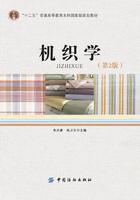
第三节 清纱、接头、定长、毛羽控制及上蜡
一、清纱
为提高纺织品的质量和后道工序的生产效率,在络筒工序中应有效地清除一些必须除去的有害纱疵,这项工作称为清纱,生产中可以使用机械式清纱器或电子清纱器。
机械式清纱器主要有隙缝式清纱器、梳针式清纱器、板式清纱器,如图1-28所示。纱线从薄钢片1和2、上板6和下板7或针齿4与固定刀片5之间的缝隙中通过,纱线的疵点在通过缝隙时受阻,发生断头,进而由人工清除纱疵。8为垫片。它们虽然结构简单、价格低廉,但清除效率低,对纱疵长度不能鉴别,并且接触纱线容易把纱线刮毛、产生静电,在化纤产品、混纺产品和高档天然纤维产品的生产中已无法满足日益提高的产品质量要求,因此现在很少使用。
图1-28 三种机械清纱器
电子清纱器不仅具有非接触工作方式、清除效率高等优点,而且可以根据产品质量和后工序的需要,综合纱疵长度和截面积两个因素,灵活地设定清纱范围。清除必须除去的有害纱疵,保留对质量和后加工无影响或影响甚微的无害纱疵。生产实践表明,使用电子清纱器后产品的质量和后工序生产效率都有明显提高。
从电子清纱器的功能来分,有单功能(清除短粗节纱疵)、双功能(一般为清除短粗节和长粗节纱疵)、多功能(清除短粗节、短细节、长粗节、长细节、棉结疵点)多种。从电子清纱器的工作原理来分,有光电式和电容式两种。
(一)光电式电子清纱器
光电式电子清纱器是将纱疵形状的几何量(直径和长度),通过光电系统转换成相应的电脉冲信号来进行检测,与人视觉检测纱疵比较相似。其装置由光源、光敏接收器、信号处理电路、执行机构组成。典型的光电式电子清纱器工作原理如图1-29所示。
图1-29 光电式电子清纱器工作原理
纱线高速运行时通过光电检测槽,槽的一侧是由红外发光管和光学装置构成的检测光源。光学装置起到漫射作用,产生三维光源的效果,使得对扁平纱疵的检出能力得到提高。槽的另一侧为光电接收器,采用了硅光电池。当纱线上出现纱疵(粗节、双纱、细节等)时,硅光电池的受光面积发生变化,硅光电池的受光量及输出光电流随之变化,光电流的变化幅值与纱疵的直径变化成正比。当纱线运行速度恒定时,纱疵越长,则光电流变化的持续时间也越长。光电式电子清纱器就是这样把纱疵的直径及长度两个几何量的变化转换为光电接收器输出电流脉冲的幅值及宽度的变化,达到光电检测纱疵的目的。
光电接收器输出的电流脉冲经后续信号处理电路处理,如果处理电路输出的电信号幅度超过其设定值,则触发切刀驱动电路工作,驱动切刀切断纱线,将纱疵除去。
(二)电容式电子清纱器
电容式电子清纱器以电容传感器测定单位长度内纱线质量,从而间接反映纱线截面积的变化,进行纱疵检测。其装置由高频振荡器、电容传感器、检测电路、信号处理电路和执行机构组成。典型的电容式电子清纱器工作原理如图1-30所示。
图1-30 电容式电子清纱器工作原理
作为检测元件的电容传感器由两块金属极板构成,极板之间无纱线通过时,电容量最小。当纱线以基本恒定的速度通过时,由于纤维介电常数比空气大,于是电容量增加,增加的数量与单位长度内纱线的质量成正比关系。因此,纱线截面积的变化,即单位长度内质量的变化被转换成传感器电容量的变化。
发自高频振荡器的高频等幅波经电容传感器后,被调制成随纱线截面积做相应变化的调幅波。调幅波经检测电路转换成电脉冲信号。在纱速恒定条件下,脉冲信号幅度和宽度与电容内纱疵截面积增量及纱疵长度成正比。
脉冲信号经后续信号处理电路处理,如果输出的电信号幅度超过其设定值,则触发切刀驱动电路工作,驱动切刀切断纱线,将纱疵除去。
由于光电式电子清纱器和电容式电子清纱器的检测工作原理不同,因此它们的工作性能有较大差异。表1-1对两者的工作性能进行了对比。
表1-1 光电式和电容式电子清纱器主要工作性能对比
二、接头
络筒过程中,清除纱疵、处理纱线断头和换管等都需要对纱线进行接头。在少数普通络筒机上,接头工作由手工或手工辅助打结器完成打结动作,进行接头;在自动络筒机上,上下吸嘴之间的纱线接头工作由捻接器自动完成,实现无结接头,加工的纱线称为无结纱。纱线打结之后形成了结头,对应于不同纤维材料的加工,结头有多种形式。由于络筒结头在后道加工中会脱结或重新断头,严重影响后道加工工序的生产效率,并且机织物、针织物正面的结头使成品外观质量下降,于是络筒工序的打结频率(长度为105m纱线中结头个数)受到限制,进而络筒的清纱除疵作用就很难得到加强,阻碍了布面质量的进一步提高。随着捻接技术的产生和发展,这一矛盾得到解决。捻接技术从根本上改变了以往清纱去疵工作的实质:以一个程度不严重的“纱疵”(结头)代替一个程度严重的纱疵。捻接后接头处的纱线直径为原纱直径的1.1~1.3倍,接头后断裂强力为原纱断裂强力的80%~100%。捻接器的使用克服了由结头引起的诸多缺点,从而使清纱去疵工作有条件得以加强,可以采用高灵敏度的电子清纱器,积极有效地切除纱线上的疵点,使纱线质量提高、后工序断头减少,对提高后工序生产效率和产品质量有显著效果。
纱线打结对机织物和针织物布面外观的影响很大。布面上纱线结头明显可见,而纱线捻接处与其他区域之间的差异难辨。
目前,络筒捻接技术的应用已十分普遍,考虑到优化产品质量,普通络筒机也配置了捻接器,以取代纱线打结。纱线的捻接方法很多,有空气捻接法、机械捻接法、静电捻接法、包缠法、粘合法、熔接法等。但是技术比较成熟,使用比较广泛的是空气捻接法和机械捻接法两种。
图1-31 捻接腔结构示意图
1.空气捻接 空气捻接器分为自动式和手动式两种。它们的捻接原理都是利用压缩空气的高速喷射,在捻接腔内将两根纱尾的纤维捻缠在一起,形成一根符合后道工序加工质量要求的、无结头的捻接纱。捻接质量较好的捻接器,通常在保持管内先以高速气流对被捻接的两根纱线的纱头进行吹拂退捻,此后退捻的纱头在捻接腔内相对叠合,并由高速漩流进行捻接。捻接腔有很多种形式,其中用于短纤纱的捻接腔结构如图1-31(a)、(b)所示,图1-31(c)适用于长丝、长纤纱的捻接腔。
用于短纤纱的管状捻接腔壁上有两个出流孔,压缩空气自孔中射出时,形成向管腔两端扩散、反向旋转的两股高速漩流。纱尾在高速漩流的拍击下,纤维相互混合,并以Z捻向或S捻向捻缠成纱,捻缠外形较好。
用于长丝、长纤纱的捻接腔壁上只有一个出流孔。纱尾的纤维在高速气流的冲击振动下能更均匀地相互混合、纠缠、捻接成纱。
空气捻接器应用范围很广,可用于不同特数的棉纱、毛纱、合纤纱、混纺纱、股线及弹力包芯纱。用于不同品种纱线时,工艺调整乃至空气捻接器更换都较方便。
2.机械捻接 机械式捻接器使用范围比较狭窄,主要是棉纱。随着机械捻接技术的发展,其适用范围也会扩大。机械式捻接器是靠两个转动方向相反的搓捻盘将两根纱线搓捻在一起,搓捻过程中纱条受搓捻盘的夹持,使纱条在受控条件下完成捻接动作,捻接质量好,明显优于空气捻接,捻接处纱线条干均匀、光滑、强力高。
三、定长
后道加工工序对络筒提出了定长自停要求,这不仅能减少后工序的筒脚纱浪费及倒筒工作,还可以提高后加工的工艺合理性。早期的筒子定长采取挡车工目测筒子大小或尺量筒子直径等方法。目前普遍采用电子定长,筒子定长的精度大为提高,定长误差要求一般为±1%以内。
电子定长按测长原理可以分为直接测量和间接测量两种。前者通过测量络筒过程中纱线运行速度,达到测长的目的,后者则是通过检测槽筒转数,转换成相应的纱线卷绕长度,进而实现定长。目前通常应用间接测量原理。
间接测量定长装置把槽筒转过圈数转换成m个电脉冲信号,n为传感器磁钢极数。于是纱线卷绕长度L与脉冲个数的关系为:
式中:m——脉冲个数;
a——槽筒回转一周筒子绕纱长度。
a数值的确定将直接决定定长精度,由于传动点上槽筒和筒子的相对滑移、张力作用下纱线伸长量、纱线的质量、络筒机械状况等随机因素的影响,a的数值不可能通过理论计算求得,只有利用标定的方法来测算。
现有的电子定长仪采用归一化计数方式,它通过改变控制面板上的设定值M来调整筒子定长长度,定长长度:
式(1-18)中Lp为实际平均级差值,即单位设定值所对应的纱线实际卷绕长度,以标定的方法进行测算。
在纺纱生产及络筒机械本身状况比较良好稳定的条件下,间接测量原理能够保证一定的筒子定长精度,达到预定长度后络筒机即停止卷绕。
四、纱线毛羽控制
纱线毛羽是指伸出纱线基体表面的纤维,其数量、长度及其分布情况不仅对织物的外观、手感、风格和使用等有密切的关系,还将直接影响后道工序的质量和生产效率。因而,纱线毛羽作为影响织物产、质量的重要因素,受到普遍重视。
在络筒工序,由于纱线与器件接触部位多,摩擦大,退绕气圈长,对纱线毛羽的影响极大。据大量实验表明,络筒工序使毛羽增加100%~500%,随纱线品种、设定长度、设备状况等而异,且主要以3mm及以上的有害毛羽的增加率最大。国内外控制络筒纱线毛羽的方法很多,可分为两类:一类是采用机械方式,在纱线通道上安装假捻装置,通过对纱线进行假捻来控制纱线毛羽;另一类则通过在纱线通道中喷射气体,让纱线受到流体(空气和蒸汽)涡旋的作用,使突出纱体的毛羽缠绕到纱线上,以减少毛羽。
图1-32 毛羽减少装置的结构示意图
1—纱线 2—壳体 3—搓抹器 4—纱线通道 5、6—喷气孔
某专利介绍了一种毛羽减少装置,其结构如图1-32所示。
纱线1穿过直径为2mm的纱线通道4,壳体2上有两个通向纱线通道的斜向喷气孔5、6(直径为0.3mm、与管子轴线倾斜角为50°)。压缩空气经喷气孔在纱线通道中形成与纱线行进方向相反的旋转气流。在纱线通道的入口处,该旋转气流与纱线捻向相同,对纱线有退捻作用,从而降低纱线的捻度,使纱身疏松;而在纱线通道的出口处,对纱线起加捻作用,让纱线原来的捻度又得到恢复,纱身捻紧。纱线结构经过这样的疏松和捻紧,一些突出纱身的长毛羽就被旋转气流缠绕到纱线上或被捻入纱线结构内,于是纱线毛羽得到初步减少。
位于纱线通道出口处的搓抹器3由四根两两正交的搓抹棒组成。搓抹口对纱线的运动具有微弱的约束作用。在搓抹口内,做旋转向上运动的纱线受搓抹棒光滑表面的机械作用,使游离毛羽头端沿纱线捻向捻贴到纱身上,进一步提高了纱线毛羽减少效果。
络筒纱线毛羽减少装置的效果见表1-2。
表1-2 8.4tex大豆蛋白纤维纱线的络筒毛羽量对比
纱线毛羽测试条件:测试长度10m,测试速度30m/min,测试次数10次。
由表1-2可见,两种改进都取得了理想的效果,相比而言,在气室压力较高的0.245MPa的条件下,毛羽减少得更多,大多长度段的毛羽数量都减少了50%以上,其中尤以5mm为最,达61.7%。
五、上蜡
根据后工序加工的需要,有些纱线需要在络筒加工中上蜡,以减少纱线表面的毛羽,降低其表面摩擦因数40%~50%,譬如部分用于针织工程的纱线。上蜡方法为:在纱线通道上设置蜡辊,纱线行进过程中和蜡辊接触,完成上蜡。蜡辊以一定的速度作主动回转,改变其回转速度可以调节上蜡量。上蜡量和后加工要求、纱线的材料与品种等因素有关。最佳的上蜡量为0.8~2.2g蜡/kg纱。