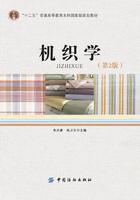
第三节 整经卷绕
一、分批整经卷绕
分批整经时,片纱密度较稀(一般为4~6根/cm),为使经轴成形良好,分批整经按一很小的卷绕角卷绕,接近于平行卷绕方式,对卷绕过程的要求是整经张力和卷绕密度均匀、适宜,卷绕成形良好。
分批整经机上伸缩筘左右往复移动,引导纱线平行地均布在整经轴表面,并且互不嵌入,以便于退绕。根据纱线直径及纱线排列密度,伸缩筘动程在0~40mm范围内调整。在伸缩筘到导纱辊以及导纱辊到整经轴卷绕点之间存在着自由纱段,因为自由纱段的作用,整经轴上每根纱线卷绕点的左右往复动程远小于伸缩筘动程,一般可达2~5mm。部分分批整经机在结构设计上做了改进,缩短了自由纱段长度,使伸缩筘往复运动的导纱功效准确地传递到整经轴上,提高了经纱排列的均匀性。
为保持整经张力恒定不变,整经轴必须以恒定的表面线速度回转,于是随整经轴卷绕半径增加,其回转角速度逐渐减小,然而整经卷绕功率恒定不变。因此,整经卷绕过程具有恒线速、恒张力、恒功率的特点。
(一)整经轴的卷绕
1.摩擦传动的整经轴卷绕 如图2-20所示,交流电动机4通过传动带传动滚筒1恒速转动,整经轴2搁在导轨上,受水平压力F的作用紧压在滚筒表面,接受滚筒的摩擦传动,由于滚筒的表面线速度恒定,所以整经轴亦以恒定的线速度卷绕经纱3,达到恒张力卷绕目的。这种传动系统简单可靠、维修方便,但亦存在制动过程经轴表面与滚筒之间的滑移造成的纱线磨损,断头关车不及时等弊病,随着整经速度提高,情况进一步恶化,因此高速整经机不采用这种传动方式。
图2-20 经轴摩擦传动方式
2.直接传动的整经轴卷绕 这是目前高速整经机普遍采用的传动方式。这种整经机的经轴两端为内圆锥齿轮,它工作时与两端的外圆锥齿轮啮合,接受传动。采用经轴直接传动后,随经轴卷装直径逐渐增加,为保持整经恒线速度,经轴转速应逐渐降低,这种对经轴的调速传动可以采用三种方式。
(1)调速直流电动机传动。直流电动机直接传动整经轴卷绕纱线,压辊紧压在整经轴表面,施加压力,并将纱线速度信号传递给测速发电机。机构采用间接法恒张力控制,它以纱线的线速度为负反馈量,通过控制线速度恒定来间接地实现恒张力的目的。
(2)变量液压电动机传动。纱线经导纱辊卷入由变量液压电动机直接传动的整经轴,在电动机的拖动下,变量油泵向变量液压电动机供油,驱动其回转。串联油泵将高压控制油供给变量油泵和变量液压电动机,控制它们的油缸摆角,以改变液压电动机的转速。
(3)变频调速传动。由交流电动机传动整经轴卷绕纱线,根据所设计的整经线速度,由电位器设定一个模拟量,实际的整经线速度经测速发电机测出作为反馈取出一个模拟量,经过A/D转换、PLC运算后输出一个模拟调节量,送入FVR变频器,从而控制交流电动机速度。随着经轴直径的增大,线速度反馈量随之增大,经过PLC运算后送入FVR,控制电动机速度不断下降,使整个整经过程中线速度保持恒定,传动系统如图2-21所示。由于变频调速系统具有调速精度高、响应快、性能可靠等特点,目前高速整经机普遍采用变频调速传动方式。
图2-21 采用变频调速电动机的经轴直接传动方式
(二)对经轴的加压
整经加压是为了保证卷绕密度的均匀、适度,保证卷装成形良好。加压方式有机械式、液压式和气动式。
图2-22 机械式水平加压
1.机械式 整经机的机械式水平加压机构如图2-22所示。整经轴1安放在轴承滑座2上,滑座可沿滑轨3前后移动。齿杆4的一端装在滑座中,另一端与齿轮5啮合。重锤7通过绳轮6使齿轮5顺时针方向回转,并带动齿杆将整经轴紧靠在滚筒8上。整经过程中,随整经轴卷绕半径不断增大,卷绕加压压力N基本不变,这种加压装置亦为恒压加压装置,加压压力由重锤调节。
2.液压式 液压式压辊加压机构如图2-23所示。自重为P的压辊1对整经轴2施加压力N′,压辊装在压辊臂3上,绕O点转动,压辊臂的另一端A上装有拉力弹簧,弹簧拉力F对O的力矩用以平衡压辊对O的重力矩,在压辊臂上还施加着由压辊加压油缸和制动器所产生的恒定力矩M。以压辊臂为脱离体,如图2-24所示,根据对O点的力矩平衡方程可得:
式中,l1、l2、l3分别表示压辊臂回转轴心O到压力N、重力P、弹簧力F作用线的距离,其中l2、l3以逆时针方向的力矩所对应的力臂为正。通过机构的参数合理选择,使整经过程中N数值几乎不变,这种加压装置为恒压力加压装置。为适应不同品种纱线的卷绕,可调节加压油缸中工作油的压力,使力矩M变化,从而改变加压压力。
图2-23 液压式加压机构1—压辊 2—整经轴 3—压辊臂
图2-24 压辊臂受力图
(三)三辊同步制动
分批整经的线速度很高,新型分批整经机的设计速度普遍达到1000m/min,为使发生经纱断头后能迅速制停,不使断头卷入经轴,分批整经机上配备高效的液动或气动制动系统。为了防止制动过程中测速辊、压辊与经纱发生滑移造成测长误差和经纱磨损,在高速整经机上普遍采用测速辊、压辊和经轴三者同步制动,其中压辊在制动开始时迅速脱离经轴并制动,待经轴和压辊均制停后压辊再压靠在经轴表面。
二、分条整经卷绕
分条整经机的卷绕由大滚筒卷绕和倒轴两部分组成。新型分条整经机的卷绕一般有两种形式,即直流电动机可控硅调速和变频调速,都可达到整经恒线速的目的。
(一)大滚筒卷绕
分条整经机的整经大滚筒如图2-25所示,由呈一体的一长圆柱体和一圆台体构成,首条经纱a是贴靠在圆台体表面卷绕的。对于纱线表面光滑的品种,圆台体的锥角应小些,有利于经纱条带在大滚筒上的稳定性,但大滚筒总长度变长,即机器尺寸增加。在条带的导条速度分档变化的整经机上,圆台体部分为框式多边形结构,圆台体的锥角可调,这可达到导条速度与锥角之间的匹配,使条带精确成形,但框式多边形结构的圆台部分会导致首条经纱卷绕时因多边形与圆形周长之间误差出现的卷绕长度差异,所以在新型分条整经机上普遍采用固定锥角的圆台体结构,锥角有9.5°、14°等系列,根据加工对象进行选型。
图2-25 分条整经大滚筒
分条整经的卷绕由大滚筒的卷绕运动(大滚筒圆周的切线方向)和导条运动(平行于大滚筒轴线方向)组成,大滚筒卷绕运动类似于分批整经机的经轴卷绕,大滚筒也由独立的变频调速电动机传动,整经线速度由测速辊检测,在每一条带开始卷绕时,大滚筒转速最高,随着卷绕直径增加,测速信号通过变频调速控制部分使大滚筒传动电动机转速降低,实现大滚筒卷绕的恒线速。大滚筒装有高效的制动装置,一旦发生经纱断头,立即动作,能保证断头未被卷入大滚筒之前停车。
(二)导条
第一条带的纱圈由滚筒头端的圆台体表面为依托,以免纱圈倒塌。在卷绕过程中,条带依靠定幅筘的横移引导,向圆台方向均匀移动,纱线以螺旋线状卷绕在滚筒上,条带的截面呈平行四边形,如图2-26所示。以后逐条卷绕的条带都以前一条带的圆台形头端为依托,全部条带卷绕之后,卷装呈良好的圆柱形状,纱线的排列整齐有序。
图2-26 分条整经大滚筒上的经纱条带
由于导条运动是定幅筘和大滚筒之间在横向所做的相对移动,因此其相对运动方式有两种:一种是大滚筒不做横向运动,在整经卷绕时由定幅筘做横向移动将纱线导引到大滚筒上,而在倒轴时倒轴装置做反向的横向移动,始终保持织轴与大滚筒上经纱片的对准,将大滚筒上的经纱退绕到织轴上;另一种方式定幅筘和倒轴装置不做横向运动,在整经卷绕时由大滚筒做横向移动,使纱线沿着大滚筒上的圆台稳定地卷绕,而在倒轴时大滚筒再做反向的横向移动,保持大滚筒上经纱片与织轴对准,将大滚筒上的经纱退绕到织轴上。由于第一种方式定幅筘做横移,为保持筒子架经纱与定幅筘对准,筒子架及分绞筘均需做横移,使得移动部件多,机构复杂,因此新型分条整经机大都采用大滚筒横移的导条运动方式。
导条速度用大滚筒每转一转条带的横移量表示。在固定圆台体锥度的情况下,条带的横移量取决于大滚筒每转一转纱层厚度的增量,圆台体锥度α、每层纱厚度b与条带横移量h三者的关系为:
图2-27 一种新型分条整经机的定幅筘底座
由于圆台体锥度α已知,上机时只要工艺设计的纱层厚度值b与实际情况一致,那么由式(2-4)确定的h值能保证条带成形良好。为了保证纱层厚度值设定正确,一些新型分条整经机在定幅筘底座上有纱层厚度自动测量装置,如图2-27所示,在底座5上装有定幅筘1、测长辊2、测厚辊3、导纱辊4等部件。测厚辊的工作过程是在条带生头后,将测厚辊紧靠在大滚筒6表面上,传感器检测其初始位置,随着大滚筒绕纱层增加,测厚辊便随之后退,传感器将后退距离转换成电信号,输入计算机并显示出来,一般取大滚筒100圈为测量基准,测量的厚度值被自动运算,得到精度达0.001mm的横移量,控制部分按这个横移量使大滚筒和定幅筘底座做导条运动,实现条带的卷绕成形。测长辊2的一端装有一个测速发电机,将纱速信号和绕纱长度信号送到滚筒传动电动机的控制部分和定长控制装置。导纱辊4的作用是增大纱线在测长辊上的包围角,以减少滑移,提高测长精度。
定幅筘底座装在大滚筒机架上,整经过程中当大滚筒相对筒子架做横移进行条带卷绕成形时,定幅筘底座需做反向的横移,从而保证定幅筘与分绞筘、筒子架的直线对准位置不变,这由一套传动及其控制系统自动完成,并能实现首条定位、自动对条等功能。首条定位可使定幅筘底座与大滚筒处于起步位置,即经纱条带靠近圆台体一侧的边纱与圆台体的起点准确对齐。自动对条是控制部分的计算机根据输入的条带宽度,在进行换条操作时,使定幅筘底座相对于大滚筒自动横移到下一个条带的起始位置,其精度可达0.1mm,对条精确,提高了大滚筒卷装表面的平整,消除带沟和叠卷现象,也缩短了换条操作时间。
(三)分绞
为使织轴上的经纱排列有条不紊,保持穿经工作顺利进行,要进行分绞工作。分绞工作借助于分绞筘完成,分绞原理如图2-28所示。条带的纱线依次引过筘眼1和封点筘眼2,筘眼1与封点筘眼2间隔排列。筘眼1不焊接,封点筘眼2在中部有两个焊封点,纱线在筘眼1中可上下较大幅度移动,但在封点筘眼2中移动受两个焊封点约束。分绞时,先将分绞筘压下,筘眼1中的纱线不动,留在上方,而封点筘眼2中纱线随之下降,于是奇偶数两组纱线被分为上下两层,在两层之间引入一根分绞线3,如图2-28(a)所示。然后,把分绞筘上抬,筘眼1中的纱线不动,留在下方,而封点筘眼2中纱线随之上升,于是奇偶数两组纱线被分为下上两层,在两层之间再引入一根分绞线,如图2-28(b)所示。这样相邻经纱被严格分开,次序固定。
图2-28 分绞筘及其分绞
分绞筘内穿纱的多少视织物品种而异。一般每眼穿一根,如逢方平或纬重平组织时,每眼可穿两根。
(四)倒轴卷绕
滚筒上各条带卷绕之后,要进行倒轴工作,把各条带的纱线同时以适当的张力再卷到织轴上。倒轴卷绕由专门的织轴传动装置完成,在新型高速整经机上,它也是一套变频调速系统,控制织轴恒线速卷绕。倒轴过程中,大滚筒做与整经卷绕时反方向的横移,保持退绕的片纱始终与织轴对准。
倒轴卷绕张力的产生借助于大滚筒的制动器,制动器为液压或气压方式,在倒轴时,根据所需经纱张力,调节液(气)压压力,制动器便对与大滚筒一体的制动盘施加一定的摩擦阻力,从而产生倒轴卷绕张力,使织轴成形良好,并达到一定的卷绕密度。
(五)对织轴的加压
新型的分条整经机上采用织轴卷绕加压装置,利用卷绕时纱线张力和卷绕加压压力两个因素来达到一定的织轴卷绕密度,所以能用较低的纱线张力来获得较大的卷绕密度,既保持了纱线良好的弹性,又大大增加卷装中的纱线容量。加压装置的工作原理如图2-29所示。液压工作油进入加压油缸1,将活塞上抬,使托臂2升起,压辊3被紧压在织轴4上。工作油压力恒定,于是卷绕加压压力也维持不变,这是一种恒压加压方式。不同的织轴卷绕密度通过工作油压力来调节。
部分分条整经机上不装织轴卷绕加压装置,织轴卷绕时,为达到一定的织轴卷绕密度,必须维持一定的纱线卷绕张力,纱线张力大小取决于整经滚筒上制动带的拉紧程度,制动带越紧,拖动滚筒转动的力就越大,从而纱线张力和织轴卷绕密度也大。这种机构对保持纱线的弹性和强力不利。
(六)经纱上乳化液
毛织生产中,为提高经纱的织造工艺性能,在分条整经织轴卷绕(倒轴)时,对毛纱上乳化液(包括乳化油、乳化蜡或合成浆料)。经纱上乳化油(蜡)后,可在纱线表面形成油膜,降低纱线摩擦因数,使织机上开口清晰,有利于经纱顺利通过经停片、综、筘,从而减少断经和织疵。对经纱上合成浆料乳化液,在纱线表面形成浆膜,则更有利于经纱韧性和耐磨性的提高,在一定程度上起到了上浆作用。
上乳化液的方法有多种,比较常用的方法如图2-30所示。经纱从滚筒1上退绕下来,通过导辊2、3后,由带液辊4给经纱单面上乳化液,然后经导辊5卷绕到织轴6上。带液辊以一定速度在液槽7中转动,液槽的液面高度和温度应当恒定,调节带液辊转速可以控制上液量,一般上液量为经纱重量2%~6%。
图2-29 分条整经机织轴卷绕加压
图2-30 常用的经纱上乳化液方法
乳化液成分主要有白油、白蜡、油酸、聚丙烯酰胺、防腐剂和其他一些助剂。经纱上乳化液后,其织造效果有明显改观。毛纱上聚丙烯酰胺乳化液,可提高断裂伸长率10%~30%,提高断裂强度约4%~5%,使织造经向断头率降低20%~40%。上乳化油或乳化蜡后,断经、脱节和织疵均有减少,经向断头率降低10%~30%。