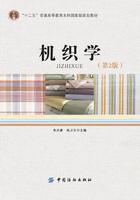
第四节 整经工艺与产量及质量控制
一、整经的工艺设计原理
(一)分批整经
分批整经工艺设计的主要内容为整经张力、整经速度、整经根数、整经长度、整经卷绕密度等项内容。
1.整经张力 整经张力与纤维材料、纱线线密度、整经速度、筒子尺寸、筒子架形式、筒子分布位置及伸缩筘穿法等因素有关。工艺设计应尽量保证单纱张力适度、片纱张力均匀。
整经张力通过张力装置工艺参数(张力圈重量、弹簧加压压力、摩擦包围角等)以及伸缩筘穿法来调节。工艺设计的合理程度可以通过单纱张力仪测定来衡量。
在配有张力架的整经机上,还需调节传感器位置、片纱张力设定电位和导辊相对位置等。
2.整经速度 整经速度可在整经机的速度范围内任意选择,一般情况下,随着整经速度的提高,纱线断头将会增加,影响整经效率。若断头率过高,整经机的高速度就失去意义。高速整经条件下,整经断头率与纱线的纤维种类、原纱线密度、原纱质量、筒子卷装质量有着十分密切的关系,只有在纱线品质优良和筒子卷绕成形良好和无结纱时,才能充分发挥高速整经的效率。
新型高速整经机使用自动络筒机生产的筒子时,整经速度一般选用600m/min以上;滚筒摩擦传动的1452A型整经机的整经速度为200~300m/min。整经轴幅宽大,纱线质量差,纱线强力低,筒子成形差时,速度可设计稍低一些。
3.整经根数 整经轴上纱线排列过稀会使卷装表面不平整,从而使片纱张力不匀。因此,整经根数的确定以尽可能多头少轴为原则,根据织物总经根数和筒子架最大容量,计算出一批经轴的最少只数,然后再分配每只经轴的整经根数。为便于管理,各轴整经根数要尽量相等或接近相等。
整经轴盘片间距为1384mm时,棉纱的整经根数如表2-1所示。其他纤维的整经根数可参考此表。
表2-1 棉纱分批整经根数
一次并轴的轴数与整经根数的关系为:
式中:n—— 一次并轴的轴数;
M——织物总经根数;
Z——各轴整经根数的平均值。
4.整经长度 整经长度的设定依据是经轴的最大容纱量,即经轴的最大绕纱长度。经轴最大绕纱长度可由经轴最大卷绕体积、卷绕密度、纱线线密度和整经根数求得。整经长度应略小于经轴的最大绕纱长度,并为织轴上经纱长度的整数倍,同时还要计及浆纱的回丝长度以及浆纱伸长率。
5.卷绕密度 经轴卷绕密度的大小影响到原纱的弹性、经轴的最大绕纱长度和后道工序的退绕顺畅。经轴卷绕密度可由对经轴表面施压的压纱辊的加压大小来调节,同时还受到纱线线密度、纱线张力、卷绕速度的影响。卷绕密度的大小应根据纤维种类、纱线线密度等合理选择。表2-2为经轴卷绕密度的参考数值。
表2-2 分批整经经轴卷绕密度
(二)分条整经
分条整经工艺设计除包括整经张力、整经速度、整经长度的设计外,还有整经条数、定幅筘计算和斜度板锥角计算等内容。
1.整经张力 分条整经的整经张力设计分滚筒卷绕和织轴卷绕两个部分。
滚筒卷绕时,张力装置工艺参数及伸缩筘穿法的设计原则可参照分批整经。
织轴卷绕的片纱张力取决于制动带对滚筒的摩擦制动程度,片纱张力应均匀、适度,以保证织轴卷装达到合理的卷绕密度。织轴的卷绕密度可参见表2-3。倒轴时,随大滚筒退绕半径减小,摩擦制动力矩也应随之减小,为此制动带的松紧程度要做相应调整,保持片纱张力均衡一致。
表2-3 分条整经经轴卷绕密度
2.整经速度 受换条、再卷等工作的影响,分条整经机的机械效率与分批整经机相比是很低的。据统计,分条整经机整经速度(大滚筒线速度)提高25%,生产效率也仅仅增加5%,因此,它的整经速度提高就显得不如分批整经那么重要。
新型分条整经机的设计最高速度为800m/min,实际使用时则远低于这一水平,一般为300~500m/min。纱线强力低、筒子质量差时应选用较低的整经速度。
3.整经条数 在条格及隐条织物生产中,整经条数n为:
式中:M——织轴总经根数;
Mb——两侧边纱根数总和;
Mt——每条经纱根数。
每条经纱根数系每条所经的花数与每花配色循环数之积。第一和最后条带的经纱根数还需修正:加上各自一侧的边纱根数;对应n取整数后多余或不足的根数做加减调整。
在素经织物生产中,整经条数n为:
当无法除尽时,应尽量使最后一条(或几条)的经纱根数少于前面几条,但相差不宜过大。
4.整经条宽 整经条宽即定幅筘中所穿经纱的幅宽,整经条宽B为:
式中:B0——织轴幅宽;
k——条带扩散率。
条带经定幅筘后发生扩散。高经密的品种在整经时条带的扩散现象较严重,造成滚筒上纱层呈瓦楞状,为减少扩散现象,可将定幅筘尽量靠近整经滚筒表面,减小条带扩散。
5.定幅筘计算 定幅筘的筘齿密度N为:
式中:C——每筘齿穿入经纱根数。
每筘齿穿入经纱根数一般为4~6根或4~10根,以大滚筒上纱线排列整齐、筘齿不损伤纱线为原则。
6.条带长度 条带长度(整经长度)L为:
式中:l——成布规定匹长,系公称匹长与加放长度之和;
mp——织轴卷绕匹数;
aj——经纱缩率;
hs——织机的上机回丝长度;
hl——织机的了机回丝长度。
二、整经的产量和质量
(一)整经的产量
整经机的产量是指单位时间内整经机卷绕纱线的重量,又称台时产量,它分为理论产量G′和实际产量G。
整经时间效率除与纱线线密度、筒子卷装质量、接头、上落轴、换筒等因素有关外,还取决于纱线的纤维材料和整经方式。例如1452型整经机加工棉纱的整经时间效率(55%~65%)明显高于绢纺纱的时间效率(40%~50%)。分条整经机受分条、断头处理等工作的影响,其时间效率比分批整经机低。
1.分批整经的产量 分批整经的理论产量G′[kg/(台·h)]为:
式中:v——整经线速度,m/min;
m——整经根数;
Tt——纱线线密度,tex。
分批整经的实际产量G为:
式中:K——时间效率。
2.分条整经的产量 分条整经的理论产量G′[kg/(台·h)]为:
式中:v1——整经大滚筒线速度,m/min;
v2——织轴卷绕线速度,即倒轴线速度,m/min;
M——织轴总经根数;
n——整经条数。
分条整经的实际产量G为:
(二)整经的质量
整经质量包括卷装中纱线质量和纱线卷绕质量两个方面,整经的质量对后道加工工序影响很大,因此抓好整经质量是提高织物质量和织造生产效率的关键。
1.纱线质量 纱线经过整经加工后,在张力的作用下发生伸长,其细度、强力和断裂伸长均有减小趋势。为保持纱线原有的物理机械性能,整经时纱线所受张力要适度,纱线通道要光洁,尽量减少纱线的磨损和伸长。
纱线从固定的筒子上退绕下来,其捻度会有些改变。筒子退绕一圈,纱线上就会增加(Z捻纱)或减少(S捻纱)一个捻回。随着筒子退绕直径减小,纱线的捻度变化速度加快。
研究表明:在正常生产情况下,整经后纱线的物理机械性能无明显改变。
2.纱线卷绕质量 良好的纱线卷绕质量表现为整经轴(或织轴)表面圆整,形状正确,纱线排列平行有序,片纱张力均匀适宜,接头良好,无油污及飞花夹入。卷绕不良所造成的整经疵点有以下几种。
(1)长短码。测长装置失灵和操作失误所造成的各整经轴绕纱长度不一的疵点。在分条整经中指的是各整经条带长度不一致。长短码疵点增加了浆纱或织造的了机回丝。
(2)张力不匀。因张力装置作用不正常或其他机械部件调节不当等原因所引起的整经疵点。整经加工所造成的纱线张力不匀在浆纱过程中不可能被消除,遗留到织机上会产生开口不清、飞梭、织疵等一系列弊病,严重影响布面质量。在浆纱工序中,整经轴纱线张力不匀也会导致浆轴上纱线倒头、并头、绞头等疵点。
(3)绞头、倒断头。断头自停装置失灵,整经轴不及时刹车,使断头卷入以及操作工断头处理不善所造成的整经疵点,它是影响浆纱工序好轴率的主要因素。分条整经的织轴绞头、倒断头使织机开口不清,影响布机效率,增加织疵。
(4)嵌边和凸边。整经轴或织轴的边盘与轴管不垂直,伸缩筘左右位置调整不当,或分条整经机倒轴时对位不准,都容易引起整经轴或织轴的嵌边和凸边疵点。在后道浆纱并轴时造成边纱浪纱,织造时形成豁边坏布。
由于操作不善,清洁工作不良,还会引起错特、杂物卷入、油污、滚绞、并绞、纱线排列错乱等各种整经疵点,对后加工工序产生不利影响,降低布面质量。
三、提高整经产量及质量的技术措施
(一)分批整经的技术措施
1.高速、大卷装 新型高速整经机的最高整经速度达1100m/min。随着织机幅宽的增加,整经机的幅宽也相应增加,幅宽可达2.4m,特殊规格可达2.8m。整经轴边盘直径为800~1200mm。
2.完善的纱线品质保护 取消滚筒摩擦传动,采用直流变速电动机或变量液压电动机直接拖动整经轴,保持纱线恒线速、恒张力卷绕,并以压辊加压控制整经轴的卷绕密度。既得到均匀的卷绕密度,又大大减少了纱线的摩擦损伤,从而减少了纱线毛羽,使纱线的原有品质得到保护。
3.均匀的纱线整经张力 采用单式筒子架,实行筒子架集体换筒,提高了片纱张力均匀程度。为缩短换筒工作停台时间,使用了高效率的机械装置或自动装置。
应用双张力盘式、压辊式、电子式张力装置,减小纱线的张力波动和各纱线之间的张力差异。电子式张力装置还具有自动调整整经张力的功能。
4.均匀的纱线排列 伸缩筘做水平和垂直方向的往复移动,引导纱线均匀排列,保证整经轴表面圆整。
5.减少整经疵点 采用高效的整经轴、压辊、导纱轴同步制动,减少断头卷入整经轴所产生的倒断头疵点。制动方式有液压式、气压式和电磁离合器式。液压制动系统的制动力大,制动效果好,在纱线卷绕直径达800mm、卷绕速度1000m/min条件下,制动距离仅为4m。不过液压系统加工要求高,工作油的泄漏会污染纱线和工作环境。气压制动虽不引起污染,但制动效果略逊,并需配备压缩空气系统。
部分整经机还备有倒纱装置,倒纱长度达10m,对减少倒断头疵点更为有利。
6.良好的劳动保护 整经机上装有光电式或其他形式的安全装置,当人体接近高速运行区域时,立刻发动关车,以免发生人身和机械事故。部分整经机装有车头挡风板,保护操作人员免受带有纤维尘屑的气流干扰。
7.集中方便的调节和显示 整经机主要工艺参数的调节、产量的显示、机械状态指示以及各项操作按钮均集中安装在操作方便的位置,利于管理。
8.改善纱线质量,提高纱线的可织性 可织性是纱线能顺利通过织机加工而不致起毛、断头的性能。在分批整经和分条整经的新技术中,都反映出改善纱线原有质量,提高纱线可织性的发展趋向。
在部分长丝分批整经机上装有毛丝检测装置和静电消除装置。静电消除装置利用尖端放电原理。由高压发生器获得的高压,经高压电缆送到电极管针尖上,使针尖周围空气电离所产生的正负离子与纱线上所积累的负的或正的静电荷中和,从而达到消除静电的目的。去除毛丝、消除静电是提高无捻长丝可织性的重要技术措施。
(二)分条整经的技术措施
分条整经的技术措施除与分批整经相同外,还有以下方面。
1.高速、阔幅、通用性强 分条整经机滚筒卷绕速度可达800~900m/min,幅宽可达3.5m,适用于各种纱线加工,如细特纱或粗特纱、天然或人造纤维长丝(包括无捻长丝、玻璃纤维、加弹涤纶丝等)。
2.良好的卷绕成形 新型分条整经机上,定幅筘到滚筒卷绕点之间距离很短,即自由纱段长度很短,这有利于纱线条带被准确引导到滚筒表面,同时也减少了条带的扩散程度,使条带卷绕成形良好。
采用定幅筘自动退移装置。随滚筒卷绕直径增加,定幅筘逐渐退移,自由纱段长度维持不变,于是条带的卷绕情况、条带扩散程度不变,条带各层纱圈卷绕正确一致。
滚筒具有固定的锥角和无级变化的定幅筘移动速度,保证纱线条带截面形状正确,而且条带纱圈获得最佳稳定性。现代分条整经机上配备编有程序的计算器,可以方便地根据有关参数计算定幅筘移动速度。
织轴卷绕采用加压装置,使卷绕密度增加,卷绕成形良好,而且减少纱线弹性损失。
3.高效生产 两台整经机合用一个筒子架,轮流整经和倒轴,节省占地面积,提高生产效率。
采用可搬动的滚筒结构,整经后将滚筒移到专门的倒轴机构上进行织轴卷绕,提高整经机生产效率。
本章主要专业术语
整经(warping)
分批整经(batch warping)
轴经整经(beam warping)
分条整经(sectional warping and beaming)
筒子架(creel)
伸缩筘(extensible reed)
整经轴(warp beam)
倒轴(beaming)
退绕张力(unwinding tension)
张力圈(tension washer)
恒线速(constant line speed)
恒张力(constant tension)
恒功率(constant power)
分绞(warp separating)
分绞筘(separating reed)
静电消除装置(static eliminator)
电气接触式自停装置(contact electric auto-stop device)
光电式电子自停装置(photo-electric auto-stop device)