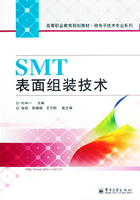
2.4 SMD/SMC的使用
2.4.1 表面组装元器件的包装方式
表面组装元器件的包装形式已经成为SMT系统中的重要环节,它直接影响组装生产的效率,必须结合贴片机送料器的类型和数目进行优化设计。表面组装元器件的包装形式主要有4种,即编带、管装、托盘和散装。大批量生产建议选择编带封装形式;低产量或样机生产,建议选择管装;散装很少使用,因为散装必须一个一个地拾取或需要装配设备重新进行封装。
1.编带包装
编带表装是应用最广泛、时间最久、适应性强、贴装效率高的一种包装形式,并已标准化。除QFP、PLCC和LCCC外,其余元器件均采用这种包装方式。编带包装所用的编带主要有纸带、塑料袋和粘接式带3种。纸带主要用于包装片式电阻、电容。塑料袋用于包装各种片式无引脚组件、复合组件、异性组件、SOT、SOP、小尺寸QFP等片式组件。
如图2-40所示为编带包装料带盘及料带。

图2-40 编带包装料带盘及料带
2.管式包装
管式包装主要用来包装矩形片式电阻、电容以及某些异形和小型器件,主要用于SMT元器件品种很多且批量小的场合。包装时将元件按同一方向重叠排列后一次装入塑料管内(一般100~200只/管),管两端用止动栓插入贴片机的供料器上,将贴装盒罩移开,然后按贴装程序,每压一次管就给基板提供一只片式元件。
管式包装材料的成本高,且包装的元件数受限。同时,若每管的贴装压力不均衡,则元件易在细狭的管内被卡住。但对表面组装集成电路而言,采用管式包装的成本比托盘包装要低,不过贴装速度不及编带方式。
图2-41为集成电路的防静电管式包装图。从图中可以看出,集成电路的形状决定着塑料管的形状。同时,硬塑料可以避免SMD/SMC运输中被损坏。

图2-41 防静电管式包装
3.托盘包装
托盘包装是用矩形隔板使托盘按规定的空腔等分,再将器件逐一装入盘内,一般50只/盘,装好后盖上保护层薄膜。托盘有单层、三层、十层、十二层、二十四层自动进料的托盘送料器。这种包装方法开始应用时,主要用来包装外形偏大的中、高、多层陶瓷电容。目前,也用于包装引脚数较多的SOP和QTP等器件。
托盘式包装的托盘有硬盘和软盘之分。硬盘常用来包装多引脚、细间距的QTP器件,这样封装体引出线不易变形。软盘则用来包装普通的异形片式元件。
单层托盘包装SMD如图2-42所示。

图2-42 托盘包装
4.散装
散装是将片式元件自由地封入成形的塑料盒或袋内,贴装时把塑料盒插入料架上,利用送料器或送料管使元件逐一送入贴片机的料口。这种包装方式成本低、体积小,但适用范围小,多为圆柱形电阻采用。
SMT元器件的包装形式也是一项关键的内容,它直接影响组装生产的效率,必须结合贴片机送料器的类型和数目进行最优化设计。
2.4.2 表面组装器件的保管
表面组装器件一般有陶瓷封装、金属封装和塑料封装。前两种封装的气密性能较好,不存在密封问题,器件能保存较长的时间。但对于塑料封装的SMD产品,由于塑料自身的气密性较差,所以要特别注意塑料表面组装器件的保管。
绝大部分电子产品中所用的IC器件,其封装均采用模压塑料封装,其原因是大批量生产易降低成本。但由于塑料制品有一定的吸湿性,因而塑料器件(SOJ、PLCC、QFP)属于潮湿敏感器件。由于通常的再流焊或波峰焊,都是瞬时对整个SMD加热,等焊接过程中的高热施加到已经吸湿的塑封SMD壳体上时,所产生的热应力会使塑壳与引脚连接处发生裂缝。裂缝会引起壳体渗漏并受潮而慢慢地失效,还会使引脚松动从而造成早期失效。
1.塑料封装表面组装器件的储存
在塑料封装的表面组装器件存储和使用中应注意:库房室温低于40℃,相对湿度小于60%,这是塑料封装袋表面组装器件贮存场地的环境要求;塑料封装SMD出厂时,都被封装于带干燥剂的潮湿包装袋内,并注明其防潮湿有效期为一年,不用时不开封。
2.塑料封装表面组装器件的开封使用
开封时先观察包装袋内附带的湿度指示卡。当所有黑圈都显示蓝色时,说明所有的SMD都是干燥的,可以放心使用;当10%和20%的圈变成粉红色时,也是安全的;当30%的圈变成粉红色时,即表示SMD有吸湿的危险,并表示干燥剂已经变质;当所有的圈都变成粉红色时,即表示所有的SMD已严重吸湿,贴装前一定要对该包装袋中所有的SMD进行驱湿烘干处理。
下面介绍湿度指示卡读法。湿度指示卡有许多品种,但基本上可以归纳为六圈式和三圈式,三圈式如图2-43所示。六圈式的可显示湿度为10%、20%、30%、40%、50%和60%,三圈式的只有30%、40%和50%,其所指示的某相对湿度是介于粉红色圈和蓝色圈之间的淡紫色圈所对应的百分数。例如,30%的圈变成粉红色,40%的圈仍显示蓝色,则蓝色与粉红色之间显示淡紫色的圈旁的30%,即为相对湿度值。

图2-43 三圈式湿度指示卡
3.包装袋开封后的操作
SMD的包装袋开封后,应遵循下列要求从速取用。生产场地的环境:室温低于30℃、相对湿度小于60%;生产时间极限为:QFP为10h,其他(SOP、SOJ、PLCC)为48h(有些公司为72h)。
所有塑封SMD,当开封时发现湿度指示卡的湿度为30%以上或开封后的SMD未在规定的时间内装焊完毕,以及超期储存的SMD等情形时,在贴装前一定要先进行驱湿烘干。烘干方法分为低温烘干法和高温烘干法。
低温烘干法中的低温箱温度为40±2℃,适用的相对湿度小于5%,烘干时间为192h;高温烘干法中的烘箱温度为125±5℃,烘干时间为5~8h。
凡采用塑料管包装的SMD(SOP、SOJ、PLCC、QFP等),其包装管不耐高温,不能直接放进烘箱中烘烤,应另行放在金属管或金属盘内才能烘烤。
QFP的包装塑料盘有不耐高温和耐高温两种。耐高温的可直接放入烘箱中进行烘烤;不耐高温的不能直接放入烘箱烘烤,以防发生意外,应另放在金属盘进行烘烤。转放时应防止损伤引脚,以免破坏其共面性。
4.剩余SMD的保存方法
(1)配备专用低温低湿储存箱。将开封后暂时不用的SMD连同送料器一起存放在箱内,但配备大型专用低温低湿储存箱的费用较高。
(2)利用原有完好的包装袋。只要袋子不破损且内装干燥剂良好,仍可将未用完的SMD重新装回袋内,然后用胶带封口。
2.4.3 表面组装元器件的使用要求
SMT在电路安装生产中成为电子工业的重要技术,原因在于SMC和SMD的体积小、质量轻、互连性好、组装密度高、寄生阻抗小、高频性能好、可冲击震动性能高、具有良好的自动化生产程度,可大幅提高生产效率,现在SMD已经广泛用于PC、程控交换机、移动电话、寻呼机、对讲机、电视机、VCD、数码相机等为数众多的电子产品中。目前,世界发达国家SMC和SMD的片式化率已达到70%以上,全世界平均片式化率达到40%,而我国的片式化率不到30%,因此应将SMT、SMD、SMC等新工艺和新型电子元器件作为电子工业的发展重点。
采用SMT工艺与过去传统的“插件+手工焊”工艺对生产设备的要求和元器件的选用、PCB的设计、工艺、工序的安排有很大的不同,在设计中就应全盘考虑,统一规划。因为设计质量不仅仅是由电路设计的先进性和电路原理的可行性所决定,同时要统筹安排SMC和SMD的选择、PCB设计和板上布局、工艺流程的先后次序及合理安排等。即电子元器件的采购和生产制造工艺在设计初期就应融于设计师的主导思想中,并落实在具体产品生产中。