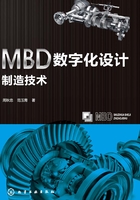
1.3.1 基于TC/UG的数字化管理平台总体框架
基于TC/UG的数字化管理解决方案并不是简单罗列一些零散的应用程序,而是以产品、工艺、工厂和资源关联数据模型为核心,对数字模型进行集中管理、协同和互操作,同时保证数据的一致、有效和重用。基于产品、工艺、工厂和资源的关联数据模型保证了快速、准确而安全地存取制造信息,同时可对产品结构、制造工艺进行可视化分析和优化,使生产企业各个部门和工作岗位之间的信息流动得以彻底实现。在吸收传统产品、工艺设计方式优点的基础上,充分发挥产品、工艺信息从产生、接受、维护、发送到再运用的组合功效,满足不同使用者对产品、工艺信息和数据的共享、共用,为从根本上实现产品全生命周期内数字化设计、数字化制造、数字化检测和数字化装配提供了有效的方式。
在MBD技术条件下,企业设计部门通过三维NX设计软件用MBD方式表达设计结构信息,而工艺部门接收这些MBD数据模型后,在三维NX/CAM软件中开展三维工艺设计仿真,并通过如图1.7所示的基于TC/UG的数字化管理平台总体框架对所有的数据与过程进行全面管理,保证从产品设计到工艺规划再到产品制造过程的密切相关性和数据流、信息流的传承与统一。在以TC PLM解决方案为核心构建形成的基于TC/UG的三维数字化产品数字化管理平台总体架构中,在三维数字化设计与管理的基础上,考虑并解决了设计与工艺数据之间的继承。通过与ERP、MES系统的集成,使制造BOM信息、工艺路线、材料定额、工艺规程等各种工艺数据传递到生产管理部门,成为开展生产管理过程的依据,从而实现了产品设计、工艺设计、工装设计到车间现场生产执行的全流程信息化管理,提高了产品研发协同、工艺制造协同和工装设计协同的效率,实现了企业产品三维数字化设计与制造的全生命周期管理。

图1.7 基于TC/UG的数字化管理平台总体框架
基于TC/UG的三维数字化管理解决方案引起了产品和工艺设计方式的变革,使产品的工艺设计在三维环境下进行,包括三维结构建模、三维PMI标注、三维工艺过程设计仿真等,抛弃了原有的二维工程图纸;同时工艺规程由原来的二维图形转化为三维可视化图形,要求工艺人员抛弃原有的工艺编制思维,直接应用设计提供的三维数模编制出适合现场生产的三维模型工艺、数控程序等,达到工艺设计一体化目的。