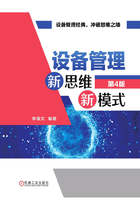
第三节 日本的TPM及其在世界的影响
TPM(Total Productive Maintenance)又称全面生产维护、全员生产保全,是日本前设备管理协会(中岛清一等人)在美国生产维修体制之后,在日本的Nippondenso电器公司试点的基础上,于1970年正式提出的。
20世纪50年代初期,日本基本上是学习美国的设备管理经验。随着日本经济的增长,在设备管理上一方面继续学习其他国家的好经验,另一方面进行了适合日本国情的创造,这就产生了全面生产维护体制。这一体制既有对美国生产维修体制的继承,又有英国综合工程学的思想,还吸收了我国“鞍钢宪法”中提出“台台(设备)有人管,人人有专责”这种吸收工人参加、走群众路线、提倡合理化建议及劳动竞赛的做法。最重要的一点是,日本人身体力行地把全面生产维护体制贯彻到底,产生了突出的效果。
1.TPM给企业带来的效益
为什么TPM在日本乃至全世界都得到承认并不断发展呢?这主要是因为实行TPM可以使企业获得良好的经济效益和广告效应,充分发挥设备的生产潜力,并使企业树立起良好的社会形象。
自从TPM在日本乃至世界各国企业中推行以来,给企业创造了可观的经济效益,同时也增加了企业的无形资产。我国随着改革开放,国内大批企业引进TPM体系,也取得了明显成效。
TPM给企业带来的效益体现在产品成本、质量、生产率、库存周转、安全与环境保护以及职工的劳动情绪等方面,如图1.3-1所示。

图1.3-1 TPM对企业产生的影响
2.全面生产维护的基本概念和特点
TPM可以称为“全员参加的生产维护”或“带有日本特色的美式生产维修”,它是各种现代理论在企业生产中的综合运用。TPM的理论基础包含维修预防、预防维修、系统工程、生产维修、行为科学、维修改善、可靠性工程,以及生态学、可维修性工程、工程经济学、综合工程、后勤工程学等理念和方法。
(1)全面生产维护(TPM)的定义
按照日本工程师学会(JIPE),TPM有如下定义:
1)以最高的设备综合效率为目标。
2)确立以设备全寿命周期为目标的全系统预防维修。
3)对设备的计划、使用、维修等,所有部门都要参加。
4)从企业的最高管理层到第一线职工全体参加。
5)实行动机管理,即通过开展小组的自主活动来推进生产维护。
(2)全面生产维护的特点
日本的全面生产维护与原来的生产维修相比,主要突出一个“全”字。“全”有三方面含义,即全效率、全系统和全员参加。所谓的全效率,是指设备寿命周期费用评价和设备综合效率;全系统是指生产维修的各个侧面均包括在内,如预防维修、维修预防、必要的事后维修和改善维修;全员参加是指TPM维修体制的群众性特征,从公司经理到相关处室,直到全体操作工人都要参加,尤其是要开展操作工人的自主小组活动。
TPM的主要目标落在“全效率”上。“全效率”在于限制和降低六大损失:
1)设备停机时间损失。
2)设置与调整停机损失。
3)闲置、空转与短暂停机损失。
4)速度降低(速度损失)。
5)残、次、废品损失,边角料损失(缺陷损失)。
6)初期产量损失(由安装到稳定生产间隔)。
有了这三个“全”,生产维修得到更好的贯彻执行,能使生产维修的目标得到更有力的保障。这也是日本全面生产维护的独特之处。
随着TPM的不断发展,日本把这一从上到下、全系统参与的设备维修管理体制的目标提到了更高水平,又提出了“停机为零!废品为零!事故为零!”的奋斗目标。
3.全面生产维护的开展过程
推行TPM要从三大要素的实现方面下功夫,这三大要素分别是:
1)提高(操作、工作)技能。
2)改进(工作、精神)面貌。
3)改善(企业、操作)环境。
即使是在日本的企业里,推行这一体制也不是一件容易的事情,需要领导层下定决心,而且要有一套较好的开展程序。全面生产维护大体上分成4个阶段和12个具体步骤,其推进过程可归纳为表1.3-1。
表1 .3-1 TPM的推进过程

4个阶段的主要工作和作用是:
1)准备阶段。引进TPM计划,营造适宜的环境和氛围。这就如同产品的设计阶段。
2)开始阶段。TPM活动的开始仪式,通过广告宣传造出声势。这就相当于下达产品生产任务书。
3)实施、推进阶段。制定目标,落实各项措施,步步深入。这就相当于产品加工、组装过程。
4)巩固阶段。检查评估推行TPM的结果,制定新目标。这就相当于产品检查、产品改进设计过程。
4.设备综合效率
TPM追求的是设备效率最大化,为此设计了设备综合效率指标加以度量。
影响设备综合效率的主要因素是停机损失、速度损失和废品损失。它们分别由时间开动率、性能开动率和合格品率反映出来,故得到下面的设备综合效率公式:
设备综合效率=时间开动率×性能开动率×合格品率

式中,负荷时间为规定的作业时间减去每天的停机时间,即
负荷时间=总工作时间-计划停机时间-非设备因素造成的停机时间
工作时间则是负荷时间减去那些非计划停机时间,如故障停机、设备调整和更换刀具、工夹具停机等。
减少六大损失与设备综合效率(OEE)计算的关系如图1.3-2所示。
在日本全面生产维护体制中,要求企业的设备时间开动率不低于90%,性能开动率不低于95%,合格品率不低于99%,这样设备综合效率才不低于85%。这也是TPM所要求达到的目标。
由于不同资料,对设备综合效率中英文单词的译法不尽相同。为了便于读者对照参考,现给出以上计算中出现各种术语的英文原文。
• 总工作时间——Total Available Time
• 计划停机时间——Planned Down Time
• 负荷时间——Loading Time

图1.3-2 设备综合效率的计算和减少六大损失的关系
• 工作时间——Operation Time
• 停机时间——Down Time
• 时间开动率——Availability
• 性能开动率——Performance Efficiency
• 净开动率——Net Operation Rate
• 速度开动率——Operating Speed Rate
• 理论加工周期——Theoretical Cycle Time
• 实际加工周期——Actual Cycle Time
• 加工数量——Processed Amount
• 合格品率——Rate of Quality Products
• 设备综合效率——Overall Equipment Efficiency
5.TPM在全世界的推广和影响
日本在本国推行TPM的同时,还注意对外交流和宣传。
虽然PM产生于美国,1987年,当中岛清一率代表团访问美国辛辛那提参加第四届国际维修会议,在匹兹堡的TPM专题会议上宣讲TPM时,有80多个美国企业的150多名代表参加了会议,美国企业对TPM表现出极大的热情。
1987年12月,在巴西的圣保罗和阿雷格里港举办了“TPM管理干部培训班”,TPM随后在巴西和墨西哥等发展中国家推行,并取得了一定成效。
在意大利,15%~20%的企业在推行TPM,也有的企业遇到工会的抵制,导致推行工作无法深入下去。
在英国和斯堪的那维亚地区,成立了“TPM中心”“TPM俱乐部”。
到目前为止,在挪威、意大利、马来西亚、巴西、葡萄牙、西班牙、韩国、美国、中国、印度和新加坡等国都举行过 TPM研讨班。
TPM的国际会议也频繁召开。例如,1991年在日本东京召开“91TPM世界大会”;1992年4月在比利时的布鲁塞尔举行“欧洲公司最高领导人TPM会议”;1992年6月在英国伯明翰召开一次 TPM会议;1992年9月在美国芝加哥召开另一次 TPM会议。
1995年TPM世界大会在日本东京召开,参加会议的代表约800多人,其中有300多人来自北美、拉丁美洲、欧洲和亚洲各国,这次会议受到了国际维修界的瞩目。
总之,据不完全统计,目前世界上引入TPM的国家和地区有美国、南美地区、墨西哥、韩国、泰国、马来西亚、中国、法国、挪威、瑞典、芬兰、英国、意大利、葡萄牙、西班牙等。TPM在全世界范围内产生了较大的影响。