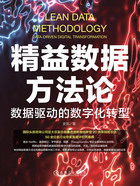
2.2 全面认识精益思想
2.2.1 精益思想的产生
二战结束后不久,统治汽车工业的生产方式是以美国福特汽车公司为代表的少品种、大批量的流水线生产方式。在当时,这种生产方式代表了先进的管理思想与方法,通过专用设备实现大批量生产是降低成本、提高生产率的主要方式。
与处于绝对优势的美国汽车工业相比,日本的汽车工业则处于相对初级的阶段,丰田汽车公司从成立到1950年的十几年间,总产量甚至不及福特汽车公司1950年一天的产量。汽车工业是日本经济倍增计划中的重点发展产业,日本派出了大量人员前往美国考察。
丰田汽车公司的考察人员在参观美国的几大汽车厂之后发现,通过大批量生产来降低成本的方式仍有进一步改进的空间,他们认为在日本进行大批量、少品种的生产是不可取的,应考虑一种更适应日本市场需求的生产组织策略。
以丰田汽车公司的大野耐一等人为代表的精益生产的创始者们,在不断探索之后,终于找到了一套适合日本市场的、新的汽车生产方式:及时制生产、全面质量管理、并行工程、充分协作的团队工作方式和集成的供应链关系管理,逐步创立了独特的多品种、小批量、高质量和低消耗的精益生产方法。1973年的石油危机使日本的汽车工业在世界舞台上闪亮登场。由于市场环境发生变化,大批量生产方式的弱点日趋明显,而丰田汽车公司的业绩却开始上升,与其他汽车制造企业的距离越来越大,精益生产方式开始为世人瞩目。
2.2.2 精益思想的2个核心要义
精益思想有2个核心要义:创造价值,消除浪费。
精益思想提倡以较少的资源投入,包括较少的人力、较少的设备、较短的时间和较小的场地,创造出尽可能多的客户需要的价值。
精确地定义业务价值是精益思想的第一步,如果不能精准地识别和定义客户需要的价值,就会带来很多浪费。
紧接着,要使保留下来的、创造价值的各个步骤流动起来。比如,使需要若干天才能办完的订货手续在几小时内办完,从而快速、持续地给用户提供价值。
随后就要及时跟上不断变化的客户需求,建立产品能力,在用户真正需要的时候能及时设计、生产和交付满足用户需求的产品,甚至直接按用户告知的实际要求进行生产,让用户需求拉动产品设计和生产,而不是把用户不想要的产品强推给用户,以减少双方的浪费。
精益思想包含一个目标,两个支柱和一系列基础实践。一个目标:构建高质量、低成本和快速响应的生产体系。达成这个目标,企业需要构建两个支柱能力:准时化和自动化。这三者的基础是一系列实践,包括均衡生产、标准化作业和看板拉动。如图2-3所示。

图2-3 精益思想的主要构成
2.2.3 精益思想的5个原则
精益思想认为,企业产品或服务的价值必须且只能由最终用户来定义,产品也只有满足特定用户的需求才有存在的意义。精益思想重新定义了价值的原则,同传统的高效率大量制造既定产品向用户推销是不一样的。
精益思想有5个核心原则,这5个原则也是指导企业实施精益思想的关键指引。
1.用户价值
詹姆斯· P.沃麦克和丹尼尔· T.琼斯在《精益思想》一书中提出的第一个核心原则就是要定义价值,要以客户价值为核心,而不是以生产者为核心。
精益思想认为,价值是在公司提供的产品中顾客愿意付费购买的部分。
生产一个产品之前,先要定义该产品的用户,明确产品能为这些用户带来什么价值。即使一个产品的功能再多,如果不能帮用户解决问题,那么该产品也是没有商业价值的。反之,哪怕这个产品只能解决一个很小的用户问题,它也是有价值的。
“用户不是要买钻头,而是要买一个洞。”如果生产者不能从根本上理解价值的内涵,一味关注那些用户本质上并不关心的问题,而忽略真正的用户需求,产品的设计就会产生偏差。
识别和定义用户价值是一个很复杂的事情,因为很多时候用户自己也不清楚自己的问题在哪里。在这种情况下,发现价值的工作和责任是提供产品和服务的企业要承担的。
精益思想进一步指出,价值是由用户定义的,但是产品的生产者要站在用户的立场上去思考,产品给用户提供的真正有用的东西是什么,能够为用户解决什么问题。
2.识别价值流
价值流是一系列活动的集合,包括从用户的原始需求到产品实现这整个过程中的增值部分。比如,概念设计、产品设计、工艺设计、投入生产的技术过程,订单处理、计划、送货的信息过程,从原材料到产品的物质转换过程,以及产品全生命周期的支持和服务过程等。
精益思想识别价值流的核心是找到这些过程中真正增值的活动,识别并消除不增值的活动。
价值流通过可视化的方式让团队清晰地了解生产的全链路,并从中识别存在浪费和可以优化的地方。价值流对企业有着非常重要的作用,主要体现在如下4个方面。
● 能够优化生产过程,减少浪费,节约成本。
● 能够让团队清晰地认识到问题所在,从而更好地持续改进。
● 使团队统一价值认知,促进沟通和协同,达成最终一致目标。
● 全链路畅通的价值流是自动化的基础。
识别价值流就是要发现浪费和消除浪费,创造效率最高、流动最快的链路。通过价值流的绘制,我们可以把一个产品的构建过程分解成可视化的步骤,从而让团队统一对产品的认知,更好地沟通和协作,并且有效识别整个过程中有价值的部分,以及识别浪费,优化生产流程。
价值流通常以价值流图的方式呈现,价值流图包括3部分——信息流、材料流和延迟时间,如图2-4所示。

图2-4 价值流示例
价值流图可以量化描述生产过程中每一个环节的处理时间、延迟时间、等待时间以及材料的消耗情况。有了这些量化的指标,业务人员能够更方便地发现浪费,从而优化改进流程。
价值流并不局限于企业内部,大多数价值流向前延伸到供应商,向后延伸到客户,从而按照最终用户的观点全面考察价值流,寻找全过程的全局优化。
3.流动
精益思想要求创造价值的各个活动(步骤)能够“流动”起来,强调不间断地快速流动。
在传统生产观念里,精细分工和大量生产能提高效率,精益思想认为大批量的生产往往意味着等待和浪费,往往阻断了高速流动的价值流,如部门间交接和转移时的等待时间、大批量生产时机床旁边堆积的在制品等。
精益思想要求“所有的人都必须和部门化的、批量生产的思想做斗争”,用持续改进、单件流等方法创造价值,使其持续流动。
让价值高速流动需要具备以下3个条件。
● 消灭缺陷。缺陷造成的废品和返工都会造成价值流的中断。持续的流动要求每个过程和每个产品都是正确的。
● 良好的环境和完好的设备是流动的保证,为此企业要做到5S,即整理(Seiri)、整顿(Seiton)、清扫(Seiso)、清洁(Seiketsu)和素养(Shitsuke)。此外,全面生产性维护(Total Productive Maintenance,TPM)也是价值流动的前提条件之一。
● 系统地进行流程设计和能力规划,避免因不当设计产生阻塞。
4.拉动
拉动就是不主动推送服务给客户,而是将获取产品和服务的权利交给客户,按客户的需求生产,使最终用户能够在合适的时间得到需要的东西。
按照拉动原则实施生产流程以后,用户就像在超市的货架上选取所需产品一样,能真正满足自身需求,而不是让超市强行推荐产品。拉动原则将产品的生产和用户的需求直接对应,避免企业过早、过量投入,减少了大量的库存和在制品,大大压缩了提前期。拉动原则更深远的意义在于,用户一旦需要,企业就能立即设计、计划和制造,交付用户真正需要的产品。这种能力让企业最终可以抛开预测,直接按用户的实际需要进行生产。
5.尽善尽美
按照上述4个原则对产品全生命周期进行不断改进,能显著提高价值流动速度,企业可以有效地用价值流分析方法进一步找出隐藏的浪费环节,这样循环操作,最终使生产过程趋于尽善尽美。
精益管理的目标就是:通过尽善尽美的价值创造过程(包括设计、制造和对产品或服务整个生命周期的支持),为用户提供尽善尽美的价值。
尽善尽美是一种理想状态,但持续追求尽善尽美,能够打造一个用户满意、无差错生产、永远充满活力、不断进步的企业。
回看企业利用数据的六大挑战,其中很重要的是企业缺少价值场景、无法识别用户价值。而现在很多企业面临的数据质量不高、数据孤岛的问题就是低质量和过度的数据生产导致的,这也产生了极大的浪费。当我们结合精益思想来观察企业的数据生产时,发现众多数据问题都可以迎刃而解,这就是精益数据方法的主要目标之一。
除了精益思想外,精益数据方法同时借鉴和吸收了Cynefin框架、设计思维和敏捷思想的理论体系。