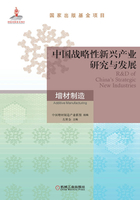
2.1.5 粉末床熔融工艺
粉末床熔融工艺是指通过热能选择性地熔化/烧结粉末床区域的增材制造工艺。代表性工艺有激光选区熔化、激光选区烧结、电子束选区熔化。
激光选区烧结最早由美国德克萨斯大学奥斯汀分校的Carl Deckard于1989年提出,之后他组建了DTM公司,于1992年开发了基于激光选区烧结工艺的工业级装备——Sinterstation。该技术采用半固态液相烧结机制,主要特点是“粉末”和“烧结”,主要成形过程为:采用铺粉方式将一层粉末材料平铺在已成形零件上表面,并加热至恰好低于该粉末烧结点的某一温度,控制激光束按照截面轮廓在粉层上扫描,使粉末温度升到熔化点,进行烧结并与下面已成形部分实现黏结。一层完成后,工作台下降一层厚度,进行新一层截面的铺粉和烧结,直至完成整个部件。该工艺成形原理如图2-6所示。

图2-6 激光选区烧结技术原理图
该技术最大优点在于选材较为广泛,如尼龙、蜡、ABS、树脂裹覆砂(覆膜砂)、聚碳酸酯(Poly Carbonates)、金属和陶瓷粉末等都可以作为烧结对象,成形过程无须支撑,可广泛应用于汽车、家电、建筑、航空、电子、消费品及医疗等行业。当前,市场上激光选区烧结成形专用材料中尼龙材料的应用占到80%以上。
激光选区熔化起源于美国德克萨斯大学奥斯汀分校Carl Deckard提出的激光选区烧结技术。1995年,德国弗朗霍夫激光技术研究所发现激光选区烧结技术成形过程中层间黏结不牢固,试样件致密度较低,在此研究的基础上提出激光选区熔化技术构想,即成形过程中使粉末完全熔化/凝固,主要成形过程为:通过扫描振镜控制激光束按照每层轮廓的扫描路径有选择地熔化金属粉末,逐层堆叠成致密的三维金属零件实体。该工艺成形原理如图2-7所示。
相对于传统制造方法及其他快速成形技术,激光选区熔化技术优势明显,主要体现为:其成形过程具有很大柔性,能够实现复杂结构件的整体制造;金属粉末完全熔化,得到冶金结合的高致密实体,显微组织细小均匀,综合力学性能高于铸件,并接近锻件;激光束能量密度高、光斑直径小,成形结构较为精细;可选材料种类较多,理论上能够被激光束熔化凝固在一起的材料都可以使用该技术进行成形加工。正是由于以上这些诸多优势,激光选区熔化技术的应用范围已拓展到航空航天、军工、医疗、汽车、模具等众多领域,有望变革传统制造方法,发展前景广阔。

图2-7 激光选区熔化成形原理图
资料来源:广东省增材制造(3D打印)产业技术路线图。
电子束选区熔化起源于1994年瑞典Arcam公司申请的一份专利中的电子束熔化成形技术,此后美国麻省理工学院、美国航空航天局、北京航空制造工程研究所和清华大学等分别开发出了基于电子束的快速成形系统。电子束选区熔化利用高能量密度的电子束在高真空环境下逐层熔化金属粉末,与激光选区熔化技术类似,利用电子束实时偏转实现熔化成形。其主要成形过程为:先在铺粉平面上铺展一层粉末;然后电子束在计算机控制下按照截面轮廓信息进行有选择的熔化,金属粉末在电子束的轰击下被熔化并与已成形部分黏结,层层堆积,直至整个零件全部完成;最后,去除多余的粉末,便得可到所需的产品。该工艺成形原理如图2-8所示。
与激光选区熔化工艺相比,电子束选区熔化工艺使用电子束作为能量来源,具有更大的功率密度、更高的材料-电子束能量吸收率、更强的穿透能力、更高的成形件致密度、更高的粉床温度、更低的成形热应力和残余应力、更快的制造速度、更广的材料适应范围等优势。但电子束成形过程较难同激光束一样聚焦出细微的光斑,因此成形件难以达到较高的尺寸精度。目前,该工艺广泛应用于航空航天高性能复杂零部件和医疗植入体制造等领域。

图2-8 电子束选区熔化成形原理图
资料来源:广东省增材制造(3D打印)产业技术路线图。