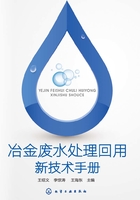
1.4 有色金属工业废水减排回用与差距
1.4.1 有色冶炼用水与废水水质状况
有色金属工业废水年排污量约9亿吨,其中铜、铅、锌、铝、镍等五种有色金属排放废水占80%以上。经处理回用后有2.7亿吨以上废水排入环境造成污染。与钢铁工业废水相比,废水排放量虽小,但污染程度很大。由于有色金属种类繁多,生产规模差别较大,废水中重金属含量高,毒性物质多,对环境污染后果严重,必须认真处理消除污染。
重金属是有色金属废水最主要的成分,通常含量较高、危害较大,重金属不能被生物分解为无害物。重金属废水排入水体后,除部分为水生生物、鱼类吸收外,其他大部分易被水中的各种有机和无机胶体及微粒物质所吸附,再经聚集沉降沉积于水体底部。它在水中的浓度随水温、pH值等的不同而变化,冬季水温低,重金属盐类在水中的溶解度小,水体底部沉积量大,水中浓度小;夏季水温升高,重金属盐类溶解度大,水中浓度高。故水体经重金属废水污染后,危害的持续时间很长。其中铜、铅、铬、镍、镉、汞、砷等重金属的危害性最为严重。
有色金属种类繁多,矿石原料品位差别很大,且冶炼技术与设备先进与落后并存,生产规模各异。因此,有色金属生产企业用水与排水量差别较大。有色工业是用水大户,吨产品用水量较大,见表1-9。
表1-9 有色金属冶炼吨产品平均用水量 单位:m3/t

有色金属工业废水的复杂性与多样性的主要原因是有色金属冶炼所用的矿石大多为金属复合矿,含有多种重有色金属、稀有金属、贵金属以及大量的铁和硫,并含有放射性元素等。在冶炼过程中,往往仅冶炼其中主要的有色金属,而对低品位的有色金属常作为杂质以废物形式清除。一般而言,几乎所有的有色金属冶炼废水都含有重金属和其他有害物质,成分复杂,毒性强,危害大。
表1-10列出国外锌、铜、铅冶炼厂废水水质。表1-11列出国内铜、铅锌冶炼厂废水水质。
表1-10 国外有色金属冶炼厂废水水质

表1-11 国内有色金属冶炼厂废水水质

同一有色金属冶炼废水水质随工艺方法的差别而异,即使是同一工厂也会因操作情况、生产管理的优劣而差异较大。例如,烧结法生产氧化铝厂的废水含碱量为78~156mg/L(以Na2O计);联合法厂为440~560mg/L,但在管理水平较差的情况下,可达1000~2000mg/L。几种不同生产工艺的氧化铝厂的废水水质见表1-12。
表1-12 不同生产工艺的氧化铝厂废水水质

有色金属工业废水造成的污染主要有有机耗氧物质污染、无机固体悬浮物污染、重金属污染、石油类污染、醇污染、酸碱污染和热污染等。表1-13列出有色金属工业废水的主要污染物。表1-14列出铜、铅、锌、铝、镍五种有色金属的主要工业污染物种类情况。
表1-13 有色金属工业废水的主要污染物

注:“√”表示含有该类污染物。
表1-14 我国五种有色金属主要工业污染物种类情况

1.4.2 减排水平与差距
(1)节水减排现状与差距
近年来,有色金属企业,特别是有色大型冶炼企业节水减排成效显著,行业新水用量呈下降趋势,重复用水率有所提高,吨有色产品和万元产值新水取用量均有下降。几家大型铝企业,如中铝中州分公司、山东分公司、广西分公司、河南分公司和云南铝业公司都实现了工业废水“零排放”,工业废水全部回用,大大减少了新水用量。
据统计,14个大型重金属冶炼企业和14个大型铝企业吨产品和万元产值总用水量和新水用量均有明显下降。14个大型重金属冶炼企业的有色金属总产量为291.54万吨,工业总产值为750.10亿元,吨金属产品总用水量、新水用量分别为550.87m3和91.78m3;万元产值总用水量、新水用量分别为214.10m3和35.68m3。
14个大型铝企业年产电解铝180.88万吨,氧化铝679.77万吨,工业总产值466.30亿元。吨产品(电解铝+氧化铝)总用水量、新水用量分别为125.25m3和13.99m3;万元产值总用水量、新水用量分别为231.18m3和25.82m3,节水减排效果显著。主要表现在:a.工业用水循环利用率不断提高,主要通过净冷却水循环、串级用水与处理回用;b.废水治理从单项治理发展到综合治理与回用;c.从废水中回收有价金属且成效显著,但与国外相比差距较大。例如俄罗斯锌的冶炼生产中水的循环率达93.6%,排放率为1.5%,镍为90%,排放率为零;有色金属加工厂为95%,排放率为零;硬质合金厂水循环率为96.8%,排放率为零。美国、加拿大、日本等有色金属选矿厂废水回用率均达95%~98%,大部分有色金属冶炼厂废水处理回用基本实现“零排放”。
根据中国有色工业协会统计,我国有色工业水的重复利用率为58.1%,其中选矿用水的重复利用率为56.6%,冶炼企业的水的重复利用率为66.6%,机修厂水的重复利用率为56.3%。我国有色金属工业“三废”资源化利用程度还很低,固体废弃物利用率仅在13%左右,低浓度二氧化硫几乎没有利用;从工业废水中回收有价元素,除几个大型企业外,绝大多数企业尚属空白,年排放未处理或未达标废水2.7亿吨以上。我国有色金属工业“三废”资源化利用程度低,已成为制约有色工业持续发展最突出的问题。
(2)差距分析与技术对策
①差距形成 有色金属工业节水减排差距形成的原因有以下几个方面。
1)当前我国有色金属工业的快速发展主要是依靠扩大固定资产投资规模实现的。“十五”期间完成固定资产投资为2509亿元,是新中国成立到2000年行业累计投资额的1.6倍。2009年电解铝产能达2000万吨,还有200多万吨在新(扩)建,产能过剩严重,在生产过程中,消耗大量矿石资源、水资源和能源,产生大量废水、废气和固体废弃物,且未能得到有效治理和利用。据统计,有色金属矿山年采剥废石已超过1.6亿吨;产生尾矿约1.2亿吨,赤泥780万吨,炉渣766万吨;排放二氧化硫40万吨以上,废水9亿吨,这些均未做到妥善处置与资源化处理。
2)产业集中度低,技术能力差,环保设施欠账过多。统计资料表明,目前全国有色金属工业企业接近1.6万个,但年销售收入3亿元以上的大型企业有52个,年销售收入3000万元以上的中型企业424个,大中型企业合计只占企业总数的3%,且地处我国中西部山区或欠发达地区,绝大多数企业生产技术比较差,节水减排和节能降耗技术能力比较弱,环保设施欠账多,造成污染严重。
3)产品结构不合理,淘汰落后设备任务重。有色金属工业长期存在技术开发能力不强,产品结构不合理;生产分散,集中度低,集约化程度不高;过多依赖国外市场,资源储备少,企业综合能力弱;生产工艺设备落后,淘汰落后设备任务重;环境保护设施投资少,环保能力弱等问题。
②解决途径与技术对策 根据国内外有色金属工业产业现状及发展趋势,我国有色金属工业在新的发展时期要适应国家节水减排和节能降耗的目标要求,必须做到以下几点。
1)优化产品结构,提高产业集中度,增强市场竞争力。面对国内外市场的激烈竞争,实现集约化经营,提高产业集中度;依靠科技创新,淘汰缺乏竞争力的落后生产能力,是产业发展的必然选择。当前我国有色金属工业大而不强的一个突出表现就是生产经营高度分散、产业总体规模虽然很大,但是还没有一家企业拥有进入全球有色金属工业企业前10名行列的实力,对世界有色金属工业发展的影响力薄弱。解决途径如下。
a.依托九大资源基地发展具有综合生产能力的有色金属企业集团。我国有色金属储量主要分布在中西部地区的九大有色金属矿产资源基地,占全国相应矿种储量的80%以上,并具有伴生性的特点。应鼓励同一资源基地内有色金属企业间联合重组,依托骨干企业,发展企业集团。实行多种金属品种的联产与企业重组,扩大企业规模,优化产品结构,在提升企业产业水平的同时,提高资源能源利用率,降低环境污染。
b.妥善解决有色金属资源基地的可持续发展。为保护我国有色金属资源,减少浪费和损失,保护环境,应坚决制止滥采乱开。对那些浪费资源,破坏和污染环境的小型采选厂和冶炼厂,坚决清理和关闭,集中优势,合理开发,综合利用,以妥善解决有色金属资源基地的可持续发展。
2)推动有色金属工业技术进步,鼓励企业一体化经营,提高市场竞争力。当今有色金属工业技术进步的重点:一是以先进实用技术和高新技术改造现有生产工艺设备,大力提升产业水平,解决环境污染与节水降耗问题;二是针对国民经济发展和国防建设对有色金属新材料的要求,大力进行科技攻关研究,以缩短与世界水平的差距;三是加强对有色金属资源综合利用、再生回收、节水减排与节能降耗的新工艺新设备,以及前瞻性重大科技的研究。
近年来,我国有色金属工业改革与发展实践表明,凡是一体化的大型企业,拥有较强的技术进步实力,对资源有效利用能力较强,在市场竞争中表现出较强的生存能力,节水减排与节能降耗成就显著。
3)以节水减排、节能降耗为中心,适度发展。有色金属工业是高耗能产业。我国有色金属工业的年能源消耗总量已超过8000万吨标准煤,约占全国能源消耗的3.5%。其中铝工业万元GDP能耗是全国平均水平的4倍以上。如果我国有色金属工业继续把扩大生产规模放在发展的首要地位,随着产量的增长,能源消耗和污染物排放进一步增加将是确定无疑的,为实现国家控制的节水减排和节能降耗目标,一定要严格控制总产量,加快淘汰落后产能。今后几年原则上应不再核准新建、改扩建电解铝项目。严格控制铜、铅、锌、钛、镁新增产能。按期完成淘汰反射炉及鼓风炉炼铜产能、烧结锅炼铅产能、落后锌冶炼产能和落后小预焙槽电解铝产能。逐步淘汰能耗高、污染重的落后烧结有机铅冶炼产能。