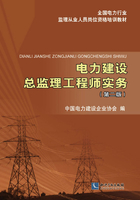
第三节 火力发电新技术介绍
我国一次能源利用主要以煤炭为主,其中,火电机组使用超过2/3的煤炭总量,虽然多数机组已经安装脱硫、脱硝、除尘等环保设施,但是大量的二氧化碳、二氧化硫和烟尘排放,还是加重了对大气环境的污染,给我国带来了一系列生态环境保护问题。为此,当今世界广泛开展洁净煤燃烧技术的开发,研究燃煤机组的高效率和低排放。超超临界机组、大型CFB(循环流化床锅炉)、PFBC(增压流化床燃气——蒸汽联合循环)、IGCC(整体煤气化燃气——蒸汽联合循环)、GTCC(燃气——蒸汽联合循环)等火力发电新技术,因其高效率和优越的环保性能,在世界发达国家得到了广泛应用。我国也开展了大量的研发和应用工作,特别是洁净煤燃烧技术已成为目前我国火力发电机组的热门技术。
为了降低环境污染物排放量,火电设备发展趋势和目标为:以高效率、低污染、低能耗、低造价的发电设备和新型的清洁煤燃烧发电技术为开发重点,结合碳捕捉和封存技术(CCS),实现2050年,将火电机组温室气体排放是降低50%。
为了实现上述目标,目前可行和正在攻关的工作方向如下:
(1)大力发展高参数高效超超临界机组(蒸汽温度620℃,二次再热机组),降低单位发电量燃煤消耗。高效超超临界燃煤发电是当前最可行的高效节能技术,目前的超超临界机组效率已经达到45%,碳氧化物排放量低于740g(CO2)/(kW·h)。世界各国正在研究进一步提高火电机组初参数,在今后的10~15年,研制、开发出700~720℃、30~35MPa水平的超超临界机组,届时机组的热效率将达到50%~55%,碳氧化物排放量低于700g(CO2)/(kW·h)。而我国计划研发的700℃超超临界发电机组发电效率将超过51%,单位标煤耗则可以降低到241g/(kW·h)。一台600MW机组,年利用小时数按照5500h计算,700℃超超临界机组每年的耗煤量比600℃超超临界机组的减少9.9万t。
(2)发展循环流化床机组以降低火电机组污染物排放。由于循环流化床中等温度燃烧和炉内污染物处理的特性,使得CFB锅炉技术实现了低污染物排放量和燃料灵活性,并且随着锅炉参数的逐步提高,超(超超)临界CFB锅炉技术也逐渐成熟。
(3)研究整体煤气化联合循环(IGCC)技术,作为清洁煤燃烧技术的代表。燃煤气化、燃烧前碳捕捉和燃气——蒸汽联合循环发电将是提高发电效率、大幅降低污染物排放最有前景的技术之一。为了进一步提高IGCC机组的效率,国外已经开始研制运行温度达到1700℃的重型燃机,将单机发电效率提高到60%,同时碳氧化物排放下降到670g(CO2)/(kW·h)以下。
随着近年工程实践,大量适应国家高效和减排政策的火电机组涌现。各种新技术、新材料应用于工程实践,如变频技术的大量采用、高位冷却塔、低温省煤器、汽机十级抽汽、前置蒸汽冷却器等技术。与之同步改变的是机组的新工法和新调试技术,例如:深化深度调试应用、机组调试过程控制、超超临界机组稳压吹管、启动节能技术、全过程化学指标监督以及自动控制相关的新技术等。
下面介绍几种火力发电新技术。
一、700℃超超临界燃煤发电机组
提高汽轮发电机组的初参数是当前提高发电设备效率的主要手段,相比同等容量的亚临界机组,超临界机组效率提高了2%,超超临界机组又在此基础上提高3%~4%。超超临界机组具有明显的高效、节能和排放的优势,为全世界工业化国家广泛采用,已经是商业化的成熟机组。
燃煤发电机组主蒸汽和再热蒸汽温度一般为600℃以上,700℃超超临界燃煤发电机组是超超临界发电技术的发展前沿。在超临界与超超临界状态,水由液态直接成为汽态,即由湿蒸汽直接成为过热蒸汽、饱和蒸汽,热效率较高,因此,超超临界机组具有煤耗低、环保性能好和技术含量高的特点,且温度越高,热效率越高,煤耗越少。例如,与600℃超超临界发电技术相比,700℃超超临界燃煤发电技术的供电效率将提高至50%以上,每千瓦时煤耗可再降低近70g,二氧化碳排放减少14%,采用700℃超高参数火电机组是我国实现CO2减排目标的最重要措施之一。该技术的实施将使我国掌握700℃超超临界燃煤发电主要设备及部件高温材料冶炼工艺、加工制造、焊接及检测等关键技术,进而形成700℃超超临界燃煤发电机组的自主设计、开发和制造能力,全面提升我国冶金、机械和电力企业的核心竞争力。
当然,燃煤电厂蒸汽参数达到700℃,仍需要解决一系列的技术问题:如高温材料的研发及长期使用的性能;大口径高温材料管道的制造及加工工艺;高温材料大型铸、锻件的制造工艺;锅炉、汽轮机设计、制造技术;高温部件焊接材料研发及焊接工艺;高温材料的检验技术;机组初参数选择、系统集成设计及减少高温管道用量的紧凑型布置设计。
1.世界各国700℃超超临界燃煤发电机组的研发计划
700℃超超临界燃煤发电技术将全面提升燃煤发电设备的设计和制造水平,为制造厂和电厂换来巨大的经济效益。为此,欧盟、日本和美国均采取由政府组织电力用户、毛坯和原材料的供应商及设备制造公司联合开发的方式,制定了长期的700℃超超临界发电技术和设备的发展计划,使超超临界机组朝着更高参数的技术方向发展。目前,国际上700℃超超临界燃煤发电机组研发计划主要有三个:欧洲AD700的17年计划(1998—2014年);日本的A-USC的9年计划(2008—2016年);美国的A-USC的15年计划(2001—2015年)。
(1)欧盟AD700计划。欧盟在确定洁净燃煤发电节能减排的发展战略中,偏重于燃煤火力发电,因此,早在1998年就开始执行由丹麦ELSAM电力公司负责,组织欧盟45家公司参加的700℃超超临界AD700发展计划,计划在2013年完成。关键部件将采用镍基合金,热效率由目前最好的47%提高到预期的52%~55%,CO2排放降低15%。项目要解决的主要问题是研发满足运行条件的成熟高温材料,并通过优化设计降低建造成本。AD700项目分六个阶段实施,计划在2014年欧洲建立第一个参数为35MPa、700℃/720℃的示范电厂。AD700发展计划是目前世界上进展最快,并唯一有示范电厂的700℃超超临界发电计划。
(2)日本A-USC计划。日本在2008年G8会议之后,针对2050年CO2减排50%的目标,提出了“冷地球计划”,列出重点发展的21个技术领域,洁净燃煤发电技术列为六个能源供给技术中的一个。随后于2008年日本推出了700℃超超临界发电技术和装备的九年发展计划——“先进的超超临界压力发电(A-USC)”(2008—2016年)项目。由日本政府组织材料研究、电力及制造厂联合进行700℃超超临界装备的研发工作,明确在2015年达到35MPa、700℃/720℃以及2020年实现750℃/700℃超超临界产品的开发目标。项目内容包括系统设计,锅炉、汽轮机、阀门技术开发、材料长时性能试验和部件的验证等。为了实现CO2减排要求,对现有大量超临界机组,日本提出25MPa不变,采取700℃的一次再热USC+AUSC改造方案,实现整个日本燃煤电厂的升级换代。
(3)美国AD760计划。美国于2001年启动700℃超超临界机组研究项目——AD760。为了与IGCC竞争,美国AD760计划采取的起步参数比欧洲和日本更高,定为37.9MPa、732℃/760℃,热效率将达到47%左右。其设定的蒸汽参数目标显著高于欧洲的700℃,其原因是该参数更适合美国的高硫煤种。AD760研究内容包括概念设计与经济性分析、先进合金的力学性能、蒸汽侧氧化腐蚀性能、焊接性能、制造工艺性能、涂层、设计数据和方法等。目前,美国已完成732℃/760℃、35MPa/7.5MPa的750MW机组的可行性分析,两次再热机组为52%,美国700℃超超临界发电技术和设备的研发时间表定为:2015年完成各项研究项目,2017年建设示范电厂。
2.中国700℃超超临界燃煤发电机组的研发计划
中国已是世界上1000MW超超临界机组发展最快、数量最多、容量最大和性能最先进的国家。通过600℃超超临界机组的技术研发及工程实践,除锅炉、汽轮机部分高温材料及部分泵和阀门尚未实现国产化外,其他已基本形成了600℃超超临界机组整体设计、制造和运行能力,建立起了完整的设计体系,拥有了相应的先进制造设备及加工工艺,这些为我国700℃超超临界燃煤发电机组的发展奠定了良好的基础。
近年来,国内企业和相关科研院所也开展了相关研究。例如,材料制造方面已开展镍基合金转子材料的研究,现已完成原料采购和试验成分的选择,下一步开始冶炼小钢锭的研究。设备制造方面已开展“更高参数1000MW等级超超临界锅炉设计技术研究”课题,主要研究31.5MPa、703℃/703℃等级超超临界锅炉的初步方案设计。在此基础上,我国也于2010年7月成立启动了700℃超超临界燃煤发电技术创新联盟,开展“700℃超超临界燃煤发电关键设备研发及应用示范”项目,主要参加单位为上海电气集团、中国电力工程顾问集团、清华大学、中国科学院材料研究所等单位。根据700℃超超临界发电技术的难点及与国外差距,目前,已形成我国700℃超超临界发电技术发展路线图(2010—2015年)。路线图分综合设计、材料应用技术、高温材料和大型铸锻件开发、锅炉关键技术、汽轮机关键技术、部件验证试验、辅机开发、机组运行和示范电厂建设9个部分进行。路线图目标参数:压力≥35MPa、温度≥700℃、机组容量≥600MW,机组循环效率达到50%~55%。中国700℃超超临界燃煤发电机组热力系统如图1-4所示。

图1-4 中国700℃超超临界燃煤发电机组热力系统
3.700℃超超临界机组的材料研发情况
金属材料是提升机组性能的主要制约因素,过热器/再热器管材是关键技术之一,目前大量使用的耐热钢(T91、TP347H、Super304H等)的最高使用温度为650℃,不能满足700℃使用要求。
欧美正在研发过热器/再热器管材用高温合金,主要材料是镍基高温合金IN617或IN617改型,如IN740、IN617、IN617mod、N263。新的超级奥氏体钢(“super”austenite Sanicro25)和镍基管材IN740已达到目标要求,正在取得质量证书的过程中。
我国目前正在研究的过热器/再热器管材用高温合金材料有GH2984铁镍基高温合金等,主要性能与In740处于同一水平。需要作进一步的试验,主要是管材的焊接工艺、合金的最佳热处理温度、合金的典型力学性能及化学性能、长期(达3万h)组织性能稳定性等。可以作为700℃超超临界机组用高温材料储备。
近年来,国内企业和相关科研院所也开展了相关研究。例如,材料制造方面已开展镍基合金转子材料的研究,现已完成原料采购和试验成分的选择,下一步开始冶炼小钢锭的研究。材料研发是工业发展的基础,需要长时间、巨大的人力和物力的投入,在历次的技术转让中,材料的性能数据始终是作为机密,被排除在转让范围之外。与欧盟、日本和美国等相比,我国缺乏自主产权的高温材料基础数据,这成为约束700℃超超临界发电技术发展的瓶颈。虽然近年来,在国内钢铁生产公司、锅炉制造企业及相关研究院所的联合攻关下,在模拟国外高温材料的基础上,基本实现锅炉用高温材料的国产化,但与欧盟、日本和美国等相比,材料研究的差距仍很大。
二、汽轮机组分轴高低位布置的二次再热机组
虽然二次再热机组已属成熟技术,但其推广的瓶颈在于投资太大,而且投入产出不合理。
进一步发展更高参数的机组,耐热合金是基础。对于单轴二次再热汽轮机组,其中主蒸汽管道、高温一次再热管道和高温二次再热管道需要使用耐高温合金钢,且单根高温再热管道的管长度均需160m左右。
目前超超临界600℃等级的合金钢,价格已达人民币12万元/t,而下一代700℃等级的超级镍基合金钢,估计价格可高达人民币80万元/t。以目前600℃参数等级的一次再热2×1000MW超超临界机组为例,总投资约70亿元人民币,其中“四大管道”的价格约3亿元人民币。若将参数提高至700℃等级,其“四大管道”的总价格可能上升至25亿元人民币以上,加之锅炉及汽轮机的造价亦将相应上升,仅以5%~6%的相对效率的提高,其代价太大,必然令投资者望而却步而无法推广。因此,进一步提高蒸汽参数和采用二次再热来进一步提高发电效率的主要问题是用造价极高的高温耐热合金制成的主蒸汽和再热蒸汽管道系统距离太长,阻力很大而成本太高,造成投入产出比无法接受的大瓶颈。
在现有的技术条件下,与一次再热相比,两次再热将会大幅增加设备造价,其获得的效率收益尚不能补偿投入的增加,无法大规模推广,因此,各国基本上都倾向于建造一次再热600℃等级的超超临界机组。目前世界上效率最高的超超临界机组是丹麦Nordjyllandsværket电厂的3号机组,容量为400MW,是两次再热的超超临界燃煤机组,其蒸汽参数为29MPa、580℃/580℃/580℃,机组的供电效率为42.94%。
解决二次再热方案造价过高的有效手段就是最大限度地缩短锅炉过热/再热器出口至汽轮机的距离。目前提出了“汽轮机组分轴高地位布置”技术方案(图1-5、图1-6),这项创新技术既能突破当前超超临界机组的发展瓶颈,又可为亚临界、超临界机组的升级改造提供新的思路。该技术2010年底通过了中国电力工程顾问集团公司的设计评审,认为该方案可达到世界领先水平。这一项目已获得国家专利授权并正在申请国际专利。

图1-5 1350MW汽轮发电机组高、低配置锅炉示意图

图1-6 1350MW汽轮发电机组高、低配置双轴系示意图
(一)主要优点
(1)根据西门子所做的热平衡计算表明,若采用600℃等级蒸汽参数及二次再热方案,其汽轮发电机的热耗水平相对目前一次再热常规布置方案可再降低5%。
(2)采用了双轴高低布置方案,其单机容量的瓶颈也被打开,按目前的技术水平,单机容量可达1500MW。
(3)大大降低了绝大部分高温高压蒸汽管道的阻力损失,增加了汽轮机发电机组的做功能力,这种优点对于双再热机组更为明显。
(4)可降低绝大部分的高参数、高价格的管道及相应的支吊架、保温材料等的投资成本。
(5)可减少有害蒸汽容积,极大地提高了汽轮发电机组的调节性能。
(6)可简化由于高温高压管道布置所需的厂房结构设计,降低了相应的地基载荷,降低了相应的土建成本。
(二)应用前景
(1)对于双再热机组,其造价将与一次再热同温度等级的超超临界机组相当,与600℃等级的超超临界机组,其热效率可望超过48%。一个两台1000MW机组的双再热超超临界电厂,若改为双轴系高、低错落布置设计,节煤将超过20万t/年,节约运行成本8000万元/年。
(2)可为下一代700℃/720℃/720℃等级高效超超临界机组的发展消除了最主要的在经济上无法接受的制约因素,为目前的超超临界机组提供了一条可行的进一步提高效率的“升级”之路。
(3)如采用双轴系错落布置的设计,对于下一代700℃/720℃/720℃等级双再热机组,由于大大减少了镍基合金钢的用量,因而大大降低了成本,具有无可比拟的优势,它将可能是700℃/720℃/720℃等级双再热超超临界机组能够被市场接受的唯一选择。
(4)应用本技术的原理,可将原4×300MW或2×600MW的亚临界机组就地改建成2×(770~800)MW的新型汽轮发电机组。其新增的容量相当于零能耗发电,其商业价值及减排价值均极其可观。这对于我国现有约300000MW容量的300~600MW亚临界机组的改造,具有重大的意义。
(5)双轴系高、低错落布置在造价上基本上与一次再热同温度等级的超超临界机组相当,从而可使现有600℃超超临界机组采用两次再热设计,将理论净效率提高6%,达到48%,也就是用600℃超超临界一次再热材料和造价,基本实现700℃超超临界两次再热原布置方案的效率。
三、低温省煤器
电站锅炉排烟热损失是锅炉运行中最重要的一项热损失,电站锅炉的排烟温度通常为120~150℃,相应的热损失相当于燃料热量的5%~12%,占锅炉热损失的60%~70%。我国火力发电厂的很多锅炉排烟温度都存在超过设计值的情况,为了降低排烟温度,减少排烟热损失,提高电厂的经济性,低温省煤器这一提高烟气余热利用效率的手段已得到了火电行业的广泛关注。
(一)国外烟气余热回收技术现状
在国外,低温省煤器较早就得到了应用。最初,苏联为了减少排烟损失而改装锅炉机组时,在锅炉对流竖井的下部装设低温省煤器供加热热网水之用。目前国外烟气余热回收技术和工程应用以德国和日本为代表领先。
1.德国烟气余热回收技术和工程应用
德国锅炉烟气余热回收技术和工程应用主要分为3种类型:
(1)回收烟气余热加热凝结水。以德国黑泵(Schwaree Pumpe)电厂为代表,低温省煤器烟气侧布置在电除尘器和脱硫塔之间的烟道上,烟气流过低温省煤器,烟气温度从170℃降低到130℃后进入脱硫塔;水侧布置在汽轮机低压抽汽回热系统加热凝结水。德国Schwaree Pumpe电厂锅炉低温省煤器和暖风器系统如图1-7所示。

图1-7 德国Schwaree Pumpe电厂锅炉低温省煤器和暖风器系统
(2)回收烟气余热加热锅炉进风(低温省煤器和暖风器组合)。以德国(梅隆)Mehrum电厂为代表,德国Mehrum电厂一台712MW烟煤锅炉应用这一系统。低温省煤器烟气侧布置在电除尘器和脱硫塔之间的烟道上,烟气流过低温省煤器,烟气温度从150℃降低到90℃后进入脱硫塔;循环水侧冷端进入低温省煤器、热端进入锅炉暖风器,将锅炉进风温度由25℃提高到64℃。德国Mehrum电厂锅炉低温省煤器和暖风器系统如图1-8所示。

图1-8 德国Mehrum电厂锅炉低温省煤器和暖风器系统
(3)旁路高温省煤器和低温省煤器组合(加热高压与低压给水)。以德国科隆Niederaussem(950MW机组)电厂为代表。德国科隆Niederaussem(950MW机组)电厂在空气预热器旁路烟道系统内设置高温省煤器,加热汽轮机高/低压抽汽回热系统的凝结水;在电除尘器和脱硫塔之间的烟道上布置低温省煤器,烟气流过低温省煤器,烟气温度从160℃降低到100℃后进入脱硫塔;循环水侧冷端进入低温省煤器、热端进入锅炉暖风器,将锅炉进风温度由25℃提高到120℃。德国Niederaussem电厂高温省煤器和低温省煤器系统如图1-9所示。

图1-9 德国Niederaussem电厂高温省煤器和低温省煤器系统
上述三种系统比较全面地覆盖了锅炉烟气余热回收技术和应用方式。
2. 日本烟气余热回收技术和工程应用
日本由于烟气排放的要求比较高,所以一般都安装有GGH(GASGASHeater,烟气换热器)。烟气放热段的GGH布置在电除尘器上游,烟气被循环水冷却后进入低温除尘器(烟气温度在90~100℃),烟气加热段的GGH布置在烟囱入口,由循环水加热烟气。脱硫后的净烟气被加热到80℃以上再排向大气。
(二)国内烟气余热回收技术现状
近年来,国内低温省煤器技术研发、设计、制造也逐渐发展起来,能满足电厂工程实施的应用要求。国内已有电厂进行了低温省煤器的改造工作,如外高桥电厂三期2×1000MW机组工程建设时采用预留方式,并在机组大修时进行了低温省煤器改造安装,低温省煤器布置在引风机后脱硫装置前,现省煤器已投运两年半左右时间,运行情况较好;漕泾电厂一期在除尘器入口和引风机出口设置两级低温省煤器,回收热量加热凝结水的同时,除尘器入口烟温降低,飞灰比电阻降低,提高除尘效率。
玉环电厂等部分工程也正在实施设置低温省煤器改造。
(三)低温省煤器典型布置方式
在欧洲,除个别项目由于烟气量大,空预器利用的烟气热量有限,设计了空预器旁路,将部分锅炉排烟用于加热给水外,其他大部分采用低温省煤器的项目均设置在脱硫装置前。日本则是采用水媒式GGH方案,部分项目在除尘器前和脱硫装置后分别设置水媒式GGH,采用热媒水在前后两级GGH之间进行换热。
对于我国燃用烟煤的大容量机组而言,综合起来可采用的低温省煤器设置方案主要有以下布置方式:
(1)布置在空预器与除尘器之间;
(2)布置在引风机与脱硫塔之间;
(3)分段布置,第一级低温省煤器布置在空预器与除尘器之间,第二级低温省煤器布置在引风机与脱硫塔之间。
(四)优缺点分析
低温省煤器布置在引风机后、脱硫装置前,这种布置方式在欧洲采用较多,我国近年逐渐应用的低温省煤器基本上采用这种方案。
1.优点
(1)脱硫旁路取消后,引风机与脱硫增压风机合并,使得合并风机的轴功率大,烟气通过引风机温升一般约为10℃,可充分利用引风机温升,提高烟气余热利用率。
(2)电除尘器、引风机可采用国内常规设计,技术成熟、可靠。
(3)经过除尘器收尘,低温省煤器工作环境含尘少,对换热管道的磨损较小,积灰少,低温省煤器吹灰次数可以大大减少,运行风险大为降低。
(4)对于湿法脱硫,由于脱硫装置入口烟温降低,蒸发水分少,可节约脱硫用水。
2.缺点
(1)无法利用烟气温降带来的提高电除尘器收尘效率、减少引风机功率的好处。
(2)低温省煤器布置在引风机后、脱硫装置前,离主厂房相对稍远,用于回收热量的凝结水管(或水煤管)和用于吹灰的水管(或蒸汽管)稍长,相关水泵需克服的管道阻力也略高一些。
(五)应用前景
为了充分利用烟气余热,提高电厂热经济性,并利用烟气温度降低对除尘效率和引风机电耗产生的好处,可考虑将低温省煤器分段布置。这种布置方式设置两级低温省煤器,第一级低温省煤器布置在空预器与除尘器之间,第二级低温省煤器布置在引风机与脱硫塔之间。这种布置方式的优点是充分利用了锅炉尾部烟气余热(包括引风机温升);同时,由于烟温降低,烟气体积减小,设计中可采用较小规格的除尘器、烟道及引风机,除尘器和引风机的电耗也会降低。
目前国内1000MW燃煤机组已实施的低温省煤器方案中,如神华重庆万州电厂、安庆电厂等新建的百万机组,其在锅炉效率达到设计要求时的计算经济性收益一般均在发电煤耗1.3g/(kW·h)左右(排烟温度为设计值),采用低温省煤器的节能技术将在国内新建的超超临界燃煤发电机组中被广泛采用。
四、高位冷却塔
(一)高位收水冷却塔技术的起源与发展
20世纪70年代末,为减少采用二次循环的核电机组循泵功率,由法国电力公司和比利时哈蒙冷却塔公司研发出一种冷却塔高位收水装置,该装置装设在常规冷却塔淋水填料下部,可将淋水填料底部流出的循环水截留收集,通过管沟送至循泵房的高位吸水井,再经过循环水泵房送回至冷却塔,这样就避免了循环水从冷却塔填料下部直接滴落至冷却塔水池造成的能量浪费,从而达到减少循环水泵扬程的目的,同时还可取消常规冷却塔的集水池,后来就把这种带高位收水装置的冷却塔称为高位收水冷却塔。20世纪80年代中期,这种塔开始在法国核电厂中采用,总体运行情况良好,目前由哈蒙公司建造的最高的法国贝尔维尔核电厂高位塔已安全运行近25年。
在国内,江西彭泽核电站在2009年已与哈蒙公司签订合同,拟建高位收水自然通风冷却塔,塔高达215m,目前已完成设计工作,该塔建成后将成为世界上最高的冷却塔。江西彭泽核电高位塔设计资料见表1-2。
表1-2 江西彭泽核电高位塔设计资料

(二)高位收水冷却塔的特点
1.工艺结构特点
哈蒙公司逆流式自然通风湿式冷却塔的主要特点是采用悬吊式安装方式,即在塔内只设置一层梁系,收水器搁置在梁上、配水管捆绑在梁下,填料采用悬吊装置悬吊在喷溅装置下方,从而可减少塔内结构,减少通风阻力,使冷却塔达到更好的降温性能。
哈蒙高位收水冷却塔的除水器、配水系统及淋水填料的布置与常规冷却塔相同,从上至下分层布置,填料以下则增加了高位收水装置,收水装置占据了塔进风口以上、填料底面以下高约3m的塔内空间,在进风口高度范围内,沿塔径方向布置有一条中央集水槽,高位收水装置搜集的落水通过收水槽自流至中央集水槽。
高位收水装置主要由斜板梁、收水斜板、防溅垫层及收水槽等组成,收水斜板采用PVC波型板制成,在斜板上铺设一层防溅装置,防溅装置为PVC片粘接组装成的蜂窝块,起到防溅、防冲和减噪作用。收水板下方为收水槽,采用玻璃钢制造,负责将落水排至塔中央的集水槽。
高位收水冷却塔塔芯布置示意图如图1-10所示。高位收水冷却塔中央集水槽示意图如图1-11所示。一般来说,高位收水装置利用金属框架固定在填料下方,框架采用不锈钢绳悬吊在梁上,每个收水板下方的收水槽采用法兰连接。

图1-10 高位收水冷却塔塔芯布置示意图

图1-11 高位收水冷却塔中央集水槽示意图
2.性能特点
高位收水冷却塔的主要优点是可以减少冷却塔的供水高度,从而减少循泵电耗,因此它是一种节能型的冷却塔。与根据相关的资料对比,2×1000MW机组高位收水塔系统循环水泵静扬程减少9.8m,每台机组循泵电动机功率减少约3400k W。两台机组年上网电量可增加2720(万kW·h)/年。由于雨区跌落高度降低,高位塔比常规塔的噪声可减小8~10d B,从而可大幅减少噪声治理费用。高位收水冷却塔具有较明显的节能效果及一定的降噪效果,可降低循环水泵功率约33%,符合国家节能环保的政策。
五、大容量超临界循环流化床
循环流化床锅炉是新型、高效、低污染的清洁燃烧技术,这项技术在电站锅炉、工业锅炉和废弃物处理利用等领域已得到广泛应用。循环流化床可以燃用低热值燃料,而且850℃左右是石灰石颗粒吸收二氧化硫的最佳反应温度,实现了低成本的脱硫;同时氮氧化物生成量大幅度降低,直接排放可以满足环保要求。
目前已经投入运行的超临界循环流化床机组有俄罗斯的300MW机组和波兰的460MW机组;2013年4月,我国自主研发的600MW循环流化床超临界示范机组在四川内江白马电厂正式投产,成为目前全世界容量最大的循环流化床超临界机组;2011年,Forster Wheeler公司与韩国Samcheok Green电力公司签订合同,计划2015年实现世界首台800MWCFB超超临界机组商业运行。世界首台800MWCFB超超临界机组示意图如图1-12所示。

图1-12 世界首台800MWCFB超超临界机组示意图
六、整体煤气化联合循环(IGCC)
IGCC是有机集成煤气化和燃气——蒸汽联合循环发电的洁净煤的发电技术。IGCC系统中,煤经过气化产生合成煤气(主要成分是一氧化碳和氢气)。合成煤气经除尘、水洗、脱硫等净化处理后形成净煤气,净煤气被引入燃气轮机燃烧,驱动燃气轮机组发电,燃气轮机组的高温排气在余热锅炉中产生蒸汽,驱动汽轮机组发电。IGCC实现了能量的梯级利用,发电机组的效率较常规燃煤机组效率高5%~7%。IGCC被公认是最具发展前景的洁净煤发电技术之一。
由于燃料在燃烧前进行净化,IGCC电厂的污染物排放量远远低于国际上先进的环保标准。IGCC的煤种适应性广泛,可以燃用我国储量丰富、限制开采的高硫煤,烟台IGCC示范工程在燃用劣质高硫煤(含硫量接近4%、含灰量大于25%)情况下,经计算,其供电效率仍可达43%,并且污染物排放达标。2012年底,我国首台250MW级IGCC示范工程在天津投产,成为世界上第六台商业运行的IGCC机组。整体煤气化联合循环(IGCC)示意图如图1-13所示。

图1-13 整体煤气化联合循环(IGCC)示意图
七、低低温静电除尘器
低低温电除尘器是将通过电除尘的烟气温度,通过低温省煤器等换热手段,从常规的130℃左右降低至90℃左右,以大幅度降低粉尘的比电阻,使得电除尘器的除尘效率得到显著提高,达到30mg/m3或者更低的除尘器出口粉尘浓度排放标准。
低低温电除尘器的入口烟气温度一般90℃左右,低于烟气酸露点温度,这样可使烟气中的大部分SO3气液转化,且被烟尘中的碱性物质吸收、中和,烟气粉尘的比电阻大大降低,粉尘特性得到很大改善。这种方法可大幅提高除尘效率,同时可以去除烟气中部分的SO3。由于烟气温度低、相应的烟气体积流量小,可降低引风机的功率和电耗,缩小静电除尘器的设备体积,从而减少占地面积。低低温除尘器系统示意图如图1-14所示。

图1-14 低低温电除尘器系统示意图
低低温静电除尘器在日本得到了广泛的应用,目前大唐国际福建宁德电厂已经投运此类型的静电除尘器(除尘器入口烟温为95~100℃)。
八、国产100%容量小汽轮机
100%容量小汽轮机具有效率高、投资费用低、系统简单、布置面积小等优点。1×100%容量气泵方案(小汽轮机国产、泵进口)在THA工况下较2×50%气泵方案(小汽轮机及泵国产,芯包进口)的小汽轮机效率约高3.5%,可降低热耗15k J/(kW·h)、煤耗0.6g/(kW·h)左右。目前在350MW、600MW级超临界、超超临界机组中已广泛采用。对于1000MW机组,进口100%容量小汽轮机在国内有投运业绩,国产100%容量小汽轮机尚无投运业绩,但国内杭州汽轮机厂、上海汽轮机厂、东方汽轮机厂等小汽轮机厂均已有订货业绩。
杭州汽轮机厂从20世纪70年代开始全套引进德国西门子积木块、反动式工业汽轮机技术,对原引进的技术系列进行了升级和补充,并在90年代,通过与西门子合作生产一系列机组,进一步完善和发展了该系列工业汽轮机技术。2007年12月已率先出口1000MW机组驱动50%容量锅炉给水泵汽轮机至美国、韩国等国家。
杭州汽轮机厂采用双分流汽轮机作为机型方案,继承了西门子反动式工业汽轮机产品型式。特点为中间进汽,蒸汽向两边均匀分流,分别通过两端的低压级组扭叶片排入冷凝器,汽缸的两端和内部的通流部分为镜面对称,其结构特点类似于大汽轮机的双分流低压缸。
杭州汽轮机厂已有大唐三门峡三期、华能铜川二期1000MW一次再热100%全容量小汽机订货业绩,也有华能莱芜电厂1000MW二次再热2×50%容量小汽机订货业绩。对1000MW机组100%容量小汽机,最大出力满足给水泵轴功率需要,出力可到45MW,选型工况效率为86.9%,额定运行工况效率为86.2%。
上海汽轮机厂给水泵汽轮机继承主汽轮机设计理论,均为引进SIEMENS汽轮机技术,也为反动式工业汽轮机产品形式。上海汽轮机厂已有神华神东万州、神华国华寿光1000MW一次再热100%全容量小汽机订货业绩,汽轮机机型为双缸凝汽式,最大出力满足给水泵轴功率需要,最高出力可到45MW,选型工况效率86.01%,额定运行工况效率85.38%。
关于小汽轮机出力要求,即使采用1000MW二次再热机组,100%容量给水泵轴功率需求比一次再热100%容量泵高10%,达到约43MW,国产小汽轮机完全可以满足1000MW机组100%容量给水泵的需求。
九、1000MW机组变频电源技术
火电厂辅助设备的选型一般按照100%的负荷来确定的,因此辅助设备在机组低负荷时也要消耗大量的电能,运行工况的匹配则通过调节风门挡板或阀门开度等节流方式调节。为了降低系统低负荷运行时的节流损失和效率损失,常规方法多采用变频技术,即系统阀门、挡板保持大开度,通过变频器改变转动机械转速进行工况调节,这要求每台电机独立配备一套变频装置,投入成本较高,所以该技术也只能针对个别设备进行改造。
利用单独设置的调速汽轮机带动发电机提供变频厂用电,依据负荷变化调节变频汽轮机转速,从而实现厂用电变频,大幅降低系统低负荷运行的节流损失及辅机效率损失,达到节能目的。这种方式突破了传统变频技术及理念,创新性提出集中式变频供电系统技术,辅机设备投资将大幅度降低,变频运行的可靠性将大幅度提高。其优势表现在以下两方面:
(1)变频汽轮发电机可工频运行,提高机组的发电量。
(2)增加机组整体排汽面积,可提高机组经济性,1000MW机组可降低1g/(kW·h)煤耗。