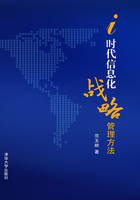
4.5 并行工程应用实施案例
4.5.1 波音公司的并行工程应用案例
资料分析表明,产品设计制造过程中存在着巨大的发展潜力,节约开支的有效途径是减少更改、错误和返工所带来的消耗。一个零件设计完成后,要经过工艺规划、工装设计、制造和装配等过程,在整个过程中,设计约占15%的费用,制造占85%的费用。过去飞机开发大都沿用传统的设计方法,按专业部门划分设计小组,采用串行的开发流程。大型客机从设计到原型制造多则十几年,少则七到八年。
波音公司在新型767-X飞机的开发中,全面应用CAD/CAM系统作为基本设计工具,使设计人员能够在计算机上设计出所有的零件三维图形,并进行数字化预装配,获得早期的设计反馈,便于及时了解设计的完整性、可靠性、可维修性、可生产性和可操作性。同时,数字化设计文件可以被后续设计部门共享,从而在制造前获得反馈,减少设计更改。表4-2列出了波音公司767-X开发所采用的技术与传统方式的比较情况。
表4-2 波音公司767-X开发方式与传统方式的比较

实现“设计—计划—制造—保障”过程的集成化产品开发对于波音每个机构或员工都是一个挑战。计算机技术的推广应用和其他新技术的逐渐发展应用,对波音公司原有的工作模式提出了迫切的改进需求。采用100%数字化产品设计预示着波音经营管理的巨大改革,但更多的是组织机构的改革,以适应计算机工具的应用要求和新的操作规程。概括地说,波音公司在新型767-X飞机的并行设计中采取了以下措施:
(1)按飞机的部件组成了两百多个集中办公的多功能产品开发队伍。设计制造团队是一个由设计、管理、协调、材料、财务等人员组成的独立团体,目的在于提高产品设计的可制造性,减少更改、错误及返工,实现设计的一次性成功。
(2)改进产品开发流程。在产品开发过程中,制定了集成化计划,该计划中包含了对设计、计划、制造、测试、飞机交付等过程的管理。在设计开发过程中进行自动超差控制,提供在线式电子化拒收单,管理整个拒收过程,提供统计控制数据并及时向上级报告。
(3)采用DFA/DFM等工具在设计早期尽快发现下游的各种问题。
(4)利用巨型机支持的产品数据管理系统辅助并行设计,保证并行、协同的产品设计,共享产品模型和设计数据库。
(5)大量应用CAD/CAM技术,做到无图纸生产。
(6)应用仿真与虚拟现实技术。
1.集成产品开发团队
767-X的产品开发队伍(IPT)是按功能划分的(图4-11),如电子IPT、机械IPT、结构IPT等。

图4-11 波音767-X集成产品开发团队的组织结构
波音公司建立IPT工作的目标是:
(1)提高质量:团队的每个成员均对用户需求和质量需求负责;
(2)降低成本:团队制工作方式显著减少了更改、错误和返工;
(3)缩短开发周期:通过增加预发布和并行协同工作,保证对用户需求和设计更改作出快速反应。
设计制造团队由各个专业的技术人员组成,在产品设计中起协调作用,最大限度地减少更改、错误和返工。设计制造团队的任务是进行飞机结构和主要系统设计。他们参与制造计划、工装设计、NC加工、用户服务等工作。设计制造团队从制造部门和其他小组获得可制造性和可维修性反馈信息,工装设计员利用数字化预装配工具检查零件-工装、工装-工装之间的配合和干涉情况,用户服务组利用3D/2D设计数据研制地面保障设备,出版相应的技术资料。在获得下游组织的反馈信息、完成零件设计和最终干涉配合检查后,进行零件模型的发图生产。
2.改进产品开发过程
为什么波音公司在过去的十多年中也采用了CAD/CAM系统却没有明显地加快进度、降低费用和提高质量呢?究其原因,是其开发过程及管理还停留在原有的水平上。波音767-X采用全数字化的产品设计,在设计发图前,设计出767-X所有零件的三维模型,并在发图前完成所有零件、工装和部件的数字化整机预装配。同时,采用其他计算机辅助系统,如用于管理零件数据集与发图的IDM系统,用于线路图设计的WIRS系统,集成化工艺设计系统,以及所有下游的发图和材料清单数据管理系统。由于采用了先进的计算机辅助手段,波音公司在767-X开发时改进了相应的产品开发过程,如在发图前进行系统设计分析,在CATIA上建立三维零件模型,进行数字化预装配,检查干涉配合情况,增加设计过程的反馈次数,减少设计制造之间的大返工。CAD/CAM系统的应用有效地减少了更改和设计返工的次数,设计进程也大大加快,由此而带来的效益远大于减少更改和返工所带来的直接效益。
767-X数字化产品设计活动起始于用户需求。当项目开发的任务单下发后,设计制造团队就开始安排第一阶段的工作任务,制造部门根据项目进度确定初步的生产周期,生产部门则制定各种生产计划。波音767-X研制中,对工程设计研制过程、数字化整机预装配过程、数字化样件设计过程、区域设计、设计制造过程、综合设计检查过程、集成化计划管理过程等飞机开发的主要过程进行了改进。限于篇幅,下面仅对工程设计研制过程进行详细的描述。
工程设计研制过程起始于3D模型的建立,它是一个反复循环的过程。设计人员用数字化预装配工具检查3D模型,完善设计,直到所有的零件配合满足要求为止。最后,建立零件图、部装图、总装图模型,完成2D图形并向制造部门和工艺部门发图。设计研制过程需要设计制造团队来协调,其主要步骤如下。
(1)建模:对飞机零件进行3D数字化设计,在飞机坐标系中建立初步模型,当设计定型后,设计出详细的零件图、部装图、总装图。
(2)共享:把3D零件图、部装图、总装图作为数字化预装配共享文件的输出,每个设计员必须及时将设计结果传送到共享数据库中与有关成员共享。
(3)检查:由于零件处在设计过程中,其定位尺寸可能会不断发生变化,因此应经常通过数字化预装配查阅有关零件位置的变动情况,保证各个部分设计的协调。
(4)分析:分析3D数字化模型,将分析结果连同存在问题的设计模型储存在反馈文件中,反馈给设计人员。
(5)检查数字化预装配数据、制造数据,获得早期的可制造性反馈信息,计划员、工程设计员、制造工程师共同解决干涉及可制造性问题,并把干涉模型或有关可制造性问题存放于制造反馈文件中。
(6)解决所有干涉配合问题,并根据工程分析的要求进行设计修改。设计更改的结果再次存入数字化共享文件,确保该文件中设计数据是最新结果。
(7)不断重复上述过程,直到设计满足要求为止。这一循环过程一直持续到零件数字化装配完成,且不产生干涉问题。在3D设计定型时,设计员完成2D设计,标注尺寸、附注及重要特性等。
(8)冻结:冻结有关数据集。
(9)修改:进一步修改数据集,如有必要,根据上述过程输入制造信息。
(10)发图:即释放相关数据集。
3.采用数字化技术,在设计早期尽快发现下游的各种问题
数字化整机预装配是在计算机上进行建模和模拟装配的过程,它根据设计员、分析员、计划员、工装设计员的要求,利用各个层次中的零件模型进行预装配,用于检查干涉和配合问题,这个过程以设计文件共享为基础。数字化整机预装配将协调零件设计和系统设计(包括管线、线路布置),检查零件的安装和拆卸情况,零件以3D实体形式进行干涉、配合及设计协调情况检查,利用整机预装配过程,全机所有的干涉能被查出,并得到合理解决。如波音757的1600~1720站位之间的46段,约1000个零件利用12个CATIA模型进行了数字化预装配。
利用数字化预装配过程,工程设计对所有设计干涉和配合情况进行检查,这使得后期设计更改次数大为减少。在波音飞机设计中规定数据集在没有进行最后的审批前不能发图,这一规定有利于降低项目风险,保证发图后无零件干涉情况的出现。
数字化整机预装配的应用将有效地减少因设计错误或返工而引起的工程更改,可以在发图前辅助设计员消除干涉现象。设计员能搜索并进入其他相关设计系统中检查设计协调情况。其他设计小组如工程分析、材料、计划、工装、用户保障等也陆续介入设计过程,并在发图前向设计员提供反馈信息。
4.大量应用CAD/CAM/CAE技术,实现无纸设计生产
(1)100%采用数字化技术设计飞机零部件
采用CATIA系统设计零件的3D数字化实体模型,支持在计算机上进行装配,检查干涉与配合情况,也可利用计算机精确计算重量、平衡、应力等零件特性。此外,还有多种优点:易于从实体中得到剖面图;利用数字化设计数据驱动数控机床加工零件;产品外形设计直观;产品插图也能更加容易、精确地建立;用户服务组可利用CAD数据编排技术出版物和用户资料。767-X中的所有零部件都采用数字化技术进行设计,所有零件设计都只形成唯一的数据集,每个零件数据集包括一个3D模型和2D图,提供给下游用户。针对用户的特殊要求,只对数据集修改,不对图纸进行修改。
(2)建立了飞机设计的零件库与标准件库
减少新零件的设计能极大地节约费用。基于这一认识,767-X开发中建立了大量的零件库,包括接线柱、角材、支架等。零件库存储于CATIA系统中,并与标准件库相协调,设计人员可以方便地查询零件库。充分利用现有的零件库资源能有效减少零件设计、工艺计划、工装设计、NC加工程序等环节的成本。标准件库包括紧固件、垫圈、连接件、垫片、轴承、管道接头、压板等,这些标准件存储于CATIA标准图库中。设计人员可直接从标准件库中选择所需的零件。
(3)采用CAE工具进行工程特性分析
包括应力分析、重量分析、可维修性分析、噪声控制分析等。
(4)计算机辅助制造与NC编程过程
计算机辅助制造过程通过提供可生产性输入和增加附加信息到数据库以改进工程设计,从而满足部装和总装要求。在工程发图前,NC程序员利用CATIA工具进行零件线架和表面的数控编程,必要时在计算机上模拟数控加工的过程,从而减少了设计更改、报废和返工,并缩短了开发周期。
(5)计算机辅助工装设计
工装设计人员利用3D零件数字化模型设计工装的3D实体模型或2D标准工装,保证零件基准,计算机系统存储有关工装定位数据。同时建立工装的数字化预装配系统,利用3D数字化数据集检查零件-工装、工装-工装之间的干涉与配合情况。工装数据集提供给下游的用户,如工装计划用于工装分类和制造计划,NC工装程序提供给NC数据集,用于NC验证或给车间进行生产。
5.利用巨型机支持的产品数据管理系统辅助并行设计
767-X采用巨型计算机建立了一个大型的综合数据库管理系统,用于存储和提供配置控制,管理多种类型的有关工程、制造和工装数据,以及图形数据、绘图信息、资料属性、产品关系、电子签字等,同时对所接收的数据进行综合控制。
管理控制包括产品研制、设计、计划、零件制造、部装、总装、测试和发送等过程,它保证将正确的产品图形数据和说明内容发送给使用者,通过产品数据管理系统进行数字化资料共享,实现数据的专用、共享、发图和控制。
在PDM系统管理下,数据集成为设计过程唯一的设计依据,数据集释放后进入数据库系统。对工程数据的修改需要有关人员的签字。数据集的发放过程是:首先,工程师将已验证的数据集准备好,并在发放期把它提供给释放单元。待释放的数据集包括一个数字化模型(3D实体图形、2D图形和下游需要的有关数据)、材料清单和一个在线的释放单元清单。仅有的纸上条文是列有由谁查阅在线数据集及进行电子签字的报告。为准备发图,数字化模型以只读格式共享,进行电子签字以及在线跟踪。当所有签字完成时,该模型将处于共享状态。其次,验证待释放数据集的完整性。最后,发图员在数据库中将该模型状态改为发图状态,释放相应的数据集进行发图。采用数字化产品设计的每个模型都有一个完整的零件号,以便图形在发放时进行跟踪检查。
6.并行工程技术在波音飞机开发中的应用效果
波音公司在767-X的开发过程中采用了“并行产品定义”的全新概念,通过优化设计过程,采用新的项目管理办法,改善设计,提高飞机生产质量,降低成本,改进计划,实现了三年内从设计到一次试飞成功的目标。并行设计技术的有效运用带来了以下几方面的效益:提高设计质量,极大地减少了早期生产中的设计更改;缩短产品研制周期,和常规的产品设计相比,并行设计明显地加快了设计进程;降低了制造成本;优化了设计过程,减少了报废和返工率。
波音公司于1991年开始开发新型的777双发动机大型客机。按照传统开发方法,波音777飞机的研发需要九年时间,预计研发费用120亿美元。波音公司在777的开发过程中沿用并扩展了并行工程的思想,应用了“并行产品定义”的概念,建立了世界第一个全数字化样机,全面采用数字化技术,实现了三维数字化定义、三维数字化预装配和并行工程,建立了全机数字样机,取消了全尺寸实物样机,使工程设计水平和飞机研制效率得到了极大的提高;大幅度降低了干涉、配合、安装等问题带来的设计更改,使研发成本降低了25%,制造成本降低30%~40%,产品开发周期缩短了40%~60%,出错返工减少75%,整个飞机从立项到首架交付只花了四年半时间,用户交货期也从18个月缩短到12个月。
4.5.2 并行工程在我国企业的应用效果
在国家“863”计划支持下,我国多家企业实施了并行工程,取得了良好的成果。在航天机电集团某型号产品的两个复杂部件中进行了成功的应用与验证,与这两个部件过去的开发模式相比,取得了三个方面的直接效益:
(1)总体设计周期压缩了60%,工程绘图周期从1~2个月减少为2~3周,工艺检查周期减少50%,更改反馈次数降低50%,工艺规划时间减少30%,工装准备周期减少30%,数控加工编码与调试周期减少50%。这些工作保证了两个复杂部件的总体开发周期均缩短30%。
(2)毛坯成品率由原来的30%~50%提高到70%~80%。
(3)降低产品成本20%。
齐齐哈尔铁路车辆(集团)有限公司应用并行工程改进了产品开发过程,降低了铁路货车产品设计、工装设计、工艺方案的返工次数,减少静强度、动力学试验次数一到二次,产品报价时间缩短50%,冲压件试制次数减少3~4次。避免了铸钢件制造较大的工艺调整,降低局部工艺调整50%,缩短铸钢件试制周期50天,总的产品开发周期缩短30%~40%。
海南新大洲摩托车公司,通过实施并行工程,快速研发出“四轮摩托车”新产品,使研发周期缩短40%~50%,使新产品提前五个月上市。新产品销往美国25000辆,当年为公司增加销售额2亿1千万元,增加销售收入1亿2千万元。在四轮沙滩车研制过程中,减少出错返工70%,实现了装配一次成功,减少直接损失每年700万元。四轮沙滩车的设计开发和小批试制周期从15个月减少到9个月。通过实施产品模型的数字化定义和合理化工程,将系列化产品的开发过程缩短50%,由过去的8个月缩短到3个月以内。通过建立各种设计指南、规范、标准件和通用件的优选原则和优选库的电子档案,提供方便、灵活的检索和查询,将摩托车零部件的通用化率提高了50%,即从原有的11%提高到16%,为企业节约开支200万余元。通过部品压缩,可节约存储、管理费每年100万元。