology and equipment as well as production software which are not available at home or the domestic products cannot meet the requirement can be imported properly;the imported equipment or technology shall be of technical advancement,affordable and reliable running.
3.0.27 Obsolete and backward second-hand continuous casting production equipment is forbidden to use.