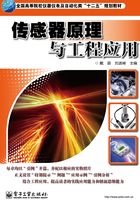
B部分 力及力矩测量传感器
2.8 测力基本知识及测力传感器
2.8.1 力的测量方法
力是最重要的物理量之一。当力施加于某一物体后,将产生两种效应,一是使物体变形,在材料中产生应力,这是力的“静力效应”;二是使物体的机械运动状态或所具有的动量改变而产生加速度,这是力的“动力效应”。力的测量方法可以归纳为利用力的动力效应和静力效应两种。
1.利用动力效应测力
力的动力效应使物体产生加速度,由牛顿第二定律可知:当物体质量确定后,该物体所受力和产生的加速度之间有确定的对应关系,因此只需要测出物体的加速度,就可间接测得力的大小。
2.利用静力效应测力
由胡克定律可知:弹性物体在力的作用下产生变形时,若在弹性范围内,物体所产生的变形量与所受力值成正比,如果通过一定手段测出物体的弹性变形量,就可间接确定物体所受力的大小,电阻应变式测力传感器就属于此类。另外也可利用与内部应力相对应参量的物理效应来确定力值,如利用压电效应、压磁效应的测力传感器。在机械工程中,大部分测力方法都是基于静力效应,以下介绍此类方法中常用的测力传感器。
2.8.2 电阻应变式测力传感器
利用电阻应变片制作的测力传感器广泛应用于静态和动态测量中,它是目前数量最多、种类最全的测力传感器,量程范围为10-2~107N。电阻应变式测力传感器主要作为各种电子秤和材料试验机的测力元件,目前90%的电子秤使用的都是电阻应变式测力传感器。
各类电阻应变式测力传感器的工作原理相同:利用弹性元件将被测力转换成应变,粘贴在弹性元件上的应变片将应变转换为电阻变化,再由电桥电路转换为电压,经放大处理后显示被测力的大小。弹性元件是电阻应变式测力传感器的基础,其性能好坏是保证测力传感器使用质量的关键。根据所利用的应力场的类型,测力传感器弹性元件的结构可分为三类:
(1)正应力式,如柱式弹性元件。
(2)弯曲应力式,如梁式弹性元件。
(3)剪切应力式。为保证测量精度,必须合理选择弹性元件的结构尺寸、型式、材料、加工工艺。
考察测力传感器的优劣除常规的灵敏度、精度、稳定性指标外,还包括过载能力、抗侧向能力大小等特殊要求。设计高精度测力传感器的指导思想是,追求良好的自然线性,提高传感器的输出灵敏度,使传感器的抗侧向能力高,结构简单并易于密封,加工容易等。
以下介绍几种典型的应变式测力传感器,更多形式的测力传感器请读者参考有关书籍。
1.柱式测力传感器
这类应变式测力传感器采用实心或空心圆形或方形柱体作为弹性元件,其特点是结构简单、紧凑、易于加工,可设计成压式或拉式,或拉、压两用型。柱式力传感器可承受最大载荷107N,用于大、中量程的称重传感器(1~500t)。在测103~105N载荷时,为提高变换灵敏度和抗横向干扰,一般采用空心圆柱结构。
柱式测力传感器的缺点是灵敏度、精度较低;受力点位置变化对输出灵敏度有较大影响;抗侧向力和抗偏载能力差,因此柱式测力传感器需要在桥路和结构中采取补偿措施。
以图2.16所示的柱式测力传感器的布片和桥路连接方式为例,对图2.16(a)所示的柱体,当受拉力F作用时,根据材料力学,柱沿轴向的应变为
式中,S为圆柱的横截面积;E为材料弹性模量。
可见,应变的大小取决于S、E、F的值,与圆柱的轴长度无关。
设计柱式测力传感器时,圆柱直径d应根据所选用材料的允许应力[σb]来计算。根据,可得圆柱直径大小为
根据式(2-39),要想提高灵敏度,必须减小圆柱横截面积S,但圆柱抗弯能力会减弱,且对横向干扰力敏感,为此,对较小集中力的测量,多采用空心柱。
对空心柱,式(2-39)仍适用。空心柱在同样的横截面下,其心轴直径可更大,抗弯能力大大提高,但空心柱在壁簿时,受力后将产生桶状变形而影响精度。
由于空心柱面积,则空心柱外径D大小为
式中,D为空心柱外径;d为空心柱内径。
弹性元件的高度对传感器的精度和动态特性都有影响。由材料力学可知,高度对沿其横截面的变形有影响。当高度与直径的比值H/D≫1时,沿其中间断面上的应力状态和变形状态与其端面上作用的载荷性质和接触条件无关。试验研究的结果建议采用式(2-42)计算:
H≥2D+l (2-42)
式中,l为应变片的基长。
对空心柱建议采用式(2-43)计算:
H≥D-d+l (2-43)
当柱体在轴向受拉或压作用时,其横断面上的应变实际上是不均匀的。这是因为作用力不可能正好通过柱体的中心轴线,这样柱体除受拉(压)外,还受到横向力和弯矩。通过恰当的布片和桥路连接方式可以减小这种影响。

图2.16 柱式测力传感器的布片和桥路连接方式
图中各应变片的应变分别为
式中,εt为温度引起的虚假应变。全桥电桥的输出电压为
图2.17所示为国产的BLR-1型拉力传感器。传感器弹性元件为空心圆筒,材料为40Cr钢。沿轴向和径向各粘贴4片应变片,共8片应变片组成全桥。这种传感器可测的载荷范围为0.2~100t,弹性元件尺寸依据测量载荷的上下限设计。BLR-1型传感器性能指标见表2-5。

图2.17 BLR1型拉力传感器
表2-5 BLR-1型应变传感器性能指标

图2.18 拉力传感器弹性元件形状
【设计示例1】
以图2.17所示的国产BLR-1型拉力传感器为例,设计一个满量程为9.8kN的拉力传感器。拉力传感器弹性元件形状如图2.18所示,材料选用40CrNiMo,材料的强度极限σb=1100MPa,比例极限σp=800MPa,材料弹性模量E=210GPa,泊松系数μ=0.29。
1)设计思路
常规柱式应变力传感器的测量灵敏度应达到1~3mV/V,设计时以此为依据计算弹性元件的相关参数,再对弹性元件进行强度校核,直至同时满足测量灵敏度和使用强度要求。
采用恒压源电桥电路,布片及电桥如图2.16所示,电桥的输出表达式为Uo=(1+μ)KεUi,即
取应变片灵敏系数K=2,Uo/Ui=2mV/V,代入上式计算得最大应变值为
取[ε]max=8×10-4。
2)弹性元件内径、外径的计算
根据拉伸时轴向应变ε、力F与面积S之间的关系:,将已知参数代入,计算出弹性元件截面积:
弹性元件的外径d1不能选择得太小,否则会由于力的偏心造成很大的误差。这里选用外径为d1=1.5cm的空心管,其面积为,则内径d2为
,可保留一位小数,即d2=1.3cm。可知空心管壁厚t=0.1cm。
3)柱高h及其他尺寸的确定
为了防止弹性元件受压时出现失稳现象,柱高h应当选得小些,但又必须使应变片能够反映截面应变的平均值,这里选用弹性元件工作段的长度:h=2d1=3cm。
由于壁很薄,还必须检验管心是否会出现局部失稳。薄壁管的失稳临界应力计算如下:
校核在超过满量程150%情况下,弹性元件截面中的应力大小如下:
计算表明,受力超过满量程150%时的应力远远小于材料的比例极限和临界应力,这表明该弹性元件不会出现弹性失稳。另外,弹性元件两端有螺纹孔,以便连接拉力螺栓,螺孔设计为M14,查阅相关手册可知它的许用载荷远远大于9.8kN。
4)输出量的计算
根据弹性元件设计尺寸,计算满量程下的轴向应变:
对应电桥单位激励电压下的输出量为
故知设计满足灵敏度和强度要求。
【应用示例1】
应变式荷重传感器在电子汽车衡中的应用。
汽车衡是大宗货物计量的主要称重设备,用于企业物资进出、公路交通收费站对货物的计量称重。作为机械式衡器的更新换代产品,电子汽车衡已被广大用户所认可,为越来越多的企业所选用。如图2.19所示,电子汽车衡主要是由承载器、称重传感器、称重显示器三部分组成。承载器为钢制构架或钢架混凝土结构,称重台面的尺寸根据车型选择不同规格。称重传感器被喻为电子衡器的心脏,它的性能在很大程度上决定了电子衡器的准确度和稳定性。汽车衡工作环境比较恶劣,高温、粉尘、潮湿、腐蚀、电磁干扰等对传感器工作性能都会有很大影响,在传感器的制作和安装时要考虑上述因素的影响,并采取相应措施。
根据电子汽车衡的用途、秤体需要支撑的点数(支撑点数应根据使秤体几何重心和实际重心重合的原则而确定)确定一台汽车衡中所用称重传感器数量。一般为4个、6个或8个。
传感器量程用以下公式计算:
C=K0K1K2K3(Wmax+W)/N (2-46)
式中,C为单个传感器的额定量程;W为秤体自重;Wmax为被称物体净重的最大值;N为秤体所采用支撑点的数量;K0为保险系数,一般取值在1.2~1.3之间;K1为冲击系数;K2为秤体的重心偏移系数;K3为风压系数。
例如:一台型号为SCS-30的电子汽车衡,最大称量是30t,秤体自重为1.9t,采用四只传感器,根据实际情况,选取保险系数K0=1.25,冲击系数K1=1.18,重心偏移系数K2=1.03,风压系数K3=1.02。根据式(2-46),传感器的吨位C=12.36t,可选用量程为15t的传感器。

图2.19 电子汽车衡
【特别提示】
一般应使传感器工作在其30%~70%量程内,但对于一些在使用过程中存在较大冲击力的动态轨道衡、动态汽车衡等,一般要扩大其量程,使传感器工作在其量程的20%~30%之内,保证传感器的使用安全和寿命。
2.梁式力传感器
为了获得较大的灵敏度,可采用梁式结构的弹性元件。弹性梁的基本形式如图2.20所示。图2.20(a)所示的等强度梁受力弯曲后,梁表面的应变为

图2.20 弹性梁的基本形式
【特别提示】
由式(2-47)可知,等强度梁对应变片粘贴位置的准确性没有严格要求,但应变大小随着力点的位置而改变,可能引起测量误差。
设计等强度梁时,可先设定梁的厚度h、长度l,根据在最大载荷下梁的应力不应超过材料允许应力[σb],即可求得梁的宽度b0以及沿梁长度方向宽度的变化值,即
需注意的是,等强度梁端部截面积不能为零,所需的最小宽度应按材料的允许剪应力[τ]来确定如下:
对图2.20(b)所示的等截面梁,当力作用于自由端时,在应变片粘贴位置的应变为
【特别提示】
等截面梁结构简单,易加工,灵敏度高,但梁各个位置的应变不同,因此对应变片粘贴位置准确性有严格要求,同时着力点的移动也会引起测量误差。
【引例分析】
本章引例中的电阻应变式荷重传感器是一种广泛应用于工业电子秤和商业电子秤的测力/称重传感器,适于几百克到几百千克载荷的测量。这种传感器的弹性元件是一种改进形式的梁——双孔平行梁,试证明该传感器的灵敏度不受荷重位置的影响。
分析:无论荷重安放在秤盘的任何位置,都可以将其简化为作用于双孔平行梁端部的力F和力矩M,如图2.21所示。

图2.21 双孔平行梁式力传感器
根据式(2-50),梁上各应变片粘贴处的应变为
电桥输出电压:
灵敏度:
可见,这种传感器的最大特点是载荷的安放位置不会影响传感器输出信号的大小。
3.剪切式力传感器
剪切式力传感器是将电阻应变片安装在弹性元件上剪应变最大处的主应变方向而实现测力的。通过理论分析和实践发现,剪切式力传感器的输出灵敏度和精度比柱式力传感器高,且输出灵敏度不受受力点位置变化的影响,适于设计中等量程(0.5~50t)、高精度的称重传感器。

图2.22 梁式剪切力传感器的基本形式
图2.22所示为两种梁式剪切力传感器的基本形式。梁长度的中间截面弯矩为零,中性层处是最大剪应变所在处,为此将电阻应变片安装在该截面的中性层上,栅丝与中性层成45°方向,即最大正应变方向。
矩形截面梁应变与外力的关系:
工字形截面梁:
式中,G为剪切弹性模量,G=E/2(1+μ)。
矩形截面梁的剪应力分布呈高抛物线状,剪应力变化梯度大,当应变片贴片位置有偏差时对传感器的灵敏度和性能影响较大,为此,通常将梁的截面设计成工字形。工字形截面梁的剪应力分布比较均匀(τmax/τmin=1.25),易于保证中性层处的相当应力和应变是弹性元件中的最大值,贴片位置偏差对传感器的灵敏度和性能影响小,而且从式(2-51)与式(2-52)的比较可以看出,还可以提高灵敏度。
【设计示例2】试设计一个轮辐式剪切力传感器。
轮辐式剪切力传感器的弹性元件好像一个车轮,由轮毂、轮箍和轮辐三部分组成,通常是用整块金属加工出来的,如图2.23所示。轮辐式剪切力传感器结构紧凑、外形低、抗偏心载荷和侧向力强,可承受较大载荷并有超载保护能力,用于0.5~500t的高精度载荷测量。
1)轮辐截面尺寸设计
轮辐尺寸设计思路:以满足传感器灵敏度为前提,先确定b和h大小,再进行强度校核。
在保证轮毂和轮圈的刚度足够大的情况下,轮辐就可以看成两端固支的矩形截面梁,在轮辐条中间截面(L/2处)的弯矩为零,在该截面中性层处安装电阻应变片,可以得到轮辐中性层处沿45°方向的正应变为
每个轮辐两侧面各粘贴一片应变片,与中性层成±45°,一片受拉,一片受压,8片应变片的电桥连接方式如图2.24所示,则应变电桥的输出为

图2.23 轮辐式剪切力传感器

图2.24 电桥连接方式
式中,各符号含义见图2.22以及前文所述。
一般轮辐式传感器灵敏度为Uo/Ui=(1~3)mV/V,则由式(2-54)可求出b和h的大小。
2)轮辐强度校核
选定的轮辐截面上切应力应满足:
式中,[τ]为材料许用剪切力。
弯曲强度校核:
式中,[σb]为材料许用应力。
校核中若不能满足要求,应重新选取h和b的比值,再进行验算,直到满足为止。
3)轮辐长度
在贴片允许的情况下,为保证轮辐承受纯剪切力作用,长度L应尽量小,一般取。
4)过载保护间隙δ
在轮毂底面与轮箍底面之间留有一定间隙δ,其作用是:当载荷施加在轮毂上时,轮辐产生挠曲变形,使δ减小。当超过额定值时,将使δ=0,轮辐不再产生变形,从而起到保护作用。设过载最大载荷为额定载荷F的m倍,则间隙δ为
【特别提示】
为准确测出轮辐上的剪切应力,最好通过光弹实验找出主应力方向,再沿与主应力方向成45°方向贴片。
2.8.3 压磁式力传感器
压磁式力传感器的工作原理是基于铁磁材料的压磁效应,压磁效应是指某些铁磁材料在机械力的作用下磁导率发生变化的现象,也称为磁弹性效应。图2.25所示为压磁元件结构及工作原理,由工业纯铁、硅钢等铁磁材料制成的铁芯上分别绕着互相垂直的励磁线圈和测量线圈,若无外力作用,励磁线圈所产生的磁力线在测量线圈两侧对称分布,合成磁场强度与测量线圈绕组平面平行,磁力线不和测量线圈交链,因此测量线圈不会产生感应电势,如图2.25(b)所示。当外力作用在铁芯上,如为压力,则沿应力方向磁导率下降,与应力垂直的方向磁导率增加;如受拉力,磁导率变化相反。总之在外力作用下磁力线分布发生变化,部分磁力线与测量线圈交链从而产生感应电势。作用力越大,感应电动势越大。

图2.25 压磁元件结构工作原理

图2.26 压磁式力传感器结构
1—压磁元件;2—柜架;3—弹性梁;4—钢球
图2.26所示为一种典型的压磁式力传感器结构。压磁元件安装在弹性体结构的框架内,弹性梁的作用是对压磁元件施加预压力和减少横向力及弯矩的干扰,钢球用来保证力F沿垂直方向作用。
压磁式力传感器的输出信号大,测量电路中一般不需要放大器,而只需要有稳定的励磁电源和良好的检波、滤波电路。压磁式力传感器可测载荷大(达1MN以上)、过载能力强(达300%),测量精度较高(1%),主要应用在冶金、矿山、造纸、运输等行业。
2.8.4 压电式力传感器
压电式力传感器利用石英晶体、压电陶瓷等材料的压电效应,将施加于压电元件上的力转换成与其成正比的电量输出(详见本书第5章)。
压电式力传感器主要用于动态力的测量,具有很好的动态响应特性,工作频带宽,灵敏度高,线性度好,量程从几十毫牛到几十兆牛。
图2.27所示为YDS-78型压电式传感器结构。它是单向压电式测力传感器,可用于机床动态切削力的测量。石英晶片为零度x切晶片,尺寸为φ8×1mm,上盖为传力元件,其变形壁的厚度为0.1~0.5mm,由测力范围决定,Fmax=5000N。绝缘套用来电气绝缘和定位。基座内外底面对其中心线的垂直度、上盖以及晶片、电极的上下底面的平行度与表面粗糙度都有极严格的要求,否则会使横向灵敏度增加或使晶片因应力集中而过早破碎。为提高绝缘阻抗,传感器装配前要经过多次净化(包括超声清洗),然后在超净工作环境下进行装配,加盖之后用电子束封焊。YDS-78型压电式传感器的性能指标见表2-6。

图2.27 YDS78型压电式传感器结构
表2-6 YDS78型压电传感器性能指标
【应用示例2】YDS-78型压电式传感器在车床切削力测试中的实际应用。
图2.28所示压电式动态力传感器在车库中用于动态切削力的测量,压电传感器安装在车削刀具的下端。当工件旋转,车刀开始切削工件时,垂直方向的车削力Fz作用于刀具上,并通过刀具传递到压电传感器上,由此完成对车削力Fz的测量。

图2.28 压电式动态力传感器在车床中用于动态切削力的测量
1—压电式动态力传感器;2—夹具;3—车刀;4—工件
2.9 力矩测量基本知识及力矩传感器
2.9.1 力矩的测量方法
力矩是力和力臂的乘积。在力矩作用下机械零部件会发生转动或一定程度的扭曲变形,因此力矩也称为转矩或扭转矩。力矩的法定计量单位为“牛顿·米”(N·m)。
在测量扭矩的诸多方法中,最常用的是通过弹性轴在传递力矩时产生的变形、应变、应力来测量扭矩。常用的弹性轴如图2.29所示。

图2.29 用于测量扭矩的弹性轴
把弹性轴联接在驱动源和负载之间,弹性轴就会产生扭转。在材料的弹性极限内弹性轴的扭转角与扭矩呈线性关系:
式中,φ为弹性轴的扭转角(rad);l为弹性轴的测量长度(m);d为弹性轴的直径(m);M为扭矩(N·m);G为弹性轴材料的切变模量(Pa)。
按弹性轴变形测量时
按弹性轴应力测量时
式中,σ为转轴外表面的剪切应力。
按弹性轴应变测量时
式中,ε45°、ε135°为转轴外表面上与轴线成45°方向或135°方向的主应变。
可见只要测得扭转角或应力、应变,就可知道扭矩大小。按扭矩信号产生的方式可以设计为光电式、光学式、磁电式、电容式、电阻应变式、压磁式、振弦式等各种扭矩仪器。
2.9.2 电阻应变式扭矩传感器
电阻应变式扭矩传感器测量精度高达±(0.2~0.5)%,线性度可达0.05%,重复性达0.03%,测量范围为5~50000N·m,在扭矩测量中应用较广泛。但它的安装要求高,且易受温度影响,在高转速时测量误差较大。
测量时将应变片沿与轴线成45°或135°方向粘贴在弹性轴或直接粘贴在被测轴上,扭力杆上应变片的粘贴及电桥连接如图2.30所示。当转轴受转矩M作用时,应变片感受到弹性轴的应变,转矩与应变的关系如式(2-61)。

图2.30 扭力杆上应变片的粘贴及电桥连接
当测量小转矩时,考虑到抗弯曲强度、临界转速、应变片尺寸及粘贴工艺等因素,多采用空心轴。对于空心圆柱形轴,应变片产生的应变量与转矩的关系为
式中,d和D分别为空心转轴的内径和外径。
大量程转矩测量时一般采用实心方形截面弹性轴。对于正方形轴,应变与转矩的关系为
式中,a是正方形轴边长。
为保证转轴在正反力矩作用下的输出灵敏度相同,应该注意应变片的中心线必须准确地粘贴在弹性轴表面的45°及135°螺旋线上,一般粘贴角度的允许误差范围±0.5°。采用应变花可以简化粘贴并易于获得准确的位置。
电阻应变式扭矩传感器的工作原理如图2.31所示。扭矩传感器由弹性轴和粘贴在轴上的应变片组成,它作为扭矩传递系统的一个环节,和转轴一起旋转。为了给旋转着的应变片供电,并提取电桥输出信号,采用由滑环和电刷组成的集流环部件来完成传递。通过滑环(固定在转轴上)和电刷(固定在机架上)的接触,将应变电桥所需的激励电压输入,并获得电桥输出信号传输到静止的仪器上。
由于轴转动时滑环和电刷的相对滑动会产生电噪声,影响检测信号的质量,因此现在多采用电磁场耦合方式的电感和电容集流环,无接触地实现输入、输出端信号的耦合。

图2.31 电阻应变式扭矩传感器的工作原理
2.9.3 其他类型的扭矩传感器
转轴受扭矩作用产生扭转变形后,轴上两横截面的相对扭转角与扭矩成正比,若用磁电式或光电式传感器提取信号,则信号相位差与扭转角成正比,从而实现扭矩测量。
以磁电式扭矩传感器为例,其工作原理如图2.32所示。在转轴上固定一对测量齿轮,如图2.32(a)所示,它们的材质、尺寸、齿形和齿数均相同,两个相同的磁电式检测头A和B对着齿顶安装。图2.32(b)是磁电式测头转换原理示意图。磁电式测头的工作原理是法拉第电磁感应定律:当测量齿轮转动时引起通过线圈的磁通量变化,从而使线圈输出感应电动势e=-NdΦ/dt,式中N为线圈匝数。两测头输出信号波形如图2.32(c)所示。设转轴空载旋转时两测头输出信号相位差为θ0,当被测轴受到扭矩产生扭转变形时,引起两测量齿盘相对转动角度φ,因此两个传感器输出的感应电动势将因扭矩在相位上改变相位角Δθ,Δθ=zφ,结合式(2-59)得扭矩与两路信号相位变化的关系为
式中,z为传感器测量齿轮的齿数。
考虑到正、反方向转矩及超载转矩,一般取π/2<Δθ<π,则对应齿数z为10~100。
对两路信号相位差Δθ的处理计算可采用硬件电路或软件编程的方法,具体内容可参阅相关资料。此类相位差式转矩仪测量范围一般为0.2~100000N·m,转速分挡为0~1500~6000r/min,测量精度为±(0.2%~0.1%)。

图2.32 磁电式扭矩传感器原理示意
1—永久磁铁;2—铁芯;3—线圈;4—测量齿轮