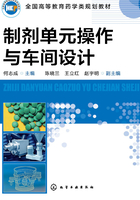
第二节 固体的粉碎
所谓粉碎,即在冲击、压缩、剪切及研磨力的作用下,使固体颗粒发生弹性或韧性破坏的操作。
一、粉碎的目的
制药生产中,常需将固体物料粉碎至一定粒径以供制备药剂使用。粉碎使药物的比表面积增加,有利于药物的溶解、吸收。药物的疗效与粒径的大小有直接关系。
某些固体药剂,诸如片剂、颗粒剂、胶囊剂等,往往需要数种物料进行混合。如将各种物料颗粒粉碎成粒径相近、甚至相同的细粒,更加易于混合均匀。最终制得的药品剂量更为准确,药效、质量更为稳定。
粉碎后的中药或动物腺体,其有效成分更易于提取。由于溶剂与固体间接触面积的增大,以及溶剂穿透距离的减小,缩短了药剂有效成分提取的时间。同理,一些液体药剂所需的固体药物溶解过程,亦因经粉碎使其溶解速率加快而缩短。
在固体制剂的制粒等操作中,如预先将原料适当粉碎,则更易于制粒,颗粒及片子的机械强度也会因此而提高。
对混悬型液体药剂中的固体粒子,减小粒径可明显提高其分散性、稳定性等物理性质。
针对药物制剂中的不同剂型,《中华人民共和国药典》(简称中国药典)作出的固体粒径相关规定见表1-4。为方便区分固体粒径的大小,中国药典还将固体粉末简单地分为六级,其规定见表1-5。
表1-4 中国药典关于固体粒径的规定

表1-5 中国药典关于固体粉末的六级规定

二、粉碎的机理
粉碎时,对物料的作用力主要有冲击、压缩、剪切、研磨等,一般情况下,上述几种力往往联合作用于物料。通常,粗碎以冲击力与压缩力为主,细碎以剪切力与摩擦力为主。
在外力的作用下,物料的内部可产生压缩、拉伸、剪切等各种应力。在应力超过临界值(一般为弹性极限)时物料破碎或发生塑性变形,当塑性变形达到一定程度后破碎。物料在弹性变形范围的破碎称为弹性破坏(或脆性破坏),塑性变形之后的破坏称为韧性破坏。
理论上,在外力作用下,物料内部的应力超过其本身分子间引力,物料才能破碎。但因物料内部构造上存在固有缺陷,物料破碎时实际的破坏强度有时仅是理论破坏强度的1‰~1%。
脆性破坏一般显示于物料内部存在的微小裂缝,当裂缝处产生的应力集中超过了物料的破坏强度即引起破碎。
在物料的破坏中,外力首先作用于物料的突出点上,局部产生很大的应力和温度,迅速导致内部生成多处小裂缝,随着裂缝的成长、传播,最终使物料破碎。
细粉研磨需要很大能量,其中一些用于产生新的表面,而更多的能量则用来产生新的裂纹。
粉碎机中的物料只有一部分因受到足够的外力而破碎,但另一些物料因接受的外力不足而不能破碎。其余的能量消耗在未粉碎粒子的弹性变形,物料在粉碎室内的迁移,粒子之间及粒子与粉碎机之间的摩擦生热、振动与噪声,电机与传动装置的损耗等方面。所以,粉碎机的效率很低(仅有0.1%~0.2%)。
如物料粉碎时的受力变形未超过弹性极限,则只能产生弹性变形,当外力移去后物料又恢复到原来状态,变形机械能以热量显现出来。若物料的受力变形超过弹性极限,则物料将发生塑性变形,当超过断裂极限,则物料破碎,所释放的能量一部分作为新的表面能量,其余的能量表现为热量。
粉碎过程粒度的变化情况如图1-9所示。图中粒度的分布以被粉碎物料的粒径关于粉碎时间的函数表示。原始的粒度分布呈比较宽的单峰型,随着粉碎时间的延长,该峰逐渐减小并且在左侧产生第2个峰。随着生成小粒子的增多,第2个峰逐渐增高,直至第1个峰消失。此时,只剩下一条单峰曲线。

图1-9 粉碎中的粒径频率曲线变化
如以图1-9下端的初始线为物料的粒径频率曲线,以其顶端的终态线为粉碎产品要求的粒径频率曲线,则可将物料试样在粉碎机中按不同的时间进行粉碎并作出其频率曲线,直至与终态线重合为止。此时将所有粉碎时间加在一起,即可得出该物料最适宜和最经济的粉碎条件——最佳粉碎操作时间。
三、粉碎的能量定律
(一)能量理论
实验证明,粉碎中粒径变化所需要的能量符合Lewis定律:
(1-8)
式中,E——粉碎单位质量物料所需的能量,kJ/kg、kW·h/t;d——物料的粒径,μm、mm等;n——与物料性质及粉碎方式有关的常数;C——积分常数(单位取决于E、d)。
(二)能量计算
1. Rittinger方程
该方程依据Rittinger理论(表面积理论):粉碎所需的能量与新产生的表面积成正比。此时式(1-8)中,C=CR、n=2,代入积分并整理得
(1-9)
式中,CR——Rittinger系数。
2. Kick方程
该方程依据Kick理论(体积理论):粉碎所需的能量与粉碎前后粒子的粒径之比成对数比例。此时式(1-8)中,C=CK、n=1,代入、积分并整理得
(1-10)
式中,CK——Kick系数。
3. Bond方程
该方程依据Bond理论:粉碎所需的能量与粉碎后粒子表面积与体积之比的平方根成正比。此时式(1-8)中,C=CB、n=3/2,代入积分并整理得
(1-11)
式中,CB——Bond系数。
一般情况下,Rittinger理论多用于细碎,Kick理论多用于粗碎。由于Bond理论综合了前两者,所以得以广泛应用。为方便使用,需作一些简化。式(1-11)经整理可变成下式:
(1-12)
式中,d1/d2——粉碎比。
当d1≫d2时(通常如此),式(1-12)简化为
(1-13)
如果有d2=100μm,代入式(1-13)并整理得
(1-14)
将式(1-14)代入式(1-11)得
(1-15)
式中,d1,d2——粉碎前后粒子的粒径,μm;Ei——功指数,kJ/kg、kW·h/t。
Ei的物理意义为:将单位质量某物料从较大粒径粉碎至100μm所需的能量。对不同的物料,其值可由试验测得。计算中,对没有功指数的物料,也可用硬度相近物料的已知值代替。表1-6中列出的是几种常见物料的功指数。
表1-6 常见物料的功指数

【例1-1】 某片剂车间粉碎岗位有300kg待处理物料,硬度与黏土相近。如将其从150μm粉碎至20μm。略去其他能耗,计算所需能量(kW·h)。
解:根据kJ/kg,式中d1=150μm,d2=20μm。由表1-6查黏土功指数Ei=28.2kJ/kg,代入上式得
粉碎300kg物料所需能量为300×40=12000kJ,换算1kJ=1k(J/s)·s=1kW·(1/3600)h=1/3600kW·h,所以
12000kJ=12000×(1/3600)=3.33kW·h
即完成此操作所需的粉碎能量为3.33kW·h。
四、粉碎操作
(一)自由粉碎与闭塞粉碎
粉碎机内物料的滞留对粉碎效果影响很大。在粉碎过程中,若将达到规定粒度的细粉及时移出,则称为自由粉碎。反之,若细粉始终保持在粉碎系统中,则称为闭塞粉碎。在自由粉碎过程中,细粉的及时移出可使粗粒有充分的机会接受机械能,因而粉碎设备所提供的机械能可有效地作用于粉碎过程,故粉碎效率较高。而在闭塞粉碎过程中,由于细粉始终保持在系统中,并在粗粒间起到缓冲作用,要消耗大量的机械能,导致粉碎效率下降,同时产生大量的过细粉末。
用于自由粉碎的设备都装有筛网或筛板,而用于闭塞粉碎的设备则没有。一般情况下,闭塞粉碎只适于小量物料并需要一次性完成的粉碎操作。
(二)循环粉碎与开路粉碎
在粉碎产品中存有尚未充分粉碎的物料,需经筛选将过大的物料筛出返回并进行再次粉碎,这种操作为循环粉碎,如图1-10(a)所示。若物料只通过设备一次,则称为开路粉碎,如图1-10(b)所示。

图1-10 循环粉碎与开路粉碎
循环粉碎通常由粉碎机和筛组成的机组完成,而开路粉碎则由粉碎机单独完成并限于在要求不高的粉碎操作中采用。
(三)干式粉碎与湿式粉碎
通过干燥处理,使药物中的含水量降至一定限度后再进行粉碎的方法,称为干式粉碎。
在采用球磨机粉碎的操作中,物料粉碎至一定粒径以下时,内壁及球的表面会黏附一层微小粒子,减弱了粉碎中的冲击作用,使操作变得无效。在此场合可加入液体形成浆状物料,确保粉碎得以进行,此种加入液体的粉碎方式称为湿式粉碎。湿式粉碎还可用于粉碎刺激性较强的物料、有毒药物及对产品细度要求较高的药物。
对热敏性物料,在采用干式粉碎操作时要限制其干燥温度的上限;而对湿敏性物料,不宜采用湿式粉碎。
(四)低温粉碎
利用物质在低温下脆性较大的特点,将物料或粉碎机进行冷冻后再用于粉碎的方法称为低温粉碎。
低温粉碎可采用将原料冷冻或使干冰、液态空气、液氮等与物料混合的方式进行,也可通过向粉碎机夹层通入冷冻剂来实现。
对于粉碎热敏性、热塑性、强韧性、挥发性及软化点或熔点较低物料的场合,均可采用低温粉碎。
由于低温粉碎操作成本较高,不宜用于低价值物料的粉碎。
(五)混合粉碎
将两种或两种以上物料混合后再粉碎的操作方法称为混合粉碎。将单独粉碎时必须在低温下进行的热塑性物料与非热塑性物料混合粉碎,可克服前者的粘壁及附聚现象。但由于各种物料的硬度、混合比有所不同,混合粉碎时各种物料的粉碎程度可能会有差别,所得粒径可能不大一致。
为减少粉碎过程物料的黏附及附聚现象,可在物料中加入少量添加剂(或称粉碎助剂)。例如在干式粉碎中加入硬脂酸镁、硬脂酸锌等硬脂酸金属盐、粉状无水硅酸或含水硅酸等;在湿式粉碎中加入水、表面活性剂等。
由于吸附作用而使表面能降低及粉碎助剂分子的楔入效应等,可能会使粉碎助剂的作用变得不大明显。
另外,混合粉碎不能用于非同一配方物料的粉碎。
(六)超微粉碎
普通的粉碎方法可将固体药物粉碎至75μm左右,而超微粉碎则可将固体药物粉碎至5μm左右。中药材的细胞直径一般在10~100μm,运用超微粉碎技术,可以将原生药粉碎至5~10μm以下,对一般药材细胞的破壁率可达95%以上。对中药材的超微粉碎又称为细胞级的微粉碎,是一种以动植物类药材细胞破壁为目的的粉碎操作。所得细胞级微粉制成的中药称为细胞级微粉中药,即微粉中药。此外,中药材在细胞级的超微粉碎中,与细胞尺寸相当的虫卵也会因破壁而被杀死,从而可减少虫害对药材的影响,降低中药的毒副作用。
五、粉碎机
(一)粉碎机的分类
粉碎机的分类方法很多,最普遍的一种是按产品粒度进行分类。由数毫米至数十毫米为粗碎设备,数百微米的为中碎设备,数百微米至数十微米的为细碎设备,而数微米以下的则为超细碎设备。
也可按物料粉碎中所受的外力将粉碎机分类:以压缩力为主的为压缩型粉碎机,以冲击作用为主的为冲击型粉碎机,以剪断力作用于物料的为剪断型粉碎机,以磨削作用于物料表面层的为摩擦型粉碎机等。
还可按粉碎机构造特征分类:如颚式、偏心旋转式、滚筒式、锤击式、流能式粉碎机等。
每种粉碎机都有其特点及适用范围,选择中要从工艺要求及物料性质两方面考虑。
(二)冲击式粉碎机
在冲击式粉碎机的高速转轴上安装有固定或可运动的部件,对物料主要作用为冲击力。在制药工业里,物料的中碎至超细碎操作中几乎皆可使用。冲击作用可使脆性物料得到很好的粉碎,粉碎部件的边缘锋刃亦可粉碎韧性物料。常见冲击式粉碎机有锤击式、轴流式及回转盘式等。
1.锤击式粉碎机
一般由进料器、衬(牙)板、锤头、筛网、圆盘等部件组成。其结构如图1-11所示。在旋转的圆盘上安装有数个可自由摆动的锤头,机壳内的上部装有可更换的牙板,下部装有筛板。工作时,物料从锤头高速旋转的侧向投入,高速旋转的圆盘带动其上的T形锤对固体药物进行强烈锤击;物料经过锤头的冲击、锤头边缘的切割以及衬板的撞击等被粉碎;粉碎后的微细颗粒通过底部的筛孔出料,粗料被筛网截留机内继续粉碎。产品的粒径与锤头旋转速度及筛板孔径有关。转速如低于某一临界速度时,锤头不能起到冲击作用。显微镜下所形成的粒子呈球状,说明粉碎主要是摩擦作用(冲击所形成的粒子呈不规则形状)。机底的筛由金属板开孔而成,被粉碎粒子的运动受离心力与重力的双重影响。粒子通过筛孔时,粒径一般要小于筛孔的尺寸。转轴转速越高,所获粒子的粒径越小。在转速和孔径一定的条件下,筛子的厚度越厚,所得粒径也越小。如图1-12所示。圆孔形筛子强度高,但易堵塞,多用于纤维粉碎。人字形开孔多用于结晶物料,若其开孔宽度等于圆孔直径,则所通过的物料粒度会比圆孔大。人字形开孔不宜用于纤维物料,因纤维可产生顺缝隙阻塞,致使所得粒径不均。

图1-11 锤击式粉碎机
1—加料斗;2—螺旋加料器;3—转盘;4—锤头;5—衬板;6—外壳;7—筛板

图1-12 锤击式粉碎机转速、筛板厚度对产品粒径的影响
锤击式粉碎机的优点是结构紧凑,操作安全,维护方便,粉碎能耗小,生产能力大,且产品粒度比较均匀。缺点是锤头易磨损,筛孔易堵塞,过度粉碎的粉尘较多。锤击式粉碎机常用于脆性药物的中碎或细碎,但不适用于黏性固体药物的粉碎。
实际生产中,会发生粉碎产品不合格(粒径增大)和产量下降的情况,应根据锤击式粉碎机的工作原理加以分析判断。
影响粒径增大有两方面问题:一是转盘转速下降造成的锤头打击力下降,颗粒在重力作用下垂直运动增强;二是筛板受损变薄,在颗粒运行方向上的孔径增大,大颗粒自然会漏跑出来混入产品中。解决第一个问题,需要找出影响转速下降的原因并给予解决,如电机与转盘之间的传动机构松动(固定螺栓松动,轴间距变小)或老化(皮带轮的皮带松动、老化,产生打滑丢转)等;解决第二个问题,则需要更换筛板。
影响产量下降也有三方面的问题:一是锤头磨损,造成有效打击的频率下降,产量自然下降;二是衬板上的板牙磨损,剪切和冲突的效果下降,产量自然也会下降;三是部分筛孔受堵,合格粒子不能迅速排除。解决第一个问题,需要更换锤头;解决第二个问题,需要更换衬板;解决第三个问题,需要清理筛板。
2.轴流式粉碎机
其粉碎原理与锤击式粉碎机相似,其结构如图1-13所示。在水平旋转轴上通过刀盘固定5组刀片,其中正刀片4组,斜刀片1组,在转轴后端装有1个风轮。正刀片各组之间均有1个圆形挡盘,当轴高速旋转时,由于风轮的作用,物料和空气同时进入机内。物料受到刀片与衬板之间产生的冲击和剪切作用而粉碎,然后由空气夹带着自出料口排出。

图1-13 轴流式粉碎机
1—壳体;2—水冷夹套;3—刀盘;4—正刀片;5—挡盘;6—斜刀片;7—风轮
轴流冲击式粉碎机所粉碎物料的粒度可以由调节刀片与衬板之间的间隙来调整。由轴流式粉碎机所组成的粉碎机组如图1-14所示。物料由斗式提升机1提升并投入到储料斗2中。电磁振动给料器3将物料连续定量地加入粉碎机4进行粉碎。被粉碎的物料由空气夹带进入圆盘筛5。细粉与空气通过圆盘筛进入旋风除尘器6进行分离。未被分离的细粉在脉冲布袋除尘器8中进一步分离,净化的尾气由引风机9排空。由旋风除尘器及布袋除尘器所分离出的细粉在混合槽7中混合,再由电磁振动卸料器10出料。被圆盘筛5分离出的粗粒子重复进入粉碎机被再次粉碎。

图1-14 粉碎机组
1—斗式提升机;2—储料斗;3—电磁振动给料器;4—粉碎机;5—圆盘筛;6—旋风除尘器;7—混合槽;8—脉冲布袋除尘器;9—引风机;10—电磁振动卸料器
该机适用于化学药品、中成药材及纤维质物料(如植物根茎)等的粉碎。
3.回转盘式粉碎机(常称万能粉碎机)
万能粉碎机主要由回转盘、固定盘及筛板等组成,其结构如图1-15所示。

图1-15 回转盘式粉碎机
1—出粉口;2—环形筛板;3—水平轴;4—运动冲击柱;5—加料斗;6—固定冲击柱
该机在高速旋转的圆形转盘上固定有若干运动冲击柱。与回转盘相对应的是固定盘(一般以粉碎机的盖板作为固定盘),固定盘上装有固定冲击柱,且与转盘上的冲击柱交错排列,如图1-15所示。
工作时,物料由加料斗5加入,从机器中心部位沿水平轴3进入粉碎机。在离心力的作用下,物料被甩向外壁,由内到外,不断被各圈运动与固定冲击柱4、6粉碎,越到外圈,冲击柱的圆周速度越大,物料所受的冲击力也越大。物料最后达到外壁,细粉经环形筛板2由粉碎机底部出粉口1出料。
操作时,应先开启机器空转,至高速转动后再加物料,以免因药物固体阻塞于钢柱之间而增加电机的启动负荷。
回转盘式粉碎机的优点是适用范围广,适宜粉碎各种干燥的非组织性药物,如中草药的根、茎、皮及干浸膏等,但不宜粉碎腐蚀性、剧毒及贵重的药材。此外,由于粉碎过程会发热,也不宜粉碎含有大量挥发性成分或软化点低且黏性较大的药物。
4.球磨机
球磨机是一种常用的细碎设备,在制药工业中有广泛的应用。球磨机的主要部件是一个水平放置、内装瓷制或钢制圆球的圆筒——球磨罐。球磨罐由传动轴带动旋转,如图1-16(a)所示;也可靠胶轮与罐体之间的摩擦力旋转,如图1-16(b)所示。球磨的粉碎作用如图1-17所示。若球磨罐缓慢转动时,球在罐内阶梯式地滚落,物料的粉碎主要是靠球体间摩擦力的作用。

图1-16 小型球磨机
1—球磨罐;2—套筒;3—减速机;4—机座;5—胶滚;6—机架

图1-17 球磨机中物料与球的运动状态
1—罐体;2—球;3—物料
转速提高后,球体受罐壁摩擦力拖拽而被抛升至空中,呈抛物线自由落下后砸向物料,物料此刻的粉碎是冲击与摩擦力联合作用的结果。粉碎过程中,研磨效果随转速增大而下降,如转速过大,不仅会加剧罐内壁的损伤,还容易造成球体的破碎。若转速增大至某临界值时,离心力将起主导作用,球和物料在离心力的作用下随罐体一起旋转,从而失去对物料的粉碎作用。
球体开始跟随罐体旋转的转速称为罐体的临界转速,可由式(1-16)求得:
(1-16)
式中,nc——临界转速,r/min;D——罐体直径,m。
球磨机的工作转速n通常是临界转速的60%~85%。一般取:
(1-17)
通过改变球径,可以得到不同粒径的产品。一般认为,最适宜球径DE应与物料粒径d呈如下关系:
(1-18)
对软质物料K=35;对硬质物料K=55。
使用小直径的球可得较小粒径的粉碎产品,但小球不易将物料中的大粒子粉碎,因而生产能力较低。
加料量过多或过少,均会影响球磨机的粉碎效果。球体的装入量一般为罐内容积的30%~50%,物料的加入量以能否全部充填于球间的空隙为度。球体的密度对球磨机的生产能力及产品粒度均有影响,建议使用密度较大的钢球。但在物料不允许有铁混入的场合须使用瓷球。
图1-18所示的是一台连续式球磨机。罐体内设有3个侧壁有筛孔的粉碎室,物料由一端加入,在另一端出料。室中放置的球体由进料端至出料端,依次减小,借此可将较大粒径的物料依次粉碎至很细。

图1-18 连续式球磨机
1—带筛孔的壁面;2—球
近来小型振动式球磨机得到广泛应用,该机可将物料粉碎至数微米。图1-19所示为振动式球磨机的两种结构。其工作原理是以振动代替前述球磨的罐体的旋转运动。振动由偏心振动块和弹簧产生,振幅大约4mm,频率为1500~2500次/min。罐内球体在振动下自器底以抛物线轨迹向上运动,在其落下时与上升的球体相遇,故其粉碎作用仍属于冲击压缩型粉碎。

图1-19 振动式球磨机工作原理
1—弹簧;2—振动块;3—电机
与普通球磨机相比,振动式球磨机粉碎速度快,适用于物料的细碎。但其构造复杂,对机械部件的强度和加工要求较高,不易大型化。与罐体只有上下运动的振动球磨相比,既有纵向运动又有横向运动的振动球磨粉碎速度更快,故罐体以螺旋状回旋振动为优。
对于少量物料的快速粉碎,可采用高速回转球磨机,其结构型式见图1-20。在工作盘1上装有4只球磨罐2,当工作盘旋转时,带动球磨罐围绕同一轴心作自转运动。在离心力的作用下,罐内的球体不断将物料粉碎。由于工作盘旋转,球磨罐可以在比临界转速高得多的转速下旋转,故粉碎时间可由数十小时缩短至数十分钟。这种球磨机粉碎效率较高,但结构复杂且仅适宜于少量物料的细碎。

图1-20 高速回转球磨机
1—工作盘;2—球磨罐
球磨机结构简单,运行可靠,无需特别管理且可密闭操作,因而操作粉尘少,劳动条件好。球磨机常用于结晶性或脆性药物的粉碎。密闭操作时,可用于毒性药、贵重药以及具有吸湿性、易氧化性和刺激性药物的粉碎。球磨机的缺点是体积庞大,笨重;运行时有强烈的振动和噪声,需有牢固的基础;工作效率低,能耗大;此外,研磨介质与罐体衬板的损耗较大,需要定时检修。
5.流能磨
利用高压气体自喷嘴喷出的动能将粒子加速,使粒子之间或粒子与器壁间碰撞而将物料粉碎的设备称流能磨。工作气体可采用压缩空气或高压过热蒸汽。流能磨适用于物料的细碎或超细碎,特别是由于焦耳-汤姆逊冷却效应,在粉碎过程中温度几乎不升高是流能磨的一个特点,因而适用于热敏性药物,如抗生素、酶等的粉碎。流能磨的主要缺点为能耗较大,故物料应预先在其他粉碎设备预粉碎后再采用流能磨细碎。
流能磨型式较多,图1-21为微粉磨的工作原理。在空气室1内壁装有数个喷嘴2,高压空气经喷嘴高速喷入粉碎室3,物料由加料口被空气引带进入粉碎室,再被由喷嘴喷出的高速气流吸入并被加速到50~300m/s。物料因受到高速气流的剪切及粒子间的相互撞击作用而被粉碎。被粉碎粒子到达靠近内管的分级蜗4处,较粗粒子再次被气流吸引并继续被粉碎,空气夹带细粉通过分级蜗由内管出料。

图1-21 微粉磨
1—空气室;2—喷嘴;3—粉碎室;4—分级蜗
微粉磨的流程如图1-22所示。压缩空气由压缩机1、经空气冷却器2、空气贮罐3、过滤器4等,在分水、分油及除尘后成二路进入微粉磨5。物料由料斗6经定量加料器7被压缩空气引射进入微粉磨。粉碎后的微粒由底部出口管进入旋风分离器8得到成品。若需重复粉碎,可通过旁通管重新进入微粉磨,直至粒度达到要求为止。尾气进入脉冲袋滤器9捕集细粉后放空。

图1-22 微粉磨流程
1—压缩机;2—空气冷却器;3—空气贮罐;4—过滤器;5—微粉磨;6—料斗;7—定量加料器;8—旋风分离器;9—脉冲袋滤器
如图1-23所示的轮形流能磨是流能磨的另一种型式。物料被压缩空气引射进入磨的下部,压缩空气通过喷嘴2进入粉碎室3,物料被高速气流带动在粉碎室内上升的过程中相互碰撞或与器壁碰撞而粉碎,压缩空气夹带细粉由出料口4进入旋风分离器及袋滤器,较大颗粒的物料由于离心力沿磨的外侧而下,重复被粉碎为细小颗粒。

图1-23 轮形流能磨
1—加料口;2—喷嘴;3—粉碎室;4—出料口
6.乳钵研磨机
研钵内,靠研磨头的回转运动将物料粉碎,并可用干磨或水磨方法操作。其粉碎作用主要是靠研磨头的摩擦,设备适用于少量物料的细碎或超细碎。目前多应用于中药材细料(麝香、牛黄、珍珠、冰片等)的研磨和各种中成药药粉的套色及混合等。其缺点是粉碎效率较低。
乳钵研磨机的构造示于图1-24,研磨头1在研钵2内沿底壁作一种既有公转又有自转的有规律的研磨运动,并依此将物料粉碎。其公转、自转转速分别为100r/min和240r/min。操作时将物料置于研钵后将研钵上升至研磨头接近钵底,调整好位置即可进行操作。研钵通常具备升降和翻转功能,研磨及卸料都很方便。

图1-24 乳钵研磨机
1—研磨头;2—研钵
固体粉碎操作已在国民经济的许多部门得到广泛应用,相关的要求也不尽相同。表1-7所示为物料性质与粉碎方式的关系。对于制药工业而言,所使用的粉碎设备还应注意如下的特点:
表1-7 物料性质与粉碎方式的关系

注:∨∨—适宜;∨—有条件的适宜;×—不适宜。
①对粉碎产品的质量要求高,故粉碎设备的材质应尽量采用防腐材料,应选用对粉碎产品无污染并符合药品生产质量管理规范(GMP)要求的设备;
②同时规定粒径的上、下限,并且粒径分布范围较窄;
③较多情况为小批量、多品种生产,且品种更换频繁;
④由于有机化合物熔点较低,粉碎过程中产生的温升可使物料发生熔融现象;
⑤物料中不耐热及不稳定的有机物较多,粉碎中的发热及由粉碎造成的物料比表面积增大会降低其化学稳定性;
⑥粉碎柔韧性较大的动植物性物料时,由于物料对粉碎的抵抗力较大,即使重复粉碎也很难得到细小的粉末。
不同粉碎方式的粉碎机性能及其适用范围如表1-8所示。
表1-8 不同粉碎方式的粉碎机性能及其适用范围
