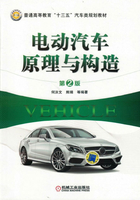
第三节 典型的纯电动汽车结构
一、改装式的纯电动汽车(福特公司纯电动汽车福克斯)
2009年6月24日,由福特汽车公司推出的福克斯纯电动汽车在英国展出。该车型是为了满足英国政府关于低碳环保车型的需求而对传统福克斯车型进行纯电动改造后推出的。
在Scottish and Southern Energy公司的支持下,首批福特福克斯纯电动汽车率先被两家能源公司购进使用和评估。从2010年开始,相关公司和大学在试点建立了相应的充电基础设施。随着试点车辆数目的增加,这款纯电动汽车带来的环保效益日渐显露出来。
基于TourneoCustom概念车和纯电动汽车(Battary Electric Vehicle,BEV)技术,福特福克斯纯电动汽车选用了最新技术水平的动力电池组——一款23kW·h的磷酸铁锂电池包。同时由一台最大90kW、245N·m的永磁电机搭配单速变速器,这套动力系统可以使该车获得最大160km的续驶里程和最高136km/h的车速。在120V电压下,它的满电充电时间需要18~20h,而240V的电源则仅需充电3~4h。除了先进的驱动系统,福克斯电动汽车还拥有能量再生制动系统、与汽车互联的手机APP等先进技术。
独特的远程控制功能也值得一提,用户智能手机上下载控制程序之后就可以随时对车辆进行远程控制:可以通过手机直接查看汽车的充电状态和电容量、充电完成自动提醒;可以直接下载车辆的工作状态,然后远程发送给福特公司,从而判断车辆的故障问题;此外,还可以远程起动和解锁车辆,或者通过GPS定位车辆。
福特福克斯纯电动汽车的结构如图2-33所示。
(1)电机控制器及转换装置 电机控制器监视电机的位置、速度、功率和温度等参数,利用这些信息和由驾驶人发出的加速踏板命令,电机控制器和逆变器将电池提供的直流电压转换成3个用于精确定时驱动的电机信号以完成对驱动电机的控制。
(2)高压空调压缩机 高压空调系统是专为纯电动和混合动力汽车而设计应用的,其能量直接从主电池获取。压缩机中需要包含逆变器相关设备。
图2-33 福特福克斯纯电动汽车的结构
1—电机控制器及转换装置 2—高压空调压缩机 3—电控水冷管路 4—驱动电机 5—电动助力转向装置 6—变速器 7—模块化动力总成悬架 8—电控真空泵 9—高压制冷/加热装置及控制器 10—整车控制单元 11—电池箱和电池单体 12—交流充电器 13—DC/DC变换器
(3)电控水冷管路 电控水冷管路为驱动电机、变换器和空调器进行冷却。
(4)驱动电机 驱动电机承担着将电能和机械能互相转换的作用。同时,相比同样功率的内燃机,电动机的效率要高3倍,可以有效减少能量损失和热量的产生。
(5)电动助力转向装置 是从汽油机版本福克斯继承下来的电动助力转向装置。
(6)变速器 电动汽车的变速器传动装置与传统车辆中的传动装置作用相同,但是由于电机不同的高转速特性和高效率及低噪声要求,在对电动汽车的变速器传动装置进行设计时,需要考虑不同的重点。一般电动汽车变速器传动装置是一级变速单元,具有约为5.4∶1的减速比。
(7)模块化动力总成悬架 相当于传统车辆的发动机舱,将电动汽车各种子系统组建集成起来,并实现与车身的隔离。
(8)电控真空泵 真空泵向制动系统提供真空环境以对动力总成实现辅助。
(9)高压制冷/加热装置及控制器 纯电动汽车和混合动力汽车对所使用的加热系统进行了特殊设计,使用了能量效率PTC技术对冷却剂加热并在加热系统中进行循环。
(10)整车控制单元(VCU) VCU将驾驶人及车内各个独立的系统与监视器进行连接,同时根据汽车总成系统提供的各种参数对整车进行控制。VCU还可以将电动汽车中不同的有效能量源和向车轮传送的机械动力进行管理。
(11)电池箱和电池单体 整个电池箱由处于后排座椅后面和下面的两个电池模块组成,并包含有电池管理系统(BMS),对每个电池单体的温度和电荷状态进行管理。
(12)交流充电器 交流充电器用于将来自电网的电力能源转换为动力电池所需要的直流电,这样就能在约6h的时间内完成对动力电池的全状态充电。
(13)DC/DC变换器 DC/DC变换器可以使电动汽车的动力电池为车身电气用电池提供12V的电压。
福特公司纯电动汽车福克斯实物、电池舱布置及底盘结构如图2-34所示。
图2-34 纯电动汽车福克斯
a)整车实物 b)电池舱布置 c)底盘结构
二、完全开发的纯电动汽车
1.通用EV1/EV2系列纯电动汽车
通用EV1纯电动汽车是通用汽车公司于1996~1999年间生产及改进的纯电动车型,是通用汽车公司开展纯电动汽车研发与制造的开山之作。EV1纯电动汽车属于完全开发型的纯电动汽车,不是对现有车辆的转换,也没有与其他车型共享车型,这有助于其开发和生产适当的动力传动系统。
通用汽车公司于1999~2003年推出第二代EV2,主要改进包括降低生产成本,使运行更安静,大大减轻重量,应用了镍金属氢化物(NiMH)电池,其容量为77A·h,额定电压为343V。装配有镍氢电池的车辆续驶里程为161~225km(100~140mile)。
(1)整车技术和设计 EV1纯电动汽车不仅用于展示电驱动系统,而且还担任了技术首演的任务,后来开发的纯电动汽车大多采用了同样的模型和概念。该车是最早利用铝框架结构生产的汽车,其车身面板由塑料制成,而不是金属,使汽车质量很轻。无钥匙进入和点火系统、自动胎压监测系统、电动助力转向、可加热车窗玻璃、可编程的空调系统等先进技术投入应用。
为了提高效率,EV1纯电动汽车具有非常低的风阻系数(cd)和迎风面积(A),分别为0.19和0.36m2。超轻型镁合金轮毂和座椅能有效降低整车质量,米其林开发的自封闭、低滚动阻力轮胎的应用也符合EV1高能量效率的设计特点。其结构如图2-35所示。
图2-35 通用EV1电动汽车的结构
(2)传动系统 这款车使用的三相交流异步电机可以在7000r/min时产生102kW(137hp)的功率。与内燃机驱动的汽车不同,EV1纯电动车有提供充足转矩功率频带的能力,可以在0~7000r/min的任何转速下产生149N·m的转矩,并通过单级减速装置将动力传输到前轮。
(3)动力电池 通用汽车公司1996年发布的EV1纯电动汽车使用铅酸电池,质量为1400kg(3086lbf)。第二代汽车于1999年发布,采用了由松下公司提供的一批新的铅酸电池,具有60A·h的电量,并可提供312V的电压,有效增加了EV1电动汽车的行驶里程,达到120~160km(75~100mile)。不久后,第二代汽车(EV2)推出,使用了基于镍金属氢化物(NiMH)的“Ovonic”电池组,从而使得EV2电动汽车的整备质量降至1319kg(2908lb)。“Ovonic”镍氢电池组的总电量为77A·h,可以在343V的给定电压下放电,使续驶里程增至120~240km(75~150mile),超过原来的2倍。
“Ovonic”镍氢电池组完全充满电需要约8h,80%的容量可以在1~3h达到。松下公司提供的铅酸电池组包括26个12V、60A·h的铅酸电池单体,每个单体有67.4MJ的能量(18.7kW·h)。在镍氢电池包中则为26个13.2V、77A·h的电池单体,每个单体有95.1MJ的能量(26.4kW·h)。
2.本田EV-plus纯电动汽车
1996年4月,本田公司HondaEV-plus纯电动乘用车面世,并开始进行道路试验。1997年9月,本田公司开始在日本主要城市的本田销售公司出租装备数据记录器的EV-plus纯电动汽车,租期为36个月。EV-plus车型专门针对电动汽车开发了全新车身,能满足美国和日本的安全法规。该车使用的是高性能镍氢蓄电池,充电一次可行驶210~350km,最高车速可达130km/h。
本田是第一家使用非铅酸电池制造纯电动汽车的主要汽车制造商,虽然只有300辆左右的EV-plus纯电动汽车被制造并发布。EV-plus汽车在1999年停止生产,以便本田进行混合动力电动汽车如本田Insight的研发和制造工作。本田汽车公司研发EV-plus车型的原因之一是为了在电动汽车领域赶上通用汽车公司的EV1纯电动汽车。本田EV-plus纯电动汽车的结构视图如图2-36所示。其局部结构图如图2-37所示。
图2-36 本田EV-plus纯电动汽车的结构视图
EV-plus纯电动汽车使用的电力冷却系统复杂的水冷管路如图2-37所示。
图2-37 本田EV-plus纯电动汽车局部结构图
与其他使用空冷系统的汽车不同,EV-plus纯电动汽车使用一个中央水冷系统对电机、电机控制器、变换器和逆变器等部件进行集中冷却。驱动电机使用一个单独的冷却水套,同时在电机控制器上也有一个独立的冷却水套以达到最优的冷却效果。一个电动水泵驱动冷却液不断循环,同时根据需求安装有专门设备对冷却液的温度及流动状况进行实时监测。EV- plus纯电动汽车动力舱内实物图如图2-38所示。
图2-38 EV-plus纯电动汽车动力舱内实物图
EV-plus纯电动汽车拥有两种不同的驾驶模式:常规模式和经济模式。在常规模式下,整车具有良好的行驶性能;在经济模式下,动力性能会下降很多,以便于保证最佳续驶里程。与其他几乎所有车辆相同,驾驶风格的不同对车辆行驶里程的影响很大。急加速、高速行驶和频繁起停会降低续驶里程。经济模式下的驾驶可以使EV-plus纯电动汽车获得130~180km(80~110mile)的最大续驶里程。
EV-plus纯电动汽车参数如下。
①前/后轮距:1.50m/1.49m(59.1in/58.7in)。
②传动系统:前轮驱动。
③乘客数:4位。
④电压:288V。
⑤电机:直流无刷。
⑥功率:49kW(66hp)。
⑦电池:12V镍氢电池模块。
⑧充电时间:6~8h。
⑨加速性能:4.9s(0~48km/h)。
⑩最大速度:130km/h(80mile/h)。
(11)续驶里程:100mile,即160km(80%放电)。
3.奥运纯电动大客车
(1)整车概述 BK6122EV型纯电动客车(图2-39)的整车动力性、可靠性、安全性、能耗经济性均较好,具有完全的自主知识产权;BK6122EV型纯电动客车整车造型设计独特,内饰美观高雅,舒适性高,采用专用电动化低地板底盘,整车达到发动机客车超二级相关要求,并解决了与无轨电车电网兼容的电-电混合的关键技术;该车在国际上首次使用先进的锂离子动力电池组、分散式充电快速更换方案、无离合器3档机械自动变速电驱动系统、电动涡旋式一体化冷暖空调器等具有自主知识产权的关键部件,综合技术水平和产品化程度高,整车能耗低。
图2-39 BK6122EV型纯电动客车的外形
(2)整车布置 BK6122EV型纯电动客车采用动力装置后置、后轮驱动形式。动力电池组全部放置在车的下部,车内全部采用双排座椅,冷暖一体化空调器放置在车顶前部,电机控制器等高压部件放置在后舱。整车具有合理的轴荷分配和良好的操纵稳定性。其整车布置形式如图2-40所示。
(3)整车技术方案(图2-41)
1)先进的超低地板结构。低地板公交客车由于采用了方便残疾人的一级踏步设计方案,是国外发达国家的主流高端城市公交车型。我国近5年才研发成功内燃机车型专用的低地板底盘,并在此基础上开发出了低地板整车。但低地板结构方式给整车布置带来了困难,对于纯电动客车来说,由于电池组数量多,占用空间大,采用低地板布置更加困难。BK6122EV型纯电动客车同时服务于北京奥运会和残奥会的中心区,低地板结构是必然选择,也是国际奥委会和北京奥组委提出的要求。围绕整车高效节能的要求和奥运需求,设计时彻底摒弃了纯电动汽车以改装设计为主的传统思路,开发了低地板公交车专用电动化底盘,解决了动力系统的集成与匹配、整车轻量化、结构和高电压安全、二次绝缘、电磁兼容等核心技术困难,开发了国际上首创的电动低地板公交客车,乘客门一级踏步高度为370mm,车厢地板离地高度为390mm。该车可参照的技术指标达到了建设部CJ/T162—2002《城市客车分等级技术要求与配置》标准中最高级别——大型客车超二级标准要求,研制的两种基本车型和两种扩展车型通过了国家产品定型试验,并获取了国家汽车产品公告。
2)先进的能量源和动力驱动系统。锂离子动力电池工作电压高(单体达到3.6V),能量密度高,具有放电电压平台好、循环寿命长、无污染、无记忆效应等优点,是最有发展前景的动力电池类型。随着锂离子动力电池技术的飞速发展,美国、日本和欧洲发达国家等地区已经将电动汽车动力电池从镍氢电池转向锂离子动力电池。但是到目前为止,国外的电动客车基本使用铅酸电池或镍镉电池作为能量源,锂离子动力电池在电动汽车上大规模的应用还没有其他先例。BK6122EV型纯电动客车是世界上锂离子动力电池第一次大规模的应用(图2-42),同时为了保证奥运期间24h不间断运行,采用了集中充电、快速更换电池的运行方案。为此开发了新型标准化动力电池箱,它具有防水、防尘、防火的功能,支持快速更换;同时开发了手动和自动快速更换装置,建设了充电站。
图2-40 BK6122EV型纯电动客车整车布置形式
a)正视图 b)侧视图 c)座椅布置图
图2-41 BK6122EV型纯电动客车的整车技术方案
图2-42 BK6122EV型纯电动客车动力电池组
纯电动客车的能量完全来源于动力电池,能量利用效率的高低直接影响到电动客车的续驶里程和经济性。传统电动客车设计方法中多采用无变速器或者二档手动变速器设计,不能很好地保证整车的动力性和经济性。BK6122EV型纯电动客车采用三相交流感应电机和多档机械自动变速器(AMT)组成的一体化电驱动系统(图2-43)。整车控制器通过网络化信息系统进行智能监控,提高了整车的能量利用效率,使整车的动力性能和经济性能明显得到改善,可靠性和舒适性大大提高。
3)兼容无轨电车的电-电混合方案。为了使BK6122EV型纯电动客车具有高技术和高水平,考虑到无轨电车线路、现有无轨弓网充电需求,以及锂离子动力电池可能存在的高成本问题,在纯电动公交车上预留无轨电车接口,并在电动客车底盘系统集成时完善兼容弓网供电方案,这样可以使其进一步升级成为新型电-电混合城市公交车方案(图2-44)。该方案能使现有的无轨电车向无网区域延伸,技术上向前大大跨越一步,并具有实用性。具体方案如下。
①在车顶上预留无轨电车座圈结构基础,车顶预埋高压线路、低压控制线路和通信线路。
②按照无轨电车的技术要求,整车高压部件和车身均要有二级绝缘。
③整车尺寸参数
(a)外形尺寸(长×宽×高):11850mm×2540mm×3300mm。
图2-43 行驶系统简图
1—电机 2—自动变速器 3—传动轴 4—驱动轮 5—后桥
图2-44 新型电-电混合城市公交车方案
(b)轴距:5800mm。
(c)轮距(前/后):2096mm/1836mm。
(d)前悬/后悬:2560mm/3490mm。
(e)接近角≥7°。
(f)离去角≥7°。
(g)最小离地间隙:152mm。
(h)乘客门一级踏步高度:370mm。
(i)车厢地板离地高度:390mm。
(j)车厢内最大宽度:2430mm。
(k)乘客座位数:22~32个。
④整车质量参数
(a)整备质量:14500kg。
(b)乘客数:50人。
(c)总质量:18000kg。
(d)轴荷分配:空车时,前轴为4500kg,后轴为10000kg;满载时,前轴为6500kg,后轴为11500kg。
⑤整车主要性能参数如下。
(a)最高车速≥80km/h。
(b)0~50km/h加速时间≤25s。
(c)最大爬坡度(满载)≥20%。
(d)制动距离(30km/h)<9.5m。
(e)续驶里程(40km/h等速):360A·h电池组≥180km(标准型);480A·h电池组≥240km(扩展型)。
(f)最小转弯直径:24m。
三、未来的纯电动汽车技术
1.KAZ纯电动汽车
图2-45所示为由日本庆应大学环境情报系清水皓教授主持,东京R&D“JZA”和环境厅国立环境研究所共同参与开发的KAZ大型多用途纯电动汽车。
图2-45 日本KAZ大型多用途纯电动汽车
该车可乘坐8人,装有6个车门、4根车轴和8个车轮。每个车轮上都安装有1台功率为55kW的电机,车辆总功率达440kW,采用168只3.75V高性能锂离子电池作为动力源。一次充电续驶里程为300km,最高车速达300km/h。卓越的加速性能和宽敞的空间是KAZ纯电动汽车的最大特点,同时较为成熟的轮毂电机技术也使得该车具有较好的操控性。另外,KAZ纯电动汽车所使用的锂离子电池寿命较长,是整车较长使用年限的保证。其座舱布置及低地板设计如图2-46所示。
图2-46 KAZ纯电动汽车的座舱布置及低地板设计
KAZ纯电动汽车总体开发理念如图2-47所示。它应用了3个创新技术,如图2-48所示,其中最重要的技术是高性能锂离子电池,具有高比能量和高比功率的特点;智能功率模块(IPM)的应用可以有效降低不必要的能量损耗,同时可以将逆变器的体积做得很小;钕铁硼稀土永磁电机实现了能量的高效率利用,同时可以提供很高的转矩和车速,结构尺寸紧凑。
图2-47 总体开发理念
图2-48 创新型部件设计
KAZ纯电动汽车的结构分解图如图2-49所示。
图2-49 KAZ纯电动汽车的结构分解图
2.米其林轮毂电机
米其林研发的轮毂电机能够将电机和电子主动悬架都集成到轮内。其结构如图2-50所示,实物图如图2-51所示。
图2-50 米其林轮毂电机结构
图2-51 米其林轮毂电机实物图
每个米其林轮毂电机的重量为42kg,包括一个同样大小的30kW的驱动电机。该电机拥有一套完整的水冷系统并被连接到传统的起动机上。第二个电机通过齿轮齿条和小齿轮运行主动悬架,有效取代了传统的液压减振器。同时有一个螺旋弹簧来承担整车的静载荷,一个小的外转子盘式制动器进行制动。轮毂电机由一个单一的低控制臂式悬架连接到整车底盘上。
早期的原型Hy-light(图2-52)有四个轮毂电机,可以进行两轮驱动和四轮驱动的切换。两个前轮电机提供总共60kW(82hp)的动力,峰值可达120kW(163hp)。整车0—100km/h(0—62mile/h)的加速时间在10s内,最大速度为140km/h(87mile/h)。
图2-52 米其林基于其轮毂电机开发的主动控制汽车底盘(Hy-light)
(1)米其林轮毂电机的优点
①省略大量传动部件,让车辆结构更简单。
对于传统车辆来说,离合器、变速器、传动轴、差速器乃至分动器都是必不可少的,而这些部件不但质量不轻,而且使车辆的结构更为复杂,同时也存在需要定期维护和易发故障的问题。但是轮毂电机就很好地解决了这个问题。除了使结构更为简单之外,采用轮毂电机驱动的车辆可以获得更好的空间利用率,同时传动效率也有所提高。
②可实现多种复杂的驱动方式。
轮毂电机具备单个车轮独立驱动的特性,因此无论是前驱、后驱还是四驱形式,它都可以比较轻松地实现,即使是全时四驱,在轮毂电机驱动的车辆上实现起来非常容易。同时轮毂电机可以通过左右车轮的不同转速甚至反转实现类似履带式车辆的差动转向,大大减小了车辆的转弯半径,在特殊情况下几乎可以实现原地转向(不过此时对车辆转向机构和轮胎的磨损较大),这对于特种车辆很有价值。
③便于采用多种新能源汽车技术。
采用轮毂电机可以匹配包括纯电动汽车、混合动力汽车和燃料电池电动汽车等多种新能源车型,轮毂电机可以和传统动力并联使用,这对于混合动力车型很有意义。
新能源汽车大多采用电驱动,因此轮毂电机驱动也就派上了大用场。无论是纯电动汽车还是燃料电池电动汽车,抑或是增程电动车,都可以用轮毂电机作为主要驱动装置;即便是混合动力汽车,也可以采用轮毂电机作为起步或者急加速时的助力装置,可谓是一机多用。同时,新能源汽车的很多技术,如制动能量回收(即再生制动)技术,也可以很轻松地在轮毂电机驱动车型上得以实现。
(2)米其林轮毂电机的缺点
①增大了簧下质量和轮毂的转动惯量,对车辆的操控性能有所影响。
对于普通民用车辆来说,常常用一些相对轻质的材料(如铝合金)来制作悬架的部件,以减轻簧下质量,提升悬架的响应速度。可是轮毂电机恰好较大幅度地增大了簧下质量,同时也增加了轮毂的转动惯量,这对于车辆的操控性能是不利的。不过考虑到电动汽车大多限于代步而非追求动力性能,这一点尚不是最大缺陷。
②电制动性能有限,维持制动系统运行需要消耗不少电能。
现在已经有不少传统动力商用车装备了利用涡流制动原理(即电阻制动)的辅助减速设备,如很多货车所用的电动缓速器。而由于能源的关系,电动汽车采用电制动也是首选。不过对于轮毂电机驱动的车辆,轮毂电机系统的电制动容量较小,不能满足整车制动性能的要求,因此需要附加机械制动系统。但是对于普通电动乘用车,没有了传统内燃机带动的真空泵,就需要电动真空泵来提供制动助力,但也意味着更大的能量消耗。即便是再生制动能回收一些能量,但为了保证制动效能,制动系统消耗的能量也会影响电动汽车的续驶里程。此外,轮毂电机工作的环境恶劣,面临水、灰尘等多方面影响,在密封方面也有较高要求,同时在设计上也需要为轮毂电机单独考虑散热问题。
与电机集中动力驱动相比,轮毂电机技术具有很大的优势,它布局更为灵活,不需要复杂的机械传动系统,同时也有自己显著的不足。例如:密封和起步电流/转矩间的平衡关系,以及转向时驱动轮的差速问题等。如果能在工程上解决这些难题,则轮毂电机驱动技术将在未来的新能源汽车中拥有广阔的前景。