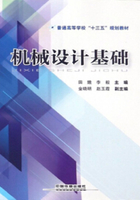
4.4 凸轮机构的设计
在凸轮机构的设计过程中,当根据工作条件的要求,选定了凸轮机构的形式、凸轮转向、凸轮的基圆半径和从动件的运动规律后,就可以进行凸轮轮廓曲线的设计。凸轮轮廓曲线的设计方法有图解法和解析法。图解法简便易行,比较直观,但设计精度较低,一般适用于低速或对从动件的运动规律要求不太严格的凸轮机构设计。解析法设计精度较高,常用于运动精度较高的凸轮(如仪表中的凸轮或高速凸轮等)设计,由于其计算工作量较大,适宜在计算机上计算。但这两种设计方法的基本原理是相同的,本节仅讨论图解法。
4.4.1 凸轮机构类型的确定
设计凸轮机构时,要根据凸轮机构在机器传动链中的位置、作用和所要完成的动作及其过程,确定凸轮机构的类型。例如确定采用摆动从动件还是直动从动件;采用对心从动件还是偏心从动件;采用滚子从动件还是平底从动件;采用盘形凸轮还是圆柱凸轮等。
4.4.2 从动件运动规律的选择
凸轮机构的类型确定后,还需要选择从动件的运动规律,再根据凸轮的(角)位移升程转角等参数写出运动方程(对于解析法设计凸轮轮廓),或绘制从动件的位移线图(对于图解法设计凸轮轮廓),就可以设计凸轮的轮廓曲线了。
凸轮的轮廓曲线完全取决于从动件的位移运动规律。图解法设计凸轮轮廓所使用的位移线图由凸轮的(角)位移与从动件的(角)位移的对应点及其对应点之间的过渡曲线所组成。对应点是根据凸轮机构的功能要求所确定的,而过渡曲线的形式首先应满足凸轮机构的功能要求。若凸轮机构的功能对过渡曲线的形式无特殊要求,则应根据动力特性和加工工艺特性等条件选择上节所介绍的从动件位移规律作为过渡曲线。
4.4.3 图解法设计凸轮轮廓曲线
传统的凸轮轮廓曲线是采用图解法进行设计的,凸轮轮廓曲线设计所采用的基本方法是虚拟的反转法。
以图4.9所示的尖底对心移动从动件盘形凸轮机构为例,若凸轮的角速度为ω,则假想给整个凸轮机构加上一个与凸轮的角速度大小相等、方向相反的绕凸轮转动中心的虚拟角速度-ω,使之成为虚拟的凸轮机构。此时凸轮与从动件之间的相对运动关系不会改变。但虚拟的凸轮则成为静止不动的构件,而虚拟的从动件一边随着导路以-ω的角速度绕凸轮转动中心线回转,一边又按预期的从动件运动线图在导路中作相对移动。

图4.9 反转法原理
由于从动件的尖底始终与凸轮轮廓线相接触,所以虚拟凸轮机构反转一圈后,从动件尖底的运动轨迹就是实际的凸轮轮廓曲线。
这种将凸轮看成是静止不动,而将导路与原来往复移动的从动件看成是反转运动的方法称为虚拟反转法。该方法是图解法绘制凸轮轮廓曲线的基本方法。
1.移动尖底从动件盘形凸轮轮廓绘制
(1)对心移动尖底从动件盘形凸轮轮廓绘制 对心移动指移动从动件的轴线通过凸轮的转动中心。
绘制该凸轮轮廓曲线之前,要先按与凸轮相同的比例绘制出从动件的位移线图(见图4.10b),并确定凸轮的基圆半径rb。

图4.10 绘制对心移动尖底从动件盘形凸轮轮廓
凸轮以等角速度按顺时针方向转动,对心移动尖底从动件盘形凸轮的轮廓的设计步骤如下:
①取长度比例尺μl和角度比例尺μφ,作从动件的位移线图S=S(φ)(见图4.10b);
②将位移线图的升程转角φ0=180°和回程角φ2=90°分为若干等份,通过各点作纵坐标S轴的平行线与位移曲线相交,即得相应凸轮各转角时从动件的位移量11′、22′…;
③取同样长度比例尺μl,以O为圆心、OB0=rb/μl为半径画基圆。此基圆与从动件导路中心线的交点B0即为从动件尖底的起始位置;
④在图4.10a中,自OB0沿-ω的方向,根据位移图中各运动角的前后顺序分别作角度φ0=180°、φ1=30°、φ2=90°和φ3=60°,并将它们分成与图4.10b对应的若干等分,得OC1、OC2、OC3…点。连接并延长OC1、OC2、OC3…,它们便是反转以后从动件导路中心线的各个位置;
⑤在位移线图中量取各位移量,并取B1C1=11′、B2C2=22′、B3C3=33′…,得反转后从动件尖底的一系列位置B1、B2、B3…;
⑥将B0、B1、B2…各点连成光滑曲线,即得所要求的凸轮轮廓曲线。
(2)偏置移动尖底从动件盘形凸轮轮廓绘制 偏置指移动从动件的轴线不通过凸轮的转动中心。转动中心到从动件的轴线的距离称为偏心距e。
绘制该凸轮轮廓曲线之前,同样要先按与凸轮相同的比例绘制出从动件的位移线图,并确定凸轮的基圆半径rb。下面仍以图4.10b所示的位移曲线为偏置移动尖底从动件盘形凸轮的位移曲线,介绍绘制其轮廓线的步骤。
如图4.11所示,设凸轮仍以等角速度按顺时针方向转动,凸轮从动件的偏置方向在凸轮轴线的左边。
①取长度比例尺μl,以O为圆心、OB0=rb/μl为半径画基圆;
②以O为圆心,以e/μl为半径画偏心圆;
③过B0点作与偏心圆相切的直线;
④将升程转角和回程转角分成与其位移曲线图相同的等分;每隔一等分,逆时针作一条与偏心圆相切的直线,这些直线分别与凸轮的基圆相交。
⑤在位移线图中(见图4.10b)量取各位移量,并取…,可得到反转后偏置尖底从动件的一系列位置B1、B2、B3…;
⑥将B0、B1、B2…各点连成光滑曲线,即得所要求的凸轮轮廓曲线。

图4.11 偏置移动尖底从动件盘形凸轮轮廓绘制
2.对心移动滚子从动件盘形凸轮轮廓的绘制
对心移动滚子从动件盘形凸轮轮廓的绘制方法,与对心移动尖底从动件盘形凸轮的绘制方法基本相同。如图4.12所示,将滚子中心视为尖底从动件的尖点,按上述方法求出的凸轮轮廓η称为凸轮的理论轮廓。然后以η上各点为圆心,以从动件的滚子的半径rT/μl为半径画一系列滚子圆,则此圆族的内包络线η′(对于凹槽凸轮还应作外包络线η″),即为凸轮与滚子从动件直接接触的轮廓,该轮廓称为凸轮的实际轮廓,或称凸轮的工作轮廓。相应的η称为凸轮的理论轮廓。由以上作图过程可知,以凸轮的转动中心为圆心,以凸轮理论轮廓的最小向径为半径所作的圆,称为凸轮的理论轮廓的基圆。所以,对于对心移动滚子从动件盘形凸轮,图中的rb是指凸轮理论轮廓的基圆半径。
偏置移动滚子从动件盘形凸轮轮廓的绘制方法,与偏置移动尖底从动件盘形凸轮的绘制方法基本相同,只是将其绘制的凸轮轮廓线作为理论廓线,然后再以理论廓线的各点为圆心,绘制一簇与滚子半径相同的圆,这些圆的内包络线即为该凸轮的实际轮廓线。
3.对心移动平底从动件盘形凸轮轮廓的绘制
绘制平底移动从动件盘形凸轮轮廓的方法与上述方法相似。如图4.13所示,首先按照尖底从动件盘形凸轮的设计方法求出从动件的各尖点B1、B2、B3…,将各点作为从动件导路中心线与平底的交点,然后过B1、B2、B3…作一系列表示平底位置的直线,此直线族的包络线即为该凸轮的实际轮廓线。由于从动件的平底与凸轮实际轮廓的切点是随机构位置而变化的,所以为了保证在所有位置上平底都能与轮廓相切,从动件的平底左右两侧的长度必须分别大于导路至左右最远切点的距离。

图4.12 绘制对心移动滚子从动件盘形凸轮轮廓

图4.13 绘制平底移动从动件盘形凸轮轮廓
其他凸轮机构中凸轮轮廓线的绘制原理与方法,请查阅凸轮设计手册。
4.4.4 凸轮机构的压力角及其许用值
设计凸轮时,要考虑凸轮与从动件之间的作用力与反作用力问题。图4.14所示为对心移动尖底从动件盘形凸轮机构在推程中的受力情况。不考虑摩擦时,Q为作用在从动件上的载荷,其中包括工作阻力、重力、弹簧力和惯性力等。F为凸轮作用于从动件的法向力,该力沿着接触点A处的公法线n—n方向。

图4.14 凸轮机构的压力角
根据工程力学的定义,从动件受力方向与其运动方向间所夹的锐角α称为凸轮机构的压力角。压力角是凸轮机构设计中的一个重要参数。在凸轮转动过程中,从动件与凸轮轮廓线的接触点位置是变化的,各接触点处的公法线方向是不同的,因而凸轮对从动件的作用力F的方向也不同。所以,凸轮轮廓线上各处的压力角也不相同。
如图4.14所示,将作用力F沿平行于从动件的运动方向和垂直于从动件的运动方向分解成为两个正交的分力,各分力与法向力之间的关系为

式中 F——凸轮作用于从动件的法向力(N);
F′——方向与从动件运动方向一致的分力(N),该分力是克服载荷Q并使从动件产生运动的主动力,所以也称为有效分力;
F″——方向与从动件运动方向垂直的分力(N),该分力能够使从动件紧压在导路上,并使从动件与导路之间产生摩擦阻力,所以该力也称为有害分力;
α——凸轮机构的压力角(°)。
从式(4.5)可以看出,压力角α愈小,则有效分力F′愈大,有害分力F″愈小,机构的受力情况和工作性能也就愈好。反之压力角α愈大,则有效分力F′愈小,有害分力F″愈大,由其所产生的摩擦阻力也就愈大。当压力角α增大到某一数值时,有效分力将小于由有害分力所产生的摩擦阻力。此时,无论凸轮给从动件施加多大的作用力F,都无法使从动件运动,此时机构处于自锁状态。机构开始出现自锁现象时的压力角称为极限压力角,以αlim表示。
极限压力角的大小与多种因素有关,如运动副之间的摩擦因数、润滑条件、从动件导路的有效长度和从动件的悬臂长度等。
在机械工程中,为改善凸轮机构的受力状况、保持较高的传动效率,使机构具有良好的工作性能,规定了压力角的许用值。该许用值比极限压力角αlim小许多,根据经验和理论分析,推荐的凸轮机构的许用压力角的数值如下:

回程 [α]h=70°~80°
由于凸轮机构在回程时发生自锁的可能性比较小,一般载荷也很小,所以许用压力角可取得大一些。
4.4.5 凸轮基圆半径与压力角的关系
设计凸轮轮廓时,首先要确定凸轮的基圆半径,所以凸轮的基圆半径也是凸轮设计中的一个重要参数。显然,凸轮的基圆半径大,则凸轮机构的结构尺寸大,体积和重量也大,承载能力得到提高,反之,则凸轮机构的结构尺寸小,体积和重量也小,承载能力降低。同时凸轮基圆半径过小,还会影响到凸轮的受力状况、凸轮轮廓曲线的连续性和滚子从动件的半径等。因此,设计凸轮时,应首先根据影响凸轮基圆半径的条件之一确定基圆最小半径,再根据其他条件校核凸轮的基圆半径。
1.基圆半径与压力角的关系
当从动件的运动规律确定后,凸轮基圆半径rb的大小将直接影响到压力角α的大小。
如图4.15所示,尖底从动件与盘形凸轮在A点接触。凸轮逆时针转动,凸轮上A点的速度为v1,从动件上A点的速度为v2,从动件与凸轮在A点的相对速度为vs,根据相对运动原理,从动件与凸轮在A点的相对速度的方向平行于凸轮在A点的切线t-t。且v1、v2与vs三者构成一个速度多边形。
因为v1与v2相互垂直,所以,由速度多边形可知
v2=v1tanα=rωtanα
式中 r——凸轮上A点的向径(mm),r=rb+s;
ω——凸轮的角速度(rad/s)。
将r代入上式后,得到

式中 rb——凸轮的基圆半径(mm);
s——从动件的位移(mm)。
由式(4.6)可知,在给定凸轮角速度和从动件运动规律(位移规律、速度规律和加速度规律)之后,凸轮机构的压力角愈大,则凸轮的基圆半径愈小,反之则增大。
所以,若从减小凸轮机构体积使其结构紧凑、减轻质量方面考虑,则凸轮机构应取较大的压力角。但从改善机构的受力状况、使其具有良好工作性能、提高其传动效率方面考虑,又应取较小的压力角。
设计凸轮机构时,应根据具体情况,合理确定其许用压力角与凸轮的基圆半径。
比如对机构的体积没有严格要求时,可取较大的基圆半径,以便减小压力角,使机构具有良好的受力条件;但若要求凸轮机构的体积小、质量轻且结构紧凑,则可取较小的基圆半径,此时压力角会增大,最大压力角不得超过许用压力角。

图4.15 基圆半径与压力角的关系
一般在工程设计中,受力状况和结构紧凑两方面的要求是应兼顾的,一般的设计原则是在凸轮机构的最大压力角不超过许用压力角及满足强度和稳定性的前提下,尽量使凸轮的基圆半径最小。
设计凸轮机构,不仅要保证从动件能实现所预期的运动规律,而且还要求其传动性能良好、体积小、结构紧凑。这些要求均与滚子半径、基圆半径、压力角等因素有关。下面就来研究它们之间的关系,以便合理地确定机构各部分的尺寸,设计出质量较好的凸轮机构。
2.凸轮最小基圆半径的确定
凸轮最小基圆半径与凸轮传动的强度有关,与凸轮机构的压力角有关,与凸轮轮廓曲线的光滑连续性有关,还与凸轮机构的结构有关。因此,设计凸轮时,应首先根据有关条件,按照一定的方法确定凸轮最小基圆半径,然后再设计凸轮轮廓。
(1)根据凸轮机构结构确定凸轮最小基圆半径时,可根据凸轮轴的半径r′,参考经验公式

初步确定凸轮的最小基圆半径。
(2)根据强度确定凸轮基圆半径时,可参考有关凸轮强度计算的专著。
(3)根据凸轮机构许用压力角条件确定凸轮最小基圆半径时,可采用以下几种方法。
①图解法确定凸轮最小基圆半径。该方法的精度较低,且绘图的工作量较大。
②解析法确定凸轮最小基圆半径。该方法就是根据式4.9,将式中的压力角换成许用压力角,再解方程。这一计算过程是一个非常烦琐冗长的过程。
③诺模图法确定凸轮最小基圆半径。诺模图法实际上是根据解析法,利用计算机绘制出的,便于工程上使用的一种确定凸轮最小基圆半径的方法。
本小节只介绍确定凸轮最小基圆半径的诺模图法。
图4.16所示为几种凸轮机构从动件常用运动规律的诺模图。图中上半圆周的数字表示凸轮升程或回程的转角,下半圆周的数字表示凸轮机构的最大压力角,通过直径的水平标尺表示从动件升程h与基圆半径rb之比。

图4.16 对心移动滚子从动件盘形凸轮机构的诺模图
例4.1 已知对心移动滚子从动件盘形凸轮机构的升程按简谐运动规律运动,升程转角φ0=60°,升程许用压力角[α]=35°,从动件的行程h=20mm,试按升程许用压力角确定凸轮最小基圆半径rb。
解:根据凸轮机构的升程转角φ0=60°和升程许用压力角[α]=35°在图4.16b中找出相应的点,然后作直线连接两点。直线与诺模图水平标尺交点的值为0.64,则

从而,凸轮最小基圆半径为

4.4.6 凸轮从动件偏置方向的确定
其他条件不变的情况下,从动件偏置方向和偏心距大小的改变,可以影响到凸轮机构压力角。因此合理地选择从动件的偏置方向和偏心距的大小,可以改善凸轮机构的受力情况,使凸轮机构的压力角控制在允许的范围之内。
具体措施为:若凸轮逆时针转动,则从动件的轴线(或力的作用线)偏置于凸轮转动中心的右侧,若凸轮顺时针转动,则从动件的轴线(或力的作用线)偏置于凸轮转动中心的左侧。
上述措施可以减小凸轮机构升程压力角,增大回程压力角。但由于回程时的许用压力角比升程时的许用压力角大,故这种措施是可行的。
4.4.7 滚子半径的确定
在凸轮机构的从动件形式中,使用较多的为滚子从动件。滚子从动件与凸轮之间的摩擦为滚动摩擦,从而提高了凸轮传动的效率,延长了凸轮传动的使用寿命。故在滚子从动件凸轮机构设计中,要解决的一个重要问题就是要合理的确定滚子的半径,使凸轮的实际轮廓曲线为连续光滑的曲线,以确保凸轮机构运动的真实性和稳定性。
从滚子本身的结构设计和强度等方面考虑,将滚子半径取大些较好。因为这样有利于提高滚子的接触强度和寿命,也便于进行滚子的结构设计和安装。但是滚子半径的增大受到凸轮结构和凸轮轮廓的限制,因为滚子半径的大小对凸轮实际轮廓线的形状有直接的影响。当滚子半径过大时,将导致凸轮的实际轮廓线变形,从动件不能实现预期的运动规律。
如图4.17a所示,对于外凸的凸轮轮廓线,凸轮实际轮廓线最小曲率半径ρbmin等于凸轮的理论廓线最小曲率半径ρmin与滚子半径rG之差。
①当ρbmin大于零时,即
ρbmin=ρmin-rG>0
则凸轮实际轮廓线是连续光滑的曲线。一般应使凸轮实际轮廓线最小曲率半径ρbmin大于凸轮实际轮廓线许用曲率半径[ρb],以确保强度和减小磨损,即
ρbmin=ρmin-rG≥[ρb] (4.7)
②当ρbmin小于零时,即
ρbmin=ρmin-rG<0
则凸轮实际轮廓线在该处呈现交叉,如图4.17b所示。加工凸轮时,此处交点以外的轮廓线将被切削掉,从而无法使滚子从动件获得预期的运动规律,该现象称为凸轮机构的运动失真。
③当ρbmin等于零时,即
ρbmin=ρmin-rG=0
则凸轮实际轮廓线在该处呈现尖点,如图4.17c所示。当滚子从动件经过此处时,将产生冲击现象,凸轮也极易磨损。
对于内凹的凸轮轮廓,凸轮实际轮廓线最小曲率半径ρbmin等于凸轮的理论廓线最小曲率半径ρmin与滚子半径rG之和,即
ρbmin=ρmin+rG
故无论滚子半径的大小如何,凸轮轮廓线都是连续光滑的曲线,如图4.17d所示。因此设计凸轮时,对于内凹的凸轮轮廓,可以不必考虑凸轮的理论廓线最小曲率半径ρmin与滚子半径rG的关系。

图4.17 凸轮滚子半径与凸轮轮廓曲率半径的关系
综上所述,设计外凸的凸轮时,滚子的半径不能太大,要考虑其对凸轮轮廓线的影响,从滚子的强度考虑,滚子半径又不能取得过小。当滚子半径未指定时,可按照经验公式
rG=(0.1~0.5)rb
初步确定滚子半径。
滚子半径rG过小会给滚子结构设计带来困难。如果不能满足此要求,可适当加大凸轮的基圆半径或对从动件的运动规律进行修改。
当外凸的凸轮轮廓设计完成后,应当按照式(4.7)校核凸轮实际轮廓的最小曲率半径ρbmin。校核凸轮实际轮廓曲率半径的方法有图解法和解析法两种。图解法的精度低,但使用方便;解析法很精确,但需要计算机辅助计算。
图解法校核凸轮实际轮廓曲率半径的方法是,当绘制完成凸轮实际轮廓线后,制作一个半径为凸轮实际轮廓线许用曲率半径[ρb]的圆模版,用目测的方式将模版放在凸轮实际轮廓线曲率半径最小的位置,观察轮廓线是否满足式(4.7)的条件。若不满足,则需增大凸轮基圆半径rb或减小滚子半径rG。
在有条件的场合,解析法校核凸轮实际轮廓曲率半径的方法已经被广泛采用,本书不专门介绍。目前已经有商业化和非商业化的凸轮设计程序,读者可自行参考。