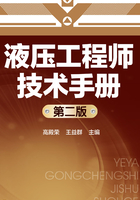
第三章 微流体技术
1 微流体力学
微尺度传感器和制动器依托于20世纪80年代后期发展起来的微机械工艺技术迅速发展,这些微型转化器与信号调节和处理电路集成后,组成了可执行分布式实时控制的微电子机械技术(MEMS)。这种性能为流体控制的研究开辟了崭新的领域。微小型化的尺度效应,微细加工工艺,微型机械材料和微型构件,微型传感器,微型执行器,微型机械测量技术,微量流体控制系统,微系统的集成与控制等八个方面成为MEMS的主要研究方向,微流体力学是其中一项重要的基础理论。
微流体与宏观流体的主要差别表现在微尺度效应,由于从宏观到微观尺度变化很大,因此流体在微观条件下的运动状态需要区别对待,使用在宏观条件下成立的假设和相应的方程来解释微观流体需要进行条件限制和修正,其过渡阶段仍可从经典流体力学中得到解释,但当特征尺度接近微米量级时,流体的流动特性,与宏观相比,发生了很大的变化,基于连续介质的一些宏观概念和规律就不再适用,黏性系数等概念也需重新讨论。由于尺度的微小,使原来的各种影响因素的相对重要性发生了变化,从而导致流动规律的变化。因此,确定微流体尺度等级的划分是一项紧迫的任务。
1.1 微流体尺度等级划分
研究小尺寸通道与宏观尺寸通道中流动现象的不同。首先要阐明关于通道尺寸的划分问题,但是研究者对于这一问题尚未形成统一的定论。Shah在定义小尺寸热交换器中指出通道尺寸小于6mm称为小尺寸;Kandlikar提出小尺寸界限为3mm,小于200μm的尺度称为微尺度。
另外,根据不同的描述流体特征的无量纲参数,对微尺度的界定也不同。Triple等人定义水力直径Dh小于拉氏常数时成为微尺度。拉氏常数定义为
式中,σ为表面电荷密度;g为重力加速度;ρl和ρu分别为液体密度和气体密度。
Kew和Cornwell基于拉氏常数提出Co常数(confinementnumber)作为小尺寸沟道直径的界限,则
可见,对微尺度等级的划分还未确定。现在一般将大于1mm的尺度称为宏观尺度,1μm~1mm的尺度称为微尺度。
1.2 微尺度流动的尺寸效应
在微尺度流动中,特征尺寸的减小对流动规律的影响体现在两种情况中:①流体运动的特征尺度减小到微米数量级时,支配流体运动的各种作用力发生了变化,在宏观流动中居于次要地位而被忽略的表面作用力超过了体力,而成为微流体的支配力,这意味着传统的宏观流体驱动技术以及研究方程在微流体中可能不再适用;②微米尺度范围内微管道具有极大的面积/体积比,例如对于1m尺度的常规流体,该比值为1/m,然而对于微米尺度来说,该比值变成106/m,这种现象被称为表面现象。该表面现象使得微流体呈现出与常规流体不同的性质,如牛顿流体在微管道中表现出的非牛顿流体性质,极大的表面积/体积比值还导致了电黏性效应、电双层效应、表面张力效应等。随着构件的特征尺度减小到微米数量级时,基于连续介质假设的纳维—斯托克斯方程不能处理微流体中壁面与流体间的速度滑移,固液界面的边界条件本身成为需要求解的变量。而且,微流体运动中出现了微流动表观黏度与体积黏度不一致等一些经典连续介质模型无法解释的现象。这说明在微米数量级流体条件下,由于固体表面分子力对液体分子的作用,使得微流体内部分子之间的作用力成为不可忽略的因素。
1.2.1 描述方程的适用性问题
用于描述宏观尺度流动的经典Navier-Stokes方程基于连续性假设,微尺度下,特征尺度与分子平均自由程相近或者小于分子平均自由程,流体质点的统计特性就可能受到质点内部个别分子行为的影响,因此依照现有的连续介质方程无法描述微尺度下的流动状态。在微尺度下,即使流体的连续性假设仍然存在,黏性耗散、热扩散、可压缩性、流动滑移等在宏观流动中往往忽略的因素在微尺度流动中的作用应该给予充分考虑。
在宏观条件下,流体黏度不变,而只与流体本身性质有关,在微观条件下,流体黏度受多方面因素的影响。Pfahler等人的实验结果显示,流体在不同截面形状管道中流动时,黏度各不相同,而且黏度与温度、压强有关,目前尚不能用量化方式准确表达黏度与各种因素的关系,但由于黏度成为管道尺寸、截面形状、温度、压强等的函数,在Navier-Stokes方程中,不能把黏度μ认为是常量,用N-S方程来解释微流体特性需要严格制其应用条件。对于μm尺度范围内的现象,分子动力学方程是比较合适的工具,它用于揭示那些量子力学效应不明显的物理现象的分子特征。分子统计理论如Boltzmann方程及直接Monte-Carlo模拟法可以提供分子碰撞动力学方面的知识。对于由量子效应明显的物理过程,则应采用量子分子动力学方法,并通过同时求解分子动力学方程及Schrodinger方程来加以分析。使用传统方程并加以适当修正,也是解决微尺度下流动问题行之有效的方法之一,但是每一次修正都需要有大量的实验对其进行验证。另一种可行的方法是使用基于“第一原理性方程”的分子模拟,如适用于微尺度下液体和密集气体流动的分子动力学模拟(MD)。
1.2.2 极大的表面积/体积比值
随着流动的特征尺度由cm~m量级减小到μm~mm量级,表面积和体积也随之减小,但衰减的速率不同,因而表面积与体积之比由102m-1量级变成106m-1量级,这使得与表面有关的传热、传质过程及表面效应的作用大大加强。Sharp K.V.等人研制的一种袖珍式换热器,通过微加工方法增加换热面积,面积与体积之比达到257×103m-1,大大提高了制冷器的效率。作用在流体上的力主要表现为体积力和表面力。体积力依赖于特征尺度的三次幂,表面力则依赖于特征尺度的一次或二次幂,随着尺度的减小,表面力的作用不断加强,在微尺度中表面力将起主要作用。表面积与体积比值达到百万倍,更加强化突出了表面力的作用。这些表面力都来源于分子间的相互作用力,包括范德华力、静电力、位形力等,从本质上说它们都是短程力(小于1nm),但其积累效果可达1μm的长程。范德华力是各种作用力中最弱的,它与距离的六次方成反比(1/r6),属于短程力,在表面积与体积比很大的结构中影响很显著;静电力是带电分子或粒子间的作用力,与距离的平方成反比(1/r2),作用范围比范德华力大,其作用力在距离10μm时仍有显著影响,距离小于0.1μm时其作用最强;空间位形力主要产生在含有长链分子的液体中,其作用力可达到0.1μm范围,而且在含有大量长链分子的液体中作用更加显著。因此,在微米尺度条件下,极大的表面积/体积比值还导致的表面张力效应等是影响微流体特性的一个主要因素。
1.2.3 表面粗糙度的影响
自19世纪Darcy提出表面粗糙度是流体流动的重要因素以来,很多研究者致力于这方面的研究。Moody总结前人的工作绘制了著名的Moody图,描绘了相对粗糙度(ε/Dt)为0~0.05流体的fdarcy(Darcy摩擦因数)与雷诺数的关系,为后来研究者的工作提供了极大的方便。随着沟道尺寸的减小,相对粗糙度已超出5%的范围,Moody图表的适用性问题进一步引起质疑。目前,Kandlikar等人已经研究了相对粗糙度值达14%的微系统的单向流动特性,为了更精确地描述微尺度下的粗糙度,定义了6个粗糙度参数,并根据实验对Moody图表进行了修正,使其适用于相对粗糙度值高达14%的单相流动系统。随着管道直径的减小,粗糙度相对于管道直径的比例增大,导致表面粗糙度的影响显著增加。有实验证明,表面粗糙结构可用于增强热量和质量传递。在热管启动方面的研究表明,如果毛细管的管壁很光滑,粗糙尺度小于0.5μm,则热管的加热段需要很大的热流密度来激活核化点使之产生气泡。脉动热管加热段的热流密度随着壁面毛细成核半径的变化,如图1.3-1所示。当核化尺寸小于2μm时,随着核化半径的减小,内壁面变得光滑,热管启动的热流密度急剧上升。

图1.3-1 脉动热管加热段热流密度q与壁管毛细成核半径ra的关系
1.2.4 梯度参数效应
尺度缩小使得流场中某些梯度量变大,与梯度量有关的参数的作用将增强,例如,对于平行剪切流动,黏性剪切应力τ与速度的一阶空间导数成正比。尺度缩小使沿壁面法向的速度梯度变大,因此剪切作用增强,而剪切应力τ正比于剪切应变率γ。强的剪切应力对应高剪切应变率γ,流变学研究表明,当γ大于流体分子频率两倍时,流动的流体将呈现非牛顿流的特性。
在传热学中,层流的对流换热系数α∝,l是特征尺度。当l从cm变成μm,即l减小4个数量级,α将比常规条件时高1~2个量级。从物理上解释,微尺度下流体流经长度很短,所以附面层很薄。同样温差下平均温度梯度大,使换热强度提高。
1.2.5 边界层流动对总流动贡献
在宏观流动中,边界层引起的流动对整个通道的总流动贡献很小。然而,随着通道直径的减小,边界层流动的作用变得显著起来。当通道尺寸减小到几个微米,边界层的厚度(几百纳米)相对于通道直径已不可忽视。考虑到边界层诱导效应和黏滞效应,微通道中的流速可以表示为:
U=Ua+Us (1.3-3)
式中,Ua为黏滞流动速度,Us为边界层流动速度
其中,c=cos(βz),S=
sin(βz),
式中,h代表径向尺寸,A代表激励声源波速,α代表声吸收系数,ρ0代表密度,μ表示动态黏性,z表示径向坐标。
由此可见,黏滞流动速度Ua与通道尺寸有关,而边界层诱导效应引起的流动速度Us与通道尺寸无关。因此,随着通道直径的减小,边界层流动对通道内总流动的贡献越来越显著。图1.3-2说明了边界层诱导流动在总平均流速中所占比例R与管道直径的关系。图中不同的曲线代表不同的激励频率,实验所用液体是水。可以看出,当管道直径d小于100μm时,边界层诱导效应非常显著。

图1.3-2 边界层流动对总流动的贡献与通道尺寸的关系
式(1.3-5)表明,边界层流动的影响主体体现在贴近管壁附近很小的范围内。随着沟道直径减小,边界层厚度保持不变,诱导流动的影响范围(面积与直径的平方成正比)相对于管壁截面积增加。随沟道尺寸的减小,边界层流速保持不变,而黏滞力引起的流速减小,所以边界层流速在总流动中的比例增加,如图1.3-3所示。

图1.3-3 不同直径沟道中归一化流速v与流动层位置z/r(边界层位置与管道半径之比)的关系
1.2.6 黏滞力的影响
雷诺数Re是用来描述流体流动状态的一个无量纲数,定义为惯性力和黏滞力的比值
式中,ρ为密度;v为特征速度;d为特征长度或直径;η为黏度。
在直管道中一般认为Re≈103是层流与湍流的分界,Re与特征长度d成正比,因而在微尺度下Re均很小,即流动几乎全是层流,不存在湍流或紊流,而且,流体内部黏性力和流体与外部接触界面上的作用力起着主要作用。S.W.Chau等人研究微流动系统流动特性对微制造中沉积过程的影响,论述了当表面张力和黏滞力足以抵消惯性力时,流动会被衰减或拖曳,如果黏滞力相当小就不能形成稳定的流动层。
1.3 极性流体与非极性流体
流体虽然总体上不会呈现极性,但含有极性离子的流体与非极性流体的流动特性存在显著差异,极性流体的流阻要大于非极性流体,这可以从离子吸附得到解释。此外,不同非极性流体的流阻也各不相同,据Stemme的观察,蒸馏水流过0.2μm的管道时,所受的流阻只有酒精的1/31对于这一点,尚未有令人满意的解释,但流体的极性对微流体的影响是显然的。
2 微泵
微机电系统(MEMS)具有微型化,能耗低和集成度高等优势,其应用已扩展至汽车工业、生物医学、航天、军事等各个领域。微流体器件作为微机电系统的重要分支在药物输送、燃料喷射、细胞分离、电子元件冷却、微量化学分析及微小型卫星推进等方面具有广泛的应用。微泵作为构成微流体系统的重要部件是微流体器件的代表产物,可实现流体输送、流体测量、流体混合、流体的浓缩和分离,受到人们的普遍关注。
2.1 微泵材料
微泵材料的选择对微泵的设计制作、性能、成本以及应用都有显著的影响。良好的微泵材料应该具有与操作环境良好兼容、制作工艺简单、可大批量生产、疲劳寿命高等特点。根据当今发表的微泵文献,多数以硅半导体、玻璃为材料。随着微泵技术的发展,聚合物材料如聚二甲基硅氧烷(PDMS)、光刻胶、电致动聚合物材料(EAP)、离子导电聚合胶片(ICPF)、聚对二甲苯(Parylene)、聚甲基丙烯酸甲酯(PMMA)等也广泛用来制作微泵,其中PDMS最为常见,电致动聚合物如离子聚合物金属复合材料(IPMC)、介电弹性体(DE)、聚偏二氟乙烯(PVDF)等作为新型智能材料以其独特的优点成为国内外研究的热点。以硅为材料的微泵工艺成熟,但加工制作复杂,成本较高,生物相容性差,在生物医学领域的应用受到限制。而基于聚合物材料的微泵有种类多、可供选择余地大、制作工艺简单、易于集成、生物兼容性好、性能优良、成本低等优点,非常适合大批量生产,使一次性使用的医学微泵成为可能。
2.2 微泵分类
2.2.1 有阀微泵和无阀微泵
微泵根据其有无可动阀片分为有阀微泵和无阀微泵。典型的无阀微泵有收缩—扩张型微泵,以及基于流体性质的非机械式微泵。有阀微泵的优点是原理简单,制造工艺成熟,易于控制,反向截止性能较好。但缺点也很明显:由于阀片的存在,微泵加工工艺要求高,结构复杂,不利于集成以及微型化;阀片易疲劳,并且回流现象不可避免,微泵效率低;在药物输送、血液运输等领域应用中,阀门的存在会造成堵塞,且容易损伤细胞。相比于有阀微泵,无阀微泵有以下优点:结构简单,易于加工和制备,可以制成平面结构,或者直接和微流控芯片一体化加工,便于微泵的微型化、集成化;无阀微泵利用微流体的特性,可以连续输送流体,能精确检测和控制流量,因此无阀微泵成为21世纪微流体系统微型化、集成化、控制精准化程度进一步提高的突破口,具有广阔的应用前景。
无阀微泵的工作原理是基于Torsten Gerlach提出的微扩散理论。无阀微泵是利用流路差异引起的压力损失的不对称性来实现流体泵送的。无阀微泵的主要组成部件包括带有驱动膜的腔体和两个锥形管结构,其工作原理如图1.3-4所示。当泵膜向上运动时腔体扩大,微泵进入“吸取模式”[图1.3-4(a)]时,入口处的锥形管充当扩散口,而出口处的锥形管充当喷口,其结果是入口(扩散口)的流进量大于出口(喷口)的流进量;当泵膜向下移动时,腔体收缩,微泵进入“压缩模式”[图1.3-4(b)],出口处的锥形管充当扩散口,而入口处的锥形管充当喷口,结果是出口(扩散口)的流出量大于入口(喷口)的流出量。经过一个工作周期,就会有一定的净流量从出口流出。

图1.3-4 无阀微泵的工作原理
2.2.2 机械式微泵和非机械式微泵
按泵类有无运动部件分,可以分为机械式微泵和非机械式微泵。机械式微泵驱动力较大、响应速度快,是目前应用的主流,但因为有可动部件,结构复杂,存在机械磨损和泄漏现象,不利于微型化、集成化发展。非机械式微泵将非机械能转变为微流体的动能,没有运动部件,结构简单、流量连续稳定,是目前研究的热点。
(1)机械式微泵
①压电驱动微泵 压电驱动微泵是基于压电晶体的压电特性驱动薄膜振动从而实现泵送流体的。常见的压电材料有压电片、PZT压电堆、压电薄膜。压电驱动的优点是结构简单、驱动力大、响应时间短、能耗低、效率高;其缺点是驱动电压高、振幅小,自吸困难,限制了其应用范围。
②静电式 静电驱动是指基于库仑力的原理,在平行的2个极板中,给其中一个固定极板加上单一极性的电压:在另一个与泵膜连接的极板上加上交变电压,交替产生该极板的双向形变,从而实现泵的功能。极板间的引力,如式(1.3-7)所示。
式中,F为静电驱动力,V为所加的电压,A为极板的面积,x为极板间的距离;ε为介电常数。这种微泵具有低功耗(典型值1mW)和较快的响应速度等优点,主要不足在于其加上较高的电压也只能产生较小的形变,导致最大泵出量很小。国内对于静电式微泵的研究主要集中于理论分析和数值模拟上。
③热气动式 热气动微泵具有空气腔和泵腔2个由泵膜分隔开的腔体,通过对空气加热器和冷却器使空气腔中的气体周期性地膨胀和收缩,从而使薄膜同时发生周期性的振动,实现泵的功能。加热、冷却导致的气温变化(ΔT)使空气腔容积产生变化(ΔV),从而引起泵腔中压力的变化(Δp),三者之间的关系可以表示为:
式中,E为表示薄膜弹性的体积模量,β为热膨胀系数,ΔT为气体温度的变化,ΔV/V为容积的变化比。构成热气动泵体和泵膜的材料一般为玻璃和PDMS(聚二甲基硅氧烷)。
④电磁式 基于洛伦兹力的典型电磁驱动微泵由带有进、出口微阀门的腔体、柔性可变的泵膜、1个永磁体和1套驱动线圈组成。一般永磁体附着于泵膜上,也可以是线圈附着其上。当交变电流通过线圈产生交变磁场时,就会与永磁体之间相互排斥和吸引,从而产生微泵的动力。平面线圈是微电磁驱动的研究重点。电磁驱动的优点是输入电压低、泵膜变形大、频率调节方便、响应快,并且可以远程控制。其缺点是能耗大、电磁材料微加工困难、由于线圈存在难以微型化。
⑤形状记忆合金式 形状记忆合金(shapememoryalloy,SMA)是一种能够记忆原有形状的智能合金材料。形状记忆效应是指SMA的2种固态相——高温下的奥氏体和低温下的马氏体之间的相变而发生的延展性形变。SMA微泵正是利用了这种周而复始的两种固体相的相变作为泵的动力来源。常见的记忆合金有钛镍合金、金镉合金、铜锌合金等。SMA需要的输入功率较大,其响应速也较慢,效率低,泵膜变形较难控制,但其具有较大功(率)重(量)比,集驱动、传动和传感于一身,变形大、输出应力高、驱动电压低和生物相容性等优点,使得它在微小型应用领域具有独特的前景。
⑥离子导电聚合片式 与硅、金属等膜片相比,聚合物泵膜可以产生较大的形变,输入功率也更小。一种最常见的聚合物泵膜材料是离子导电聚合胶片(ionicconductive polymerfilm,ICPF),它是由聚合电解质胶片和胶片两面化学结合的白金导体构成的。白金导体构成了胶片的两极,胶片在外在电场的作用下会发生阳离子向阴极迁移,同时吸附聚合物中的水分子运动,从而发生阴极膨胀、阳极收缩的现象。当施加周期性交变电场时,聚合物泵膜也会发生周期性形变为微泵提供动力。
⑦相变式 相变式微泵的执行部件包括加热器、由泵膜分隔开的工作腔和泵腔。加热器工作时使工作腔内的液体汽化,腔内体积增大,从而推动泵膜膨胀,压缩泵腔内的流体;加热器不工作时,热气体冷凝。工作腔内体积减小,使得泵膜回缩,从而利用工作腔内的这种气态和液态的往复转变为微泵提供动力。
⑧双金属式 铆合在一起的2种不同金属一般具有不同的热膨胀系数,当通过微泵内的加热器对双金属泵膜进行加热时,由于2种金属的热膨胀程度不同,泵膜就会产生形变。双金属膜可以产生较大的推动力,然而由于常见金属的热膨胀系数都较小。因而双金属膜片的形变较小,响应的速度也不高,并不适用于需要高频振动的应用。
(2)非机械式微泵
①磁流体式 磁流体式(magnetohydrodynamic,MHD)微泵通过导电流体与磁场之间的相互作用来获得动力。MHD是指导电流体在垂直相交的磁场和电场相互作用而产生的洛伦兹力的驱动下流动。典型MHD微泵的结构相对比较简单,除了矩形微通道之外,微通道的上下两面是用于产生磁场的极性相反的永磁体,微通道的左右两面是用于产生电场的电极。除了外部提供的电磁场外,还要求所采用的流体应具有1s/m或更高的电导率。总的来说,MHD微泵可以用于具有较高电导率的流体,很多种流体都满足这一条件,这使得MHD微泵可以广泛应用于生物医学领域。
②电液动力微泵 电液动力(EHD)微泵基本原理是利用流体中带电离子在电场作用下的迁移,从而带动整个流体迁移流动的目的。这种微泵的优点是无阀无活动部件、结构简单、对微加工工艺要求不高、成本低;但这种微泵对流体的介电性质有特殊要求,只能用于绝缘液体或导电率极低的液体,如乙醇、丙酮、异丙醇等,限制了其应用。按驱动电压类型可分为两种,一种是平行电极间施加直流电压的EHD泵,另一种是在电极阵列上施加不同相位行波电压的EHD泵。
③电渗流式 电渗流(electroosmotic)也被称为动电现象。是指在外加电场下电解质溶液由正极向负极移动的过程。这是一种在微细尺度条件下发生的与电泳类似的现象,但通常情况下电渗流淌度大于组分的电泳淌度。电渗流微泵无需任何运动部件,如止回阀等,其运作效率较高,流向完全由外加电场的方向控制,普通廉价的MEMS技术即可胜任这种微泵的制造。其主要的限制在于需要较高的操作电压,且不能用于非离子溶液。
④电浸润式 电浸润式微泵利用表面张力来驱动流体运动。微尺度下,表面张力是一种主要作用力,而金属液体的表面张力会因电压改变而变化,在充满电解液的管道中施加电压金属液滴就可以沿着管道运动,推动流体运动。这类微泵具有功耗低、响应快、表面电化学不活泼等优点。
⑤曲面波式 曲面波(flexural lanar wave,FPW)微泵是采用超声驱动的。在这种微泵中存在一种称为声冲流(acoustic streaming)的现象。即具有一定幅度的声场可以被用来驱动流体。在这类微泵中。由压电晶体驱动器阵列产生声场,即沿一薄板传递的曲面波。这个薄板形成了流通道的一壁,在该壁与流体之间存在着动力传递。曲面波微泵的工作电压较低,也无需阀门和加热机构,与EHD微泵相比,对流体的导电率也没有限制。
⑥电化学式 电化学微泵通过电解水产生的气泡向液体提供驱动,电化学微泵主要由电极、微通道、电解水的腔室以及进出口的阀门等组成,其设计和制造比较简单,并较易于其他微流控系统集成。电化学微泵的主要不足在于其产生的气泡在排出泵的时候可能会引起塌陷效应,气泡也有可能溶解于水,导致不稳定和不可靠的药物释放。
⑦蒸发式 蒸发式微泵的原理类似于树木的水分运输系统,这种微泵具有一套控制液体蒸发和对气体吸收的装置。关艳霞等通过改变蒸发孔的面积或使用风扇调节微泵的流速,在较长时间内提供稳定的μL/min级液体流速。
2.3 微泵结构的优化
首先是微泵腔体结构的优化。微泵腔体结构会影响微泵的压力、流量、流动损失系数以及流动稳定性。多数微泵均为单腔体结构,为了提高微泵的性能,研制多腔体结构微泵已成为一种趋势,目前主要集中在两腔体的研究上。多腔体微泵可减轻流体脉动性,提高输送能力,并且压力和流量稳定,提高微泵效率。有实验研究发现,两腔串联结构,其输出压力和流量分别是单腔的2倍和1.4倍,而且综合性能较高;并联结构输出压力不变,但流量增加一倍,而且脉动小。微流道是无阀微泵的关键结构,其结构制约着微泵性能,有必要对微流道结构进行优化。有关学者提出了利用锯齿形微流道代替传统扩张/收缩微流道,有效提高了微泵性能。锯齿型微流道由于侧面齿形角的存在,流动过程更易产生漩涡,使流道压力损失降低,其最大流量和最大压头都得到提高。Li等模仿鱼的鳍片,在微流道侧壁增加微翅片结构,微泵流动效率提高了10%,在100V,3kHz的驱动电压下测试,微泵性能提高了35%。浙江大学傅新等利用Micro-DPIV技术对无阀微泵进行流场检测,探究了微泵的流动机理,为微泵性能检测、流道结构优化设计提供了实验验证和技术指导。
3 微阀
微阀作为微流体系统的主要元件之一,其作用包括径流调节、开/关转换以及密封生物分子、微/纳粒子、化学试剂等,其性质包括无泄漏、死体积小、功耗低、压阻大、对微粒玷污不敏感、反应快、可线性操作的能力等。目前,微阀主要被分为有源微阀和无源微阀。有源微阀需要在某种驱动能的作用下实现对微流体的控制,无源微阀则不需要从外部输入能量,通常在顺压与逆压作用下实现对微流体的控制。此外,按照最初的状态,微阀可分为常开型和常闭型两种。
3.1 有源微阀
根据驱动源的不同,有源微阀又可分为压电、磁、电、热、相变、双稳态有源微阀以及由外部辅助系统如气体驱动的有源微阀,其中热驱动微阀包括热空气、双金属和形状记忆合金微阀,相变微阀包括水凝胶、溶胶—凝胶和石蜡微阀。在这些微阀中,压电阀具有灵敏度高、响应快、死区体积小等特点,应用广泛;静电与磁微阀可以控制流动方向且功耗低;热驱动微阀易于集成化并具有优良的动态特性,适于与硅热流量传感器一体化的应用,但这种微阀消耗的功率多,反应时间长;相变微阀由于成本相对较低,因而在一次性使用的生物芯片中广泛使用;气动微阀因薄膜为弹性材料,能产生较大的变形,所以密封性能很好,泄漏低。
3.1.1 压电微阀
压电驱动能够产生很大的驱动力、反应时间快,但即使有很高的电压,隔膜也只能产生很小的偏移量。J.Kruckow等人利用体微加工的方法,通过硅熔融键合,将两层硅结构键合在一起,研制了一种由压电驱动的自封锁常闭型微阀,其结构和工作原理,如图1.3-5所示。在没有施加电压时,该微阀具有良好的密封性能,当电压为100V时,气体流速为0.38mL/min。

图1.3-5 压电硅微阀原理图
J.M.Park等人研制了一种用于低温下流速调制的常开型压电微阀,它包括由绝缘体上硅(SOI)制成的芯片、玻璃片、压电堆栈驱动器和玻璃陶瓷封壳。该阀的反应时间低于1ms,带宽可达820kHz。在室温下,入口压力为55kPa时,若微阀全开(0V),流速可达980mL/min,当施加60V驱动电压时,流速为0mL/min,当温度为80K,入口压力为104kPa时,该阀能成功地将气体流速从350mL/min调至20mL/min。E.H.Yang等人研发了一种应用于微飞船的常闭型压电微阀,其结构如图1.3-6所示。

图1.3-6 防泄漏压电微泵的原理图
当输入电压为10V,入口压力为2068.5kPa时,层流速率为52mL/min。为使该阀完全打开,输入电压须为30V,微阀消耗的功率为3mW。由于阀座上含有窄边座套环和受张应力的硅支链,因而具有很好的防泄漏能力,当压力为5516kPa时,泄漏速率为104mL/min。
3.1.2 磁微阀
C.H.Cheng等人在PDMS中掺入铁粉,将该混合物填充在硅KOH各向异性刻蚀后的V形腔中,作为阀塞及阀塞支撑。这是一种常闭形微阀,当外加磁场时,阀塞和支撑被抬起,阀被打开。M.Duch等人提出了一种低功耗、使用方便的磁微阀。这种微阀由上部V形悬臂梁和下部硅隔膜组成,V形悬臂梁上电镀一层Co2Ni合金。当分别在微阀的上部和下部施加磁场时,阀相应地被打开和关闭,如图1.3-7所示。

图1.3-7 磁驱动微流量调节器原理图
C.Fu等人利用直径3mm铁球作为可由外部磁场驱动的部件研制了一种常开型微球阀。该微球阀由三个热压聚合物层和三个金属层组成,各层通过黏附薄膜连接,开关频率可达30Hz,开关时间为10ms。当电流为200mA,压力为50kPa时,微阀被关闭,泄流速度为0.5L/min。此外,这种微阀还可用作比例阀来调节出口压力,当入口压力为200kPa时,调节范围为0~112.5kPa。
3.1.3 静电驱动微阀
静电驱动反应时间快、功率低,但是驱动力较小。此外,由于静电驱动微阀通常是以二进制的模式工作,所以需要使用阀阵列来控制流动。T.Hasegawa等人提出了一种由空气驱动无死体积的微分配系统,其中主要元件就是由微螺线管驱动器实现方向转换的10出口多方向微开关阀。这种开关阀包含带有硅树脂橡胶环的旋转装置和带钢球的自定位闭锁装置。定位装置能精确地自动定位出口并检测当前选中的出口,因而不需要其他传感器和控制器。为使芯片能在500kPa以上的高压下快速转换,硅胶环的高度应为300μm,转子压缩力为3N,转子旋转力为0.8N。当在螺线管上施加电压6VDC时,吸引力为1N,开关时间为0.1s。
3.1.4 热驱动微阀
使用热驱动的微阀包括热空气驱动微阀、双金属驱动微阀、形状记忆合金驱动微阀三种。虽然它们消耗功率多、反应时间长,但由于它们结构简单,且能提供较大的驱动力,因而也十分受关注。
(1)热气
J.H.Kim等人利用PDMS研制了一种常开型热气驱动的微阀,该微阀由玻璃片、铟锡氧化物(ITO)加热器、PDMS热气腔、PDMS振动膜和PDMS通道组成。在ITO加热器上施加电压,使加热器加热PDMS热气腔中的气体,由于气体膨胀,PDMS振动膜发生变形将阀关闭。将阀关闭所需的功率取决于膜的厚度和输入压力,与微阀通道的宽度无关。当膜厚为70μm时,使薄膜形变达到40μm所需的功率为25mW;膜厚为170μm时,所需功率为200mW,关闭和开启时间分别为20s和25s。C.A.Rich等人研制了一种皱褶隔膜式热空气微阀,其结构如图1.3-8所示。隔膜下的密封腔内装有挥发性液体,它的蒸发压可以通过电阻加热来提高,因而使隔膜发生偏移并将阀关闭。当入口压力为133.3kPa,功率为350mW时,阀关闭,维持关闭状态所需的功率为30mW。该阀泄漏速率可低达10-3mL/min。

图1.3-8 热空气驱动微阀结构图
(2)双金属
双金属驱动器的结构简单,能够产生很大的力,但是功耗大,对环境温度敏感。20世纪90年代,H.Jerman研制了由厚度分别为8μm和5μm的硅膜和铝层组成的二金属驱动的微阀,如图1.3-9所示。当输入压为7~350kPa,流速为0~0.15L/min时,该阀能很好地实现比例控制。

图1.3-9 双金属驱动微阀截面图
(3)形状记忆合金
形状记忆合金是一种智能材料,其特点是具有形状记忆效应。将形状记忆合金在高温下定型后,冷却到低温(或室温),并施加外力,使其存在残余变形,经过加热到临界温度之上,就可使存在的残余变形消失,并恢复到高温下的形状。M.E.Piccini等人利用直径为75μm的镍钛金属线研制了一种硅树脂管状常闭型微阀,通过施加脉冲电压实现对微阀的开关控制。当脉冲功率为213mW时,它的反应时间为2.5s,平均流速为28.4μL/min。该阀的爆破压力为68.9kPa,当压力为20.7kPa时,流速约为33μL/min。米智楠等人利用形状记忆合金作为驱动元件,开发了一种微型气动开关阀。低温时,由于受气体压力作用,形状记忆合金弹簧被压缩,阀门关闭。通过对NiTi合金弹簧通电加热,使其屈服应力变大,从而产生较大的恢复力并克服气体压力,推动阀门开启。NiTi合金弹簧断电后,通过气流进行冷却,从而降低温度,其屈服应力变小,在气体压力的作用下关闭阀门。微型阀在气压为0.4MPa通电电流为5A时,阀门的开启时间为0.8s,关闭时间为2.6s。
3.1.5 相变驱动微阀
相变驱动微阀使用水凝胶、溶胶-凝胶、石蜡等材料,通常要消耗能量,如温度、电或光等,但由于它们的成本相对较低,因而在一次性使用的生物芯片中广泛使用。
(1)石蜡微阀
R.H.LIU等人用石蜡为材料研制了一种由热驱动的微开关阀,含有该微阀的DNA聚合酶链式反应微装置能够将样品溶液密封在反应腔内,其原理如图1.3-10所示。当压力小于137.9kPa,微阀处于关闭状态时,没有泄漏发生;当压力达到275.8kPa时,在流道壁和石蜡界面上就出现了泄漏。这种微阀的反应时间大约为20s,但增加凝固通道的宽度或缩短凝固区与加热区的距离能有效减少反应时间。

图1.3-10 石蜡微开关阀原理图
(2)水凝胶微阀
早期的水凝胶微阀主要是通过改变溶液的盐浓度来控制,并使用原位光刻技术制造。目前,许多研究人员开发了基于温度效应和热效应的水凝胶微阀,如A.Richter等人研制了基于温度敏感的常闭型水凝胶微阀,通过光聚合作用,将水凝胶驱动物直接定位在微通道内。该水凝胶的状态转变温度为34℃,微阀开启和关闭所需时间分别为0.3s和2s。J.Wang等人研制了一种基于热效应的水凝胶微阀,能够承受200kPa以上的压力而没有泄漏,它的关闭时间大约为4.5s,开启时间与凝胶体的长度成正比。当凝胶的长度为300μm和1500μm时,开启时间分别为5s和12s。
(3)溶胶-凝胶微阀
S.Y.Dae等人利用纤维素甲醚的可逆溶胶-凝胶转变特性制造了一种凝胶微阀,他们在每个微通道中都植入了一个微加热器和微温度传感器。为使该阀能正常工作,须保持加热通道温度在60℃左右,流动通道在35℃左右,且两通道间的温度差为23K。此外,要使该阀能稳定工作,流速应该大于5μL/min。当使用风扇冷却时,最初的加热和冷却速度分别为5.7K/s和5.8K/s。当压力为2.07×104Pa时,没有泄漏产生。
3.1.6 双稳态微阀
Y.C.Goll等人所研制的双稳态微阀由流体腔和驱动腔组成,两腔之间是25μm厚的聚酰亚胺薄膜,薄膜在上下两个方向的最大偏移均为120μm。由于是双稳态微阀,因而需要快速升压和降压以实现阀的开和关。通过快速加热驱动腔中的空气,可以将阀关闭;要使阀打开,需先将驱动腔里的空气加热使之从驱动腔下的孔溢出,然后将电流切断使气体冷却。当输入压力为30kPa时,流速为250μL/s,阀关闭时,泄流速率低于0.001μL/s。M.Capanu等人研制了一种基于电磁驱动的常闭型双稳态微阀,它主要由两部分构成:上部电镀的金线圈和下部Ni/Fe合金梁。双稳态性是通过平衡梁的弹力和46μm厚磁性金属箔的磁力实现的。用去离子水测试阀的动态反应时间,当施加1.16V脉冲电压30ms阀打开;施加1.18V脉冲电压80ms,阀关闭。
3.1.7 外部气动微阀
外部气动微阀在开/关转换或密封中有很好的性能。到目前为止,带有外部驱动力的压力型微阀由于能够提供零泄流和较大的可抗压力,因而十分受欢迎。然而,为适应手持式生物化学应用,它的外部系统(如空气/真空泵)应进一步小型化。
C.K.Malek等人利用硅和PDMS研制了一种多层气动常闭微阀,其工作原理简单,即若要使流体流动,需在外部施加一个负压使阀开启;当流体压力过高时,需要施加正压使阀紧闭。这种阀的结构简单,制造成本低,易于操作。由于PDMS是一种弹性材料,其变形大,故只需施加很低的压力就能使薄膜变形,具有很好的密封性,其结构如图1.3-11所示。

图1.3-11 气动常闭微阀截面图
S.R.Quake团队已经报道了多种应用多层软光刻工艺制造的微流体系统,其中主要结构是一个由空气驱动的串联微阀,它是由空气控制层和流道层叠加而成气体通道和流体通道的宽度,通常为100μm,它们正交形成面积为100μm×100μm振动薄膜。当气道中的气体压力为60kPa时,在几毫秒内薄膜就能偏离平衡位置阻止流体流动。在弹性回复力作用下,微阀回到打开状态。值得注意的是流道的深宽比不能小于1:10,否则结构容易塌陷。
3.2 无源微阀
无源微阀在微流体系统中主要被用作止回阀元件,根据是否含有可动部件,它们可被分为含有机械可动部件微阀(如悬臂梁式和薄膜式)和不含机械可动部件微阀(如毛细管微阀)。含可动部件的无源微阀通常只能沿顺压的方向打,呈现二极管特性,结构简单,容易制造,可以由体硅刻蚀、金属沉积、多晶硅或聚合物材料表面微加工工艺制得,但是它的性能受输入压力的影响。毛细管微阀是通过表面张力来调节流体流动,由于没有可动部件,因而通常不易堵塞通道,而扭矩驱动微阀是通过旋紧螺钉将阀关闭,使用十分方便。
3.2.1 悬臂梁式微阀
B.Li等人利用原位UV2LIGA工艺,以硅和镍为主要材料研制了一种由80个微阀组成的微阀阵列,该微阀阵列具有大流速(大于10mL/s)高压力(承载能力大于10MPa)和高工作频率(大于10kHz)的特点。单个微阀为常闭型微阀,它的入口通道和阀塞由硅制造而成,阀瓣由镍制成,与悬臂微梁连接被键合在硅衬底上。在正压力差的作用下,阀瓣被抬起,阀打开;在负压差与悬臂梁弹性回复力的共同作用下,阀被关闭。将阀瓣设计成交叉形状,能有效提高微阀在关闭状态时的承压能力,以及克服阀瓣接触塞子时的黏附问题。
3.2.2 薄膜式微阀
M.Hu等人利用SOI硅片研制了硅薄膜厚度为90μm的微阀,它包括一个六边形孔、一个六边形薄膜和三个柔性支链。在顺压为65.5kPa时,最大流速为35.6mL/min,当反向压力为600kPa时,泄漏速率为0.01μL/min。在空气中该阀的共振频率为17.7kHz。
3.2.3 毛细管微阀
由于微通道的表面或几何形状特性,毛细管微阀能够实现自治,因而可用于微流体中。此外,由于毛细管微阀成本低且易于集成到片上实验室(LOC)装置中,所以在生命科学中也常有所应用。
最初的毛细管阀是通过在亲水微管道上沉积一层疏水物质,外加驱动压力使流体通过疏水区。C.Delattre等人研制的毛细管微阀不需要沉积疏水层,而是利用深度反应离子刻蚀使通道的长度和宽度突然变大,因而增加了流体的可湿性。J.Melin等人提出了一种“Y”形的毛细管微阀,它可利用液体触发作用来避免当两种液体在交点相遇时的被困气泡。当液体从一个入口进入到达交汇点时,会等待从另一个入口进来的液体,当第二种液体到达交汇口后,第一种液体的流动就会被触发。
3.2.4 扭矩驱动微阀
D.B.Weibel等人研制了一种扭矩驱动的微阀(TWIST),其中包含直径大于500μm的螺钉,通过螺丝刀顺时针转动螺钉,微阀被关闭,逆时针旋转就能将阀打开,这种阀的优点是不需要额外输入便可保持关闭状态,能够容易地集成为便携式和任意使用的微流体器件。此外,它还能将高度大于50μm的流道完全关闭,其实物图如图1.3-12所示。

图1.3-12 扭矩驱动微阀实物图
4 微流体驱动与控制技术
微米乃至纳米尺度构件中流体的驱动和控制是微电子机械系统(MEMS)中经常要遇到的问题,也是MEMS发展需要解决的关键技术之一,它在微型传感器、微型致动器等微流体器件、微生物化学分析以及各种涉及微流体输运的场合中均有着广泛的应用,而近几年生物芯片技术的进步和“lab-on-a-chip”概念的提出更是迫切要求实现微量流体的自动精确的驱动和控制。微流体驱动与控制技术的发展也严重影响着微流体器件的进一步小型化和性能的改进,后者反过来也促进了微流体驱动与控制技术的发展,微流体驱动和控制技术的研究已逐渐成为MEMS研究的一个热点。
微流体的驱动与控制和宏观流体的驱动与控制有很大的不同,这主要是由于当尺度减小时,流体的流动特性发生了变化,这种流动特性的变化使得宏观流体驱动与控制技术在微流体中的简单移植往往不成功或者效果不好,微流体的驱动与控制技术更为复杂和多样化。
目前,微流体的驱功和控制技术种类很多,采用的原理和形式不尽相同,如按原理来分,可分为压力驱动、电水力驱动、电渗驱动、热驱动、表面张力驱动、离心力驱动等如按有无可动部件分,又可分为有阀和无阀的驱动和控制,其中每一种驱动和控制方式又有各种不同的操作形式,微流体的流动特性复杂、影响因素众多,而且有时几种方式是组合在一起的,上述条框式的分类只是近似的,不全面的,但为叙述方便,下面将大致按照原理分类对各种驱动和控制微流体的技术进行介绍。
4.1 压力驱动和控制
微流体的压力驱动和控制与宏观流体的原理相似,都是依靠入口、出口和腔体内部的相对压差驱动流体,利用机械阀实现流动控制在这点上,微流体的压力驱动和控制可以看作宏观流动控制技术的一种移植。目前,利用压力驱动和控制微流体有两种方法,一种是利用外部的宏观泵或注射器与微流体管道结合,通过前者的推动力驱动流体在微管道中流动,流体冲开管道中的阀门被释放出,这种方法简单、容易实现、成本低,而且已经商业化,但不易小型化是它的一个主要缺点。另一种微流体的压力驱动和控制方法是采用微机械技术制作的微泵来提供压力。
4.1.1 机械压差驱动
机械压差驱动方式是运用机械零件的摆动运动将机械能转化为流体运动,依靠进出口和腔体内部的相对压差驱动流体。机械压差驱动原理简单,制造工艺成熟,易于控制。目前,微流体系统中主要以微泵为主,运用机械压差技术驱动。微泵的早期发展遵循的就是隔膜或活塞原理。这类传统典型的例子就是所谓“活塞式”微泵,如微隔膜泵和蠕动式微泵。驱动原理如图1.3-13所示,泵室腔被一层或多层可移动隔膜盖住。驱使隔膜的上下运动就可以导致室腔体积的改变,从而产生了上下压力瞬时改变Δp。其工作原理可以描述为一个循环过程,分为供给过程(泵室腔体积增大)和压出过程(泵室腔体积减小)。

图1.3-13 “活塞式”微泵工作原理示意图
在供给过程中泵室腔产生低压,使得进口端的液体被吸入(压力差大于进口端的极限压力);在压出过程中泵室腔产生高压,将腔室内的液体挤向出口端(压力差大于出口端的极限压力)。此时,进口端关闭以防止不必要的回流,同样在供给过程中出口端关闭。
微泵腔体的扩张或缩小就是驱动隔膜的上下运动,所以其微型化取决于致动器的大小。致动器可分为外部致动器和微致动器。
外部致动器必须粘接或装配到微结构的泵体上,主要有电磁致动器,即通过电磁线圈与铁芯配合致动。这种运动方式可获得大的位移,而力的大小则取决于线圈的匝数和通过的电流,由于受电磁线圈尺寸的限制,微型化较困难;压电致动器(见图1.3-14)由压电陶瓷片(PZT)和电极组成,商品压电陶瓷可用环氧树脂粘接在膜片上,膜片越薄变形量与驱动电压和频率成比例,通常将多片压电片堆叠以增加压力,但所需的驱动电压较高;双金属致动器,致动原理是利用两金属在相同温差下膨胀或收缩量的不同产生内应力,从而使双金属片发生形变而工作。

图1.3-14 压电致动器驱动微泵示意图
微致动器则是利用微加工技术直接在泵体上加工出来的,省去了装配工艺,但是受到加工工艺和加工精度的限制,不易加工。主要致动器有静电力驱动,如图1.3-15当给激励电极加电压后,可挠性膜片将根据电压的方向和大小不同产生凸形变,从而使谐振腔内产生相应的方向和大小的脉冲压力,打开或关闭阀的出入口;热气动致动器,它由密封的压力室和属于压力室一部分的可移动膜片构成,室腔里的气体通过电加热膨胀产生压力,从而推动膜片工作,但其工作效率则取决于与外界的热交换能力;由Ti-Ni合金构成形状记忆合金做成膜片,利用材料母相在超过某一温度的情况下冷却产生马氏体相变,经加热至一定温度后又转变为母相(称为逆相变)的特性,使其具有形状记忆效应,从而使膜片上下运动。

图1.3-15 静电力驱动微泵示意图
4.1.2 外部压力驱动
外部宏观泵或注射器与微流体管道耦合连接,利用前者产生的外部压力推动微管道内流体的流动。已经商品化的微注射系统就是利用外部气压或液压驱动微注射针中液体流动。2000年,Unger等人报道了一种采用多层软光刻技术制作的气动致动PDMS微阀。2005年,K/hler J.M.等人报道的微混合系统也是用外部压力驱动流体运动,该驱动方式要采用外置设备,不利于整个系统的微型化。这种驱动方式多数适用于对整体微型化要求不高、对核心微流体管道的反应有要求的微流体系统。
4.2 电渗驱动与控制
利用电渗流产生泵和阀的动作驱动流体在微管道中流动,是一类较成熟的方法在微流体系统,尤其是在生物和电泳芯片中,得到了广泛的应用,是目前最成功的微流体驱动和控制方法之一,电渗现象是一种宏观现象,它是指在电场作用下,管道中或固相多孔物质内,液体沿固体表面移动的现象。图1.3-16为电渗流形成的原理图,电渗流产生的前提是在与电解液接触的管壁上有不动的表面电荷,这种表面电荷来自于离子化基或是液体中被强力吸附在表面的电荷,例如,石英毛细管壁上的表面负电荷来自于硅经基在水溶液中发生电离所产生的负离子在表面电荷的静电吸附和分子扩散的作用下,溶液中的抗衡离子就会在固液界面上形成双电层,而管道中央液体中的净电荷则几乎为零,双电层由紧密层和扩散层组成,其中紧密层的厚度约为1~2个离子的厚度,当在管道两端施加适当的电压时,在场的作用下,固液两相就会在紧密层和扩散层之间的滑动面上发生相对运动。由于离子的溶剂化作用或黏滞力的作用,当形成扩散层的离子发生迁移时,这些离子就会携带着液体一同移动,因此形成了电渗流。液体随扩散层的离子移动,从开始到形成稳定的速度轮廓,所需要的时间很短。数值计算的结果表明这一时间是100μs~1ms。在这段时间之后,电渗流的速度轮廓是一个平面,就像一个瓶塞。电渗流在管道中匀速流动,不存在径向的流速梯度。这一点与压差引起的抛物线形的流体速度轮廓不同,两者对比见图1.3-17。

图1.3-16 电渗流的原理

图1.3-17 电渗流的速度轮廓与压差引起的速度轮廓对比
Hasrrison等用电渗流来驱动微流体,成功实现了微芯片上的电泳分离实验。后来这种技术经过不断完善,被广泛应用于生物芯片等微型化学分析系统中样品的传输和控制。利用电压切换,可以在微管道的交叉口控制电渗流流动的方向,实现阀的功能。优化管道的几何尺寸,可以在管道的不同部分产生不同的流速,这在生化分析中,例如,溶液的混合和多个样品的并行处理中很有用处。Harrison等在微机械技术制作的宽度为20μm的玻璃微管道中获得的电渗流流速达1cm/s。目前典型的电渗驱动驱动技术流速在10nL/s~0.1μL/s。值得一提的是Schas-foort等制作的称为“流动场效应晶体管”的流动控制元件。这种元件具有微电子中的场效应晶体管功能,可以实现在电渗流驱动的微流体管道中流动的控制和切换。Schasfoort等利用50V的电压在垂直微管道的方向上产生1.5MVCM的电势差,利用该电势差可实现对电渗流的大小和方向控制。利用两个Flow FET,甚至可以逆转单管道中电渗流的方向。图1.3-18为Flow FET的结构图。Rice等和其他研究员对电渗流进行了理论分析。Manz等对电渗驱动和控制与微芯片上的电泳分离进行了综述。

图1.3-18 流动场效应晶体管结构图
电渗驱动与控制方法简单、无可动部件、容易在微管道中运用。该方法虽然没有机械阀,却可以通过电压的切换实现阀的动作,所以被广泛应用在微生化分析领域,是目前较成熟和效率较高的微流体驱动技术。但电渗驱动与控制也存在一些缺点。首先,电渗流对管壁材料和被驱动流体的物理化学性质敏感,因此它只适用于一定范围的流体和管壁材料。例如:由于焦耳热过大,高离子强度的液体不能用电渗流来驱动,因此很难用电渗的方法来驱动血液和尿液这样的生物流体。为形成电渗流所需要的双电层,溶液的pH和离子浓度都有一定要求。一些有机化合物和溶剂就不能形成双电层。而且表面杂质也会影响双电层的形成。此外,电渗流的形成,对与液体接触的表面材料也有要求,表面要能提供负电荷;此外产生电渗流所需要的高压电压电源会带来安全、功耗、和所占空间大的问题,这不利于系统的微小型化;电渗流的实现要求流体在管道中保持连续性,这使得当管道中存在气泡时该方法不再有效,这就需要在用电渗法驱动流体时,要加倍小心地防止管道中产生气泡;最后电渗流尽管适于驱动和控制狭窄管道(<100μm)中的微量液体,但由于焦耳热问题,它却不能高速(>1μL/s)驱动更宽管道中的流体。而这一能力在许多微流体应用中是必要的。
4.3 电水力(EHD) 驱动
EHD驱动需要在流体—流体或流体—固体界面诱导产生自由电荷,通过电场与自由电荷的相互作用来驱动流体,适用于导电率极低的液体。图1.3-19为原理结构示意图。

图1.3-19 EHD驱动原理示意图
如图1.3-19所示,两种材料的介电常数或导电率不同,在电极阵列上施加电压就可以在材料界面诱导自由电荷。在电极阵列上施加一个电势行波,下面的材料界面就会产生与之同步的诱导电荷。由于材料的电荷松弛会使自由电荷的运动滞后于行波,这样两者之间的位移就会产生一个作用在界面上的电表面应力,从而驱动流体流动。EHD驱动技术在大器件中被广泛应用于绝缘流体的驱动和地下输油管道中油的冷却等领域。移植到微流体驱动中,其驱动电压从原来的几万伏降低到几百伏甚至几十伏,但EHD驱动技术的适用范围仍太小。
4.4 表面张力驱动
通过化学或物理的方法,在管道中形成特定的表面张力梯度γ的表面(见图1.3-20),就可以使微流体无需任何外部作用而自发运动。

图1.3-20 表面张力驱动原理
改变表面张力梯度的方法是通过改变固体支持面的润湿性,使基底形成亲水区和疏水区。当把液滴点在疏水区时,由于液滴边沿相反两面的接触角不同,造成两边表面张力不平衡,两边压力差可以驱动液滴向亲水区运动。利用该方法(见图1.3-21),Chaudhury和Whitesides使2μL的水滴在15°的斜坡上以1~2mm/s的速度“爬山”。

图1.3-21 液滴“爬山”
产生表面张力梯度的方法是改变流体表面活化分子分布浓度,常用改变液体成分或温度实现。有人利用电化学方法控制表面活化分子的浓度,进而改变表面张力的梯度,在4mm宽的管道上用400mV电压产生2.5mm/s的速度。该驱动方法可应用于微化学反应器或微化学分析。
4.5 热(气泡) 驱动和控制
加热液体使其产生表面张力梯度的变化来驱动微流体也应该属于热驱动和控制的一种,但由于前面对表面张力驱动和控制的介绍中已提到过,这里我们不再重复,下面我们集中在一种特殊的热驱动和控制技术上进行讨论,这种技术的操作过程一般是通过给液体加热,使液体中产生气泡,气泡随温度的增加而膨胀,从而驱动和控制液体,Hewle-Packard公司的热喷墨打印机中墨的喷射就采用这种驱动方法。Evns等采用这种方法来混合微液体,Tseng等将该方法用于燃料注射器,但上述这些例子都是液体在只有一个开口喷嘴的腔体中的情况,当液体中的气泡随温度的增加而膨胀时,液体自然会直接从开口喷出,但当液体在两端开口的管道中时,这种方法就不能实现液体的单向驱动,Ozaki在180μm水压直径的金属管道中通过给单个气泡进行不对称加热,使气泡向一个方向膨胀,从而可以驱动液体在管道中定向流动,Jun等提出了两种气泡驱动方法,其中一种与Ozaki的方法类似,也是采用单个气泡的不对称加热,另一种方法采用多气泡模式,其中气泡可以起到阀的作用,图1.3-22为上述两种方法的原理图。利用该方法,Jun等人在2μm深,30μm宽、726μm长(水压直径3.4μm)的微管道中得到流速为160μm/s,压力头将近800Pa的流动,而加热所需的电压不过20V左右。

图1.3-22 两种气泡驱动模式
这种利用对气泡不对称加热控制和驱动微流体的方法,所需加热电压小,没有可动部件,实现简单,而且易于将控制电路和流体管道集成为一体,是一种较理想的控制方式,但目前达到的驱动速度较小,还需要进一步的改进。
4.6 离心力驱动
利用离心力驱动流体运动,在宏观流体中很早就有应用。Mandou和Kellogg利用离心力来驱动微流体运动。采用光刻方法在塑料圆盘上制作微管道网络,流体被装载在靠近圆盘中的储液池内,当圆盘旋转时,流体在离心力作用下,沿着微管道网络向远离圆心的方向流动,流速大小可以通过圆盘转速调节。通过控制转速、微管道分布和几何构型可以实现流体的混合和被动阀的功能。该驱动方式现已比较成功地用于酶分析中的试剂混合、反应、检测等操作。
4.7 磁流体驱动
利用电场和磁场施加于导电流体的洛仑兹力驱动。微管道在磁场中,微管道内电解液随着微管道上方的电场改变电流方向,受磁场作用产生洛仑兹力,带动电解液的流动。图1.3-23为磁流体驱动原理示意图。

图1.3-23 磁流体驱动原理示意图
Jang等人研制出磁流体动力微泵(MHD)。微流体系统利用磁流体驱动方式,其器件结构较为简单,比较容易加工,液体无脉动,流动方向可以双向调节。但是该驱动方式只能局限于中等导电液体和水溶液。
4.8 数字化微流体系统的驱动方式
在微尺度下,流体在稳定状态时受到微小的扰动,就会破坏原先的平衡,外加周期性的引起不稳定性的扰动可以产生惯性力,同时受到黏性力的作用,可以驱动微流体运动。这就是“数字化微流体技术”所说的“黏性力,惯性力交替作用驱动微流体运动”的含义。南京理工大学微系统研究室利用该驱动方式,研制了数字化无阀微泵(见图1.3-24)

图1.3-24 数字化无阀微泵结构原理示意图
该微泵利用毛细作用力作为进口动力源,再利用“数字化微流体技术”驱动,将出口处的液体喷出。由于进出口有压力差,进口形成自锁,微泵也就形成了单向流。该微泵喷出的液体量微小、可控,可达纳升级并可实现连续流、离散流。该微泵制作简便、成本低,有很好的应用价值,可与其他微器件集成为微化学分析系统、微流体系统、微推进系统等。
4.9 电流变(ER) 流体驱动
近年来,出现了运用ER流体特性驱动微流体运动。这主要运用电流变流体的黏性力随着外加电场强度变化而变化的特性。Zhang Lei,Kuriyagawa等人报道了运用ER流体为传导材料进行辅助打磨。电流变流体就是将一些细小的电流变微粒分散在不传导的液体中,其黏性力和压力等流变特性随着外加电场作变化。外加电场使流体内电流变微粒间的吸引力增加,从表象上看就是流体的黏性力增加。这种黏性力的变化是瞬间的,也是可逆的。磨料颗粒加载ER流体内,外加电场工作时,磨料颗粒悬浮在ER流体中,形成相应稳定的链状排列群(见图1.3-25),可随着外加电场运动。但是这种方式流体适用性不广。

图1.3-25 ER流体辅助打磨工作件
4.10 各种驱动方式比较
对最有代表性的各种微流体的驱动和控制方式进行比较,如表1.3-1所示。
表1.3-1 微流体驱动方式比较

4.11 发展趋势与前景
随着微电子机械系统的不断发展,微流体的驱动和控制技术的重要性越来越引起人们的注意,在微流体驱动和控制技术的研究中,微机械工艺技术往往决定着驱动和控制的性能,所以开展相应微机械工艺技术的研究对于微流体的驱动和控制是十分重要的。另一方面,微流体的流动特性复杂,而且影响因素众多,尤为重要的一点是,由于流动尺度的减小,在宏观流动中许多被忽略的效应,例如表面效应,在微流体的流动中往往成为流体流动的主要影响因素,这些特点使得微流体的驱动和控制方式与宏观流动控制方式十分不同,而且形式更为多样,在微流体的驱动和控制的研究中,注意到微流体的上述特点,开展相应的微流体流动特性的研究,深入理解驱动的机理,不仅对于发现新的驱动机制,而且对于已有驱动和控制方式性能的提高,都是十分必要的。为了更好地促进微流体驱动技术的发展,微机械技术的专家需要与力学工作者通力合作,共同致力于这一研究。我们相信,随着微机械工艺技术的不断进步和微流体流动机理的深入研究,新的、性能更好的微流体的驱动和控制方式会不断出现在我们面前,作为微流体系统的关键技术,微流体驱动与控制技术的进步将会大大促进微流体系统如微全分析系统,(如微全分析系统uTAS)的发展。