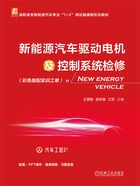
五 三相交流永磁同步电机
永磁电机一般可以分为两类:一类称为永磁同步电机(Permanent Magnet Synchronous Motor, PMSM),另一类称为永磁无刷直流电机(Brushless Direct Current Motor, BLDCM)。这两类电机共同的结构特点是转子都是永磁体,定子都是三相绕组;不同的是永磁无刷直流电机输入的是交流方波,采用离散转子位置反馈信号控制电机定子绕组换相,从而产生旋转磁场,而永磁同步电机输入的是交流正弦波或近似正弦波,采用连续转子位置反馈信号进行控制。
图1-26所示为永磁无刷直流电机工作原理图。离散转子位置传感器安装于电机一端,由3个位置相差120°的光电器件VP1、VP2、VP3和随转子旋转的遮光板(信号盘)组成。当转子旋转时,遮光板控制从光源射来的光线依次照射在各个光电器件上从而使其导通。3个光电器件VP1、VP2、VP3分别控制3个功率开关晶体管V1、V2和V3。

图1-26 永磁无刷直流电机工作原理图
当光电器件VP1被光照射,从而使功率开关晶体管V1呈导通状态,V2、V3截止时,电流流入绕组A-A′,如图1-27a所示。该绕组电流同转子磁极作用后所产生的转矩使转子磁极按图中所示的顺时针方向运动。当转子位置传感器的遮光板旋转到光电器件VP2被光照射时,V1截止,V2导通,V3截止,电流从绕组A-A′断开,而流入绕组B-B′,使得转子磁极继续朝箭头的方向转动,如图1-27b所示。同理,当转子位置传感器的遮光板旋转到光电器件VP3被光照射时,V1、V2截止,V3导通,电流从绕组B-B′断开,而流入绕组C-C′,使得转子磁极继续朝箭头的方向转动,如图1-27c所示。转子磁极继续朝顺时针方向旋转,并重新回到图1-27a所示的位置。这样,随着位置传感器遮光板的转动,定子绕组在光电器件VP1、VP2、VP3的控制下依次换相,形成旋转磁场,吸引永磁体转子随旋转磁场运动。

图1-27 永磁无刷直流电机定子磁场旋转示意图
这里要注意的是永磁无刷直流电机的“换相”与有刷直流电机的“换向”是不同的。有刷直流电机的换向是在转子电枢中发生的,换向器切换不同的导体通电,确保电机产生同向转矩;而永磁无刷直流电机“换相”控制的是定子绕组,通过控制定子三相绕组一相一相地按顺序通电,产生旋转磁场从而获得转矩。不难看出,在“换相”过程中,定子各相绕组在工作气隙内所形成的旋转磁场是跳跃式的,旋转磁场在360°的范围内只有3种磁场状态,每种磁场状态持续120°。各个换相的操作是由控制器根据转子位置传感器的信号,控制功率开关晶体管截止与导通完成的。
对于电动汽车驱动电机的应用,通过理论分析对比,可知永磁同步电机(PMSM)在调速范围、转矩脉动、控制精度等方面明显优于永磁无刷直流电机(BLDCM),故车用永磁电机主要为三相交流永磁同步电机。下面主要对三相交流永磁同步电机进行介绍。
1.三相交流永磁同步电机组成结构
三相交流永磁同步电机的结构示意和外形如图1-28所示,主要包括机座(机壳)、定子铁心、定子绕组、转子铁心、转轴、轴承、端盖和外部接线盒等部件组成。定子铁心与定子绕组与三相交流异步电机基本相同,定子绕组可以采用集中式绕组或分布式短距绕组,对于极数较多的电机,不可以采用分数槽绕组。三相交流永磁同步电机的转子与三相交流异步电机不同,主要包括转子铁心、永磁体、转轴和轴承,转子结构的选择要兼顾低速恒转矩区的大转矩和高速恒功率区的弱磁调速性能,同时还应保证有足够的机械强度和冷却能力,以减少永磁体的退磁现象。

图1-28 三相交流永磁同步电机的组成结构
三相交流永磁同步电机机座通常采用水冷结构,内铸有冷却液流动空腔。此外在电机的末端还须安装有绝对位置传感器,用来检测转子位置,以此对电机进行控制。
(1)定子 三相交流永磁同步电机的定子结构和异步电机类似,均由定子铁心、定子绕组和机座、接线盒等部分组成。机座的作用主要是固定定子铁心和支撑转轴,要求具有足够的强度和良好的通风散热条件,其外壳通常铸有散热片或者水道。定子铁心作为电机主磁路的一部分,在三相交流永磁同步电机运行时,其磁场是交变的,从而产生铁损耗。为了减少铁损耗,三相交流永磁同步电机定子铁心通常采用磁导率较大、磁滞回线面积较小,厚度为0.25mm、0.27mm、0.30mm、0.35mm或0.50mm的硅钢片,经剪裁、冲压、叠压而成,硅钢片表面有绝缘层,如图1-29所示。

图1-29 定子铁心
定子铁心的内圆上均匀地分布着定子槽,槽内嵌放定子绕组。定子绕组是电机的电路部分,用以从电源输入电能并产生气隙内的旋转磁场。三相交流永磁同步电机的三相绕组每两相之间一般在空间上互相间隔120°电角度,每相绕组由若干线圈连接组成。三相绕组的首尾共有6个出线端,若将首尾相连引出3个接线端则为三角形联结方式;若将3个尾端并接在一起,由首端引出3个接线端则为星形联结方式。电机的接线盒可由3根线引出,但一般引出6根线,便于客户自行选择需要的联结方式。三相交流永磁同步电机定子绕组主要有分数槽集中式绕组和分布式绕组两种,如图1-30所示。

图1-30 三相交流永磁同步电机定子绕组形式
1)分数槽集中式绕组。绕组的每极每相槽数为分数,例如:某电机定子槽数Z=24,相数m=3,极数为2pn=6(pn为磁极对数),故每极每相槽数q=24/(3×6)=4/3。一个典型的12槽分数槽集中式绕组如图1-31所示。定子铁心内圆周开了12个槽,形成12个齿,每个齿端部有极靴。把定子线圈直接绕在定子齿极上,所有线圈节距为1,共12个线圈。4个蓝色线圈串联组成A相绕组;4个绿色线圈串联组成B相绕组;4个黄色线圈串联组成C相绕组。各相绕组的线圈通常采用串联连接,如图1-32所示。各相绕组的线圈也可以由3个单个的绕组组成星形联结,再并联使用,如图1-33所示。并联线圈要求线要更细些,匝数要多些。

图1-31 12槽分数槽集中式绕组结构

图1-32 12槽分数槽集中式绕组串联连接

图1-33 12槽分数槽集中式绕组并联连接
分数槽集中式绕组是将线圈缠绕在定子齿极上,其绕制方法比较简单,可以利用绕线机进行批量生产,成本低。此外,分数槽集中式绕组一个齿一个线圈,故绕组端部较短,产生的铜损耗小,效率高,并且绕组无重叠,相间绝缘好,适用于轴向尺寸要求苛刻的场合。但是由于其极数和槽数相近,绕组分布不是正弦的,其定子磁动势中谐波成分高,转矩脉动和径向力谐波较大,对整车噪声与振动(NVH)性能影响较大。
2)分布式绕组。分布式绕组的每个磁极由一个或多个线圈按照一定的规律嵌放组成线圈组,通电后可以形成不同极性的磁极。采用分布式绕组可有效改善定子绕组中磁动势的正弦性,削弱谐波电动势,每极每相槽数越多,改善波形效果越好。由于分布式绕组具有较好的电气性能,所以在车用驱动电机上使用较为广泛。
分布式绕组有单层绕组和双层绕组两种形式。单层绕组属于整距绕组,一般只用于小容量电机,嵌线工艺简单、无层间绝缘、槽满率高,但绕组波形不是标准正弦波,磁场谐波含量较双层绕组大,转矩脉动与NVH略高,需要通过转子磁极的设计来降低转矩脉动。双层绕组的铁心槽内每槽均嵌放有两个线圈元件边,当线圈元件的一个线圈边嵌放在某一槽的上层,其另一个线圈边嵌放在另一槽内的下层,如图1-34所示。

图1-34 双层绕组线圈的嵌线方法
以车用驱动电机最常见的三相48槽8极电机为例,电机定子绕组基本数据:槽数Z=48,相数m=3,极数2pn=8(磁极对数pn=4),每极每相槽数为q=48/(8×3)=2,极距τ=Z/2pn=6。定子内圆周按转子旋转方向的顺序给各个槽依次编号(1#~48#),定子槽分布在pn×360°的电角度内,相邻两个槽内导体感应电势的相位差就是一个电槽距角,电槽距角α=(pn×360°)/Z=(4×360°)/48=30°,则相邻两个槽内导体的感应电动势的相位就相差30°电角度,槽电动势相量图如图1-35所示。

图1-35 三相48槽8极电机槽电动势相量图
定子绕组一个线圈的两个边所跨定子圆周上的距离称为节距,用y表示。一个极在定子圆周上所跨的距离称为极距,用τ表示,节距和极距一般用槽数来计算。分布式双层绕组的总线圈个数等于总槽数。由于是双层绕组,一个槽内有两层导体,所以节距y有多种选择。当节距与极距相等(即y=τ)时,称为整距绕组,此时线圈获得的基波电动势最大,但按照非工作谐波最小原则,y=τ并不是一个最好的选择,因为此时的感应电动势通常会存在很大的谐波,因此通常采用短节距,即选取y<τ且y≈τ为宜,称为短距绕组。当y≈(5/6)τ时,可以同时有效削弱五次和七次谐波,且能节省端线的用量。
典型的分布式绕组定子车用驱动电机如普锐斯(Prius)搭载的丰田混合动力系统(Toyota Hybrid System, THS)驱动电机,其从第一代到第四代均采用48槽8极分布式绕组驱动电机,第四代THS驱动电机最高工作转速由第三代的13500r/min提升到17000r/min,通过不断提高电机的转速,实现功率密度的不断提升。此外,第四代THS驱动电机与前三代不同的是采用扁线绕组,而非圆线绕组,即用几根粗的矩形导线取代了多根细的圆形导线,如图1-36所示。采用扁线绕组后该电机的体积功率密度由4.8kW/L提高到了5.7kW/L。

图1-36 丰田混合动力系统驱动电机
根据由工业和信息化部装备工业一司指导,中国汽车工程学会牵头组织编制的《节能与新能源汽车技术路线图2.0》,到2025年乘用车驱动电机的功率密度要达到5kW/kg,2030年达到6kW/kg,2035年达到7kW/kg。随着驱动电机功率密度要求越来越高,采用扁线电机已经成为实现这一技术目标的产业共识,下面我们来对比一下圆线绕组与扁线绕组的优缺点:
①圆线绕组。圆线绕组一般需要用特定尺寸的绕线模具绕制,在绕制过程中可以根据不同的需要来调节线圈的匝数,加工工艺简单。绕制完成以后,需要先在槽内放入绝缘纸,然后通过人工或者机器嵌线的方式嵌入定子铁心的槽内,如果是双层绕组,则需要另外放入层间绝缘纸。定子嵌线完后,还需要进行绝缘处理,即通常所说的绕组浸漆以及烘干等过程。此外,圆线绕组属于柔性设计,可以根据一套设计方案,扩展出一系列的电机产品。分布式圆线绕组的不足之处主要在于端部尺寸一般较大,用铜量较多,发热严重。另外,圆线绕组的槽满率还受到槽型尺寸的限制,如果设计不合理,会使得槽满率较低,严重影响电机的温升。
②扁线绕组。与圆线绕组不同,扁线绕组是一种硬性绕组,扁线绕组嵌线前形状已经成型,而且不会轻易变形,所以扁线绕组的端部可以做到规则且短,既节省了端部的用铜量又减小了电阻,同时规则的排列又有利于端部绕组的散热。成型绕组在槽内接触紧密,和铁心接触良好,能够充分进行散热。另外,由于接触面积大,可以使得槽满率做得很高,充分利用了槽内部的空间,所以其直流电阻相对要小很多,铜损耗要比圆线绕组小,效率更高,电磁噪声更低。故相同功率下,扁线电机体积更小、用材更少、成本更低。扁线绕组的主要不足在于线径较大,高速时由于集肤效应电机温升增大,效率有所下降。扁线绕组在放入槽内之前要先进行成型,不同线型成型需要不同的特定模具,一般要通过绝缘处理、成型、扭转、焊接等多道工艺过程,工艺相对复杂,图1-37所示为扁线绕组的制造工艺过程。此外,扁线绕组对铜线材料、制造设备的要求也比圆线绕组高。

图1-37 扁线绕组制造工艺过程
(2)转子 三相交流永磁同步电机的转子主要由转子铁心、永磁体、转轴、轴承、转子支架等结构组成。与普通异步电机不同的是,永磁同步电机的转子上安装有永磁体磁极,永磁体在转子中的安放位置有多种形式。图1-38为内置式三相交流永磁同步电机的转子结构示意图。

图1-38 内置式三相交流永磁同步电机的转子结构
由于三相交流永磁同步电机目前基本都采用逆变器电源驱动,而产生正弦波的变频器输出都含有一定的高频谐波,若用整体钢材会产生涡流损耗,因此三相交流永磁同步电机的转子铁心与定子铁心一样,仍需用硅钢片叠压而成。
根据永磁体在转子上的位置进行划分,永磁同步电机的转子主要有表贴式(SPM)和内置式(IPM)两种结构。表贴式永磁转子结构又分为外表贴式(表面凸出式)和内表贴式(表面嵌入式)两种类型,如图1-39所示。

图1-39 表贴式永磁转子结构图
2.三相交流永磁同步电机的工作原理
三相交流永磁同步电机的驱动电路如图1-40所示,其定子绕组产生旋转磁场的机理与异步电机是相同的,其转子通过永磁体产生磁场,两个磁场相互作用产生转矩。定子绕组产生的旋转磁场,可看作是一对旋转磁极,吸引转子的磁极随其一起旋转。三相交流永磁同步电机带负载时,气隙磁场是永磁体磁动势和电枢磁动势共同建立的,电枢磁动势对气隙磁场有影响,电枢磁动势的基波对气隙磁场的影响称为电枢反应。
三相交流永磁同步电机的工作原理如图1-41所示,图中θ为功率角,电机的转子是一个永磁体,N、S极沿圆周方向交替排列,定子可以看成是一个以速度n0旋转的磁场。电机运行时,定子存在旋转磁动势,转子像磁针在旋转磁场中旋转一样,随着定子的旋转磁场同步旋转。

图1-40 三相交流永磁同步电机的驱动电路图

图1-41 三相交流永磁同步电机工作原理示意图
同步电机转速n(r/min)可表示为

式中 fs——电源频率,单位为Hz;
pn——电机极对数。
永磁同步电机的定子是三相对称绕组,三相正弦波电压在定子三相绕组中产生对称三相正弦波电流,并在气隙中产生旋转磁场。旋转磁场与已充磁的磁极作用,带动转子与旋转磁场同步旋转并力图使定、转子磁场轴线对齐。当外加负载转矩以后,转子磁场轴线将落后定子磁场轴线一个功率角,负载越大,功率角也越大,直到一个极限角度,电机停止。由此可见,同步电机在运行时,转速必须与频率严格成比例变化,否则会失步停转。所以,它的转速与旋转磁场同步,其静态误差为零。负载扰动只是引起功率角变化,而不引起转速变化,响应时间是实时的。
3.永磁电机位置传感器
位置传感器是永磁电机重要的组成部分之一,它用于检测转子磁极的位置,在永磁无刷直流电机中为功率开关电路提供正确的换相信息,在永磁同步电机中为电机控制器提供转子转速及位置信号,电机控制器根据此信号改变三相交流电的相位、频率和幅值,控制电机的转向、转速和功率。目前在永磁无刷直流电机上使用的位置传感器主要有电磁感应式位置传感器、光电式位置传感器、磁敏式位置传感器,永磁同步电机主要使用旋转变压器式位置传感器和磁编码器式位置传感器。
(1)电磁感应式位置传感器 电磁感应式位置传感器是利用电磁感应来实现相对位置测量的传感器。电磁感应式位置传感器有开口变压器式、铁磁谐振电路式和接近开关式。目前主要采用的是开口变压器式,其结构如图1-42所示,包括定子和转子两个部分,转子随电机转子旋转。其定子通常由硅钢片叠堆或由高频铁氧体压铸而成,一般有6个极,各极间隔60°。其中3个极绕上一次绕组,并且相互串联后通以高频电流(几千赫兹到几万赫兹);另外3个极分别绕上二次绕组WA、WB、WC,它们之间分别相隔120°。转子是一个用非导磁材料做成的圆柱体,在它上面镶上一块120°的扇形导磁材料,如图1-42中涂黑的扇形片所示。以图1-42所示位置为例,当跟踪转子位置时,一次绕组所产生的高频磁通通过传感器转子上导磁材料耦合到绕组WB上,在绕组WB上产生感应电压UB,而在另外两相二次绕组WA、WC上,由于无耦合回路同一次绕组相连,其感应电压UA、UC基本上为零。随着电机转子的转动,传感器转子上的导磁扇形片也随之旋转,逐渐离开绕组WB而向绕组WC靠近(假设为逆时针旋转),从而使二次电压UB下降,UC上升。这样,随着电机转子运动,传感器定子二次绕组上依次感应出交变的电压UB、UC、UA,据此即可确定电机转子位置。

图1-42 电磁感应式位置传感器组成结构
这种电磁感应式位置传感器具有输出信号大、工作可靠、寿命长、对环境要求不高、适应性强、结构简单等优点;缺点是信噪比较低、体积较大,其输出为交流波形,一般需要整流、滤波后方可使用。
(2)光电式位置传感器 光电式位置传感器是基于光电效应制成的,由跟随电机转子一起旋转的遮光板和固定不动的光源(发光二极管,即LED)及光电晶体管等部件所组成,如图1-43所示。

图1-43 光电式位置传感器结构图
图1-43中,发光二极管作为光源,固定在一块不动的板上,光电晶体管作为接收方。遮光板Z开有120°电角度左右的缝隙,且缝隙的数目等于直流无刷电机转子的磁极对数。
当缝隙对着光电晶体管VP1时,光源G射到光电晶体管VP1上,VP1导通。因遮光板挡住了光线,光电晶体管VP2和VP3截止。随着遮光板的旋转,光电晶体管VP1、VP2和VP3依次导通,以此来检测转子磁极位置,控制电机定子三相绕组依次通电,保证直流无刷电机的正常工作。光电式位置传感器性能较稳定,但存在输出信号信噪比较大、使用环境要求较高等不足。
(3)磁敏式位置传感器 磁敏式位置传感器是某些电参数按一定规律随周围磁场变化的半导体敏感元件,又称为磁敏元件。磁敏元件的主要工作原理是电流的磁效应,主要包括霍尔效应和磁阻效应,霍尔效应元件有霍尔元件或霍尔集成电路(霍尔芯片),磁阻效应元件有磁敏电阻器、磁敏二极管、磁敏晶体管等。
霍尔元件是利用霍尔效应产生电压输出的元件,霍尔效应于1879年由美国物理学家霍尔(E. H. Hall)在探索电机原理时发现,如图1-44a所示。如果对位于磁场(B)中的长方体霍尔元件施加一个垂直于磁场方向的电场,形成电流(I),那么则在既与磁场垂直又和所施加电流方向垂直的方向上会产生另一个电压(UH),该电压即为霍尔电压。利用霍尔电压与垂直磁场的对应关系,可以将霍尔元件制成霍尔式位置传感器,如图1-44b所示,信号轮随电机转子旋转,改变作用于霍尔元件的磁场强度,从而在霍尔元件上感应出交变的霍尔电压信号。由于霍尔信号电压较低,应用时需要外接放大电路进行信号放大。随着半导体集成技术的发展,通常将霍尔元件与霍尔电子放大电路集成在一块芯片上,组成霍尔集成电路元件。除了电机外,霍尔式传感器在车上应用广泛,包括轮速传感器、曲轴及凸轮轴位置传感器、加速踏板位置传感器、节气门位置传感器等。

图1-44 霍尔效应与霍尔式位置传感器
磁阻效应是指元件的电阻值随磁感应强度变化的现象。根据磁阻效应制成的传感器称为磁敏电阻。它可以制成任意形状的两端子元件,也可以制成多端子元件,这有利于电路设计。
另外应当注意,霍尔元件输出电压的极性随磁场方向的变化而变化,磁敏电阻的阻值变化仅与磁感应强度的绝对值有关,与磁场方向无关。
(4)旋转变压器式位置传感器 车用驱动电机主要为永磁同步电机,旋转变压器式位置传感器可检测电机转子转速和磁极位置,且其结构简单可靠,是电动汽车驱动电机位置传感器的首选。
旋转变压器就是一种基于电磁感应原理的可旋转的变压器。旋转变压器的一次绕组和二次绕组分别放置在转子铁心和定子铁心上,如图1-45所示。给转子绕组(一次绕组)输入一个固定频率的交变电压信号,定子绕组(二次绕组)上会感应出一个同相位同频率的交变电压信号,当转子发生旋转时,定子上的二次绕组感应交变电压信号会发生幅值和相位的变化,该变化与转子所处的位置成一定函数关系,根据这个信号变化,可以解算出转子位置。图1-46~图1-50分别为转子在不同位置时,旋转变压器一、二次绕组信号对比。

图1-45 旋转变压器结构示意图

图1-46 旋转变压器一、二次绕组信号对比(转子角度0°)

图1-47 旋转变压器一、二次绕组信号对比(转子角度45°)

图1-48 旋转变压器一、二次绕组信号对比(转子角度90°)

图1-49 旋转变压器一、二次绕组信号对比(转子角度135°)

图1-50 旋转变压器一、二次绕组信号对比(转子角度180°)
旋转变压器按信号变化的极对数可分为单极旋转变压器和多极旋转变压器。单极旋转变压器输出电信号周期与转子旋转周期一致,精度一般在5′~15′,多极旋转变压器输出电信号变化周期数是转子周期的极数倍,根据极对数的多少,其精度一般为几角分(′)、数十角秒(″),极对数越多精度越高。
旋转变压器可分为有刷旋转变压器和无刷旋转变压器。有刷旋转变压器的转子绕组电压信号通过集电环和电刷引入。由于存在带电滑动接触,可靠性差、寿命短,基本上不采用。无刷旋转变压器包括环形变压器式无刷旋转变压器和磁阻式旋转变压器等。环形变压器式无刷旋转变压器中有两套绕组,一套绕组同常规旋转变压器一样;另一套是定、转子上分别同心放置的环形变压器一、二次绕组,两套绕组的转子侧互相电气连接,常规旋转变压器转子绕组的电压通过环形变压器的定子绕组输入。磁阻式旋转变压器是根据定、转子之间的气隙磁阻变化,实现输出信号变化的旋转变压器,由于这种旋转变压器可靠性非常好,又具有足够的精度,所以在电动汽车驱动电机中得到了广泛的应用,其结构如图1-51所示。
常用的磁阻式旋转变压器为正余弦旋转变压器,其有3个绕组,分别为励磁绕组、正弦绕组和余弦绕组。3个绕组均固定在定子侧,正弦和余弦绕组相位差为90°,3个绕组共6根线通过焊接方式连接到旋转变压器插接器接线柱。转子凸极呈花瓣状,利用转子凸极旋转产生的交变气隙磁场,正弦绕组和余弦绕组分别感应出幅值随转子旋转角变化的正弦与余弦信号。图1-52为其简单示意图,图中定子开有10个槽,转子凸极数为3(对应的极对数为3)。当旋转变压器的转子随电机一起转动时,其定、转子气隙磁阻会发生变化,气隙磁场随之变化,从而导致励磁绕组与信号绕组之间互感的变化,最终引起信号输出绕组感应电动势变化,两相信号绕组输出的幅值随转角变化,相差90°电角度。通过专门的旋变解码电路对两相输出信号进行处理,可以得到以电量形式表达的位置信号。

图1-51 磁阻式旋转变压器结构

图1-52 磁阻式旋转变压器示意图
假设励磁绕组的输入电压为

式中 f——励磁频率,单位为Hz;
ω——励磁信号角速度,单位为rad/s;
E1m——励磁电压幅值,单位为V。
则余弦、正弦输出信号电压分别为

式中 E2m、E3m——输出信号电压最大幅值,单位为V;
α——转子旋转角度,单位为rad。
根据上述公式,当给磁阻式旋转变压器励磁绕组输入一个交变信号电压时,余弦、正弦输出信号电压幅值随转子旋转角度变化,余弦信号电压的拟合信号与转子旋转角度成余弦关系,正弦信号电压的拟合信号与转子旋转角度成正弦关系,如图1-53所示。控制器根据正弦、余弦输出信号可精确测算出转子旋转角度(即驱动电机转子位置)。

图1-53 励磁、正弦和余弦信号电压与转子旋转角度关系
由于新能源汽车安装空间及整车总重的限制,要求驱动电机及电机控制器结构紧凑、质量小。在驱动系统的机械结构设计中,多选用扁平结构类的旋转变压器,可以减小轴向尺寸。而且旋转变压器多采用无机壳、无转轴的分离式结构,分成定子与转子两大件,定、转子分别直接固定在驱动电机的定子和转子上。
目前国内主要的旋转变压器供应商有上海赢双、常州华旋等,国外供应商主要有日本多摩川、日本美蓓亚等,国内外同类旋转变压器性能及技术参数相差不大。表1-2为国内某款典型4对极旋转变压器的主要参数。
表1-2 某款典型4对极旋转变压器主要参数

(5)磁编码器式位置传感器 编码器式位置传感器有光电编码器和磁编码器,光电编码器是利用光电元件检测编码盘信号的传感器,磁编码器是利用磁性原理检测编码盘信号的传感器。
光电编码器由光源、光电码盘、光敏元件、输出电路等组成,如图1-54a所示。光电码盘是由玻璃、金属、塑料制成的一定直径的圆盘,上面等分地开通若干个长方形孔(刻线)。光源和光敏元件分别位于光电码盘的两侧,光电码盘与电机同轴,电机旋转时,光电码盘与电机同速旋转,光电码盘控制光源照射或不照射在光敏元件上,光敏元件输出脉冲信号,信号经过输出电路处理后输出有正弦波、方波(TTL、HTL)等多种不同形式信号,其中TTL为长线差分驱动(对称A、A-;B、B-;Z、Z-),编码器的信号接收设备接口应与编码器对应。
以相对位置方波光电编码器为例,输出通道A和通道B两组信号,相位差90°(1/4个周期),如图1-54b所示。当B相和A相先是都读到高电平(1,1),之后B读到高电平、A读到低电平(1,0),则为顺时针旋转,当B相和A相先是都读到低电平(0,0),之后B读到高电平、A读到低电平(1,0),则为逆时针旋转。除通道A、通道B以外,还会设置一个额外的通道Z,代表零位参考位。

图1-54 光电编码器结构与工作原理
光电编码器常见于一些高性能的永磁无刷直流电机中,获取永磁无刷直流电机逻辑换相所需要的转子磁极位置信息。但由于光电编码器抗恶劣环境的能力较差,所以极少在车用驱动电机中使用,这里主要介绍车用驱动电机常采用的磁编码器式位置传感器。
磁编码器式位置传感器的工作原理是利用磁敏元件检测磁场变化,并以电信号形式输出。将充以N、S磁性的永磁体安装在旋转运动的物体中,产生随转动变化的磁场,置于变化磁场中的磁敏元件根据磁场变化,输出相应变化的电信号,通过信号处理电路,对变化量进行放大、处理,最终输出和角度有关的模拟信号或脉冲信号,达到位置检测的目的。
磁编码器通过磁敏元件检测转子磁极位置,与旋转变压器相此,其体积较小;与光电编码器相比,它的抗冲击性强,对安装精度也无特殊要求。磁编码器式位置传感器分辨率靠细分电路实现,而不是靠极对数。和旋转变压器一样,提高其精度也要采用多对极,但这会导致其体积加大,信号处理电路变复杂,反应时间加长,电机旋转速度受到限制。
按照信号采集器件和运行原理不同,磁编码器主要分为磁阻式和霍尔式,分别通过磁阻元件和霍尔元件检测位置,体积较小且方便安装。目前常用的磁阻元件有各向异性磁阻传感器(AMR)、巨磁阻传感器(GMR)和隧道磁阻传感器(TMR)等。磁阻式是基于磁阻效应,磁感应强度工作范围为10-4~10-1T;霍尔式是基于霍尔效应,磁感应强度工作范围为10-6~1T。
磁编码器按照磁极数量可分为单对极磁编码器和多对极磁编码器。
1)单对极磁编码器:采用单对极的磁鼓,难以实现较高的精度。其构成形式如图1-55a所示,一般进行轴向充磁,主磁场在轴向。此时,磁敏元件轴向放置。
2)多对极磁编码器:采用多对极的编码器,以提高精度。多对极磁编码器磁鼓形式如图1-55b所示,一般进行径向充磁,形成径向磁场。因此,磁敏元件置于磁鼓的径向侧。

图1-55 磁编码器的磁鼓形式
磁编码器主要由磁鼓、磁敏元件和信号处理电路组成,工作原理如图1-56所示。磁鼓为等距均匀旋转分布的小磁极,一般固定在电机的转轴上,随电机一起转动。转动时,磁鼓上磁极的磁场也随之转动。固定在电机定子上、置于这个变化磁场中的磁敏元件,根据磁阻效应或霍尔效应将变化磁场信号转变为相应变化的电气信号、变化的电阻值或电压值。经过信号处理电路,模拟电压信号转变为控制器可识别的数字磁感应信号,通过串行外设接口(SPI)、增量式(ABZ)或者脉冲宽度调制(PWM)方式输出,经软硬件处理后便能得到准确的转子位置,用于电机控制。

图1-56 磁编码器工作原理
磁鼓充磁的目的是使磁鼓的磁极被磁化,当磁鼓随着电机旋转时,磁鼓能产生周期变化的空间磁场,作用于磁阻上,实现编码功能。磁鼓材料的各向一致性和稳定性、充磁工艺方法、磁极分布的均匀性、形成气隙磁场的正弦性、各磁极磁场强度及波形的一致性及稳定性,是影响磁编码器结构和输出信号质量的重要因素。
磁编码器正在不断地向微型、高速、高精度和集成化方向发展。目前,国外知名磁编码器供应商的产品质量水平较高,其分辨率可以达到1024p/r(表示1个机械周期有1024个脉冲);通过软件补偿与电路细分等处理后,其分辨率最高可以达到64000p/r,主要供应商有日本雅马哈(YAMAHA)、英国雷尼绍(Renishaw)、德国的SENTRON(西门子旗下产品)、美国安华高(Avago)、北极星(NorthStar)。我国供应商如长春第一光学有限公司、深圳市华夏磁电子技术开发有限公司也推出了相应的磁编码器产品,在国内占有一定份额。
图1-57所示为艾迈斯(AMS)公司的AS5147P磁编码器的原理框图,该磁编码器支持独立的SPI、ABZ、UVW及PWM信号输出,其中SPI可用作读取初始位置、故障信息获取和转速校验。AS5147P具备动态角度误差补偿(DAEC),从硬件角度解决了系统传输延时问题;其测量精度高,最小可以测量0.02°电角度变化;使用温度范围满足-40~125℃车规级要求;最高转速可达到14500r/min,满足大多数电机使用工况;并且自带诊断功能,能够诊断磁场状态,并反馈响应故障信息,避免位置信息错误,同时能够监控寄存器状态,避免溢出故障。AS5147P是一个双管芯(die)的芯片,芯片自带冗余监测机制,满足功能安全开发要求。

图1-57 AS5147P磁编码器原理框图
磁阻式编码器、霍尔式编码器与光电编码器的对比见表1-3。
表1-3 磁阻式编码器、霍尔式编码器与光电编码器对比
