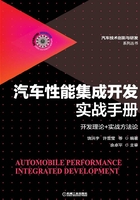
4.3.3 整车开发案例
R&H开发根据项目类别的不同,其开发内容也不同,相对应介入的开发时间节点也不同。对改款车型来说,很多架构件不做更改,此时,只能在一定范围内对调试件进行优化,如弹簧、减振器、轮胎、稳定杆、衬套等。对于全新开发车型而言,所有子系统的结构选型和硬点都重新设计,此时R&H开发是伴随着整车架构正向开发同时开始的。下面举一个案例,结合本章阐述的开发方法和开发流程,从车型规划、市场定位,到整车操纵稳定性和平顺性目标设定及分解,然后到评估调试,最后再到验收试驾和上市发布,完整地讲述R&H开发全过程。
1.车型规划及市场定位
此阶段,公司管理层、规划、市场及工程中心等部门会根据公司战略,制定预期的产品型谱定位、目标客户、品牌建设。并以此制定该款产品的一般优势、品牌DNA及产品制胜优势,此时R&H性能是一个重要的维度。在此基础上开始选择竞品车辆,包括性能对标、成本对标等。
2.性能目标车型选择试驾
有了第一步的活动之后,就要开始组织性能单一目标车型的试驾活动了,通常会将潜在的性能对标车型都找来,加上之前的上代车型(若有),一起组织包括管理层、规划、市场及工程在内的多部门联合试驾,试驾的产出就是确定性能单一目标车型,为后续的性能开发设定目标和依据。图4-66所示为对标车型试驾R&H定位。
3.目标车型性能测试
有了性能单一目标车型之后,就需要快速对该车所有重要性能进行测试。此时上代车型所有R&H性能的客观参数也要有,同时也要了解上代车型(若有)R&H方面的缺点,知道原因所在,并在本轮开发中进行改进。当然,如果条件允许,第二竞品等车辆参数也可以都进行测量,以获得尽可能多的参考样本。

图4-66 某产品R&H定位
4.整车性能目标设定
有了目标车型及上代车型的性能参数,结合上代车型的缺点,就可以制定较为准确的整车R&H目标了,表4-2、表4-3所列分别为某车型的操纵稳定性和平顺性指标及某个节点的设计状态。
表4-2 某车型操纵稳定性指标及状态

表4-3 某车型平顺性指标及状态

5.子系统结构及零件选型
从完全正向开发的角度出发,有了R&H指标之后,需要进行子系统选型,如转向机的助力形式,前后悬架的结构形式,轮胎尺寸等。图4-67所示为不同种类的前悬架在操控性、舒适性、重量、成本等方面的优劣对比,通常麦弗逊悬架成本和重量优势显著,为一般轿车前悬架首选,而双横臂悬架操控性较好,但空间效率不高,一般作为高性能轿车前悬架。

图4-67 前悬架选型
6.关键性能参数带宽设定
重大子系统选型的过程并非一蹴而就,需要架构总布置、成本、性能等各个能块不断地碰撞,此时R&H需要进行不同结构形式的模型仿真计算,甚至制造物理样车进行早期的验证。R&H关键子系统的选型也常常伴随着性能目标的分解,所选择的子系统要能够满足整车性能目标。这个过程也是一个不断优化的过程,各个子系统参数之间存在很多关联性,需要不断地调整和优化,因此不少参数设定的是带宽,而非具体数据,表4-4、表4-5所列为某车辆前、后悬架的关键指标带宽及状态。
表4-4 某车辆前悬架的关键指标带宽及状态

(续)

表4-5 某车辆后悬架的关键指标带宽及状态

(续)

7.硬点开发及优化
子系统带宽的设定和冻结过程是伴随着悬架等关键系统硬点设计及优化的过程,图4-68所示为麦弗逊悬架关键硬点,其运动件关键铰接点及弹性件的弹性中心点被定义为硬点,这些硬点决定了悬架运动学和弹性运动学特性,在仿真模型中不断地调整和优化这些硬点坐标以满足子系统设计指标。
8.调试策略制定及调试带宽设定
在进行硬点优化的同时,也需要对调试件的设计带宽进行制定,包括弹性件的刚度阻尼,弹簧、稳定杆刚度系列,可调减振器的制作和阀系选择,轮胎评估开发计划等。此过程需要与零部件工程师特别是底盘工程师一起进行,需要同时考虑零件的疲劳耐久性能。另外一个需要重点合作的对象是NVH工程师,很多弹性件的参数会直接影响NVH性能,如发动机悬置、轮胎等,在制定这些零件的调试计划时,要充分考虑NVH的需求,很多调试零件需要制作双份。
在项目实施早期,需要根据产品定位的不同,进行硬件选型,不同硬件的性能是有一定带宽的,如前麦弗逊悬架下控制臂后衬套(又称舒适性衬套),对性能要求不高的入门车型,普通橡胶衬套就可以满足要求,但如果是对性能要求高的中高级轿车,则需要选用液压衬套。同样,扭杆梁悬架无论如何调试,R&H都很难达到通用汽车统一试验标准(GMUTS)8分,此时可以选用瓦特连杆或者其他类型的独立悬架。图4-69所示为某项目架构初期R&H调试带宽及硬件选型策略。

图4-68 麦弗逊悬架关键硬点
1—车轮中心 2—控制臂外球头中心 3—控制臂前衬套弹性中心 4—控制臂后衬套弹性中心 5—减振器上安装塔衬套弹性中心 6—转向横拉杆外点 7—转向横拉杆内点 8—减振器下安装点 9—弹簧上安装点 10—弹簧下安装点 11—车轮轴承 12—副车架前安装点 13—副车架后安装点 14—横向稳定杆与副车架安装点 15—稳定杆支架上安装点 16—稳定杆支架下安装点 17—转向机与副车架左安装点 18—转向机与副车架右安装点

图4-69 R&H目标定位及措施
在确定好硬件选型之后,一台车的R&H总体水平基本被限定在一个带宽之内,此时需要精细地调试,以使操纵稳定性和平顺性平衡。
9.主观评估与调试
一切准备就绪,待样车和样件到齐之后,就可以开始进行评估和调试了,此时大部分工作开始从虚拟分析阶段逐步过渡到实车验证阶段,对于与R&H有关的悬架等关键系统,如果是全新开发,如图4-70所示,一般会制作“骡子车”提前进行调试,以尽早验证设计的有效性。然后在集成车上再进行一轮全面的调试和协同开发,该阶段调试结果发布后用于制造硬模零件,此时主要调试零件设计基本冻结。硬模零件造车基本用于性能最终的确认,对于减振器阻尼微调、转向系统助力优化,因不涉及零件模具更改,仍然可以进行适当调整。

图4-70 车辆开发的不同阶段
10.性能试驾及产品发布
在后期的开发和调试中,需要进行工程和管理层的多次试驾,一般与发动机标定节点同步,主要有65%、80%和100%三个主要的试驾。R&H工程师对试驾提出的相关问题进行改进。经过多轮试驾和调试优化之后,产品的R&H性能可达到预期,客观的测试也会开展以验证设计目标。最后市场部门会介入,开展相关的产品宣传、媒体发布和试驾活动,此时R&H工程师最了解车辆的操纵稳定性和舒适性,会参与其中进行产品的宣传,至此整个R&H开发过程圆满结束。