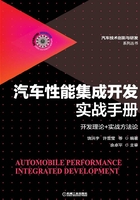
1.2.6 传动系统性能设计
传动系统用于确保驱动单元的实际运行特性尽可能地靠近理想运行特性。以下分析离合器、液力变矩器、变速器和主减速器等传统系统元件的性能设计。
1.离合器性能设计
基于动力性进行离合器的设计时主要考虑离合器的最大传递转矩的能力。当外部施加的转矩超过最大传递转矩的能力时,离合器会打滑。因此一般在设计离合器时,要求其传递的最大转矩大于或等于内燃机转矩。离合器最大传递转矩能力的计算如图1-33所示。

图1-33 离合器最大传递转矩能力的计算
离合器最大传递转矩的计算公式如下:

式中 Tcap——离合器最大传递转矩(N·m);
z——离合器盘片数;
μ——摩擦系数;
r1——离合器摩擦片内径(mm);
r2——离合器摩擦片外径(mm);
Fa——离合器盘片所受正压力。
2.液力变矩器性能设计
液力变矩器选型中,为满足整车性能要求,对其提出表1-10所列的一般要求。这些要求有时是相互矛盾的,这就为平衡设计要求提供了空间。
表1-10 液力变矩器的一般要求

(1)基本参数 液力变矩器的运行特性是选型工作最重要及最先用到的参数,其对于液力变矩器选型工作有很大的影响。
液力变矩器的运行特性可通过以下四个参数来描述:
转速比i:

转矩比K:

效率η:

容量系数(尺寸因数)Ktc:

典型液力变矩器的运行特性如图1-34所示。图中描绘了转矩比、效率和输入端容量系数相对于转速比的关系。

图1-34 典型液力变矩器的运行特性
(2)液力变矩器模型的构建 液力变矩器通过液体路径和机械离合器路径将驱动单元的转矩传递给变速器。这两条路径是并联的。液体路径中,液力变矩器的作用类似于液力耦合器,使驱动单元不受轮边转矩通过传动链传递至涡轮输出轴上的转矩的影响而独立转动,这也是自动变速器提高了驾驶舒适性的一大原因。
液力变矩器的工作原理图如图1-35所示。

图1-35 液力变矩器的工作原理图
(3)液力变矩器的工作状态 液力变矩器根据其离合器的状态,分为以下三种工作状态:
1)打开。离合器完全分离,泵轮转矩通过液压油传动传递到涡轮,涡轮与变速器输入轴刚性连接,故而转矩被传递到变速器。泵轮与涡轮存在较大的转速差,转速比和转矩比通过查表得到。
2)滑摩。离合器处于半离合状态,内燃机转矩部分通过离合器传递到变速器。泵轮与涡轮存在较小的转速差,转速比和转矩比通过查表得到。
3)锁止。离合器完全锁止,此时泵轮与涡轮之间的转速差很小(一般≤20r/min),同时内燃机转矩通过离合器直接传递到变速器输入轴。转速比和转矩比均为1,此时自动变速器的功能类似于手动变速器。
(4)基本参数 AVL Cruise进行仿真计算时需用到的液力变矩器特性参数见表1-11,其中Tp2000为在台架试验中,泵轮试验转速为2000r/min下测得的泵轮转矩。
表1-11 液力变矩器特性参数

(续)

3.变速器与主减速器性能设计
变速器和主减速器均为齿轮系(主减速器可以看成是只有一对齿轮的单档变速器),对于前轮驱动车型而言,主减速器一般集成在变速器中。本书以前轮驱动车型为例,后文中若无特殊说明,所称变速器均包含了主减速器。
变速器和主减速器的设计要点均在于传动比和传动效率。无论是手动变速器(MT)还是自动变速器(AMT/AT/DCT/CVT),均拥有若干套齿轮用于传递驱动单元的转矩。变速器的作用是将驱动单元的输出特性尽可能转化为理想的输出特性。
(1)传动比的设计
1)最小传动比的选择。最小传动比的选择对于汽车的最高车速、后备功率和驾驶性能有很大的影响。下面以最高车速目标来定义最小传动比。
传动系统的总传动比是传动系统中各部件传动比的乘积,即

式中 ig——变速器的传动比;
i0——主减速器的传动比;
ic——分动器或副变速器的传动比。
理论上,igi0ic选择到汽车的最高车速umax相当于内燃机最大功率点的车速up时,最高车速是最大的,即

此时汽车达到功率平衡,即

式中 Pmax——汽车最高车速时的内燃机功率(kW);
Pr——汽车的阻力功率(kW)。
近年来,为了提高燃油经济性,最小传动比有减小的趋势,即令up稍大于umax。
这里为简化计算,可定义ig=1、ic=1(无分动器),则此问题变成选择最优的主减速器传动比i0。
在选定主减速器传动比i0后,可采用AVL Cruise的Matrix Calculation计算功能,分别以ig、ic值为单变量变化计算得到满足最高车速目标的ig、ic值。这两个值作为变速器选型的参考依据之一。
2)最大传动比的选择。最大传动比的选择对于汽车的最大爬坡度、附着率及汽车最低稳定车速有很大的影响。下面以最大爬坡度目标来定义最大传动比。
汽车爬坡时,汽车的最大驱动力与阻力平衡时,爬坡度是最大的,此时

即

则

式中 Fc——滑行阻力(N),通过滑行试验测得,这里考虑车速为20km/h时的滑行阻力;
m——满载质量(kg);
imax——最大爬坡度(%);
Tm——内燃机最大转矩(N·m)。
3)变速器档位数和各档传动比的选择。虽然增加档位数会改善汽车的动力性和经济性,但是对于手动变速器来说,档位数不宜过多,否则会导致结构复杂,换档困难。一般多采用5MT和6MT。自动变速器因为有自动变速器控制单元(TCU)控制换档,不需要驾驶人手动操作,故而目前的趋势是档位数越来越多,如8AT、9AT,甚至是10AT。
变速器中间档位传动比通过各档传动比来确定,它们可保证内燃机在汽车的加速过程中拥有最大的加速强度和最短的加速时间,同时还需兼顾经济性。一般有以下两种确定的方法:
① 等比级数法。等比级数的传动比比较适合于常行驶于良好路面且比功率较大的汽车。其缺点是高档利用率低,平均加速速度较低,油耗增加。
等比级数的传动比如下:

式中 ig1、ig2、ig3…——各档传动比;
q——常数。
最大、最小传动比已经确定,故可按以下公式计算等比级数的传动比qg:

式中 n——变速器档位数;
ig1——变速器最大传动比;
ign ——变速器最小传动比。
② 等差级数法。等差级数的传动比比较适合于常行驶于恶劣环境且比功率较低的汽车。
最大、最小传动比已经确定,故可按以下公式计算等差级数的传动比qa:

式中 n——变速器档位数;
ig1——变速器最大传动比;
ign ——变速器最小传动比。
上述两种方法均基于理想的加速过程,实际的加速过程更复杂,汽车变速器中间档位的实际传动比处于等比级数值和等差级数值之间,且偏向于等比级数值。故可在确定等比级数的传动比之后,按以下公式修正:

式中 λ——修正系数,一般在0.90~0.98之间:比功率低,且常行驶于坏路的车辆,应取下限;比功率高,且常行驶于良好路面的车辆应取上限。
以修正系数为单变量(在0.90~0.98之间,步长为0.01),变化生成9种变速器,利用AVL Cruise的Component Calculation计算功能,得到G1~G9这9种变速器的动力性和经济性仿真数据,从中选出最优方案。
(2)变速器模型的构建
1)变速器的工作状态。变速器根据其齿轮系的转动方向,可以分为正转和反转两种工作状态。
① 正转。前进档位齿轮啮合,变速器将驱动单元的转矩传递到传动轴并最终输出到轮边。
② 反转。后退档位齿轮啮合,变速器将驱动单元的转矩传递到传动轴并最终输出到轮边。
上述两种工作状态,要求主减速器既能正转,也能反转。在校核其承扭能力时,要注意这两种工作状态下的差异。
2)变速器的工作原理。以自动变速器为例,其工作原理图如图1-36所示。

图1-36 变速器的工作原理图