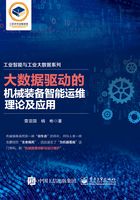
2.3.3 齿轮箱缺失数据恢复
利用如图2-25所示的多级齿轮传动系统实验台设计实验来验证基于张量Tucker分解的缺失数据恢复方法。该实验台主要由动力、传动、负载、测试等部分组成。动力部分包括控制器和驱动电动机,实现电动机转速控制传动部分由两级行星齿轮箱和定轴齿轮箱组成,实现减速传动。负载部分由磁粉制动器组成,可通过编程实现变负载控制。测试部分包括扭矩传感器、编码器、振动传感器等。扭矩传感器通过联轴器安装在驱动电动机和行星齿轮箱之间。编码器安装在输出轴末端。在实验过程中,电动机转速依次设置为1 200r/min、1 800r/min、2 400r/min和3 000r/min。将振动传感器1安装在定轴齿轮箱的轴承端盖上以采集振动数据,采样频率为6.4kHz,采样时长为40s。当转速设置为1 200r/min,采样时刻分别为10s、20s和30s时,迅速拔下并重新安装振动传感器1,以模拟传感器松动导致的数据缺失。紧邻振动传感器1的左侧位置安装振动传感器2,采样频率与采样时长等参数均与振动传感器1相同。振动传感器2采集了整个实验过程中的数据,用来验证基于张量Tucker分解的缺失数据恢复方法对振动传感器1数据的恢复效果。

图2-25 多级齿轮传动系统实验台
当转速为1 200r/min时,振动传感器1的振动数据时域波形如图2-26(a)所示,可以看出,在传感器松动时刻(10s、20s、30s)附近存在数据缺失及操作干扰引起的异常数据。由图2-26(b)可知,缺失处的数据幅值近似为0,数据缺失段几乎不包含齿轮传动系统的健康信息,利用式(2-51)计算数据的缺失率:

式中,L1表示缺失数据段总长度;L2为总数据段长度。经计算,当恢复数据缺失率达到25%时,数据质量较低。振动传感器2采集的数据如图2-27所示,振动传感器2完整采集了实验过程中的数据。对比两个振动传感器无缺失数据段的局部时域波形,如图2-28所示,二者的波形吻合程度高,表明振动传感器2数据可用于验证振动传感器1数据的恢复效果。当转速分别为1 800r/min、2 400r/min和3 000r/min时,振动传感器1的数据如图2-29所示。这三组数据均不含缺失数据。相比转速为1 200r/min时的振动传感器1数据,它们包含更加完整的齿轮传动系统健康信息。

图2-26 转速为1 200r/min时振动传感器1数据时域波形

图2-27 转速为1 200r/min时振动传感器2数据时域波形

图2-28 转速为1 200r/min时振动传感器1与振动传感器2数据局部时域波形

图2-29 不同转速下的振动传感器1数据时域波形
建立多转速监测数据的四阶张量表达,并利用基于张量Tucker分解的缺失数据恢复方法对缺失数据进行恢复。设置滑动窗的长度为6 400,将监测数据分割为不同的时窗段,则转速1 200r/min时振动传感器1的缺失数据位于采样时刻第10s、20s、30s附近。如图2-30(a)所示给出了基于张量Tucker分解的缺失数据恢复方法恢复的数据及对应振动传感器2数据的局部时域波形。为体现该方法的优势,另使用差分整合移动平均自回归模型(Autoregressive Integrated Moving Average Model,ARIMA)和支持向量回归(Support Vector Regression,SVR)对缺失数据进行恢复,结果如图2-30(b)和(c)所示。可以看出,相比于ARIMA和SVR,基于张量Tucker分解的缺失数据恢复方法恢复的数据与振动传感器2数据的波形吻合程度更高。

图2-30 利用不同方法恢复的数据与振动传感器2数据的局部时域波形对比
通过缺失数据的恢复值与对应振动传感器2数据间的均方根误差(Root Mean Square Error,RMSE)评价数据恢复效果。利用不同方法恢复缺失数据的RMSE值如表2-1所示。利用基于张量Tucker分解的缺失数据恢复方法恢复数据的RMSE值小于ARIMA和SVR方法,表明恢复后的数据包含更加完整的齿轮传动系统健康信息,提高了监测数据质量。
表2-1 利用不同方法恢复缺失数据的RMSE值
