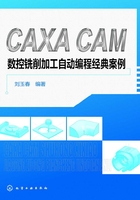
[实例1-1] 平面型腔零件的二维造型与加工
完成图1-1所示的零件二维造型及加工程序编制。零件材料为45钢,毛坯为180mm×160mm×8mm板料。毛坯的上下表面及侧面已满足加工要求。

图1-1 腔体零件尺寸
一、工艺分析
① 选用机床:数控铣床。
② 选用夹具:平口钳夹紧定位,百分表找正。
③ 工艺分析:该零件加工内容包括一个圆弧内型腔孔,两个台阶孔,两个通孔。其中型腔、小孔的尺寸公差均有较高的精度要求,并且工件内侧表面粗糙度要求Ra为1.6μm,所以应该分为粗加工和精加工来完成。
二、绘制零件模型
由于“平面区域粗加工”“平面轮廓精加工”和“孔加工”命令均可以采用2D模型进行加工,因此,结合此零件的特点,只在空间平面内建立2D平面模型就可以生成加工轨迹。
双击桌面图标,进入CAXA制造工程师2016操作界面。移动光标至特征树栏左下角,选择“特征管理”,显示零件特征栏,进入造型界面。
① 在曲线选项卡中,单击曲线生成栏中的“矩形”按钮 在曲线选项卡中,单击曲线生成栏中的“矩形”按钮,在立即菜单中选择“中心 长 宽”方式,输入长度180和宽度160,按回车键。捕捉系统中心坐标,按回车键确定,矩形生成。如图1-2所示。

图1-2 绘制矩形
② 在曲线选项卡中,单击曲线工具栏中的“整圆”按钮 在曲线选项卡中,单击曲线工具栏中的“整圆”按钮,选择“圆心_半径”,按软件提示,捕捉矩形右下交点为圆形曲线的圆心,按回车键输入50,再按回车键完成半径为“50”圆的绘制,如图1-3所示。同理作左上角R50mm的圆。
③ 在曲线选项卡中,单击曲线编辑栏中的“曲线裁剪”按钮 在曲线选项卡中,单击曲线编辑栏中的“曲线裁剪”按钮,在立即菜单中选择“快速裁剪”和“正常裁剪”。按状态栏提示拾取被裁剪曲线,单击矩形外部的圆,裁剪完成。
④ 在曲线选项卡中,单击曲线工具栏中的“整圆”按钮,选择“圆心_半径”,按软件提示,输入圆心坐标(-70,-60),按回车键输入半径8,再按回车键完成半径为“8”圆的绘制。
在常用选项卡中,单击“几何变换”栏中“矩形阵列”按钮,在立即菜单中选取“矩形”,输入行数2,行距120,列数2,列距140四个值。拾取需阵列的R8mm圆,按右键确认,阵列完成。结果如图1-4所示。

图1-3 绘制R50mm圆

图1-4 绘制R8mm圆
⑤ 在曲线选项卡中,单击曲线工具栏中的“整圆”按钮 在曲线选项卡中,单击曲线工具栏中的“整圆”按钮,选择“圆心_半径”,按软件提示,输入圆心坐标(-20,-20),按回车键输入半径47,再按回车键完成半径为“47”圆的绘制。同理,输入圆心坐标(30,30),按回车键输入半径27,再按回车键完成半径为“27”圆的绘制 。如图1-5所示。
⑥ 在曲线选项卡中,单击曲线编辑栏中的“过渡”按钮 在曲线选项卡中,单击曲线编辑栏中的“过渡”按钮,在立即菜单中选择“圆弧过渡”,输入过渡半径13,选择不裁剪曲线1和曲线2。拾取第一条曲线、第二条曲线,圆弧过渡完成。单击曲线编辑栏中的“曲线裁剪”按钮
,剪掉多余线条,结果如图1-6所示。
三、加工程序编制准备
在编制零件加工程序前应该先建立毛坯、建立工件坐标系和建立刀具。
1.建立毛坯

图1-5 绘制R47mm圆和R27mm圆

图1-6 R13mm圆弧过渡
① 选择屏幕左侧特征树的“加工管理”页框,双击特征树中的“毛坯”,弹出毛坯定义对话框。如图1-7所示。

图1-7 毛坯定义对话框
② 选取“拾取两角点”单选框,拾取左下角矩形角点A,然后输入右上角矩形角点B的坐标(90,80,8),回车返回毛坯定义对话框,单击“确定”按钮,毛坯定义完成,完成毛坯的建立。建立毛坯为蓝色矩形线框显示,如图1-8所示的矩形毛坯模型。

图1-8 矩形毛坯模型
2. 建立加工坐标系
为了加工和对刀的方便,在零件的上表面的中心建立加工坐标系(mcs)。在工具选项卡上,单击“创建坐标系”图标;在立即菜单中选择“单点”;按回车键在弹出的弹入输入条中输入坐标值(0,0,8);按回车键,输入新坐标系名称“mcs”,按回车键确定,如图1-9所示。

图1-9 建立加工坐标系
3. 建立刀具
在“轨迹管理”窗口,双击“刀具库”,弹出“刀具库”对话框,并显示当前刀具库中已存在的刀具,如图1-10所示。在该对话框中双击立铣刀02号,弹出“刀具定义”对话框,如图1-11所示,修改刀具直径为12,单击“确定”按钮退出。用这种方法完成添加本次加工所需刀具。

图1-10 刀具库
四、编写零件加工程序
根据平面型腔类零件的特点,选用“平面区域粗加工”“平面轮廓精加工”和“孔加工”的方法进行加工。
1.粗铣内型腔
① 在加工选项卡中,单击二轴加工工具栏中的“平面区域粗加工”按钮 在加工选项卡中,单击二轴加工工具栏中的“平面区域粗加工”按钮,弹出“平 在加工选项卡中,单击二轴加工工具栏中的“平面区域粗加工”按钮,弹出“平面区域粗加工(编辑)”对话框,如图1-12所示。此加工功能是生成具有多个岛的平面区域的刀具轨迹,适合 2/2.5 轴粗加工。设置相关加工参数,环切加工,选择从里向外方式。顶层高度0,底层高度-8,行距为8。

图1-11 刀具定义

图1-12 平面区域粗加工(编辑)对话框
② 加工参数设置完成后,单击“确定”按钮退出“平面区域粗加工(编辑)”对话框,系统进行刀路运算,加工轨迹如图1-13所示。
③ 在加工选项卡中,单击仿真工具栏中的“实体仿真”按钮,单击“内型腔粗加工轨迹”,单击右键拾取结束,在弹出的窗口中,单击“运行”按钮开始轨迹仿真加工,结果如图1-14所示。单击“内型腔粗加工轨迹”后单击右键,在弹出的立即菜单上单击“隐藏”,内型腔粗加工轨迹就被隐藏了。

图1-13 内型腔粗加工轨迹

图1-14 内型腔粗加工轨迹仿真
2.精铣内型腔侧壁
采用“平面轮廓精加工”功能加工内型腔侧壁,此加工功能属于二轴加工方式,由于它可以指定拔模斜度所以也可以做二轴半加工。主要用于加工封闭的和不封闭的轮廓。适合 2/2.5 轴精加工,支持具有一定拨模斜度的轮廓轨迹生成,可以为生成的每一层轨迹定义不同的余量。生成轨迹速度较快。
① 在加工选项卡中,单击二轴加工工具栏中的“平面轮廓精加工”按钮在加工选项卡中,单击二轴加工工具栏中的“平面轮廓精加工”按钮,弹出“平面轮廓精加工(编辑)”对话框,如图1-15所示。设置顶层高度0,底层高度-8,每层下降高度1。

图1-15 平面轮廓精加工(编辑)对话框
② 加工参数设置完成后,单击“确定”按钮退出“平面轮廓精加工(编辑)”对话框,拾取加工轮廓线,单击右键结束,拾取进退刀点A,系统进行刀路运算,加工轨迹如图1-16所示。
③ 在加工选项卡中,单击仿真工具栏中的“线框仿真”按钮,单击内型腔加工轨迹,单击右键拾取结束,在弹出的窗口中,单击“运行”按钮开始轨迹仿真加工,结果如图1-17所示。

图1-16 内型腔精加工轨迹

图1-17 内型腔精加工轨迹仿真
3.粗铣沉台平面
① 在加工选项卡中,单击二轴加工工具栏中的“平面区域粗加工”按钮 在加工选项卡中,单击二轴加工工具栏中的“平面区域粗加工”按钮,弹出“平面区域粗加工(编辑)”对话框,如图1-18所示。设置相关加工参数,环切加工,选择从外向里方式。顶层高度0,底层高度-2,行距为8。

图1-18 沉台平面区域粗加工(编辑)对话框
② 其他各项参数设置完成后,单击“确定”按钮,退出“平面区域粗加工(编辑)”对话框,系统进行刀路运算,加工轨迹如图1-19所示。
③ 在加工选项卡中,单击仿真工具栏中的“实体仿真”按钮 在加工选项卡中,单击仿真工具栏中的“实体仿真”按钮,单击沉台平面粗加工轨迹,单击右键拾取结束,在弹出的窗口中,单击“运行”按钮开始轨迹仿真加工,结果如图1-20所示。
4.钻中心孔
在加工选项卡中,单击孔加工工具栏中的“G01钻孔”按钮,弹出“G01钻孔(创钻孔(创建)”对话框,如图1-21所示。使用 G01 来进行各种钻孔操作,适用于各种没有钻孔循环功能的机床。设置相关加工参数,用直径为3的钻头,钻孔深度4,下刀次数设为1。单击“确定”按钮退出“G01钻孔(创建)”对话框,生成加工轨迹,其他四个小孔加工方法一样,深度为4,如图1-22所示。钻中心孔加工轨迹线框仿真如图1-23所示。

图1-19 沉台平面粗加工轨迹

图1-20 沉台平面粗加工轨迹仿真

图1-21 G01钻孔(创建)对话框

图1-22 钻中心孔加工轨迹

图1-23 钻中心孔加工轨迹仿真
5.钻孔加工
在加工选项卡中,单击孔加工工具栏中的“孔加工”按钮在加工选项卡中,单击孔加工工具栏中的“孔加工”按钮,弹出“钻孔(创建)”对话框,如图1-24所示。设置相关加工参数,用直径为8的钻头,钻孔深度8,下刀次数设为1。单击“确定”按钮退出“钻孔(创建)”对话框,生成加工轨迹,其他四个小孔加工方法一样,深度为8,如图1-25所示。钻孔加工轨迹线框仿真如图1-26所示。

图1-24 钻孔(创建)对话框

图1-25 钻孔加工轨迹

图1-26 钻孔加工轨迹仿真
6.生成G代码
在加工选项卡中,单击后置处理工具栏中的“后置处理”按钮,弹出“生成后置代码”对话框,如图1-27所示。选择对应的数控系统,单击“确定”退出“生成后置代码”对话框,拾取内型腔粗加工轨迹,生成我们需要的内型腔粗加工G代码,如图1-28所示。其他加工轨迹G代码生成方法一样,就不一一叙述了。

图1-27 生成后置代码对话框

图1-28 内型腔粗加工G代码