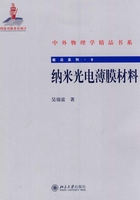
§2.2 溅射法
经加速的离子束轰击固体材料表面,打出中性原子或离子,这就是溅射.将溅射出来的原子沉积在基底上形成薄膜,这就是薄膜的溅射制备法.用溅射法制备薄膜与真空沉积法相比,其优点主要有:① 薄膜与基底的附着性好;② 对于熔点高的材料使用真空沉积法有一定困难,而溅射法就适合;③ 降低溅射气体的气压,可以使溅射沉积形成的粒子粒径小于真空沉积法,适用于某些特定要求的薄膜制备.
溅射设备基本组成如图2-4所示,它包括真空系统、高压源、被溅射靶材(靠近阴极)、溅射气体源、用于沉积薄膜的基底等.溅射气体一般是惰性气体,如Ar.但在反应溅射中,气体可以是需要形成化合物的某种气体源,例如,希望形成氧化物薄膜,则溅射气体选用O2.溅射时施加的高压一般在100~10 000 V,溅射气体在高压电极间产生辉光放电,被电离的正离子向阴极飞行,若阴极就是靶材(导电靶材),那么靶材表面原子被正离子溅射出来,那些到达基底的靶材原子沉积在基底上形成薄膜.高压源可以是直流的,也可以是交流的.
图2-4 溅射设备示意图
2.2.1 溅射的基本实验规律
1. 溅射阈能
溅射阈能是指随着入射离子的能量增加,开始发生靶材原子被溅射出来时的入射离子的能量.溅射阈能对低能区的溅射产额有很大的影响.表2-2是几种惰性溅射气体的正离子轰击金属靶材的溅射阈能数据[3].溅射阈能与靶材的升华热有关,例如W的升华热是8.82 eV,它的溅射阈能是30~35 eV,W的溅射阈能值大约是其升华热的4倍.
表2-2 金属靶材的溅射阈能(单位:eV)
(续表)
2. 溅射产额(溅射系数)
溅射产额(溅射系数)S以每个入射离子所溅射出的靶材原子数表示.实验经验告诉我们,S与入射离子能量E0的x次方成正比,且与入射离子平均自由程λ的倒数成正比[4,5]:
式中k为比例系数,M1和M2分别为入射离子质量和被溅射原子质量,且
式中n0为靶材原子数密度,R为碰撞截面半径.式(2-1)中的k可表达为
式中a和b为常数,可由实验经验确定,Eb为靶材的原子结合能.一般
式(2-4)对能量为10~60 keV的入射离子溅射较为适用,误差一般小于20%,但对金属氧化物的靶材,其误差较大,因为金属氧化物的溅射系数一般比相应金属的要小.
若入射离子能量在keV数量级,则多数金属靶材的S为1~10.
3. 溅射产额与入射离子能量的关系
入射离子的能量增加,将产生两个效应:① 对靶材碰撞能量增大,使靶材中可移动原子数目增多,离开表面的原子也相应增多,这样,S上升;② 打入靶材内的射程增大,使靶材中可移动原子产生于深处,这些可移动原子难以到达表面和离开表面,这样,S下降.这两种效应的综合结果是,S与入射离子能量的关系曲线有一最大值.
图2-5是Cu的三个不同晶面,即(111)面、(100)面和(110)面,对应的溅射产额S与入射离子Ar+能量的关系[6].由图中可看出,从一定阈值开始,随着入射离子能量的增加,S也增加,逐渐达到饱和值后下降.
图2-5 Cu的不同晶面对应的溅射产额与入射离子能量的关系
4. 溅射产额与入射离子原子序数的关系
溅射产额与入射离子原子序数有周期性关系.惰性气体作为入射离子时的溅射产额高;位于元素周期表中间部位的那些元素(如Al,Ti,Zr及稀土元素)作为入射离子时的溅射产额低.从总的趋势来说,随着入射离子原子序数的增加,溅射产额增大.图2-6是当入射离子能量为4.5 keV时,Ag,Cu和Ta靶材的溅射产额与入射离子原子序数的关系曲线[2].
图2-6 溅射产额与入射离子原子序数的关系
5. 溅射产额与靶材原子序数的关系
溅射产额与靶材原子序数的关系也呈现周期性.这种周期性体现在靶材元素的升华热与溅射产额的关系,靶材的升华热越小,原子结合能就越弱,其溅射产额就大.图2-7给出了Ar+作为入射离子,在能量为400 eV时对一些元素的溅射产额[7].表2-3是以不同能量入射时Ar+对一些靶材材料的溅射产额数据[8~10].
图2-7 溅射产额与靶材原子序数的关系
表2-3 Ar+对一些靶材材料的溅射产额
*该数据引自参考文献[10].
由于溅射产额与靶材中的元素有很大关系,若靶材是由多种元素组成的,则靶材表面在离子轰击下,不同元素被溅射出来的多少就不同了,这就是“择优溅射”问题.“择优溅射”会使离子谱分析变得复杂,这是必须注意的.
6. 被溅射出原子的能量分布
被溅射出原子的平均能量一般为几个电子伏,多数为1~10 eV,几乎与入射离子能量无关,只是会随入射离子能量的增加而稍微增加一些.入射离子的能量到哪里去了呢?它主要消耗在靶材里了,所以在溅射时靶材温度会升高.图2-8(a)是900 eV能量的Ar+入射Al,Cu,Ti和Ni时被溅射出原子能量E的分布[11];图2-8(b)是80~1200 eV能量的Kr+入射,从Cu的[110]方向被溅射出原子能量E的分布[12].
图2-8 被溅射粒子的能量分布
(a)900 eV能量的Ar+入射Al,Cu,Ti和Ni时被溅射出原子的能量分布;(b)80~1200 eV能量的Kr+入射,从Cu[110]方向被溅射出原子的能量分布
2.2.2 磁控溅射
为了提高溅射效率,可以在溅射设备中加入磁场.溅射气体被电离后轰击靶材将产生一些运动的电子,电子在磁场中受到洛伦兹力的作用而作曲线运动,电子运动路程增加使得电子与溅射气体碰撞的概率加大,溅射气体的电离效率提高,因此溅射效率也随之提高.
常见的磁控溅射设备主要有圆筒式结构和平面式结构,如图2-9所示.这两种结构中的磁场方向都基本平行于阴极表面,将电子运动有效地控制在阴极附近.磁控溅射工作时的参数一般是:加速电压为300~800 V,磁场为50~300 Gs[1],溅射气体压强为0.1~1 Pa,电流密度为4~60 mA/cm2,功率密度为1~40 W/cm2,薄膜沉积速率为100~1000 nm/min.
图2-9 磁控溅射设备结构示意图
(a)圆筒式结构;(b)平面式结构
2.2.3 射频溅射
在溅射靶上施加高频交流电压(频率一般为5~30 MHz),即为射频溅射.国际上通常采用的射频溅射频率多为美国联邦通讯委员会(FCC)建议的 13.56 MHz.
在射频电磁场作用下,电子在到达阳极之前在阴、阳极之间的空间来回振荡,从而有更大的可能与气体分子碰撞而产生电离,提高了离子产生效率,因此射频溅射可以在较低气压(如2×10-2 Pa)下进行.射频溅射的另一好处是,高频电磁辐射可以通过感应使气体电离,而不必在溅射系统内部附加电极,这样在反应溅射中就不会发生热丝因系统环境而受到污染或破坏的问题.
射频溅射的装置有多种类型,图2-10所示的装置只是示意图.把高频线圈围绕在放电室四周,利用电磁感应形成等离子体,靶材(阴极)与基底放在放电最强区域以外,但阳极放置在辉光放电区域内.当靶材偏压为500 V,射频功率为200 W时,沉积速率可达6 nm/min.
图2-10 射频溅射等离子体装置示意图
有一种装置是高频电压直接加在阴极而叠加于直流偏压上,如图2-11所示.它的特点是可以溅射任何材料(包括导体、半导体和绝缘体材料)做的靶.
图2-11 射频溅射的一般系统
图2-12说明了靶上负偏压形成过程[13].图2-12(a)是辉光放电的探极特性,由于电子的徙动率高于离子的徙动率,因此当靶电极通过电容耦合加上射频电压时,到达靶上的电子数目将大于离子数目,从而逐渐在靶上有电子积累,使靶材带上一个直流负电压.在平衡状态下,靶上的负电压使得到达靶的电子数目和离子数目相等,如图2-12(b)所示,从而在通过电容与外加射频电源相连的靶电路中就不会有直流电流流过.实验表明,靶上形成的负偏压的幅值大体上和射频电压的幅值差不多.对于绝缘体靶材,正是由于靶面上的负偏压,使得正离子能不断地轰击它而溅射,在射频电压的正半周期间,电子对靶材的轰击又能中和积累在靶面上的正离子.
图2-12 射频溅射中负偏压形成原理
(a)辉光放电的探极特性;(b)负偏压幅值
射频溅射不需要用次级电子来维持放电.但是,当离子能量高达数千电子伏时,绝缘体靶材上发射的次级电子数量也相当大,又由于靶材具有较高负电压,电子通过辉光放电的暗区得到加速,将成为高能电子,并轰击基底导致基底发热、带电而损害薄膜质量.为此,需将基底放置在不直接受电子轰击的位置上,或者利用磁场使电子偏离基底.
2.2.4 Ag-Cs2O光电薄膜溅射制备法
Ag-Cs2O光电薄膜一般用真空沉积法来制备,但为了提高近红外长波的光电灵敏度,需制备尺寸更小的Ag纳米粒子,溅射方法就提供了这样一种可能.
用于制备Ag-Cs2O光电薄膜的溅射装置由五部分组成:排气系统、充气系统、样品管、电源系统和测试系统.图2-13是溅射装置示意图.排气系统由机械泵、扩散泵、锆石墨泵组成.锆石墨泵是一种非蒸散型常温消气剂[14],对惰性气体没有吸收能力,而对N2,CO,CO2,O2,H2和水蒸气等都有很好的吸收能力,因此它可以提高系统的静态真空度.充气系统包括纯Ar气的充入控制以及纯O2气的产生和充入控制,在工艺步骤中,Ar气的充入、抽真空和O2的充入是交替进行的.O2可由KMnO4(高锰酸钾)加热到300 ℃分解得到:
图2-13 制备Ag-Cs2O光电薄膜的溅射装置示意图
1. 机械泵;2. 放气活塞;3. 低真空活塞;4. 扩散泵;5. 高真空活塞;6. 液氮冷凝捕集阱;7. 电离计规管;8. 热偶真空计管;9. 氧气活塞;10. 气体过滤板;11. 高锰酸钾;12. 隔离活塞;13. 锆石墨泵;14. 气体限量活塞;15. 氩气活塞;16. 高纯氩气瓶;17. 光电样品管;18. 铯支管;19. 烘箱;20. 复合真空计;21. 真空电离计;22. 排气台
图2-14是样品管管形示意图.
Ag-Cs2O光电薄膜溅射制备法工艺大致过程如下[15]:
(1)第一次溅射Ag,形成光透过率约为50%的薄膜;
(2)充入O2进行放电氧化,薄膜变得透明;
(3)第二次溅射Ag,使薄膜光透过率再次下降到约为50%;
(4)在150 ℃温度下进行Cs激活,监视热电流上升到最大,这时阴极已具有光电灵敏度;
(5)第三次溅射Ag,对薄膜进行敏化;
(6)经过O2敏化,光电积分灵敏度可以达到27 μA/lm.
这样一个工艺过程的优点是容易控制Ag,O和Cs三者的比例,成品率较高.
图2-14 用于溅射法制备Ag-Cs2O光电薄膜的样品管管形示意图
(a)侧视示意图(尺寸单位:mm);(b)顶视示意图1. 玻璃管;2. 银丝盘;3. 玻璃套;4. 玻璃挡板;5. 光电管阳极引线,也是溅射阴极引线;6. 接真空系统;7. 溅射阳极板(Ta片);8. 溅射阳极引线;9. 光电管阴极引线;10. 接铯支管