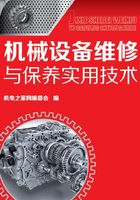
1.4 橡胶挤出机械
1.4.1 橡胶挤出机简介
橡胶挤出机,是橡胶工业的一种基本设备,是影响产品质量的关键设备之一,在轮胎和橡胶制品的生产过程中起着非常重要的作用。橡胶挤出机的发展经历了柱塞式挤出机、螺杆型热喂料挤出机、普通型冷喂料挤出机、主副螺纹冷喂料挤出机、冷喂料排气挤出机、销钉型冷喂料挤出机、复合型挤出机等阶段。如图1-3所示。

图1-3 橡胶挤出机
1.4.2 橡胶挤出机的主要分类
(1)柱塞式
挤出机起源于18世纪,英格兰的Joseph Bramah于1795年制造的用于制造无缝铅管的手动活塞式压出机被认为是世界上第一台挤出机。从那时开始,在19世纪前50年内,挤出机基本上只应用于铅管的生产、通心粉和其他食品的加工、制砖及陶瓷工业。
在挤出机作为一种制造方法的发展过程中,第1次有明确记载的是R.Brooman在1845年申请的用挤出机生产固特波胶电线的专利。固特波公司的H.Bewlgy随后对该挤出机进行了改进,并于1851年将它用于包覆在Dover和Calis公司之间的第1根海底电缆的铜线上。在此后的 25年内,挤出方法逐渐重要,并且逐渐由电动操纵的挤出机迅速替代了以往的手动挤出机。初期机械操纵的柱塞式挤出机生产了成千上万千米的绝缘电线和电缆,从而牢固地确立了挤出法用于生产电缆的地位。早期生产电缆的挤出机无论是手动的、机械的或者液压的,全都是柱塞式的。在这种生产过程中,柱塞将热的古塔波胶压入到通有铜导线口模中,古塔波胶从口模中挤出,这样就包覆在铜导线上形成绝缘层。
(2)螺杆型
1870年出现的橡胶挤出机是热喂料挤出机。它喂入的胶料要求必须经过热炼,且供料均匀、稳定、等速,料温保持在50~70℃。其螺杆短,螺纹沟深,均化效果不理想。从20世纪70年代起。一度出现长径比变小的现象。由于热喂料挤出机可连续挤出、操作简单、生产效率高、挤出成品形状稳定,在很多制品的生产工艺中,仍然采用热喂料挤出机。在轮胎生产中用于各种胎面、各种型胶的挤出以及在胶管、电缆及其他橡胶制品的生产中用于包胶及胶坯的挤出。
(3)普通型
冷喂料挤出机出现于20世纪40年代,20世纪60年代开始得到推广和普及,20世纪80年代成为发展主流。至20世纪90年代初期,欧美等发达国家用冷喂料挤出机生产的产品已经占到生产总量的95%。有分离型螺杆挤出机、挡板螺杆挤出机、空穴式螺杆挤出机、传递式混炼挤出机、销钉螺杆挤出机和多流道传递混合螺杆(MCT)挤出机等。从设备结构来看,冷喂料挤出机与热喂料挤出机相比,一般有较长的机身,长径比(L/D)为8~20,螺纹沟较浅。由于机身长、功能多,进料温度低,其功率比热喂料挤出机大得多,约相当于同规格热喂料挤出机的2~4倍。如德国贝尔斯托夫公司生产的直径为250mm的冷喂料挤出机的功率为500kW,而同规格的热喂料挤出机仅为105kW,但生产能力却比热喂料挤出机低。冷喂料挤出机的出现简化了生产工艺,所喂胶料不再需要热炼,胶料在室温下喂入挤出机,即可得到各种形状的制品胶胚。它完全可以替代热喂料挤出机,并可省去胶料热炼工序,简化了生产工艺,并可使机头建立较高压力,对提高挤出制品质量有一定效果,因此,在某些制品的生产中得到了较为广泛的应用。但是为使胶料得到较好的塑化效果而设计的主副螺纹结构的螺杆,使挤出产量受到影响,而且需要较大的驱动功率,在一些生产工艺中的使用受到了限制。
主副螺纹冷喂料挤出机出现于1970年,它的主螺纹与普通型螺杆的螺纹相同,主要结构是在主螺纹槽中设置了具有一定高低差的副螺纹,而副螺纹则在螺距和螺棱高度上有所变化,只允许通过窄缝向前输送胶料,从而有效地消除了普通螺杆螺槽中胶料的“死区”。强化了塑化和混炼的效果,但它对胶料的混炼质量不均匀,消耗的能量较大。
(4)冷喂料型
冷喂料排气挤出机的出现源于1956年Bernhatdt提出的抽真空挤出机螺杆的设计。它使用的螺杆按胶料窄压缩段螺槽中的流动状态可分为普通型冷排螺杆和强力剪切型冷排螺杆。冷喂料排气挤出机的螺杆分为喂料段、压缩段、节流段、排气段和挤出段。节流段采用了浅槽等距等深螺纹,可使胶料获得较高的剪切和稳定的输送过程,同时也提高了排气效果。在冷喂料螺杆挤出机中,向挤出机中加入的是室温的胶条。橡胶挤出机也经常按是否用于排气来进行分类。
(5)销钉型
在对挤出技术的不断探索中,即20世纪60年代后期和20世纪90年代初开始了销钉技术的研究,将销钉从机筒圆周方向径向插入螺杆螺纹槽中,将流动的胶料进行剪切和搅拌。胶料变成熔体以低剪切速率在螺杆螺纹中流动,逐渐形成连续的黏流体,这样便破坏了胶料在挤出过程中的层流和结块现象,打破了胶块,达到了胶料塑化好、胶温低和节能的效果,简化了生产工艺。1979年,该项技术在美国获得了专利。销钉式冷喂料挤出机的出现,使冷喂料挤出机技术得到了很大的发展和提高。这种挤出机不仅在螺杆结构上有了较大改进,而且由于在机筒上增加了销钉,使其对胶料的塑化性能、挤出制品的致密性、挤出量都有很大的提高,并且排胶温度较低,可满足多种生产工艺的挤出要求,同时由于改进了螺杆结构,使其驱动功率下降,单位能耗明显降低。由于其具有塑化性能好、排胶温度低、挤出量大的特点,在橡胶工业生产中得到了越来越广泛的应用。
(6)复合型
在橡胶工业生产中,复合挤出机主要用于轮胎复合胎面的挤出,汽车密封胶条、彩色车胎胎面,胶管复合及胶塑复合挤出,以及胶板多层共挤等。复合挤出生产工艺在橡胶工业生产中属于先进技术,它可根据制品的不同性能要求,采用不同配方和性能的胶料,通过复合挤出设备生产出既能节省材料,又能满足多种性能需求的制品。
1.4.3 橡胶挤出机的维修与保养
① 将旁压辊打开,使用小铲刀将旁压辊处杂胶清除,保证旁压辊表面无胶料残留。
② 使用干燥压缩空气清理风扇过滤网及扇叶上的灰尘。
③ 挤出机旋转接头加注润滑脂(3号锂基脂),用黄油枪嘴对准旋转接头加油口进润滑。设备运转时加注效果更佳。
④ 将真空管拆下,使用小铲将真空口内胶料清除;将真空管两端拆下,疏通其管路。
⑤ 将风扇罩拆下,使用毛刷或压缩空气清理扇叶表面灰尘。
⑥ 在清理循环水滤网前先将循环水阀门关闭,用扳手将循环水过滤器的螺母拆下,将里面的杂质清理干净,最后将过滤器安装好。
⑦ 使用扳手将温水循环机各进水出水口紧固。
⑧ 将链条护罩拆掉,调整入料辊位置以调整链条松紧度;链条表面加注机油。
⑨ 检测三角带松紧度,用手在每条三角带中部施加2kg左右的垂直压力,若出现松动,则调整主电机位置以调整三角带松紧度。
⑩ 拆下护罩,松开刮刀两端顶丝,调整顶丝以调整旁压辊间隙。
⑪ 断电,紧固所有接线端子,整理线路,用压缩空气吹扫电气件表面灰尘。
⑫ 使用质量分数5%~7%的除垢液进行清理,需每个机筒分开清理,切勿接总进水出水口清理。
⑬ 清除旧的润滑油,并用汽油洗净轴承及轴承盖的油槽,然后将ZL-3锂基脂填充轴承内外圈之间的空腔的1/2。
⑭ 拆下旁压辊,查看表面是否有划伤。若有,旋转旁压辊,在其转动过程中使用细砂纸打磨表面,至表面划伤打磨平整为止。
⑮ 一定时间后需拆下护罩,松开刮刀两端顶丝,调整顶丝以调整旁压辊间隙。
⑯ 一定时间后需将旧齿轮油放尽,然后将新油注入齿轮箱。