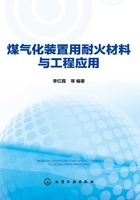
1.3.2 煤气化装置中耐火材料的主要损毁形式
煤气化炉用耐火材料使用寿命影响因素很多,包括耐火材料的组成和物理性能、灰渣的化学组成、气化炉的气氛、气化炉的操作温度和压力等。
不同类型煤气化炉操作温度及排渣形式不同,其耐火材料的损毁形式也不同,损毁主要包括磨损、侵蚀、渗透和剥落,同时还有还原性气氛对耐火材料中部分组分还原反应等。
常压固定床气化炉和加压固定床气化炉中煤粒相对于耐火材料运动速度较慢,煤粒对炉壁耐火材料的磨损较轻;流化床煤气化炉,主要是流态化的煤粒对耐火材料的冲刷磨损。以固态形式排渣的煤气化炉,气化温度较低,对耐火材料的要求不高或不使用耐火材。固态渣与耐火材料发生固相反应程度较小,耐火材料的损毁主要是磨损。
液态排渣的气化炉操作温度高,气化强度大,损毁主要包括化学侵蚀、熔蚀、熔渣渗透以及伴随着温度波动而产生的剥落等,使用寿命依赖于熔渣的组成、操作温度、气化炉的保养以及温度的循环。耐火材料侵蚀较严重,服役寿命不理想。
水煤浆气化炉均以液态形式排渣,液态形式的渣很容易渗入耐火材料内部,并与之发生反应,改变耐火材料的内部结构,在温度波动时使其产生剥落。鲁奇液态排渣炉、粉煤气化炉使用非氧化物作为内衬耐火材料,利用非氧化物导热较好的特性,采用水冷壁结构使耐火材料存在较大的温度梯度,只要操作温度稳定,耐火材料表面能够形成了稳定的挂渣层,形成以渣抗渣的结构;操作温度较高时,耐火材料表面就不能形成了稳定的挂渣层,内衬材料发生氧化而向熔渣中溶解。不同煤气化炉用耐火材料损毁特点如表1-2所示。
表1-2 不同煤气化炉用耐火材料损毁特点


(1)温度的影响
煤气化反应器工作温度随操作方法不同波动很大,一般低温型气化法温度为800~1100℃,高温气化法温度为1400~1600℃。气化炉的温度是耐火材料使用寿命最主要的影响因素。
① 操作温度对耐火材料的影响。水煤浆气化炉操作温度是根据保证煤充分气化、灰渣能顺利排出来确定的,一般控制在1300~1600℃,操作温度往往与煤灰分的性质有关。若煤灰熔渣熔点高,操作温度相应要提高,通常操作温度应较煤灰渣的熔点高30~50℃(也有报道为50~70℃),或者根据灰渣在高温下的黏温特性曲线来确定操作温度,操作温度应高于临界黏度(25Pa·s)对应的临界温度。温度过低,渣不能顺利排出,易造成排渣口堵塞;温度过高,渣对耐火材料的侵蚀和渗透增加。同时,在高压强还原气氛下,温度过高,会使耐火材料中的Cr2O3被还原,造成耐火材料结构的破坏。
上海焦化公司、鲁南化肥厂曾有过一段时间使用了高灰熔点煤,操作温度超过了规定温度1400℃达到1480~1500℃,造成了热面砖的严重损坏。根据操作经验,在合适的操作温度以上,每增加100℃,衬砖的蚀损率增加近3~4倍。
Shell气化炉用碳化硅耐火材料做里衬,碳化硅耐火材料存在易氧化的问题,气化炉操作温度的不当会导致SiC发生氧化反应。气化炉正常运行时,熔融态灰渣会在水冷壁表面形成一层渣层,渣层可起到很好的保护水冷壁的作用。但因为熔渣具有流动性,会随着气化炉运行温度的变化而减薄或增厚,当气化炉超温时,熔渣流动性增强,渣层减薄甚至没有渣层附着,此时就要靠水冷壁表面的SiC耐火衬里来抵御炉内介质的侵蚀。气化炉超温时间过长,SiC表面温度上升,超过一定温度时,就会发生氧化反应,引起层层剥落、磨损。
② 温度波动对耐火材料的影响。温度波动将会导致衬砖裂纹的产生和扩大,是造成衬砖损毁的极其重要的外部条件。气化炉温度波动主要来源两个方面:一是停开炉,二是操作控制不当。这两种温度波动,前者不可避免,后者是人为因素。因此,在开、停车时应控制升、降温速度,在操作过程中稳定操作温度。
(2)气氛的影响
煤炭气化过程中,煤在高温高压下与氧气和水蒸气作用产生含有H2、CO、H2O、CO2等混合气体,该混合气体对耐火材料具有很强的还原能力。这些气体与耐火材料直接接触,在压力作用下,通过砖的气孔、裂纹和砖缝渗透到耐火材料内部,气体不仅与热面砖作用,而且与背衬材料发生化学反应,使耐火材料的结构疏松、强度降低,最终导致耐火材料破坏。若炉内氧分压很低,材料中的Cr2O3也可能被还原成Cr2O或金属Cr。
① H2的影响。M.S.Crowley对耐火材料中SiO2与H2反应的研究结果表明:耐火材料中无论是游离态的SiO2还是结合态的SiO2,都可能与H2发生反应,生成气态SiO从耐火材料中逸出,导致耐火材料失重。失重量与耐火材料中SiO2含量成正比。
Roy.E.Dial归纳了耐火材料与H2的反应机理:当H2不含水蒸气时,发生下列反应:

由于H2的还原作用,使耐火材料中的SiO2变为气态SiO而逸出。另一方面,SiO在温度降低时,又重新氧化为SiO2,产生沉积。该过程通常称为“SiO2的转移”。当H2与水蒸气在高于1204℃共存时,上述反应不能进行。但M.S.Crowley指出:水蒸气可减缓含SiO2耐火材料的失重,但不能完全消除。
M.S.Crowley和J.E Wygant通过分层分析的方法,从氨厂二段转化器的炉头上取出使用两年后的残砖,发现工作层内的SiO2减少了50%,而离热面13mm处,SiO2含量几乎没有变化;从两个废热锅炉取出的沉积物分析结果表明:SiO2的转移是废热锅炉产生沉积物的主要因素。所以,气化炉实际运行中,在H2的作用下SiO连续逸出,留下薄弱疏松的骨架结构,强度降低,加速了炉衬蚀损。更为严重的是SiO2顺气流在冷却区(废热锅炉、催化剂床及输送管线等)沉积、堵塞管路,影响操作,甚至导致停炉事故发生。
② 水蒸气的影响。早期的研究结果认为,当气氛中有大量蒸汽存在时,SiO2可能发生溶解或者最低在816℃下可能会从耐火材料中蒸馏出。这时,耐火材料的强度降低程度随蒸汽分压的增加和温度的提高而增大。实际上,SiO2与水蒸气生成气态水化物,如Si(OH)4或Si2O(OH)4,其反应式为:

在1100℃、6.86MPa的条件下,耐火材料接触纯蒸汽250h后,试验装置内壁和Al2O3分离盘上可观察到约0.5mm厚的玻璃涂层。经能谱扩散X射线分析,其主要成分是含硅物质。同时还发现,高硅耐火材料中SiO2含量减小,证实了上述机理。
③ CO的影响。CO对耐火材料的损害作用是一种特殊的破坏形式,首先是CO渗入耐火材料的孔隙,由于气孔内CO的相对分压增大,发生布氏反应(Boudouard reaction):

反应结果使碳在耐火材料中沉积下来,碳素沉积导致耐火材料鼓胀破裂,最终损毁。碳素沉积产生在300~700℃的温度范围内,在450~550℃最为严重。这在实际中意味着碳素沉积发生在热面的里侧,热面因此而剥落掉。
碳素沉积的催化剂是氧化铁或碳化铁。研究资料表明:FeO、Fe2O3和Fe3O4三个氧化物中使碳素沉积量最大的是Fe2O3,没有发现Fe对碳素沉积有催化作用。用SEM对试样磨光面的观察表明,碳素沉积在试样表层内平均分布,沉积在形式上是大小不一、形状不规则的块状和板片状。电子探针证明沉积物的确是碳,此外在沉积的地方也发现了铁的存在。
(3)操作压力及流体速度的影响
气化炉的操作压力及流速对耐火材料的使用寿命也有较大的影响。
① 操作压力对耐火材料的影响。煤气化效率随压力提高成倍地增大。所以,各种方法都趋向于高压,一般操作压力为0.1~10.5MPa。水煤浆加压气化炉的工作压力多在2.7~6.5MPa,压力提高可以成倍提高气化效率,同时也加大对炉衬材料的冲刷。在煤灰熔渣黏度相同的条件下,熔渣渗入衬砖内部的深度要比低操作压力时要深,因而衬砖可能发生的剥落厚度要大。在富含水蒸气的气氛中较高压力将加速耐火材料的损毁,对炉衬使用寿命不利。
② 流体速度对耐火材料的影响。运动中的煤、灰、炭和其他固态组分粒子本身是没有腐蚀作用的,但它们的冲刷(磨损)作用可使因气氛及熔渣侵蚀导致表面软化的炉衬过早地损毁。物料颗粒的大小和速度对炉衬的损毁影响很大。在流化床系统中,粒子速度为1~3m/s时对炉衬蚀损不明显,而气流速度高于15m/s时,蚀损加剧。
在水煤浆加压气化炉中,包括炭粒、熔灰渣在内的固体粒子和合成气体以5~10m/s速度从炉膛上部到下部流动。当热面衬砖受熔渣和还原气体的侵蚀表面存在低熔物,这些低熔物易被冲掉,同时热面砖的剥落层也不断受到冲击。这种高速流体的冲刷(磨损),导致衬砖的损毁。
(4)灰渣成分的影响
煤熔渣的主要成分为SiO2、FeO、CaO、MgO、Al2O3,其中SiO2和Al2O3的含量大于CaO、MgO、FeO含量的总和,为酸性较强的熔渣。通常当温度高于1400℃时,煤灰熔融,所形成的煤熔渣对多数耐火材料都具有侵蚀性。
对耐火材料侵蚀最为严重的成分主要为CaO、FeO、V2O5和碱金属氧化物等。煤熔渣的黏度一般较高,为保证灰渣能在较低的温度下顺利排出,通常加入石灰或铁的氧化物等助熔剂来降低黏度。随着助熔剂的加入,灰熔渣具有良好的流动性,黏度较低,对热面衬砖的侵蚀和渗透均较严重,它是导致砖衬损毁的非常重要的因素。所以气化炉操作应在保证排渣黏度的情况下,选择较低的操作温度。
① CaO的作用。对于灰渣中氧化钙含量较低的煤来说,其灰渣的熔融温度一般高达1400℃,这对气化炉的操作是非常不利的。通常的做法是在煤中加入一定量的石灰,使灰渣熔融温度降低,黏度降低,以保证操作温度下灰渣顺利排出。加入的CaO与渣中酸性氧化物SiO2及Al2O3形成钙长石和钙黄长石,使渣的黏性急剧下降,从而保证在气化炉操作温度下,熔渣能顺利排出而不致出现堵塞。
随着CaO含量的增加,灰渣对耐火材料的侵蚀也急剧增加,图1-12给出了不同CaO含量的煤熔渣对耐火砖的侵蚀率。高钙灰渣黏度低,在耐火材料中渗透后形成致密层,若操作温度出现波动,因渗透层与原砖层热膨胀系数不同,极易引起剥落。因此,气化炉操作条件应尽量避免出现温度波动或氧化性气氛。

图1-12 不同CaO含量的煤熔渣对耐火砖的侵蚀率
② FeO(Fe2O3)的作用。在煤熔渣中增加FeO含量,可显著降低灰渣的熔化温度和渣黏度。FeO的存在,煤熔渣相组成将进入CaO-FeO-Al2O3-SiO2体系,能够表示煤渣熔融状态下平衡关系的已知有方铁矿-钙长石-假硅灰石系统和方铁矿-钙长石-二氧化硅系统。该系统表明,与煤渣有关的相组成最低液相温度应在1080~1200℃之间。通过对耐火材料侵蚀性试验,发现随FeO(Fe2O3)含量的增加,熔渣对耐火材料的渗透加剧。特别是当FeO含量达到25%时侵蚀最严重。
③ V2O5及碱金属的作用。在还原气氛下,矾的氧化物通常以V2O3的状态存在,但与Al2O3、CaO、Na2O等氧化物共存的情况下,则是以V2O5的形式与其他氧化物生成CaO·V2O5、Na2O·V2O5、Al2O3·V2O5等熔点更低的化合物,对耐火材料的侵蚀将更加严重。同时,当V3+转变成V5+时伴随着较大的体积膨胀,V2O3渗透到砖的气孔或缝隙中,在开、停车的过程中会因矾的价态转变而导致耐火砖体积膨胀,最终导致砖的胀裂。
碱金属氧化物K2O、Na2O作为渣的组分将显著降低渣的熔点和黏度,增加渣对耐火材料的侵蚀与渗透;同时,K2O、Na2O在耐火材料中存在,降低了液相出现的温度,从而降低了耐火材料的抗侵蚀性能。在炉内气氛发生变化或开、停车的过程中,K2O、Na2O还与耐火材料中Cr2O3反应生成溶于水的六价铬盐,对环境的影响很大。