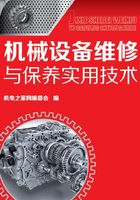
1.5 压延机
1.5.1 压延机简介
压延机是由两个或两个以上的辊筒,按一定形式排列,在一定温度下,将橡胶或塑料压制展延成一定厚度和表面形状的胶片,并可对纤维帘帆布或钢丝帘布进行挂胶的机械。压延机按照辊筒数目可分为两辊、三辊、四辊和五辊压延机等;按照辊筒的排列方式又可分为“L”形、“T”形、“F”形、“Z”形和“S”形等。压延机如图1-4所示。

图1-4 压延机
1.5.2 压延机的组成及主要分类
普通压延机主要由辊筒、机架、辊距调节装置、辊温调节装置、传动装置、润滑系统和控制系统等组成。精密压延机除了具有普通压延机主要零部件和装置外,增加了保证压延精度的装置。
压型压延机,用以将胶料压成一定厚度和一定断面形状。
万能压延机,能进行擦胶、贴胶和压片各项工作。
实验用压延机,供试验用。
1.5.3 压延机的特征参数
表征压延机的参数很多,其中主要有辊筒数目及其排列形式、辊筒的直径和长度、辊筒的调速范围、速比和生产能力、压延制品的最小厚度和厚度公差、辊筒的横压力和驱动功率等。
1.5.3.1 长径比
辊筒的长度和直径是指辊筒工作部分的长度和直径。这是表征压延机规格大小的特征参数。
(1)辊筒长度
辊筒长度表征了可压延制品的最大幅度。由于两端需留出挡料板安放的位置,因此,辊筒的有效长度为辊筒长度减去非工作表面长度(约为15 %辊筒长度)。
(2)辊筒长径比
辊筒工作部分长度和直径的比值叫长径比。辊筒的长径比(或辊筒直径)主要影响压延制品的厚度尺寸精度(异径辊除外)。它除了与压延材料的性能、辊筒的材质与工作部分长度有关外,主要取决于压延制品的质量要求。
(3)辊筒直径与横压力和功率、长径比与刚度的关系
辊筒直径与横压力和功率的关系为辊筒直径越大,横压力越大,所需驱动功率也越大,几乎成直线关系。
辊筒的长径比主要影响辊筒的刚度,直径ϕ610mm的辊筒在不同长径比下的刚性比为长径比越大,刚性越差。
(4)辊筒长度、直径和长径比的确定
辊筒长度、直径和长径比主要根据制品的生产工艺要求确定,即根据被加工原料的种类、压延制品的厚度范围和宽度范围、辊筒的压延速度(即产量要求)等要求确定。
为了确保压延制品的厚度尺寸精度,根据生产实践经验,辊筒长径比应限制在下列范围内(异径辊除外)。
加工软质料(如橡胶),一般长径比为2.5~2.7。最大不超过3。
加工的硬质料,取长径比为2.0~2.2左右。
辊筒长度、直径的标准系列:ϕ360mm×1120mm;ϕ450mm×1200mm;ϕ550mm×1600mm;ϕ610mm×1730mm;ϕ710mm×1800mm
1.5.3.2 辊筒速度与速比
压延机辊筒线速度系指辊筒的圆周速度,以“m/min”表示。辊筒的线速度是表征压延机生产能力的一个参数,也是表征压延机先进程度的参数之一。
(1)辊筒速度
辊筒速度主要根据压延机的工艺用途和生产的自动化水平来决定。辊筒速度应能满足压延工艺操作的要求,即辊速应是可调的。
国际上压延速度普遍达50~90m/min,个别的已达到115m/min。对钢丝压延平均速度可达50m/min,在采用冷压延(把压延好的两层胶片直接压贴在无纬钢丝帘布上)时,压延平均速度达30m/min。
(2)调速范围
辊筒可以无级变速的范围叫调速范围。由于加工材料品种多、性能差异大,为了既满足生产能力,又满足慢速启动及操作的要求,一般要求压延机的调速范围在10倍左右。
最高速度主要根据生产能力的要求确定,最低速度主要根据设备启动、操作安全和方便来确定。
(3)速比
由于压延时贴胶、擦胶或压片的工艺要求不同,对辊筒的速比要求亦不同,在同一台压延机上不同位置的使用要求的不同,其速比也不同。
辊筒速比与压延工艺、物料性质有关。
① 为排除胶料中的气泡,一般喂料辊都具有速比,常为(1∶1.1)~(1∶1.5),我国多采用(1∶1.1)~(1∶1.4)。软胶料取小值。
② 对于擦胶作业,为使胶料渗入到纺织物中去,擦胶辊要求有速比。速比越大剪切力越大,擦胶效果越好,但速比过大会损坏纺织物的强度,容易使胶料焦烧。而速比过小则胶料的渗透作用差。一般采用(1∶1.2)~(1∶1.5),我国多采用(1∶1.4)~(1∶1.5)。
③ 对于压片、贴合、贴胶等作业,因主要是要求取得挤压力,故一般采用等速压延,速比为1∶1。
④ 在选择辊速时要考虑的因素
辊筒速度直接影响压延机的功率消耗和生产能力。辊速越大,则功率与产量越高,对压延机的机械化自动化水平要求也越高。因此,在选择辊速时要考虑以下几点。
a.压延的工艺要求。
b.压延机的制造水平。
c.压延机组的自动化水平。
d.辊筒速度应能广泛平稳地进行调整。
e.压延时辊速尽可能用高值,这有利于发挥设备能力。
可见辊速的高低标志着压延机组的先进水平。
由于采用电动机单独地传动每个辊筒,它可使辊筒间的速比在一定范围内(从1∶1到高达1∶1.3)任意调节,从而可在一台压延机上完成多种作业,这就使机台的适应性更加宽广,并有利于提高辊速。
1.5.3.3 横压力
(1)横压力的特征
① 横压力的概念。胶料通过辊筒间隙时,对辊筒产生径向作用力和切向作用力,径向作用力垂直于辊面,力图将辊筒分开,这个力就叫横压力,也叫分离力。
② 辊筒横压力的特征。胶料通过压延机辊筒辊隙时,胶料的厚度逐渐由大变小,而压力逐渐上升。
a.在a、b区域,胶料通过速度在辊隙中央部位较慢,两边部位最快。但随着胶料前进,这一速度差异逐渐减少。
b.当达到b点时,各部位的速度相同,压力达到最大值。
c.当到达辊距处,即c点处,胶料速度在辊隙中央部位大于辊隙两边部位,压力也就逐渐地下降,胶片厚度增加。
d.直至d点胶片厚度不再增加,胶料对辊筒的压力降为零。
可见,辊隙中胶料的横压力是不均匀的,最大值出现在辊距稍前处。
(2)影响横压力的因素
在压延过程中影响横压力的因素是多方面的,主要有以下几点。
① 加工胶料的种类和性能。胶种不同则横压力不同,同种胶料的硬度不同,黏度不同,则横压力不同。硬度、黏度越大,横压力越大。
② 压延制品的厚度。制品厚度越薄,辊隙越小,分离力越大。当辊隙极端缩小时,辊筒间将产生极大的分离力。这是因为辊隙越小,制品厚度越薄,辊筒间形成刚性挤压,分离力急剧上升。从维护辊筒的观点,这对一般压延成型机是绝对不允许的。
③ 辊筒直径和压延宽度。辊筒直径和压延宽度越大,所产生的横压力也越大。
④ 加胶的包角大小(即进料口处存料量)。加胶包角越大,辊筒工作面越大,横压力也就越大。
⑤ 辊筒的速度。辊筒的速度和横压力的关系比较复杂。
a.辊筒转速增加时,单位时间内压延熔料的数量增加,致使横压力增加。
b.辊筒转速增加,熔料摩擦发热增加,温度上升引起熔料黏度降低,使横压力降低。
c.辊筒转速增加,使压力提高从而使横压力提高等。
所以,辊筒转速和分离力的关系是几个方面的综合结果。经实测,随辊筒转速的增加,横压力的增加比较缓慢。
⑥ 辊筒的温度。辊筒的加工温度越高,材料的黏度越低、流动性越好,产生的横压力也越小。反之,则越大。
⑦ 加胶的方法(连续或间歇)。当采用片状或条状料左右摆动式加料时,加料是比较连续均匀的,因此对辊筒的冲击作用较小,横压力的波动较小,当采用块状加料时,加料是间歇而不均匀的,对辊筒的冲击作用大,横压力的波动也大。
1.5.3.4 功率消耗
(1)传动功率
压延机传动功率系指驱动压延机辊筒所需之功率。其特点如下。
① 传动功率大。由于压延机属重型机械,加上辊筒的转速较高,所以,传动功率是很大的。
② 功率消耗比较稳定。又由于压延机上被加工的胶料已经预热软化,横压力较小,胶料又是一次通过辊距,压延前后胶料的变形又不大,故操作是比较稳定的。因此,压延机电能消耗比较稳定,不像开炼机那样出现高峰负荷。
(2)功率计算
功率消耗也是压延机设计的一个重要参数,很难用理论公式准确地求得。这里简要地介绍几种经验公式近似地计算:
① 单台电动机传动时的功率计算
a.按辊筒线速度计算
N=aLv
式中 a——计算系数;
L——辊筒工作部分长度;
v——压延线速度。
b.按辊筒数目计算
N=KLn
式中 K——计算系数;
L——辊筒工作部分长度;
n——辊筒个数。
以上两式的共同缺点是没有考虑被加工胶料的性质和加工方法,以及辊筒的直径对功率的影响,而它们对功率消耗的影响又是十分大的。可见上述两个公式都是片面的。
c.类比计算
借助已知若干机台特性和功率消耗,计算出计算系数a和K,再用上式计算设计(未知)压延机的功率。
② 多台电动机传动时的功率计算
一台压延机由于各个辊筒所在位置不同,工艺用途不同,转动线速度不同,在压延过程中各辊消耗的功率不同。在一般条件下,进料辊要比贴合辊所消耗的功率大。
a.压延时两辊筒消耗功率与辊筒的线速度成正比
若两辊筒的线速度分别为V1、V2,功率分别为N1、N2,则:
N1 /N2=V1 /V2
b.贴胶时所消耗的功率仅为总功率的6%
Nstick=0.06Nall η
式中 Nstick——贴胶辊功率;
Nall——有效总功率;
η——传动总效率。
根据以上两点,就可以计算出各个辊筒所占的功率。
1.5.4 压延机的主要应用
(1)简介
塑料机械中压延机通常和物料输送、筛析、计量、捏合和塑炼等先导装置,引离、牵引、压花、冷却、测厚、卷取、截断等后续装置,以及传动、监控和加热装置等组成完整的压延生产线,生产软硬薄膜、片材、人造革、墙纸和铺地卷材等产品。
(2)归类
塑料机械中压延机分类方式有多种,按压辊数分为二辊、三辊、四辊和五辊等类型。按压辊排列形式可分为F、Z、S和L等型。
(3)组成
与其他塑料机械不同,压延机由机架、压辊及其调节装置、传动系统和加热系统等部分组成,机架通常用铸铁制成,直接安装在铸铁或铸钢机座两侧,用以支承压辊轴承、轴交叉或压辊预弯曲装置、压辊调节装置、润滑装置和其他辅助装置。压辊由冷硬铸铁,铸钢制成,其长径比根据压辊材料的弯曲强度选定,约为2.6~3.5。为了补偿压辊受力产生的弯曲变形而造成制品厚度不匀的缺陷,压辊多制成腰鼓形,还可利用辊交叉装置和辊预弯曲装置消除制品的厚度不匀。每个压辊采用单独电动机传动。压辊加热一般采用水蒸气或过热水,要求两端温差不超过 1℃。每个压辊均有独立的自动加热系统。现代压延机都使用滚柱轴承代替传统的滑动轴承、以节约能量、提高轴承寿命和制品厚度的精度。
(4)产品
根据压延机规格的不同,所产软聚氯乙烯薄膜厚度也不同,为0.5~1mm不等,硬聚氯乙烯薄膜的最小厚度为0.6mm。
压成片状,并实现磁粉颗粒的机械取向,提高黏结剂与磁粉颗粒的结合性能。
(5)机械瓶颈
对于压延工序,产品外形尺寸、表面质量是其最重要的控制参数。卷材外形尺寸一般要求沿长度和幅宽方向厚度公差分别为±0.015mm和±0.05mm;表面要求平整、光滑。若达不到这些要求,难以保证后续覆膜时PVC膜与磁板黏合压力均匀一致,影响黏合强度。
(6)技术背景
国内黏结铁氧体磁体生产厂家都采用轴瓦结构的压延机,轴瓦材料一般为铜或尼龙,采用黄油润滑。轴瓦易磨损,造成轧辊转动过程中产生径向跳动,很难保证产品尺寸公差。因此,压延机一定要选用精度高的双列向心滚子轴承,并采用稀油润滑,减小轴承磨损,确保磁板沿长度方向厚度公差。
由于颗粒料流动性较差,尤其是沿幅宽方向受分子间作用力及轧辊挠曲变形的影响,压延出的磁板沿幅宽方向经常会出现中间厚、两边薄的现象。尺寸超差会造成收卷时卷材中间紧,两边松散。解决厚度超差这个问题可采用结构复杂的倒“L”形四辊压延机。该压延机具有轴交叉和轴预弯曲功能。但该压延机结构复杂、价格昂贵、占地大、维修不便,厂房造价及设备运行费用也较高。因此,我们设计了性能优越的两辊开放式压延机。
1.5.5 压延机的关键技术
两辊开放式压延机设计的关键是辊型结构、材料选择及辊面处理和技术参数确定,其次是功能的配置。在辊型结构方面,我们采取了不同于橡塑制品行业的超大辊径中高度设计,中高度=(D-d)/2。目的是补偿因轧制应力产生的轧辊挠曲变形,并提高轧辊中间部位的轧制力,强制磁粉颗粒向两边流动,同时针对压延时可能采取的不同的轧辊加热方式,分别设计了适合蒸汽加热的中空辊和适合油加热及水加热的周边钻孔辊。经生产实践,两种孔型的加热方式都可满足工艺对辊面温度波动误差的要求。在材料选择方面,我们采用耐磨性好、刚性强的合金冷硬铸铁材料,轧辊工作面硬度达HS72~75。但合金冷硬铸铁轧辊往往会因铸造缺陷以及颗粒料中的添加剂可能对辊面的腐蚀作用,造成短时间使用后辊面出现“冰花状云斑”,无法压延出表面光滑的磁板,因而对辊面进行特殊处理是十分必要的。特殊处理主要有表面喷涂耐磨材料和镀硬铬两种方式,我们采用的是后者。为增强硬铬与合金冷硬铸铁的结合强度,镀铬前需先镀镍,磨加工后镀铬层厚度一般为0.05~0.08mm。需特别指出的是,在生产一面覆PVC膜磁板时,卧式两辊压延机最好配置成一根镀铬辊,另一根为合金冷硬铸铁轧辊。由于合金冷硬铸铁轧辊轧制的磁板表面相对比较粗糙,有利于增强PVC膜与磁板的结合强度。
压延机设计参数制定的原则是尽可能实现一道压延生产出合格磁板。经反复多道压延的磁板其内部残余应力很大,与PVC膜黏合后,由于两者收缩率的差异,会出现PVC膜与磁板脱胶、磁板边缘外露PVC膜和磁板不平整等现象。通过计算和实验修正,我们确定了生产幅宽小于1000mm的磁板压延机最佳技术参数为:轧辊长径比为2.5~3,中高度为辊径的0.1‰~0.3‰,轧辊线速度≤3.5m/min,辊面温度60~80℃,速比为1∶1,并配置了刮边装置、辊面温度及辊缝显示装置。在轧辊速比选择上曾有不同的观点,有人认为带有较小速比(例如1∶1.03)的轧辊其剪切力可促进颗粒料在压延过程中进一步塑化。而实际上这种塑化作用是极其微小的,反而会因轧辊差速的剪切作用造成磁板表面搓伤,并使微小缺陷扩大化。
1.5.6 压延机的维修保养
(1)每次工作轮班的开始进行检查
① 辊筒,预负荷装置和轴弯曲轴承座内润滑油的温度及压力。
② 用于预负荷,辊筒弯曲和轴交叉设备等驱动设备的液压站的温度与压力。
③ 驱动齿轮箱内润滑设备的油温及压力。
④ 进入换热器的液体及装置的供气,供水和流体工作状态良好。
⑤ 集中润滑设备有效。
⑥ 安全设备运行良好。
⑦ 裁边刀刀刃的轮廓。
(2)每工作周的开始进行检查
① 检查油箱中输出的油没有引起管道堵塞或使浮标控制错位的沉积或其他杂物。
② 润滑设备或液压站的油箱内的油面。
③ 主要驱动齿轮箱的油面。
④ 气压站微喷雾器内的油面。
⑤ 轴交叉齿轮箱的油面。
⑥ 集中润滑设备的集中泵内的润滑油量。
⑦ 用加油器润滑辊子链条和相关齿轮。
⑧ 按钮、摇杆和所有安全设备运行良好。
(3)每月进行检查
① 所有独立的润滑脂器(如挡胶板设备)通过手摇泵注射少量的润滑脂。
② 旋转接头的密封和相关的软管道。
③ 润滑和液压设备的管道与连接。
④ 辊筒温度调节设备的管道,连接及阀。
⑤ 液压设备的管道,连接及阀。
⑥ 辊筒侧面和预负荷轴承座的橡胶包层的密封。
⑦ 压延机和轴承箱润滑设备及液压设备过滤器的清洁与更换。
⑧ 检查气压设备是否有效。
⑨ 驱动齿轮箱空气过滤器的清洁与更换。
⑩ 机器结构的准确清理。