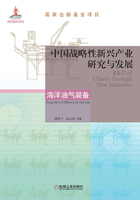
2.2.9 钻杆自动处理系统
自1895年世界上第一台旋转钻机用于石油开采以来,人们就开始寻找新的途径来减轻工作强度和提高工作效率,直到1949年,Humble oil和Byron Jackson公司推出了3臂钻杆排放系统的原型机。
1956年,CUSS-1号钻井平台安装了一套水平钻杆排放系统,这是钻杆自动处理系统第一次得到了实际运用。排放系统将钻杆立根水平摆放在甲板上,通过一个机械化坡道实现钻杆从甲板到井口的传送。与此同时,垂直钻杆排放系统也取得了较快的发展。
1968年,Discoverer号钻井船为了解决因船体在海水中晃动而造成的钻杆操作困难的问题,安装了一套垂直钻杆排放系统,该系统的运用获得成功,并在业内产生了较大影响,很多钻井船只开始效仿。
从20世纪60年代初到70年代末,钻杆自动处理系统获得了较快发展,先后有348套钻杆自动处理系统被应用。
1973年,用于挪威北海地区作业的Smedvig West Venture号半潜式钻井平台上安装了全机械化钻杆排放系统,这是钻杆排放系统首次安装在半潜式钻井平台上,同样获得了巨大成功。据统计,该钻井平台利用机械化钻杆排放系统1年节省了28天时间,平均一趟钻节省1h。钻杆排放系统在Smedvig West Venture平台的成功应用,使在北海地区作业的其他钻井平台也开始安装这类钻杆排放系统。1974年,Sedco445号钻井船安装了水平钻杆排放系统。
20世纪80年代,由于一些国家相关法规的制订和实施,促进了钻杆自动排放技术的快速发展,各种不同结构特点的钻杆自动处理系统相继研制成功,新建海洋石油钻井平台上全部配备了钻杆自动处理系统。从20世纪80年代中后期开始,随着计算机技术、信息技术和控制技术的发展,钻杆自动排放技术开始向自动化和智能化方向发展。一些先进的钻杆自动处理系统可以与钻机的其他操作系统集成在一起,一个人即可完成钻台的所有操作,系统完全按照设定的程序工作,可以自动判断工作状态,一旦出现误操作,系统可以自动停止,真正实现了安全、自动、高效作业。
20世纪90年代以后,钻杆自动处理系统由最初的专为特定钻井船设计发展为模块化、系列化设计,钻杆自动排放技术的应用也由海洋钻井平台走向陆地钻机,逐步实现了模块化和系列化。现已可以根据钻机的类型选择不同的钻杆自动处理系统。
1990年,一种在甲板与钻台之间进行钻杆传送的新型钻杆处理设备被应用于Smedvig公司的Maersk gallant号、West Epsilon号自升式钻井平台上。该钻杆处理设备即为后来的钻杆传送系统。
1997年,位于英国北海Brent油田作业的Charlie号钻井平台,为满足新的工作需求进行了升级改造,采用了甲板钻杆起重机、带式钻杆输送机、星形钻杆排放系统等钻杆操作设备。虽然在试用初期由于工作人员的操作错误等问题导致该船的作业效率一度下降,但经过几个月的使用后,Charlie号钻井平台钻杆排放作业的效率明显提高,甚至超过了原先的1倍。
1999年,挪威的Oseberg Sor平台上安装了钻杆自动处理系统。
2006年,Weather ford公司对StabMaster钻杆自动处理系统的使用情况进行了调查,该系统主要用于升级和改造传统钻井平台,可代替二层台的井架工进行钻杆排放作业。调研结果证明,该系统不仅提高了工作的安全性,也明显地降低了钻杆排放作业时间。
2008年1月,韩国船厂为Stena Drilling公司制造的第六代钻井船Stena Drill-Max交付使用。该钻井船上安装的自动化钻杆处理系统包括钻杆排放系统、氢化裂解器、龙门轨道吊、猫道机及隔水管处理系统。
2009年,Maersk公司的第六代深水半潜式钻井平台Maersk developer在墨西哥湾下水作业。该钻井平台上安装了一整套全自动化钻杆处理设备,主要包括钻杆排放V形门、氢化裂解器、钻杆排放系统上导臂等。与以往不同,新型全自动化钻杆处理系统的各个设备,不再作为独立的系统由工作人员分别对其进行控制,而是作为一个整体系统,由MMC(Microsoft Management Console)系统统一协调控制,以实现钻杆排放过程的全部自动化。MMC系统自动检测和控制各操作设备,协调运作,避免出现碰撞。
截至目前,国外在钻杆自动处理系统方面取得了较为显著的成果,已经形成了一系列完善的设备。其中,具有世界领先水平的是美国NOV公司和挪威的Aker Kvaerner MH公司。
美国NOV公司是世界上最早研究开发钻杆自动排放技术的厂家之一。目前,该公司的钻杆自动处理系统已实现系列化、模块化,可以满足海洋和陆地不同类型钻机的需要。其主要产品包括:钻台多功能机械手、钻杆输送装置、水平钻杆摆放装置、水平/垂直管柱操作装置、二层台钻柱排放系统和钻杆自动排放系统等。
美国NOV公司的各种管柱操作装置全部实现了自动化操作和智能集成控制。所有操作装置的控制与钻机其他设备的控制集成在同一个控制平台上,这样不仅可以对各系统进行操作控制,还可以对设备进行检测和诊断。所有设备按照设定的程序工作,且具有纠错和防干扰功能,如果发生误操作或设备工作过程中受到干扰,系统会停止工作,保证安全。
挪威Aker Kvaerner公司从1980年开始为海洋石油钻机提供钻杆自动排放和处理装置,其产品由最初的比较简单的钻台操作机械手、二层台液压操作装置等发展为目前多种类型的钻杆排放系统,且技术水平先进,自动化程度高,一人即可完成钻台所有工作,效率高、操作安全。而且,这些钻杆处理系统都是模块化设计的,可以根据用户的钻机类型和需要配置不同的装置。
挪威Aker Kvaerner公司的钻杆自动处理系统采用机器人运动控制技术,精确计算和控制钻杆自动处理系统的运动。其具体实现方法为:在液压缸和液压马达上安装位置传感器,控制系统利用位置传感器实现精确的位置控制,可以控制操作对象的6个自由度,其中3个位移自由度决定对象的位置,3个转动自由度决定对象的方位。
国外对钻杆自动处理系统的研究和应用较早,与国外相比,国内对这种系统的研究和设计工作才刚刚起步。
20世纪90年代,中原钻探公司引进的2000m液压钻机中使用了液压钻杆举升装置。2001年,兰州石油化工机器厂研制成功的6000m电驱动沙漠钻机采用了钻杆排放系统。
2004年,中国石油物资装备公司引进的SR250E型钻杆自动排放系统,可为石油钻井及维修作业提供职业的安全保护,适用于陆上钻机、固定平台以及自升式钻井平台。
2006年9月下水作业的海洋石油941配备了美国NOV公司的HR钻杆排放系统、折臂起重机、钻杆输送机及铁钻工等。该钻杆自动处理系统能够实现钻杆的一系列操作,明显地提高了工作安全性以及降低了工作人员的劳动强度。
2007年9月,南阳二机石油装备有限公司生产的液压动力猫道在加拿大北部地区进行作业。该设备能实现低位排放钻杆、将钻杆送入钻台及引回钻杆(即甩钻)等功能,液压动力猫道如图2-4所示。

图2-4 液压动力猫道
2008年,上海三高石油设备有限公司针对陆地钻机,提出了一种轻型桅杆式钻杆排放装置,并于2008年4月前完成了机械结构设计和液压驱动装置设计。同年,中油辽河宝石石油装备有限公司设计了一种适用于陆地钻机的自动化猫道,并就此申请了国家专利。
2011年,我国自主设计、建造的第六代3000m深水半潜式钻井平台海洋石油981,如图2-5所示,代表了当今世界海洋石油钻井技术的最高水平,其上配备了HR柱形钻杆排放系统以及一系列钻杆传送装置。

图2-5 海洋石油981
2011年,中国石油大学(华东)牛文杰研制出一种陆地钻具自动运移装置,可以实现钻具在摆放架和钻井平台间的自动运移。同年,兰州理工大学张洪生设计出一种陆地钻机桅杆式钻杆自动排放系统,该系统可以实现钻杆在摆放架和井口之间的运移,能够和其他装置配合完成钻杆的连接操作。
此外,四川宏华石油设备有限公司、宝鸡石油机械有限责任公司、江苏如石机械有限公司等石油机械制造厂商以及一部分科研单位也陆续投入到了钻杆操作设备的研究和设计工作中,并取得了一定的成果。中国石油大学(北京)海洋油气研究中心也曾和中船重工716所在2011年承担了国家海洋局“自升式钻井平台钻具自动处理系统研制”项目,并实现了国产化应用。