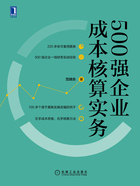
1.2 纵贯两个行业500强企业成本核算的对比
成本既是保密的,也是神秘的,很少有企业愿意公开自己的成本秘密。
【例1-6】某500强钢铁企业(以下简称“钢铁企业”)和某500强造船企业(以下简称“造船企业”),一家炼钢,一家造船。
钢铁企业主要用标准成本法,我称其成本核算为“分步法+标准成本法=分步法的PLUS版(我称之为滚雪球式的成本核算)”。
造船企业主要用非标准成本法,即目标成本法,我称其成本核算为“分批法+目标成本法=分批法的PLUS版(我称之为乐高玩具式的成本核算,制造航母即用此法)”。
两家企业的产品虽然同样都是用户定制化的、具有个性化特色的产品,但区别在于:钢铁企业的用户定制化钢铁产品十有八九是产品历史生产成本的重复,个性化只是在主体工艺不变的基础上对产品特性的微调。造船企业的用户定制化造船产品十有八九没有产品历史生产成本的重复参照,主体个性化更足。
传统理解的标准成本属于目标成本的范畴,而标准成本法和目标成本法在成本核算上有所区别:钢铁企业的标准成本核算采用“布局标准+分摊差异=实际”的核算步骤;造船企业的目标成本核算采用大订单倒逼的“价格-利润=成本”思路来控制成本。
钢铁企业也曾创新性地将标准成本法和目标成本法结合,采用“标准成本管理体系下的倒逼目标成本核算”。
两家500强企业现用的两种成本核算方法,到底谁的更好一些?
钢铁企业的工艺特点:长流程、生产周期短,涉及大量工序间的分摊和结转,之后再分摊到最终产品上。长流程成本核算流到最终产品上,核算路径会更长、更交叉、更容易失真。因此,标准成本法更适合处理长流程的烦琐复杂重复工艺,匹配契合度更好。
造船企业的工艺特点:接单生产,一单一价;流程短、生产周期长,按“分批分装中间产品+整装最终产品”的步骤生产,因此成本分摊和结转次数相对钢铁企业要少,到最终产品成本核算的路径更近,使用目标成本法核算契合度更好,结果更接近成本实际发生情况。
就两家500强企业的适用度来说,两种成本核算方式没有好与坏,只有契合度的问题。
钢铁企业更适合用标准成本法,因为这样才能说清楚长流程的复杂成本。钢铁企业满足对外披露需求,成本核算只是到成本中心(工序)层面,并未进一步细化到由成本中心分摊至明细产品、作业或机组,只有满足对内管理需求的成本核算,才细化到明细产品。
造船企业更适合用目标成本法,因为这样才能说清楚作为最终订单目标产品(一艘船)的成本发生。造船企业目标产品(项目)核算之前的成本归集,没有划小核算单元至作业或机组,只是到工序成本中心,再由成本中心分摊到各目标产品(项目)。
为什么两家500强企业暂时不能做得更细?为什么不能从成本中心归集成本全面细化到作业(机组)归集成本呢?请参见第7章“500强企业的成本核算实操解密”。
综上可以看出,两类企业虽然同属制造业,但在成本核算上有着各自不同的特点,以下进行具体解密。
1.2.1 成本核算各行其道
1.2.1.1 500强钢铁企业的成本核算特点
从实际操作层面看,钢铁企业成本核算的特点主要有以下几点。
1.不一样的成本核算步骤
标准成本法的成本核算与传统实际成本法的成本核算的不同之处有哪些呢?
标准成本法的核算步骤为“标准成本+差异分摊=实际成本”,而不是“实际成本-标准成本=差异”,即不是分摊实际,而是先根据历史经验数据制定并在预算编制时布局标准;实际发生时,先计算统计出差异;最终分摊结转的是“差异”,才得出实际核算结果。
【例1-7】如图1-2所示,就以修理费为例说明区别。假设前、后工序成本中心实际发生修理费共计100元;以修理次数占比40%∶60%作为分摊依据(成本动因)分摊给前、后工序成本中心。已知前工序修理费预算标准为30元,后工序修理费预算标准为50元。

图1-2 标准成本法与传统实际成本法的区别——T形账简例
传统实际成本法:直接把实际发生的100元修理费按40%∶60%分摊给前、后工序,即分摊给前工序实际修理费40元,分摊给后工序实际修理费60元。
前工序实际与预算的差异=实际-标准=40-30=10(元);
后工序实际与预算的差异=实际-标准=60-50=10(元)。
标准成本法:前工序标准为30元,后工序标准为50元,总标准为80元。实际为100元,则总差异为100-80=20(元)。下面要分摊总差异至前后两个工序:
前工序分摊差异=20×40%=8(元);前工序修理费实际=标准+差异=30+8=38(元);
后工序分摊差异=20×60%=12(元);后工序修理费实际=标准+差异=50+12=62(元)。
2.引入作业成本法的成本动因,做标准成本法的事情
引入作业成本法的成本动因,做标准成本法的事情,这样就可以在各项成本标准的制定上突破传统成本变动只跟产量挂钩的观念,找到影响成本变动最直接和最根本的原因。
3.以财务部门为中心统一进行成本核算
成本核算是成本管理的职能之一,而成本管理的目的是力求以最少生产耗费,以“有舍才有得的成本最佳投入产出比”思想取得最大的生产成果——提升企业成本竞争力。
4.实行一级成本核算
把生产费用核算和产品成本计算集中在厂部一线驻厂财务(成本组)进行的成本核算制度叫“一级成本核算”。各生产车间对其所发生的经济业务一般只填制有关原始凭证和原始凭证汇总表,定期送交财务部驻厂成本组。生产成本核算的全部工作都集中在财务部驻厂成本组来完成。
5.成本核算与成本管理(控制)“分离但不分家,脱离而不脱节”
对外核算相对粗:500强企业成本核算在一体化财务信息系统实现满足对外报表披露的要求,核算对象单元仅核算至工序成本中心层面。
对内核算相对细:如果要核算至明细产品,则成本核算要进一步与成本管理挂钩,即另外通过500强企业独立的数据仓库(SAS系统)实现明细产品成本核算、预算分析、盈利能力分析等管理功能,以满足内部成本管理等需求。
这就是所谓的成本核算与成本管理(控制)分开,做到内外有别。对外核算较粗以满足披露需求,对内核算较细以满足管理需求,我称之为“分离但不分家,脱离而不脱节”。
6.自动化成本核算功能覆盖产线
成本核算实现了自动做账而非人工做账,靠软件公司设计的一体化财务信息系统实现规则化的自动做账,并通过数据仓库(SAS系统)实现从工序成本中心到明细产品核算。
除了上述实际操作层面的成本核算特点以外,长流程重复生产的钢铁企业成本核算还有两个重要特点。
第一个特点:有可参照的历史数据作为成本标准。
钢铁企业每个工序、每个成本核算内容都有对应的标准成本,以备比较。
这些标准成本是怎么来的,又是怎么制定的呢?
不同于短流程的制造企业,长流程重复生产的企业工艺变化不大,生产的产品规格、性能、化学参数都比较稳定。
正是因为周而复始重复生产同样的产品,所以数据才具有可得性,才能积累大量可参照的历史数据;也正是因为重复生产,所以历史数据才能用得上。
通过数据分析,将历史数据当中正常或稳定生产状态下的数据筛选出来,作为参照。换句话说,把正常或稳定生产状态下的历史成本数据,做大数据分析后,选择常态下正常或稳定生产所发生的成本参数(例如:炼1吨铁水需要多少吨矿石)作为成本触发点标准,将它们总结出来并价值化,就形成了标准成本。
标准成本就是你要看齐的目标,实际成本就跟它比。标准成本是正常的、稳定的状态下应该发生的成本。所以标准成本是一种“应该成本”,它不受实际成本波动的影响,用于决策也更科学合理。
利用明细产品标准成本算出来哪个产品最赚钱,就可以事先模拟安排生产哪种产品的优先度,也可以支持营销决策。比如:是先产先卖还是后产后卖?利用产品标准成本来评估新投产的产品成本和到底能赚多少钱?这样,就可以支持投资决策,到底是投还是不投。
实际成本如果与标准成本差异大,很大可能就是实际不正常了,即实际发生的成本出现了异常,企业通过分析往往就能知道问题出在了哪里。
钢铁企业的标准成本核算制度,我总结如下。
事先:按照“标准成本+末梢成本触发点标准”将成本标准在编制预算时全盘布局完毕。
事中:用实际核算出来的成本与标准成本两者相减并根据差异预警动态实时调整以实现事中控制。
事后:月末将最终差异根据成本动因分摊至工序成本中心。这一步完成之后,就可以运用因素分析法来计算差异,找出产生差异的原因,从而分析并加以改善。
标准成本和目标成本都有倒逼性。从这一点上看,标准成本类似于造船企业工程项目的非标准成本,即目标成本。
基于这样一个“标准成本”建立起来的预算、核算、分析评价、绩效考核的体系,就被冠以了“标准成本制度”的叫法。
第二个特点:主工序成本中心成本核算“守土有责,谁生产谁核算”。长流程生产大规模工业基础材料,工序繁多,各工序只核算本工序的成本。
图1-3为某钢铁企业最赚钱的汽车板产品制造主工序成本核算流程简图。

图1-3 某500强钢铁企业产品制造主工序成本核算流程简图
炼铁厂需要原料,也就是生产铁水需要矿石原料,另外还会发生如其他原料、人工费、折旧费、修理费、水电费等一串成本,才能生产出铁水。
炼铁厂生产铁水的所有成本会打包后总体结转到炼钢厂的原料成本里,也就是生产钢坯所需要的铁水原料成本,另外还会发生其他原料等一串成本,才能生产出钢坯。
炼钢厂生产钢坯的所有成本,会打包后总体结转到热轧厂的原料成本里,也就是生产热轧板所需要的钢坯原料成本,另外还会发生人工费等一串成本,才能生产出热轧板。
以此类推,最终,层层结转后,就把矿石原料的成本结转(移转或者流转)到了最终产品——汽车用钢板的生产成本上。
在这个过程中,成本核算是如何进行的呢?
钢铁企业的每个主工序(成本中心)都要设置一层成本核算,用于核算本工序成本中心发生的成本内容。以其中的炼钢厂工序设置成本核算为例,如图1-4所示。

图1-4 某500强钢铁企业主工序成本中心(炼钢厂)成本核算范例
这些成本核算内容分为三个部分。
直接支出费用,指此主工序成本中心独立发生的费用。如:直接人工费、折旧费、差旅费、物料领用费等,一般为直接成本。
内部移转——标准,指此主工序成本中心领用前工序产品或辅助工序分摊结转过来的标准成本。如:辅助工序设备部维修、自备电厂电费、自备水厂水费等,一般为间接费用。
内部移转——差异,指此主工序成本中心领用前工序产品或辅助工序分摊结转过来的成本差异。
本工序的产品成本打包后,结转到后工序,作为后工序的原料。后工序不用核算价格因素,但要核算消耗因素,因为消耗是本工序发生的,而价格是前工序结转过来的。换句话说:原料除了本工序消耗指标以外,其他都由前工序来核算,正所谓“守土有责,谁生产谁核算”。
如图1-3所示,炼铁厂生产铁水,需要矿石。对于矿石价格,炼铁厂控制不了,所以由采购部门来分析;而矿石消耗,是由炼铁厂控制的,就由炼铁厂来分析。
同样,炼钢厂生产钢水,需要铁水,铁水的价格高低,由炼铁厂分析;而铁水消耗,是由炼钢厂控制的,则由炼钢厂分析。以此类推。
不难看出,钢铁企业成本核算的设计特点大致如下:
● 前工序产品是后工序的原料,前工序的单位成本是本工序的单价;
● 守土有责,谁生产谁核算;
● 事前先根据历史经验数据制定并在预算环节全盘布局标准,事中计算统计出差异并动态实时控制,事后分摊结转最终差异得出实际核算结果;
●“末梢成本触发点”标准需要与标准成本相对应、匹配并看齐。
1.2.1.2 500强造船企业成本核算特点
长流程重复生产、生产周期短的规模制造企业适合用标准成本来核算、分析。
还有很多企业,流程短、生产周期较长。比如:加工型的企业,建筑业、造船业、钢结构生产的企业等。一般像这类企业靠招投标等方式承接工程项目订单。其成本发生特点是:需要根据用户的个性化需求定制工程项目或产品,这类工程项目或产品的成本一般是一事一议的。成本发生具有独立性,没有之前的成本经验数据作为参照。
这些行业的企业大多用目标成本法进行成本核算。
【例1-8】造船企业就主要使用“分批法的PLUS版”的目标成本法进行成本核算。但由于造船工业的多工艺特点,对于某些局部零件(中间产品)的加工可能由多个生产工序连续加工制成,如铸造车叶就可能经过木模、造型、浇注、车工、钳工等工序。为了考核各工序成本,对类似铸造车叶这部分内部分批分装的中间产品成本核算就局部采用了“分步法”。
目标成本法是企业对有独立制造过程的产品进行利润计划与成本管理的方法,它是以市场价格为参考,以顾客需求为导向,在产品企划与设计阶段运用价值工程、产品功能分析、成本分析等方法以达成目标利润而制定目标成本的一种管理方法。
这里以造船企业的成本核算为例。
造船业的特点是短流程、生产周期长,订单一事一议,个性定制化强、历史成本标准无法参照。造船企业的目标成本对象为所造船只(见表1-1)。
表1-1 工程项目成本计算单汇总简表——SH18001龙之丸号船(单位:万元)

船舶的材质主要为钢材,小型船舶也有以水泥、木材、铝合金、玻璃钢为主要材料的。船舶吨位有几百千克至几十万吨不等。大型船舶结构比较复杂,造价可达几亿美元,建造周期长达好几年。
与钢铁企业的长流程工艺和建造周期短的特点形成反差,造船企业成本核算所对应的行业特点是短流程工艺和建造周期长,一般涉及以下几个过程的成本内容。
(1)生产设计、相关材料和设备的采购。生产设计的好坏直接关系到船舶生产的进度及质量。另外,船厂的采购部门需要向其他设备商订购主机及其他配件。成本核算涉及设计费、采购成本以及相关差旅费成本等。
(2)板材和型材的加工放样。板材和型材的预处理板到了船厂以后,要进行校平,表面除锈后上底漆,然后需要下料及成型加工。成本核算涉及材料费、人工费、折旧费、协力费、能源费、切割耗材成本、涂装成本等。
(3)分批组装过程的工作量很大,主要是在生产车间内把型材和板材焊接成分批中间品,再用平板车将这些分批中间品运输到现场。成本核算涉及材料费、人工费、折旧费、协力费、能源费、焊接涂装等成本。
(4)船体合龙就是在船台上和船坞内把分批中间品组合成船。这个过程难度比较大,劳动强度也很高;同时,该过程涉及大量的起重和焊接作业,因为对设备要求较高,该过程成为船舶生产中的瓶颈。成本核算涉及人工费、折旧费、协力费、能源费、焊接涂装成本等。
(5)下水是船舶建造中最危险的过程,一旦发生事故整个船就报废了,可能涉及不可预测费用。
(6)码头舾装把管子、阀门和其他大型设备及装潢材料装上船。这个过程涉及的专业最多,是船舶建造中最混乱也最容易发生事故的过程。成本核算涉及设备采购费、人工费、折旧费、协力费、装修费及安装费、焊接涂装成本等。
(7)试验交船包括系泊试验和航行试验,主要是测试实际建造完成后船舶各方面的性能数据。成本核算涉及试验检验费。
目标成本管理的特点是在产品的设计、生产到交付使用等产品整个生命周期内都进行成本管理的一种事前控制成本水平的方法。
根据造船企业的管理和生产特点分析,目标成本管理是一种很适合造船企业使用的成本管理方法,可以有效地降低造船企业在船舶设计、材料采购、分批组装及船体合龙作业、下水及设备安装、装潢、试验交船中的全过程成本。
目标成本管理,一般由企业的企划部门以工程项目号为归集费用的预算对象,编制工程项目的目标预算。这些预算在招投标竞价阶段,就已经编制出了工程项目整体成本发生的预算概况。企划部门工程项目的目标预算是根据工程进度和项目变化动态调整的。
造船企业根据采购钢材的市场价格变化等情况调整目标预算,在分期分批发货确认收入时,按调整后的生产成本进行营业成本的确认和结转,并对上批发货已确认的成本进行该工程项目的整体调整,结合目标成本分析,以期达到优化和改善造船短流程的全过程成本,因此造船企业用的成本核算方法的设计是需要契合或者匹配目标成本分析的。
我个人的理解是,目标成本法在某种意义上和作业成本法、标准成本法是相类似的,即目标成本法也是一种倒逼成本的方法。
结合钢铁企业成本核算特点以及造船企业成本核算特点对比,可以看出:“成本预算→成本核算→成本分析→绩效考核”是一个基本的成本管理路径,如图1-5所示。

图1-5 钢铁厂与造船厂成本核算特点对比图
成本核算的核心目的是:向前端为成本预算服务,向后端为成本分析服务。
然而行业的不同、先天成本属性的不同,决定了成本核算的不同。
1.2.2 凭什么钢铁企业能用标准成本而造船企业不能
为什么钢铁企业能用标准成本,而造船企业不能?这是因为生产工艺等特点决定了成本核算特点。
钢铁企业能形成标准,造船企业形成不了标准。
钢铁企业是长流程、短周期、大规模重复的分步骤生产工艺,从炼铁工序到炼钢工序、热轧工序、冷轧工序,再到汽车板工序,常年周而复始地重复着生产类似或同样的东西,容易收集数据,形成标准成本并作为“应该成本”,因此采用“分步法的PLUS版”核算。
造船企业是短流程、长周期,不重复生产相同产品,按照用户的个性化定制需求,一事一议,根据订单“中间品分批分装后再总装”生产;没有一贯重复发生的常规成本标准,只有企划部门订立的目标成本,属于非标准成本生产,因此采用“分批法的PLUS版”核算。
1.2.3 打回原形
成本核算的“打回原形”是指成本核算的还原,分为“工序间的成本还原”和“成本动因的还原”两种。
1.2.3.1 工序间的成本还原
如图1-6a所示,作为造船厂上游的钢铁厂,会涉及大量前、后工序间的还原问题。也就是说,其成本核算需要做到能够追溯还原到最初始的工序。

图1-6 上游钢铁厂和下游造船厂的工序成本还原与成本动因还原
原因很简单,因为钢铁产品是长流程的工业基础材料,是经过一道道不同的工序作为单独工序成本中心,单独进行成本核算的。需要把独立成本核算的全部成本中心(工序)都结合起来,才能说清楚最终某个钢铁产品的成本发生实际情况和影响成本的关键发生环节。
【例1-9】如图1-6a所示,假设钢铁厂的最终产品是造船用钢,如果它的成本大幅增加,很有可能是因为前工序热轧厂的生产故障;或者是前工序的前工序,即炼钢厂成本异常波动影响所致。
最终产品造船用钢的成本高低,不光要核算宽厚板厂这个“本工序”的成本,还需要还原至“前工序”热轧厂、炼钢厂的成本,并分析前工序的成本变化因素,因此导致宽厚板厂成本波动的因素可能在本工序宽厚板厂无法控制,需要在前工序热轧厂或炼钢厂控制。
什么叫工序成本间的还原?举个例子:生产的1吨造船用钢产品的单位成本里,炼钢厂的折旧费占了多少钱?假设1吨造船用钢产品的单位成本是4000元/吨,那么,炼钢厂工序中钢坯里的折旧费,在这个最终产品——4000元/吨的造船用钢产品的单位成本里,占了多少钱?这时候,就需要还原再还原,需要成本核算的匹配以达到还原目的。
1.2.3.2 成本动因的还原
除了工序间成本还原外,还有成本动因的还原。由于间接费用分摊后的成本结果无法显示费用的内容、来源和明细金额,因此需要对制造费用进行成本动因的还原才能说清楚。
【例1-10】造船的材料成本就是采购钢铁厂造船用钢的成本,是从上游企业采购的。造船企业不需要成本核算去揭示上游造船用钢成本的波动原因,只需关注整个造船过程中的成本核算。造船企业涉及工序还原问题相对较少,更多会涉及成本动因的还原问题,如各明细工程项目的间接费用还原问题,如图1-6b所示。
造船企业主工序少、辅助工序多,需要分摊的共用性费用就多;分摊就需要分摊依据,即成本动因的还原。这就是造船企业涉及工序还原问题相对较少,更多会涉及成本动因还原问题的原因。造船企业分段、分批、分装中间品和总装最终产品的分摊成本动因还原情况,如图1-7所示。

图1-7 造船企业的工序成本还原和成本动因还原