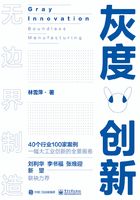
/第一节/微笑曲线是一个典型的误解
宏碁公司创始人施正荣在1992 年为“再造宏碁”提出了微笑曲线,一直被人们广泛使用(见图1-1)。微笑曲线表明,生产过程两端的增加值较高,而中间的增加值较低。
这是一个对电子行业全球价值链特征的描述,即模块化。例如,半导体行业可以分为5个模块,分别是研发和设计(熟练劳动密集型)、零部件生产(资本密集型)、组装(非熟练劳动密集型)、测试(资本密集型)和营销(熟练劳动密集型)[1]。参与者也可以被简单地分为3类:龙头企业和一级供应商、合同制造商(也称为电子制造服务商,包括代工厂、物流厂商等)、零部件供应商。在20世纪60年代到70年代,电子制造服务中的组装工序、测试工序被率先转移到低工资的国家,全球化的分工由此产生。而微笑曲线的下部自此成为“低利润制造”的标志性区域段。

图1-1 微笑曲线
(资料来源:UNIDO绘制)
然而,这其中存在着一个巨大的假设,假设认为代工都是处于价值链的最低端,而且是低利润的。其实,微笑曲线一般是针对早期代工制造被分离的供应链形式而言的。一般讨论的所谓“低价值”的场景往往都是在第三世界国家或者发展中国家出现的。实际上,许多制造企业并没有完全分离供应链,而只是选择性地将一部分制造拿出去外包,核心的制造能力还是牢牢把握在企业自己手中的,且这部分核心业务往往利润丰厚。全球化的制造外包使工业发达国家的企业可以到人工成本低的国家去办厂,从而出现了采用廉价劳动力的代工厂,但这只是其中的一种模式。在欧美一些国家的本土,代工厂获得的相对利益值其实并不算低。制造企业做得好,有的时候并不是因为其基础研究做得好,而是因为在制造技术方面有所突破。
对品牌商而言,拥有先进制造技术的代工制造企业也能带来产品的增值。例如,当年苹果公司并不掌握解决屏幕问题的相关技术,在意识到富士康公司的制造技术可以胜任苹果公司产品的生产之后,就将富士康公司的制造方法一并列入开发计划中,并将富士康公司的人员也集成到研发制造团队中。经过10多年的发展,如今富士康公司与以前已大为不同,由于其制造技术价值和人因工程的进化,在精密电子装配行业已有越来越深的积淀。这是一种相互驱动的方式在发挥作用。再例如,发动机关键零部件和子系统供应商德国戴姆勒奔驰旗下的MTU公司,在为通用(GE)公司设计新零部件的时候,凭借制造技术的优势提出采用烧结工艺制备聚晶金刚石刀具的先进方法,而报价甚至比GE原本设想的还要低。这样的制造创新技术无疑能够帮助上游企业更好地发展。
当然,在这其中知识产权的界限也很清楚。例如,日本有不同的企业在供应航空发动机的材料和零部件,基于利益关系,经双方协商,日本供应商会根据发动机主机厂的要求研发相关的零部件、材料等,而且拥有发动机部分相对独立的知识产权。
制造工厂由于在制造方面的优势,使整个价值链的合作变成了合则共赢、散则共伤的关系,谁也离不开谁。制造厂、主机厂和产品设计绑定在一起,利益共享,类似富士康与苹果、MTU与GE的关系。当然,除了富士康,苹果也能找其他代工厂合作,但富士康短期内还是有能力保证可以跟苹果合作共赢的。其实,富士康要打造自己的品牌也很容易,而之所以选择不这样做只是代工厂的一种策略选择,并非因为本身不具备相应的能力。
随着中国制造竞争力的不断提升,拥有核心制造技术的企业正在承揽这种全凭手中金刚钻的“瓷器活儿”。山东豪迈集团的轮胎模具制造能力很强,年产可以达到两万套[2],其拥有的轮胎模具电火花加工工艺可以加工钢质和铝质的轮胎模具花纹;同时该企业还掌握了雕刻工艺和精密铸造工艺,这是全球同行业少有的能够同时熟练掌握三大加工工艺的企业。虽然这家公司凭技术可以服务于全球四五十个轮胎厂,为其提供模具,但是仍然不能任意抬高价格。上游厂商担心被一家企业垄断供应,因此也经常会采用不断找替代厂家进行生产的策略,从而对供货商进行价格把控。
这样的例子不胜枚举。再例如,铝合金车轮制造企业中信戴卡,其整个产线的自动化程度高、压铸能力强,已成为世界著名品牌。该企业在扩大规模以后,很多小的竞争对手已被其远远甩在后面,主机厂也很难去找其他替代厂家。中信戴卡的议价能力可能会有所提高,但还是会因考虑到平衡的问题而不轻易提价。
当前,中国制造正处于升级换代的进程中,许多以代工为主的产业也要往更高端的方向发展。以往在很多外资办的工厂中,设备、技术统统都是外方的,外资工厂中只用中国劳工。但现在,随着越来越多像中信戴卡、万丰轮毂这类工厂的发展,企业逐渐有了自主研发能力,对技术改造和技术升级的需求越来越高。因此,企业与科研院所的结合有了更好的条件。同时,企业也可以通过制造现场的制造改进与工艺提升,刺激源头创新,释放科研院所的能力。这意味着,制造现场的创新价值同样值得关注。