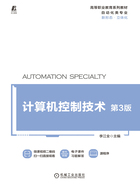
1.3 计算机控制系统的典型结构
工业控制计算机系统与所控制的生产过程的复杂程度密切相关,不同的控制对象和不同的控制要求,有不同的控制方案。下面从应用特点、控制目的出发介绍几种典型的结构。
1.3.1 数据采集系统
数据采集系统(Data Acquisition System, DAS)如图1-8所示,系统对生产过程或控制对象的大量参数做巡回检测、处理、分析、记录以及参数的超限报警。通过对大量参数的积累和实时分析,可以实现对生产过程进行各种趋势分析。这是计算机应用于工业生产过程最早和最简单的一类系统。

图1-8 数据采集系统
被控生产过程的参数经测量变送器、过程输入通道,送入计算机,由计算机对来自现场的数据进行分析和处理后,根据一定的控制规律或管理方法进行计算,然后通过显示器或打印机输出操作指导信息供操作人员参考。所以数据采集系统又称为操作指导控制系统。
数据采集系统的输出不直接作用于生产过程的执行机构,不直接影响生产过程的进行。它的输出只作用于有关的外部设备和人机接口,为操作人员的分析、判断提供信息的显示。
这是一种开环控制系统,仅对生产过程进行监视,不对生产过程进行自动控制。
1.3.2 直接数字控制系统
直接数字控制(Direct Digital Control, DDC)系统如图1-9所示,计算机通过过程输入通道对控制对象的多个参数做巡回检测,根据测得的参数按照一定的控制算法运算后获得控制信号量,经过过程输出通道作用到执行机构,从而实现对被控参数的自动调节,使被控参数稳定在设定值上。
直接数字控制系统与模拟调节系统有很大的相似性,直接数字控制系统以计算机取代多台模拟调节器的功能。由于计算机具有很强的计算和逻辑功能,因此可以实现对各种复杂规律的控制。

图1-9 直接数字控制系统
DDC系统是闭环控制系统。它对被控制变量和其他参数进行巡回检测,与给定值比较后求得偏差,然后按事先规定的控制策略,如比例、积分、微分规律进行控制运算,最后发出控制信号,通过接口直接操纵执行机构对被控制对象进行控制。这种控制方式在工业生产中应用最普遍。
1.3.3 监督控制系统
在DDC系统中是用计算机代替模拟调节器进行控制,对生产过程产生直接影响的被控参数给定值是预先设定的,并存入计算机的内存中,这个给定值不能根据生产工艺信息的变化及时修改,故DDC系统无法使生产过程处于最优工况。
计算机监督控制(Supervisory Computer Control, SCC)系统如图1-10所示,它是计算机和调节器的混合系统,是对DDC系统的改进。它通常采用两级控制形式。

图1-10 计算机监督控制系统
所谓监督控制,指的是根据原始的生产工艺数据和现场采集到的生产工况信息,一方面按照描述被控过程的数字模型和某种最优目标函数,计算出被控过程的最优给定值,输出给下一级DDC系统或模拟调节器;另一方面对生产状况进行分析,做出故障的诊断与预报。所以SCC系统并不直接控制执行机构,而是给出下一级的最优给定值,由它们去控制执行机构。
当下一级采用模拟调节器时,SCC中的计算机对各物理量进行巡回检测,并按一定的数学模型对生产过程进行分析计算后得出控制对象各参数最优的给定值,然后送调节器,使工况保持在最优状态。当SCC计算机出现故障时,可由模拟调节器独立完成操作。
当下一级采用DDC系统时,其计算机(称为下位机)完成前面所述的直接数字控制功能,SCC中的计算机(称为上位机)则完成高一级的最优化分析与计算,给出最优化的给定值,送给DDC级执行过程控制。
1.3.4 集散控制系统
集散控制系统(Distributed Control System, DCS)又称为分布式控制系统,其基本思想是集中操作管理,分散控制。
集散控制系统本质上是一种基于计算机网络的分层式的计算机监控系统,它的体系结构特点是层次化,把不同层次的多种监测、控制和管理功能有机地、层次分明地组织起来,使系统的性能大为提高。
集散控制系统适用于大型、复杂的控制过程,在我国许多大型石油化工企业就是依赖各种形式的集散控制系统保证它们的生产高质量地连续不断进行。
一般把集散控制系统分成3个层次,如图1-11所示,每一层有一台或多台计算机,同一层次的计算机以及不同层次的计算机都通过网络进行通信,相互协调,构成一个严密的整体。

图1-11 集散控制系统
在计算机控制应用于工业过程控制的初期,因为计算机价格高,所以采用的是集中控制方式,以充分利用计算机。但这种控制方式由于任务过分集中,一旦计算机出现故障,就要影响整个系统。
DCS由若干台微机分别承担任务,从而代替了集中控制的方式,由于分散了控制,也就分散了危险,因此系统的可靠性大大提高;并且DCS是积木式结构,构成灵活,易于扩展;采用液晶显示技术和智能操作台,操作、监视方便;采用数据通信技术,处理信息量大;与计算机集中控制方式相比,电缆和敷缆成本较低,便于施工。
1.3.5 现场总线控制系统
计算机技术、通信技术和计算机网络技术的发展,推动着工业自动化系统体系结构的变革,模拟和数字混合的集散控制系统逐渐发展为全数字系统,由此产生了工业控制系统用的现场总线。
现场总线控制系统(Fieldbus Control System, FCS)是继DCS之后兴起的新一代工业控制系统。它将当今网络通信与管理的概念引入工业控制领域,是一个开放式的互联式网络,既可以与同层网络互联,也可以与不同层的网络互联;在现场设备中,以微处理器为核心的现场智能设备可方便地进行设备互联、互操作,其结构如图1-12所示。

图1-12 现场总线控制系统
从控制的角度看,FCS有两个显著特点:
一是信号传输实现了全数字化。FCS把通信线一直延伸到生产现场中的生产设备,构成用于现场设备和现场仪表互连的现场通信网络。全数字化避免了传统系统中模拟信号传输过程中难以避免的信号衰减、精度下降和容易受到干扰等缺点,提高了信号传输的精度和可靠性。
二是实现了控制的彻底分散。把控制功能分散到现场设备和仪表中,使现场设备和仪表成了具有综合功能的智能设备和智能仪表,它们经过统一组态,可以构成各种所需的控制系统,从而实现彻底的分散控制。