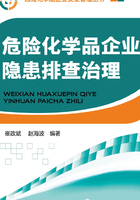
第三节 基本概念
一、安全生产事故隐患
安全生产事故隐患(隐患、事故隐患或安全隐患),是指生产经营单位违反安全生产法律、法规、规章、标准、规程和安全生产管理制度的规定,或因其他因素在生产经营活动中存在可能导致事故发生的物的危险状态、人的不安全行为和管理上的缺陷。
在事故隐患的三种表现中,物的危险状态是指生产过程或生产区域内的物质条件(如材料、工具、设备、设施、成品、半成品)处于危险状态;人的不安全行为是指人在工作过程中的操作、指示或其他具体行为不符合安全规定;管理上的缺陷是指在开展各种生产活动中所必需的各种组织、协调等行为存在的缺陷。
二、事故隐患的分级
1.一般事故隐患
可能造成一次死亡1~2人,或一次重伤3~9人,或直接经济损失100万元以下的事故隐患。
2.较大事故隐患
可能造成一次死亡3~9人,或一次重伤10~29人,或直接经济损失500万元以下的事故隐患。
3.重大事故隐患
可能造成一次死亡10~29人,或一次重伤30人以上,或直接经济损失500万元以上至1000万元以下的事故隐患。
4.特大事故隐患
可能造成一次死亡30人以上,或直接经济损失1000万元以上的事故隐患。
三、事故隐患类别
①火灾;②爆炸;③中毒和窒息;④水害;⑤坍塌伤害;⑥滑坡伤害;⑦泄漏伤害;⑧腐蚀伤害;⑨电击伤害;⑩坠落伤害;机械伤害;
煤与瓦斯突出伤害;
公路设施伤害;
铁路设施伤害;
公路车辆伤害;
铁路车辆伤害;
水上运输伤害;
港口码头伤害;
空中运输伤害;
航空落伤害;
其他伤害。
四、危险化学品企业事故隐患分类
①生产工艺类;②机械设备类;③电气仪表类;④建构筑物类;⑤作业环境类;⑥技术管理类。
五、隐患排查
隐患排查是指生产过程经营单位组织安全生产管理人员、工艺技术人员和其他相关人员对本单位的事故隐患进行排查,并对排查出的事故隐患,按照事故隐患的等级进行登记,建立事故隐患档案信息等,换句话说就是,识别事故隐患的存在并确定其特性和等级的过程。
六、隐患排查模式
危险化学品企业应建立隐患排查模式,即“隐患排查体系→风险评价体系→监控治理体系”。实现“查找隐患→风险评估→整改治理→预防事故”闭环管理的安全生产长效机制。隐患排查体系是:公司(厂)、车间、班组定期排查和岗位自查;风险评价体系:由专业技术人员组成评价组织,定期进行作业活动的风险评估;监控治理体系:公司(厂)、车间、班组和岗位进行分级监控治理。
七、隐患治理
隐患治理是指消除或控制隐患的活动或过程。对排查出的事故隐患,应当按照事故隐患的等级进行登记,建立事故隐患信息档案,并按照职责分工实施监控治理。对于一般事故隐患,由于其危害和整改难度较小,发现后应当由生产经营单位(车间、分厂、班组等)负责人或者有关人员立即组织整改。对于重大事故隐患,由生产经营单位主要负责人组织制定并实施事故隐患治理方案。
八、隐患排查步骤
(1)编制隐患排查计划,制定隐患排查表。排查表要有项目、内容。计划要结合实际,项目要具体,内容要全面。排查之后要能获取有价值的信息。
(2)组织检查人员,进行有效工作。根据检查要求挑选排查人员,隐患排查人员要有一定的专业知识和一定的工作经验,有对工作高度负责的责任心。
(3)实施隐患排查。查阅文件和记录,检查作业规程、安全技术措施、安全生产责任制以及相关记录等是否齐全、有效,是否在现场得到执行、落实。并对生产作业现场进行观察,对所有生产人员、生产设备、安全设施、作业环境、操作行为等方面进行系统检查,查找人的不安全行为、物的不安全状况、环境的不安全状态以及事故征兆等。
(4)判断处理。隐患排查结束后,整理排查记录,找出存在的问题和隐患,进行分析评价,确定监控等级,提出整改意见,采取相应措施,跟踪复查验收,实现隐患管理闭环。
九、隐患排查治理体系
(1)掌握企业底数和基本情况。根据企业规模、管理水平、技术水平和危险因素等条件,掌握企业底数和基本情况,对企业进行分类分级,建立“按类分级、依级监管”的模式。
(2)制定隐患排查标准。依据有关法律法规、标准规范和安全生产标准化建设的要求,结合各地区、各行业(领域)实际,以安全生产标准化建设评估标准为基础,细化隐患排查标准,明确各类企业每项安全生产工作的具体标准和要求,使企业知道“做什么、怎么做”,使监管部门知道“管什么、怎么管”,实现安全隐患排查治理工作有章可循、有据可依。
(3)建立隐患排查治理信息系统。包括企业隐患自查自报系统,安全隐患动态监管统计分析评价系统等内容,形成既有侧重又统一衔接的综合监管服务平台,实现安全隐患排查治理工作全过程记录和管理。
(4)明确安全监管职责。在地方党委、政府的统一领导下,进一步理顺和细化有关部门和属地的安全监管职责,明确“管什么、谁来管”的问题。
(5)明确安全监管方式。在分类分级的基础上,对企业在监管频次、监管内容等方面实行差异化监管监察,提高监管工作的针对性和有效性。
(6)制定安全生产工作考核办法。突出工作过程和结果量化,将有关部门和企业建设安全隐患排查治理体系、日常执法检查等相关工作完成情况过程的各项指标,纳入安全生产工作年终考核,提高监管的约束力和公信力。
十、隐患识别的方法
事故隐患的识别是评估与治理的前提,识别就是发现与鉴别。安全系统工程提供了许多有效的辨别事故隐患的方法。
(1)安全检查表法。是依据相关的标准、规范,对工程、系统中已知的危险类别、设计缺陷以及与一般工艺设备、操作、管理有关的潜在危险性和有害性进行判别检查。为了避免检查项目漏项,事先把检查对象分割成若干系统,以提问或打分的形式,将检查项目列表,这种表就称为安全检查表。
(2)技术鉴别法。即通过技术鉴定、技术论证、测试等形式对设施装备进行鉴别分析,发现隐患所在。如压力容器的安全装置;机动车辆的转向、制动及灯光系统,电气设备的接地接零及绝缘设施;通风防火装置及其他隔离、密闭、抗爆、泄爆、联锁、自控等安全装置都可以定期地按技术标准进行鉴定,找出安全隐患。用测试手段对有毒有害气体、粉尘等进行检测,发现超标的隐患所在等都是技术鉴定法之列。
(3)信息经验判别法。即根据企业的内外部信息,借鉴直接、间接的事故教训,对照本企业、本系统检查分析、判定是否存在类似问题,以此识别事故隐患的方法,这种方法一靠信息、二靠经验,故称之信息经验判别法。
(4)预先危险分析。又称初步危险分析,主要用于危险物质和装置的主要工艺区域等进行分析。其功能主要有:大体识别与系统有关的主要危险;鉴别产生危险的原因;估计事故出现对人体及系统产生的影响;判定以识别的危险性等级,并采取消除或控制危险性的技术和管理措施。
(5)故障假设分析。故障假设分析方法(What If Analysis)是对某一生产过程或工艺过程的创造性分析方法。使用该方法时,要求人员要对工艺熟悉,通过提出一系列“如果……怎么办?”的问题,来发现可能和潜在的事故隐患,从而对系统进行彻底检查的一种方法。在危险化学品企业的隐患排查治理工作中,该方法常被采用。
(6)故障假设/安全检查表分析。这是一种故障假设/安全检查表分析两种方法的联合体分析方法。故障假设分析方法鼓励思考潜在的事故和后果,它弥补了基于经验的安全检查表编制时经验的不足。相反,检查表可以把故障假设分析方法更系统化。因此出现了安全检查表分析与故障假设分析组合在一起的分析方法,以便发挥各自的优点,互相取长补短弥补各自单独使用时的不足。这种方法在企业隐患排查治理中使用比较普遍。
(7)故障类型和影响分析(FMEA)。故障类型和影响分析起源于可靠性技术,其基本内容是找出系统的各个子系统或元件可能发生的故障出现的状态(即故障类型),搞清每个故障类型对系统安全的影响,以采取措施予以防止或消除,该方法能查明元件发生各种故障时带来的危险性,是一种较为完善的分析方法,它既可用于定性分析也可用于定量分析,是企业隐患排查治理的重要方法之一。
(8)危险和可操作性分析(HAZOP)。危险和可操作性分析是过程系统(包括流程工业)的危险分析中一种应用最广的评价方法。是一种形式结构化的方法,该方法全面、系统地研究系统中每一个元件,其中重要的参数偏离了指定的设计条件所导致的危险和可操作性问题。主要通过研究工艺管线和仪表图、带控制点的工艺流程图(P&ID)或工厂的仿真模型来确定,重点分析管路与每一个设备操作所引发潜在事故的影响。采用经过挑选的关键词表,来描述每个潜在的偏差。最终识别出所有的故障原因,得出当前的安全保护装置和安全措施。在危险化学品企业的隐患排查中也常用此方法。
(9)故障树分析(FTA)。故障树分析是美国贝尔电报公司的电话实验室于1962年开发的,它采用逻辑的方法,形象地进行危险的分析工作,特点是直观、明了,思路清晰、逻辑性强,可以做定性分析,也可以做定量分析,体现了以系统工程方法研究安全问题的系统性、准确性和预测性。它是安全系统工程的主要分析方法之一。一般来说在企业隐患排查工作中也常用用到此方法。
(10)保护层分析。保护层分析(Layer Of Protection Analysis,简称LOPA)是在定性危害分析的基础上,进一步评估保护层的有效性,并进行风险决策的系统方法,其主要目的是确定是否有足够的保护层使过程风险满足企业的风险可接受标准。LOPA是一种半定量的风险评估技术,通常使用初始事件频率、后果严重程度和独立保护层(IPL)失效频率的数量级大小来近似表征场景的风险。
十一、隐患治理遵循的原则
(1)彻底清除原则。即采用无危险的设备和技术进行生产或称为实现系统的本质安全化。这样即使人员操作失误或个别部件发生故障时都会因有完善的安全装置而避免伤亡事故的发生。
(2)降低隐患因素数值的原则。即隐患因某种原因不能消除时,应使隐患导致事故危害程度降低到人们可以接受的水平。如作业中的粉尘,不能完全排出时,则可加强个人防护,达到降低吸入量的目的。
(3)距离防护原则。某些隐患因素的作用,依然与距离有关的规律减弱。因而采用距离防护即可有效降低其危害。如对噪声、辐射的防护等。
(4)时间防护原则。即使人处在隐患危险作用的环境中的时间尽量缩短到安全限度之内。
(5)屏蔽原则。在隐患危害作用的范围内设置障碍。如吸收放射线的铅屏蔽。
(6)坚固原则。提高结构强度,增加安全性。
(7)薄弱环节原则。利用薄弱元件使危险因素来达到危险值之前预先破坏。如保险丝、安全阀、泄压膜等。
(8)不接近原则。使人不落入危险因素作用的地带,如安全栅栏等。
(9)闭锁原则。以某种方式保证一些元件,强制发生相互作用,达到安全操作。如起重机械的超负荷限制器和行程开关等。
(10)取代原则。对无法消除危险的隐患场所,用自动控制器或机器人代替人操作。
十二、事故隐患评估的基本步骤
(1)准备阶段。主要是熟悉生产工艺、厂区布置、设备配备情况、人员配置情况、收集有关资料等。寻找事故隐患形成的条件和所在地点,在这一阶段一定要做到四个字即“严、细、实、全”。
(2)定性评估阶段。主要运用安全监察表和安全系统工程原理,在准备阶段的基础上,寻找事故隐患形成的原因及所在生产工艺流程、设备、设施、场所、岗位进行粗评估,然后利用因果分析图和排列图,确定评估的优化顺序。
(3)定量评估阶段。将定性评估阶段粗评估出的事故隐患,再进一步深化细化,分化到每个子系统和单元、岗位、人头,然后按照危险度的大小,造成事故的概率进行逐项评分,根据评分总和画出三个危险等级,制定出相应的评估、治理对策和措施。
(4)再评估阶段。根据目标值,参照不同行业、同类事故所造成的人身设备事故进行再评估,找出不足和缺陷。
(5)量化计算阶段。主要运用事故树(FTA)、等级系数法等进行深评估,寻找最佳治理对策和方法,作出综合性判断、评估和治理方案,以求得最优、最理想的效果——目标值,转入下一轮评估。
十三、无隐患管理
无隐患管理是一种系统安全的管理方法,它是贯彻“安全第一、预防为主、综合治理”方针重要的途径,它的推行和运用不仅能促进安全系统工作的运用和推广,而且对促进安全管理的“专群”结合,实现安全生产的常态化、制度化也必将起到积极的作用,必须依靠有效的管理方法和内容,才能保证实现无隐患管理。一是把查找和消除隐患的程度及效益,作为评价单位安全工作的一项重要指标。二是各企业要结合自身生产特点,研究确定隐患的分类、分级的检测和处理。三是自上而下建立隐患登记、统计制度,建立隐患检查表,提高安全检查效率。四是不断提高和完善安全技术检测手段,保障无隐患管理的科学性。五是切实建立对隐患查找和整改效益的约束及激励机制,推动无隐患管理持续健康发展。