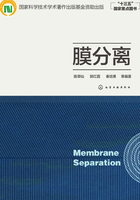
3.2 超滤膜及其组件
3.2.1 超滤膜材料
超滤膜材料包括有机高分子材料和无机材料,用这些材料及不同的制膜工艺,可以获得不同结构和性能的膜。理想的膜材料应该具备良好的耐溶剂性、优良的力学性能、热稳定性和化学稳定性等。文献报道有130多种材料可用于超滤膜的制造,然而,只有小部分实现了工业化应用。典型的制备超滤膜的高分子膜材料、无机膜材料见表3-2。
表3-2 用于超滤膜的典型材料及其性能

3.2.2 超滤膜的制备方法
超滤膜是一种非对称膜,工业上大多数的高分子膜都采用相转化法制成。相转化制膜方法是配制一定组成的高聚合物均相溶液,通过某种途径改变制膜溶液的热力学状态,使均相聚合物溶液发生相分离,最终形成一个三维大分子网络式凝胶结构,该凝胶结构中,聚合物浓相为连续相,固化后形成膜的主体骨架,聚合物稀相为分散相,洗脱后成为膜中的孔。根据改变铸膜液热力学状态的方法不同,相转化法可以分为非溶剂致相分离法和热致相分离法。
现分别介绍这两种制膜方法。
3.2.2.1 非溶剂致相分离法
非溶剂致相分离法(NIPS法,又称L-S相转化法)是发展时间最长、最为成熟的一种制膜方法。根据该方法操作方式的不同又可以分为溶剂蒸发法、蒸气相沉淀法、浸没沉淀法等。其中浸没沉淀法是目前工业上最常用的制膜方法。浸没沉淀法至少涉及聚合物、溶剂、非溶剂三种组分,制膜过程中为了制膜的需要,通常要加入添加剂来调整制膜配方,同时改变制膜工艺条件,因此制膜过程中影响因素和需要调控的参数较多。这赋予了浸没沉淀法更多的可调节性,能更好地调控膜的结构和性能。
(1)制膜方法及工艺
浸没沉淀法的制膜工艺流程如图3-5所示。

图3-5 浸没沉淀法制膜工艺流程示意图
对于某种特定的高分子膜材料,膜结构是决定膜性能的最主要因素,不同的膜结构决定不同的膜性能。非溶剂致相分离法制膜过程中,影响非对称膜结构与性能的制膜因素包括热力学因素和动力学因素,表3-3中给出了影响膜结构及性能的主要制膜因素。
表3-3 非溶剂致相分离法制膜时影响膜孔结构及膜性能的主要制膜因素

(2)制膜各因素对膜结构与性能的影响
①高聚物浓度的影响 随聚合物浓度增加,高分子链段在制膜液中的密度增加,凝胶过程中非溶剂进入铸膜液的扩散速率降低,相分离时间延长,膜孔隙率减小,通量降低,截留率升高。
②分子量、分子量分布及链结构的影响 随着聚合物分子量的提高,链长度增加,在溶剂中的溶解度下降,分子链卷曲程度增加,相互缠结增加,铸膜液黏度上升,生成膜的强度增加。聚合物分子量太大时,难以溶解,无法成膜;聚合物分子量太小,膜的机械强度差,因此应选择合适的分子量。聚合物分子量分布太宽,膜孔径不好控制,当含大量低分子量组分时,耐溶剂性差;当含大量高分子组分时,制膜过程易出现冻胶。因此,一般分子量分布窄一些好。聚合物分子链的柔顺性一方面影响聚合物在铸膜液中的构象和热力学状态,同时也影响成膜过程的凝胶速度。链柔性好的聚合物铸膜液,分子链在外界条件改变时发生重排所需时间短,固化速率快,凝胶速率大,膜结构疏松。聚合物链的刚性太强,制成的膜容易脆裂。
③溶剂种类的影响 不同溶剂对同一聚合物会产生不同的溶剂化作用,导致膜的结构形态和宏观性能不同。
当选用的溶剂为聚合物的良溶剂时,聚合物和溶剂之间的作用力远大于聚合物之间的作用力,溶剂化作用强,高分子链舒展,物理缠结点数量减少,铸膜液黏度减小,相分离速率变慢,制成的膜孔结构较致密,膜强度变好。当选用的溶剂为聚合物的不良溶剂时,聚合物和溶剂之间的作用力只稍大于聚合物之间的作用力,溶剂化作用弱,高分子链卷曲,物理缠结点数量增加,铸膜液黏度上升,相分离速度加快,制成的膜孔结构疏松,强度较差。
④添加剂种类的影响 添加剂强烈地影响着铸膜液的热力学状态、溶剂蒸发速率及凝胶速率,是决定膜性能的重要因素之一。
亲水性添加剂能够使铸膜液亲水性增强,提高了非溶剂向铸膜液的扩散速率,凝胶速率加快,膜的水通量增加。使铸膜液黏度增加的添加剂,体系扩散系数降低,凝胶速率减慢,膜的水通量减少。Cabasso、Roesink、Boom等研究了亲水性添加剂PVP对膜结构和性能的影响。Cabasso等研究发现聚砜和PVP之间的微相分离阻止致密皮层的形成;Roesink等认为聚合物膜在干燥过程中孔间PVP薄壁的破裂可得到高度贯通的孔结构;Boom等则认为含PVP的铸膜液体系能制得具有高度贯通的孔结构,是由于连续的聚合物稀相和形成膜骨架的聚合物富相相互交缠的结果,相分离过程为旋节相分离。Sourirajan等认为添加剂能够改变铸膜液中高分子的聚集状态,进而影响膜的孔径和分布;加入添加剂,铸膜液的黏度上升,铸膜液中高分子聚集体的尺寸增大。
挥发性添加剂能够迅速地提高膜表面聚合物浓度,可使膜表面孔径减小,水通量变小,截留率升高。
大量实验表明铸膜液中加入添加剂对膜的结构和性能产生较大的影响,但这种影响的理论解释和添加剂对凝胶速率的影响仍需进一步的研究。
⑤溶剂蒸发的影响 制膜溶液在浸入凝胶介质之前,溶剂会有一部分蒸发到空气中去,溶剂蒸发会引起表面铸膜液组成的变化,使膜表面结构及断面孔结构发生变化,这种变化的规律与空气气氛的温度、湿度、溶剂挥发时间及制膜高聚物溶液的性质有关。
⑥凝胶介质的影响 采用不同的凝胶介质,铸膜液体系三元相图中的二相区大小不同。凝胶介质和聚合物溶度参数相近时,二相区变小,铸膜液相分离时所需的非溶剂量增大,凝胶速率变慢,膜结构致密,水通量变小;反之,二相区变大,铸膜液相分离时所需的非溶剂量变小,凝胶速度加快,膜结构疏松,水通量变大。
⑦凝胶温度的影响 凝胶温度高,溶剂和非溶剂之间的物质交换速率快,易生成疏松结构的膜;反之,凝胶速率慢,则易生成结构较为致密的膜。
(3)凝胶动力学实验在膜结构设计与调控中的应用
聚合物铸膜液的稳定状态平衡组成可以在三元相图中描绘,但非对称膜的结构是在由铸膜液初始稳定的溶液状态向不稳定状态转变的过程中形成的,这种转变过程是复杂的多组分传质过程伴随着相变化。其膜相转变是非稳态、非平衡的。在凝胶过程中,由于溶剂和非溶剂的相互扩散,不同时刻铸膜液断面结构在不同区域会以不同的分离机理进行分相。尽管热力学从宏观上揭示了相分离过程的起始和终结,但相转化成膜过程进行的快慢与否却是微观分子运动,即动力学所决定的。平衡热力学不能给出所考察时间、地点下该分相体系的有关组成信息,因而也就不能给出膜结构变化的合理解释。如何控制相转化的成膜条件,得到所需要的膜结构与性能,是膜结构设计要解决的关键科学问题,也是膜科技工作者研究的热点。虽然自从1960年Loeb和Sourirajan用凝胶相转化法制备出了非对称膜以来,国内外的学者针对相转化成膜理论,进行了大量的基础研究,取得了许多有益的结果。但所建立的热力学、动力学模型用于描述实际成膜过程存在较大的偏差,因此,实际膜的制备仍然主要依靠经验。传统的膜制备方法,即不断改变膜配方,制成不同结构的膜,测试其性能,经过大量实验筛选出适合于某种用途的膜,整个过程“暗箱”操作,存在很大的盲目性。按照这样的方法,从配方选择、制备到测试,研究周期长,整个研究过程存在着较大的盲目性,使得分离膜的开发速度慢,不能满足工业部门对分离膜应用的需求。为了使分离膜制备摆脱依赖经验的状况,代之以理论指导为主的方法。本书的编著者在前人研究的基础上,开展了多年的成膜过程动力学研究。秦培勇等采用聚砜(PSF)、聚醚砜(PES)、酚酞型聚醚砜(PES-C,PEK-C)、杂萘联苯类聚醚砜酮(PPESK、PPES、PPEK)、聚偏氟乙烯(PVDF)等10多种聚合物膜材料,不同的溶剂及添加剂体系,先后对400多种不同的铸膜液体系的成膜过程动力学进行了研究,得出有指导意义的结果,本节中就相关研究成果进行介绍。
①凝胶动力学实验 实验装置如图3-6所示。

图3-6 凝胶动力学实验装置
主要性能参数:
a.高速拍摄和存储,每秒存储实验图片12张;
b.图片清晰度高;
c.0.1s的凝胶速度时间测试精度和1μm的距离测试精度。
凝胶动力学实验原理见图3-7。

图3-7 凝胶动力学实验原理示意图
1—数字摄像头;2—高精密度显微镜;3—特制的显微镜附件;4—温度传感器;5—湿度传感器;6—转轮除湿机;7—空调机;8—工作站;9—恒温恒湿超净工作室
实验内容及方法:首先将超净工作室内的温度、湿度、铸膜液和非溶剂的温度控制在所需的实验条件下;再将1 mL的铸膜液放在特制的显微镜附件上,调节好显微镜;然后迅速将1 mL的凝胶液导入附件内。用显微镜观察铸膜液的凝胶过程,原位观测和记录凝胶过程中膜孔生长及膜结构演化发展过程,并通过计算机自动存储下来。测定凝胶前锋位移随时间变化的关系,获得凝胶动力学曲线。
现以PPESK的成膜为例,展示其在改变添加剂种类、添加剂浓度、凝胶浴组成及温度等条件下制备非对称超滤膜时,不同铸膜液体系不同时刻所拍摄到的膜结构照片(简称动力学照片),来说明动力学实验研究在膜结构调控中的作用和意义。
②成膜凝胶过程中膜孔生长及膜结构演化发展状况 凝胶动力学实验,可以在线观测和记录凝胶过程中膜孔结构生长和演化过程,测定凝胶前锋位移随时间的变化关系,借助相关软件对图像进行处理,得出凝胶动力学曲线及膜结构转变的边界条件。本节中铸膜液体系组成均为质量分数。
图3-8、图3-9是采用不同添加剂的铸膜液体系,不同时刻生成的膜孔结构的动力学照片。图3-8是指状孔结构,图3-9是海绵状结构。动力学照片显示添加剂种类不同,所得到的膜结构形态是不同的。

图3-8 典型指状孔生长的凝胶动力学照片
铸膜液体系:PPESK/NMP/PEG;PPESK浓度:14%;PEG浓度:2.5%;凝胶介质:水

图3-9

图3-9 典型海绵状孔结构生长的凝胶动力学照片
铸膜液体系:PPESK/NMP/PVP;PPESK浓度:18%;PVP浓度:10%;凝胶介质:水
图3-10是以草酸(OA)为添加剂时,不同草酸浓度铸膜液的膜结构变化动力学照片,图3-11是其凝胶动力学曲线。

图3-10 添加不同浓度草酸时膜结构演化的凝胶动力学照片
铸膜液体系PPESK/NMP/OA;PPESK浓度:15.6%;凝胶介质:水;凝胶温度:25℃
由图3-10可见,膜结构从最初指状孔结构向海绵状结构过渡。当草酸浓度为6.7%时,膜结构由指状完全变为海绵状结构。从图3-11可以看出,随着草酸浓度的增加,凝胶速度增大,在同一时刻凝胶前锋的位移加快,动力学曲线向远离横坐标方向偏移。膜的性能测试表明,该体系制成的中空纤维膜的通量随草酸添加剂量的增加而增加。结果如表3-4所示。

图3-11 草酸添加剂浓度对铸膜液体系凝胶速率的影响
铸膜液体系PPESK/NMP/OA;PPESK浓度:15.6%;凝胶介质:水;凝胶温度:25℃;添加剂草酸的浓度为0,1.67%,5%,6.7%
表3-4 以草酸为添加剂的PPESK中空纤维超滤膜的性能测试结果

图3-12是改变凝胶介质的组成,在凝胶浴中加入溶剂时膜结构发生演化的动力学照片,图3-13是凝胶速率变化图,表3-5是凝胶介质中加入溶剂时膜的水通量变化情况。从图、表中可以看出,体系的凝胶速率随着凝膜浴中NMP浓度的增加而减小。凝胶浴中NMP含量增大,其化学位增大,铸膜液和凝胶浴间的化学位梯度也减小,铸膜液中的NMP溶剂就不容易向凝胶浴扩散,而凝胶浴中的水难于向铸膜液中扩散,因此凝胶速率减小,膜的水通量下降。膜结构逐渐由指状孔转变为海绵状孔。

图3-12 凝胶介质中加入NMP时PPESK铸膜液的凝胶动力学照片
铸膜液体系PPESK/NMP/Tween80;PPESK浓度:15.6%;Tween80浓度:6.7%;凝胶温度:25℃;凝胶浴中NMP的浓度从上向下分别为0%,20%,40%,60%,80%;拍照时间从左到右依次是0s,1s,60s

图3-13 凝胶浴中溶剂含量对PPESK凝胶速率的影响
铸膜液体系PPESK/NMP/Tween80;PPESK浓度:15.6%;Tween80浓度:6.7%;凝胶温度:25℃;凝胶浴中NMP的浓度从上向下分别为0%,20%,40%,60%,80%
表3-5 凝胶浴中加入不同溶剂含量时PPESK膜的性能测试结果

以上非对称膜成膜的凝胶动力学实验表明,高精密度显微镜/数字面阵/高速摄像及存储实验系统,是进行凝胶动力学实验研究的有效手段;通过该实验系统,可以原位可视化观测溶剂和非溶剂相互传质及相分离过程,真实再现膜孔生长及膜结构演化过程,借助相关软件对图像进行处理,得出凝胶动力学曲线,找到引起膜结构转变的边界条件。这一研究成果得到国际专家的认可。J.Membrane Science期刊审稿人认为:“The apparatus has made possible to allow people to clearly look at the membrane formation process,which is a significant progress in membrane preparation”。
③动力学图像与实际成膜结构的相关性 大量实验表明,实验动力学图像与最终膜结构有很好的一致性。图3-14~图3-17等给出了几组有代表性的动力学图像照片与成膜后电镜照片的对照图。分别是具有典型的孔分布均一的指状结构的膜;孔分布不均一的指状结构的膜;带有指状结构的海绵状结构膜;海绵结构的膜等。

图3-14 孔分布均一的指状结构的膜
PPESK:18%;溶剂:NMP;凝胶介质:水;草酸:2.5%;凝胶温度:60℃

图3-15 孔分布不均一的指状结构的膜
PSF:18%;溶剂:NMP;凝胶介质:水;凝胶温度:60℃

图3-16 指状结构与海绵状混合结构膜
PPESK:16%;溶剂:NMP;凝胶介质:水;草酸:7.5%;凝胶温度:60℃

图3-17 海绵状结构的膜
PPESK:16%;溶剂:NMP;凝胶介质:水;PVP:7.5%;凝胶温度:25℃
从图中可以看出,膜的凝胶动力学照片和膜的电镜照片有很好的一致性,说明凝胶动力学实验能较准确地反映膜孔结构。研究表明可以用凝胶动力学实验来预测膜结构,快捷方便地表征膜结构,迅速找寻结构、性能优良的超滤膜的制备工艺条件。
在其他膜材料的成膜过程动力学研究实验中都得出了相同的结论,即凝胶速率与膜制备各参数之间,凝胶速率与膜结构与性能之间有很好的相关性;动力学图像与最终膜结构有很好的一致性。因此通过动力学的研究使膜制备和膜结构与性能之间架起相互联系的桥梁,可以用动力学实验来预测和表征膜的结构,指导制膜条件的选择及优化。这就改变了传统制膜“暗箱”操作的状况,把盲目的实验转变成有指导的实验,提高了非对称膜的研发效率。秦培勇等采用这样的方法,成功研制成高性能的PPESK、PES、PSF中空纤维超滤膜,图3-18是一种大通量的聚砜超滤膜产品的电镜照片,该膜具有薄而表面开孔率高的皮层;高度贯通的网络结构的多孔支撑层;膜的断面从内到外孔径逐渐增大,在0.1MPa压力下,温度为20℃时,膜的纯水通量为1200L/(m2·h),该膜产品已在工程中使用。

图3-18 一种大通量的聚砜超滤膜产品的电镜照片
3.2.2.2 热致相分离法
热致相分离法(TIPS法,简称热法)是20世纪70年代Castrol提出的一种制备多孔膜的新方法,近10多年来开发成工业上的实用技术。
热致相分离法制膜是指将聚合物与稀释剂在高温下混合溶解成均相溶液,将溶液制成平板状或纺制成中空纤维状后,经降温冷却,体系发生液-液或液-固相分离,聚合物固化成膜后,再将稀释剂萃取(或蒸发)除去,其中的孔是由稀释剂所占据的位置所形成的。热法制膜中,稀释剂是一种高沸点、低分子量的化合物,在常温下,它与聚合物不混溶,当升高温度时能与聚合物以任意比混溶,且不与聚合物发生化学反应。制膜的初始温度必须小于稀释剂的沸点,在初始温度下,聚合物性质稳定。由于它的基本特征是“高温溶解,低温分相”,所以称为“热致相分离”法。
(1)制膜方法及工艺
热致相分离法制膜工艺流程如图3-19所示。

图3-19 热致相分离法制膜工艺流程示意图
热致相分离制备聚合物多孔膜的方法通常由下列四个步骤所组成:①选择一种高沸点、小分子量的,在室温下是固态或液态的且与聚合物不相溶的稀释剂,当升高温度时该稀释剂能与聚合物形成均相溶液;②将该均相的聚合物溶液预制成所需要的形状,如平板膜或中空纤维膜的形状;③在冷却或等温淬冷过程中实现体系的液-液或液-固相分离;④用溶剂萃取或减压蒸馏的办法脱除分相后聚合物凝胶中的稀释剂,再经过干燥或亲水化处理步骤得到多孔膜。
在热致相分离法制膜过程中,制膜高聚物/稀释剂体系及制膜条件的改变,会引起体系热力学状态和动力学模式的变化,从而对膜结构与性能产生影响,如表3-6所示为影响膜结构性能的热力学因素和动力学因素。
表3-6 热致相分离法制膜时影响膜孔结构及性能主要制膜因素

(2)制膜各因素对膜结构与性能的影响
①高聚物浓度的影响 聚合物浓度的高低会影响聚合物/稀释剂体系的相分离状态,从而改变膜孔形貌、孔隙率、孔分布及孔径。降低高聚物溶液的浓度会促进液-液分相,抑制聚合物的结晶,容易得到孔结构贯通性好的膜。同时聚合物浓度增加,膜的孔隙率会降低,膜强度会增加。
②聚合物分子量的影响 聚合物分子量主要通过以下两个方面对相分离热力学和动力学产生影响。聚合物分子量的改变,影响了聚合物与稀释剂的相互作用,进而导致体系热力学状态的改变。
聚合物分子量增加,聚合物与稀释剂的相容性变差,这是因为长链分子更具有分凝的倾向。聚合物分子量越大,铸膜液的最高共熔点温度越高,而动力学结晶温度没有较大变化。低分子量时,形成了大的包腔状孔结构;而高分子量时,形成了孔径较小的相互贯通的孔结构。由此可见,聚合物分子量的变化影响了体系的分相状态,导致孔的大小和形态均发生变化。
聚合物分子量的改变对相分离动力学也会产生影响。研究发现,随聚合物分子量的增加聚合物黏度增加,抑制了液-液分相的动力学过程,使液滴增长速度较慢而形成较小的孔。
③稀释剂种类 稀释剂种类对膜结构的影响主要体现在稀释剂与聚合物之间的相互作用,它直接影响相分离状态和相分离的机理。稀释剂与聚合物之间的相互作用强弱可以用相互作用参数来度量。随着体系相互作用参数χ增大,聚合物与稀释剂之间的相互作用减弱,发生液-液相分离的区域增大,相分离开始时的温度逐渐升高。
选择与聚合物有合适相互作用的单一稀释剂往往比较困难,而采用混合稀释剂的方法更加容易获得理想的相互作用参数。
共混稀释剂体系中,体系的雾点温度和结晶温度降低,膜的结构将由液-液相分离形成的网络孔结构转变为固-液相分离形成的球晶结构。稀释剂的流动性和结晶性也会对相分离过程产生影响。高结晶温度的稀释剂的结晶过程在聚合物结晶前发生,会限制聚合物结晶过程,对膜结构产生影响。
④冷却速率 冷却速率是热致相分离法制膜过程中重要的动力学参数。冷却速率能改变相分离机理,影响相分离速率及相分离的时间,从而对孔的结构和形态产生影响。在液-液相分离情形下,降低冷却速率微孔尺寸变大。这是因为有更长的液滴粗化生长时间,使微孔尺寸增大。如果冷却速率过快,体系迅速越过亚稳区而进入不稳区,按照旋节线分相机理发生液-液相分离形成双连续结构。在固-液相分离情形下,增加冷却速率,晶粒尺寸变小。这是因为冷却速率的增加伴随着成核点数目的增加及固化时间的缩短。
⑤后处理工艺 在后处理工艺中,萃取剂的种类和干燥方式会对膜结构产生一定的影响。聚合物与萃取剂、稀释剂之间的亲和性的竞争以及聚合物分子链的自由排列可以对膜产生溶胀、收缩或者保持原有尺寸的影响。萃取剂的种类会影响膜的孔隙率、孔径以及渗透性能,随着萃取剂的表面张力和沸点的增加,膜孔的尺寸有减小的趋势。通过冷冻干燥的方法比室温空气中干燥的方法形成的膜尺寸的收缩要小。
⑥其他因素 除上述影响膜结构和性能的因素外,成核剂的加入也会对膜结构产生影响。研究发现,成核剂的加入可以提高结晶温度,增加结晶速率,减小了球晶的尺寸。
(3)热法制备PVDF超滤膜的结构形态优化与选择
研究表明采用不同的稀释剂体系,不同配方、配比,可以制出不同的膜结构。比较典型的主要有五种,即球晶结构、束晶结构、叶片晶结构、胞腔结构及三维互穿网络结构,如图3-20~图3-24所示。

图3-20 球晶结构

图3-21 束晶结构
聚合物/稀释剂体系的液-固相分离会导致球晶结构的形成,如图3-20所示,由于球晶之间相互联系不紧密,因此膜强度很差,没有实用价值。图3-21所示的束晶结构,图3-22所示的叶片晶结构,也是通过液-固相分离而形成的,这种膜强度好,但膜孔贯通性差,一般通量较小。图3-23所示的是一种胞腔结构,它通过液-液相分离而形成,这种膜强度高,但孔之间贯通性差,甚至有的是封闭的胞腔,通量很小,没有实用价值。第五种如图3-24所示,为三维互穿网络结构,是通过液-液相分离而形成的,由于孔结构高度贯通,高分子网络相互拉扯,因此,膜的强度高,通量大,是一种理想的膜结构,但其制备难度很大,得到这种结构十分不易。

图3-22 叶片晶结构

图3-23 胞腔结构

图3-24 三维互穿网络结构
图3-25为其中一种优化条件下制备的PVDF中空纤维超滤膜断面扫描电镜照片图。该膜具有密度梯度孔结构,膜外表面孔径最小,断面外边缘孔径较小,从外向内孔径逐渐增大,内表面孔径最大。是典型的非对称型结构的中空纤维超滤膜,膜断面为三维互穿网络结构。膜外表面的平均孔径为40nm,纯水通量为600~700L/(m2·h)(水温为20℃,操作压力为0.1 MPa),拉伸强度为6.0~7.0MPa,断裂伸长率为90%~120%。

图3-25 已经商品化的热法中空纤维膜的电镜照片
注:上面4张照片除外表面放大40000倍外,其余的均放大10000倍
这种热法制备的PVDF中空纤维超滤膜已由膜华科技投入工业化生产,并在大型市政饮用水工程、工业废水再生回用工程中推广应用。
3.2.3 超滤膜组件
所有膜装置的核心部分都是膜组件,即按一定技术要求将膜组装在一起的组合构件。膜组件一般包括膜、膜的支撑体或连接物,与膜组件中流体分布有关的流道、膜的密封、外壳以及外接口等。在开发膜组件的过程中,必须考虑以下几个基本要求:流体分布均匀,无死角;压力损失小,具有良好的机械稳定性、化学稳定性和热稳定性;装填密度大;制造成本低;更换膜的成本尽可能低;易于清洗。
超滤膜组件产品,特别在我国是膜产业中生产企业最多,产品种类、型号最丰富,产能最大的膜产品,能与国外产品相抗衡。其在饮用水处理及废水处理回用工程中广泛应用,工程实例多达千余个。从结构上看,超滤膜组件可分为两种类型共五种结构形式,即管式(管式膜组件、毛细管膜组件和中空纤维膜组件)及板式(平板式膜组件、卷式膜组件)。由于卷式膜组件首先是为反渗透过程开发的,本书将在反渗透一章作介绍,本章不作重复。
(1)毛细管膜组件
毛细管膜具有自支撑的特点。毛细管膜组件是将很多的毛细管膜安装在一个膜组件中,如图3-26所示。膜的自由端用环氧树脂、聚氨酯或硅橡胶封装。膜组件的安装及操作方式有两种:①膜的皮层在毛细管内侧,原料液流经毛细管内腔,在毛细管外侧收集渗透物[图3-26(a),从内向外流动式];②膜的皮层在毛细管的外侧,原料液从毛细管外侧进入膜组件,渗透物通过毛细管内腔[图3-26(b),从外向内流动式]。这两种方式的选择主要取决于具体应用场合,要考虑到压力、压降、膜的种类等因素。组件的装填密度为600~1200m2/m3,介于管式膜组件与中空纤维膜组件之间。

图3-26 毛细管膜组件示意图
毛细管膜组件特点:投资费用较低,对料液中浊度要求比较宽松,膜装填面积较大。缺点是操作压力受到限制,对系统操作出现的错误比较敏感。
(2)中空纤维膜组件
中空纤维膜也是自支撑的,但膜丝直径比毛细管膜细得多。中空纤维膜组件是装填密度最高的一种膜组件构型,单个组件内能装填几十万到上百万根中空纤维超滤膜丝,装填面积可以达到30000m2/m3。其主要优点是膜的装填密度高,产水量大;制造方便,便于大型化和集成化;成本低;应用广泛。主要缺点是膜面污垢去除困难,不能进行机械清洗,只能采用化学清洗;对进料液要求有严格的预处理。
目前,为了最大限度地减少污染和浓差极化,商品化的中空纤维膜组件,在流道设计时,采用横向流代替切向流,在膜组件中装有一个多孔的中心管,使原料垂直于纤维流动,强化了边界层的传质过程,同时纤维本身起到湍流强化器的作用。
在实际工程中广泛使用的中空纤维膜组件的形式主要有三种,即柱式膜组件(见图3-27)、帘式膜组件(见图3-28)、集束式膜组件(见图3-29)。其中柱式膜组件又分为外压膜组件和内压膜组件;帘式膜组件中,中空纤维膜丝全裸在待处理水环境中;集束式膜组件分为全裸和半裸两种形式。

图3-27 柱式膜组件

图3-28 帘式膜组件

图3-29 集束式膜组件
图3-30、图3-31分别为柱式内压膜组件和柱式外压膜组件的错流过滤示意图。对于内压法错流过滤,从图3-30可见,原水从膜的一端进入中空纤维膜丝内部,在压力的作用下(内高外低)向膜丝外部渗透,污染物被膜内壁截留,清水透过膜壁在中空纤维膜丝外汇聚成产水。被截留在膜丝内的污染物和少量原水从膜丝另一端流出,形成浓水。对于外压法错流过滤,从图3-31可见,原水在中空纤维膜丝外部(膜丝之间)沿丝外壁轴向流动的过程中,在压力的作用下(外高内低)向膜丝内部渗透,污染物被膜外壁截留,清水透过膜壁在中空纤维膜丝内汇聚成产水。对于外压全流过滤,从图3-32可见,原水在压力的作用下(外高内低),从中空纤维膜外部向膜丝内部渗透,污染物被膜外壁截留,清水透过膜成为产水,全流过滤不产生浓水。浸没式组件、家用饮水器滤芯的过滤形式往往采用外压法全流过滤。

图3-30 内压法错流过滤示意图

图3-31 外压法错流过滤示意图

图3-32 外压法全流过滤示意图
(3)管式膜组件
与毛细管和中空纤维膜不同,管式膜不是自支撑的,膜被固定在一个多孔的不锈钢、陶瓷或塑料管内。管直径通常6~24mm,每个膜组件中膜管数目一般为4~18根,当然也不局限于这个数目。如图3-33所示,原料一般流经膜管内,渗透物通过多孔支撑管流入膜组件外壳。

图3-33 管式膜组件
管式膜组件的主要优点是能有效地控制浓差极化;可大范围地调节料液的流速,流动状态好;污垢容易清洗;对料液的预处理要求不高并可处理含悬浮固体的料液。其缺点是投资和运行费用较高;装填密度较低,≤300m2/m3。
(4)板框式膜组件
板框式膜组件结构中的基本部件是:平板膜、支撑板与进料边起流体导向作用的进料板。将这些部件以适当的方式组合堆叠在一起,构成板框式膜单元。
板框式膜单元,是由两张膜一组构成夹层结构,两张膜的膜面相对,由此构成原料腔室和渗透物腔室。在原料腔室和渗透物腔室中安装适当的间隔器。采用密封环和两个端板将一系列这样的膜单元安装在一起以满足一定的膜面积要求,这便构成板框式膜组件。
这类膜组件的装填密度约为100~400m2/m3。图3-34为板框式膜组件流道示意图。为减少流量分布不均的问题,膜组件中设计了挡板。这种板框式膜组件的优点是,每两片膜之间的渗透物都是被单独引出来的,可以通过关闭各个膜单元来消除操作中的故障,而不必使整个膜组件停止运转。缺点是在板框式膜组件中需要个别密封的数目太多,同时内部压力损失也相对较高(取决于流体转折流动的情况);价格较昂贵板框式膜组件的费用一般为500~1000美元/m2,而膜的更换费用为30~100美元/m2。

图3-34 板框式膜组件流道示意图
3.2.4 国内外超滤膜产品简介
我国生产和销售超滤膜的公司有百余家,本书列举了几家有代表性公司的产品,见表3-7;表3-8是国外公司在我国销售的膜产品,更详细的介绍可参见各公司的产品手册。