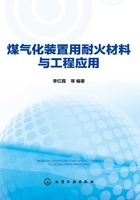
1.2.3 碎煤气化装置
碎煤气化装置可分为常压气化和加压气化。常压气化技术是以空气、蒸汽、氧气为气化剂,将固体燃料转化成煤气的过程,生成煤气的有效成分主要有H2、CO和少量CH4。加压技术是在常压气化技术基础上发展起来的,以氧气和水蒸气为气化剂。典型常压气化炉为UGI(United Gas Improvement)炉,加压气化炉为鲁奇(Lurgi)炉和BGL(British Gas and Lurgi)炉,国产化的炉型主要为赛鼎碎煤加压气化炉。
(1)UGI炉
世界上第一台气化炉是德国于1882年设计的规模为200t/d的煤气发生炉。1913年在德国OPPAU建设第一套用炭制半水煤气的常压固定层造气炉,能力为300t/d,后来这种炉演变成UGI型煤气炉。
UGI炉的工艺原理是:原料煤由炉顶加入,气化剂(空气和水蒸气或水蒸气和富氧)从炉底吹入,炉内料层自上而下可分为六个层带:空层、干燥层、干馏层、还原层、氧化层、灰渣层,原料煤依次进过各层发生不同物理化学反应。气化过程如图1-8所示。整个气化过程是在常压下进行的。在气化炉内,煤是分阶段装入的,随着反应时间的延长,燃料逐渐下移,经过干燥、干馏、还原和氧化等阶段,最后以灰渣形式不断排出(见表1-1)。UGI炉结构如图1-9所示。炉壳采用钢板焊制,上部衬有耐火砖和保温硅砖,使炉壳钢板免受高温损害,下部外设水夹套锅炉,用来对氧化层降温,防止熔渣粘壁并副产水蒸气。UGI炉采用间歇法气化工艺,气化过程中大约有30%的时间用于吹风和倒换阀门,有效制气时间短,气化强度低。

图1-8 常压固定床
气化过程简图

图1-9 UGI炉结构
1—炉壳;2—安全阀;3—保温材料;4—夹套锅炉;5—炉箅;6—灰盘接触面;7—底盘;
8—保温砖;9—耐火砖;10—液位计;11—蜗轮;12—蜗杆;13—油箱
表1-1 UGI煤气炉由下而上燃料层各区域特性


该工艺必须使用粒度为25~75 mm的优质块煤;灰渣中残炭量很高,一般在10%以上,部分企业可达25%。UGI炉属于落后技术,国外早已不再采用。我国中小化肥厂有900余家,多数厂家仍采用该技术生产合成氨原料。由于常压煤气化技术对原料要求严格,生产能力小,能耗高等缺点,随着能源政策和环境的要求越来越高,这种技术会被新的煤气化技术取代。
(2)鲁奇(Lurgi)炉
1927~1928 年,鲁奇气化技术研发始于德国,主要目的是进行褐煤完全气化试验。1936年设计出了第一代工业化鲁奇加压炉,以褐煤为原料生产城市煤气,气化剂为氧气和水蒸气,出灰口设在炉底侧面,炉内壁有120~150mm厚的耐火砖衬里,内衬砖既可避免炉体受热损坏,又可减少气化炉的热损失。第一代工业化鲁奇加压炉只能气化非黏性煤,气化强度较低。为了能够气化弱黏性的烟煤,提高气化强度,第二代加压气化炉设置了炉内搅拌装置,起到破黏的作用,可以气化弱黏结性煤,同时取消了耐火衬里,设置了水夹套。为了提高鲁奇炉的生产能力,扩大煤种的应用范围,鲁奇公司开发了第三代加压气化炉,外壳采用双层夹套外壳,同时第三代炉的结构材料、制造方法、操作控制等均采用现代技术,自动化程度较高,是目前世界上使用最广泛的一种炉型。1974年,鲁奇公司与南非萨索尔合作开发出直径为5m的第四代加压气化炉,该炉几乎能适应各种煤。此外鲁奇公司还开发研制了液态排渣气化炉,该炉可以大幅度提高气化炉内燃烧区反应温度,减少蒸汽消耗量,提高蒸汽分解率,单炉生产能力比固态排渣炉提高了3~4倍。鲁奇公司还进行了“鲁尔-100”气化炉的研究开发,可使气化压力提高到10MPa。随着操作压力的提高,氧耗量降低,煤气中甲烷含量提高。目前广泛应用的是第3代Mark Ⅳ型鲁奇炉,并已成功开发出第4代Mark+型(鲁奇公司开发)和Mark Ⅴ型(萨索公司开发)鲁奇炉。
鲁奇加压气化炉(图1-10)压力为2.5~4.0MPa,气化反应温度为800~900℃,固态排渣,以小块煤(对煤粒度要求是6mm以上,其中13mm以上占87%,6~13mm占13%)原料、蒸汽和氧气连续送风制取中热值煤气,采用固态方式排渣。其特点是生产的煤气中含有10%~12%的甲烷和不饱和烃,适合处理灰分高、水分高的块粒状褐煤。鲁奇炉内燃料和气化剂逆流运动,炉温较低。鲁奇技术主要缺点是操作流程较长,以及含酚废水难以处理。

图1-10 鲁奇加压气化炉
中国于20世纪50年代中期由云南解放军化肥厂引进第1代鲁奇炉,以煤制气生产合成氨;20世纪80年代中期,山西天脊煤化工集团公司成套引进第3代Mark Ⅳ型鲁奇炉,也用于煤制气生产合成氨;之后,兰州气化厂和哈尔滨气化厂也陆续引进了几套Mark Ⅳ型鲁奇炉,于20世纪90年代初相继投入运行。目前,中国已引进鲁奇炉超过50台(包括已投运和在建),但最新开发的Mark+型和Mark Ⅴ型鲁奇炉在我国尚未有引进和使用业绩。鲁奇加压气化技术最大不足之处在于其产生的废水成分复杂,处理难度大,达标排放困难,处理成本较高,环保压力大。但经过几十年的技术攻关,其污水经过处理后已基本能够实现稳定达标排放,在技术上已完全可以达到系统内废水零排放的目标。
(3)BGL炉
1975年,英国燃气公司在原鲁奇加压气化技术的基础上开发出液态排渣的BGL(British Gas and Lurgi)固定床加压气化技术,气化区温度在1300~1600℃,气化压力在2.0~4.0MPa。BGL气化技术的操作工艺和炉体结构与鲁奇炉相似,主要差别在于炉底排渣部分。该技术对鲁奇炉的改造主要包括取消转动炉箅系统、渣口下方增设激冷室、增设相关的水路冷却系统和炉内增设耐火衬里。与鲁奇气化技术相比,BGL加压气化技术大幅度提高了气化效率和气化强度,蒸汽用量是后者的10%~15%,蒸汽分解率超过90%;产生的废水仅为后者的25%,污水处理负荷大幅降低;具有投资少、建设周期短、生产效率高、运行和维护成本低等综合优势。
BGL炉操作压力为2.5~3.0MPa,气化温度在1400~1600℃,超过了灰渣流动温度,灰渣呈液态形式排出。液态排渣固定床加压气化炉炉体结构比传统的固态排渣固定床加压气化炉简单,煤锁和炉体的上部结构与干法排渣的鲁奇炉大致相同,BGL炉示意图如图1-11所示。不同的是用渣池代替了炉箅。块煤(最大粒度50mm)通过顶部的闸斗仓进入加压气化炉,助熔剂(石灰石)和煤一起添加。当煤逆着向上的气流在气化炉中由上向下移动时,被干燥、脱除挥发分、气化、最终燃烧。在气化炉的下部设有4个喷嘴。喷嘴将水蒸气和氧的混合物以60m/s的速率喷入燃料层底部,在喷口周围形成一个扰动状态的燃烧空间,释放出的热量维持炉内2000℃的高温,这样的高温使灰熔化,并提供热以支持气化反应。液态灰渣首先排到炉底收集池里,其次再自动排入水冷装置。灰渣在水冷装置形成无味的、不可渗滤的熔渣状玻璃态固体,最后排出。

图1-11 BGL炉示意图
BGL气化炉和鲁奇炉最大区别在于BGL炉采用液态排渣。鲁奇炉没有耐火衬里,使用水夹套保护炉壳。BGL气化炉采用常规压力容器材料制成,配有循环冷却水夹套,内壁上设计加入耐火砖衬,形成简单的水夹套保护层。熔渣池的结构和材质是该炉技术关键所在。炉内所用耐火材料需能耐高温和抗腐蚀性能,必须致密、孔径小,不含活性铁,对排渣口的耐火材料要求更高。
2005年,云南煤化工集团采用英国西田煤气化试验厂的设计方案改造了1台固定层加压气化炉作为国内首台BGL试验和示范炉,用于探索直接气化当地褐煤(含水量高达35%左右)的途径。BGL加压气化技术在国内的第1个大型商业化项目是由内蒙古呼伦贝尔金新化工有限公司从英国引进3台BGL气化炉建设的500kt/a合成氨、800kt/a尿素生产装置,2011年8月竣工,2011 年9月初进入投料试车阶段,目前已正式投运。
(4)赛鼎碎煤加压气化炉
国产化碎煤气化装置较少,主要为赛鼎碎煤加压气化炉,该炉型是赛鼎工程公司在消化、吸收鲁奇加压气化技术的基础上开发的,于1996年首次成功应用于山西化肥厂,炉型相当于鲁奇第3代Mark Ⅳ型气化炉。该技术的成功开发,基本上取代了鲁奇加压气化技术在国内的应用,具有较好的国内应用前景。