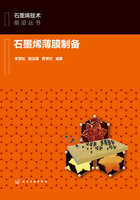
1.6 制备方法
常用的石墨烯制备方法包括以下几种。
a.微机械剥离法。该方法将从石墨中剥离出的薄片两面粘在胶带上,再撕开胶带,就可以把石墨片一分为二。不断这样操作,薄片越来越薄,直到最后获得单层石墨烯。这就是2004年Geim和Novoselov最初用于获得石墨烯研究用样品的方法[3]。这种方法操作简单,很容易在实验室中实现,被广泛应用于石墨烯等二维材料的研究,但也可以看到,这种方法无法规模化,不能用于材料的工业化制备。
b.热蒸发法。佐治亚理工大学de Heer等同样于2004年通过热蒸发法在SiC基底上合成了石墨烯[12],并于2006年对该方法进行了优化[60]。该方法将SiC基底在超高真空腔室中加热至1250~1450℃,使SiC基底表面的硅原子蒸发,留下碳原子重组形成单层和多层石墨烯。这种方法对设备要求较高,并且SiC基底本身也比较昂贵,因此成本较高。此外,生长在SiC基底上的石墨烯难以转移下来,也极大地限制了其应用。
c.氧化还原法。使用硫酸、硝酸、高锰酸钾、双氧水等氧化剂将天然石墨氧化,制得氧化石墨(Graphite Oxide),然后通过物理剥离、高温膨胀等方法将氧化石墨分散得到氧化石墨烯,最后通过加热或与还原剂反应等方法将氧化石墨烯还原,得到还原氧化石墨烯[61]。这种方法操作简单,产量高,但是还原反应并不能真正地将石墨烯的结构“还原”,产品缺陷较多。此外,该方法使用硫酸、硝酸等强酸,可能造成环境污染。
d.机械分散法。利用搅拌、超声或剪切等方式,将石墨在具有匹配表面能的有机溶剂中分散,再将得到的悬浊液离心分离,去除厚层石墨,即可留下石墨烯[62]。这种方法不引入缺陷,并且对环境的污染很小。但该方法对石墨分散的效果有限,产率较低。
e.化学气相沉积(chemical vapor deposition,简称CVD)法。CVD法使用含碳气体为原料,通过化学反应,在基底上沉积制得石墨烯薄膜,反应温度一般为800~1100℃。用于CVD法制备石墨烯的基底可以分为金属和非金属两种。金属基底中比较常用的是镍和铜。由于碳在镍中的溶解度较高,当温度降低时,会有较多的碳析出,因此可以用于多层石墨烯薄膜的制备,但石墨烯薄膜厚度的均匀性很难控制[63-65]。基于铜对碳的溶解度很低的特性,2009年,美国德州大学奥斯汀分校李雪松及R.S.Ruoff等成功地在铜箔基底上实现了大面积均匀单层石墨烯薄膜的制备,其结构可控性及品质是所有人工制备的石墨烯中最好的[33]。基于铜基底的CVD法是目前生产石墨烯薄膜最有效的方法。尽管如此,在实际应用中,通常需要将生长在金属基底上的石墨烯薄膜转移到目标基底(一般为非金属基底)上使用,转移过程不但增加了生产成本,还会对石墨烯薄膜造成破坏和污染,因此,人们也对在非金属基底上直接生长石墨烯进行了大量的研究,但目前的结果还不尽如人意,在非金属基底上生长的石墨烯的质量还无法和金属基底上的相比。